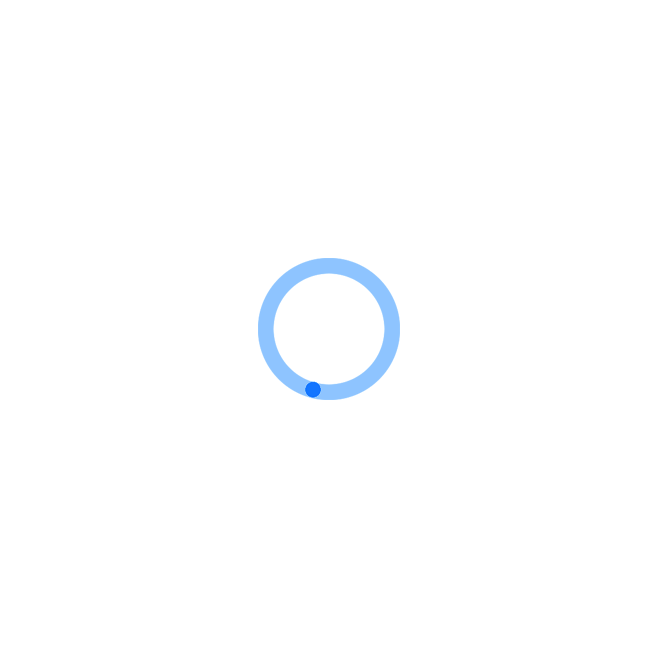
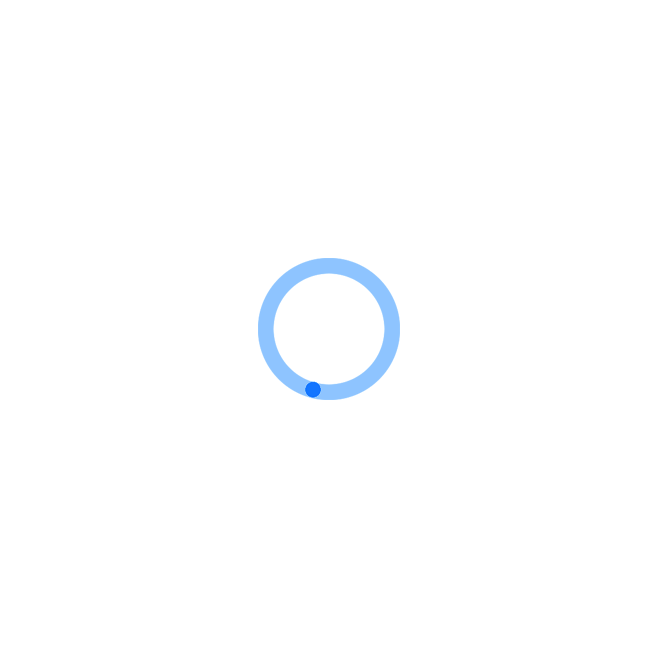
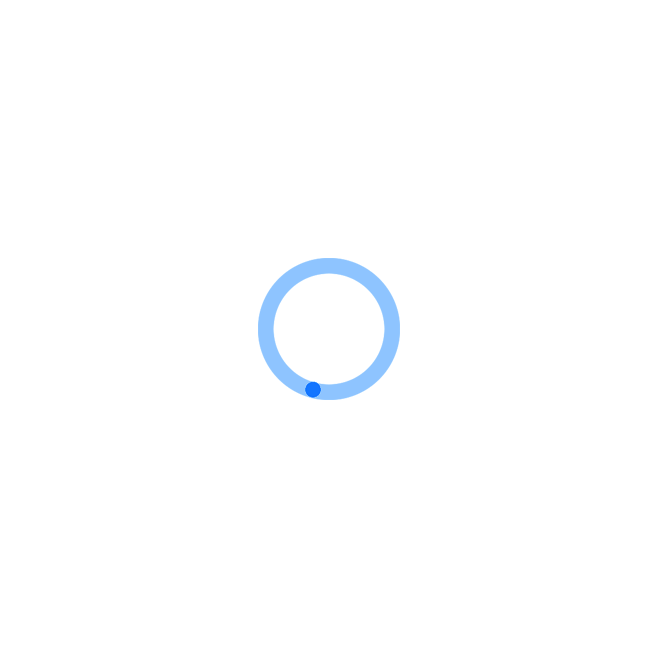
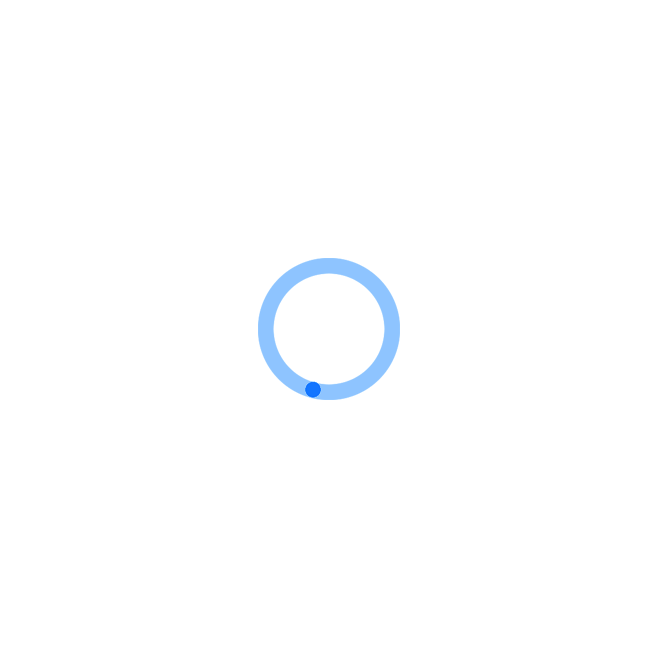
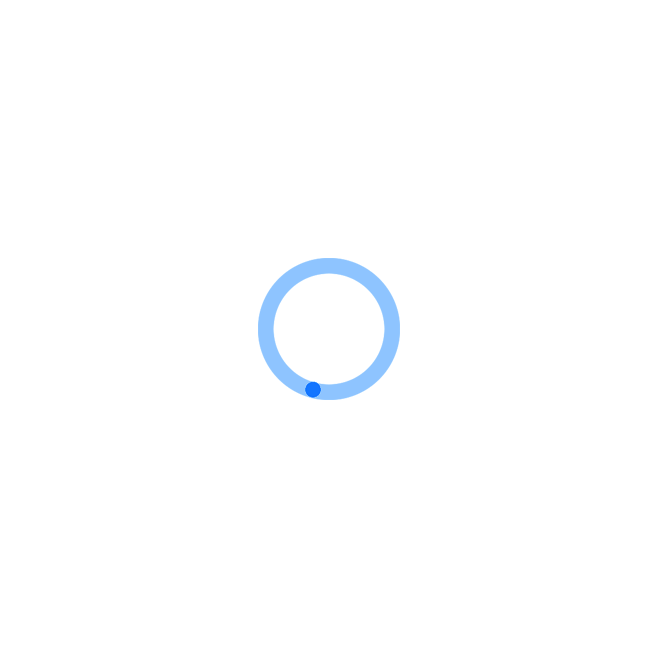
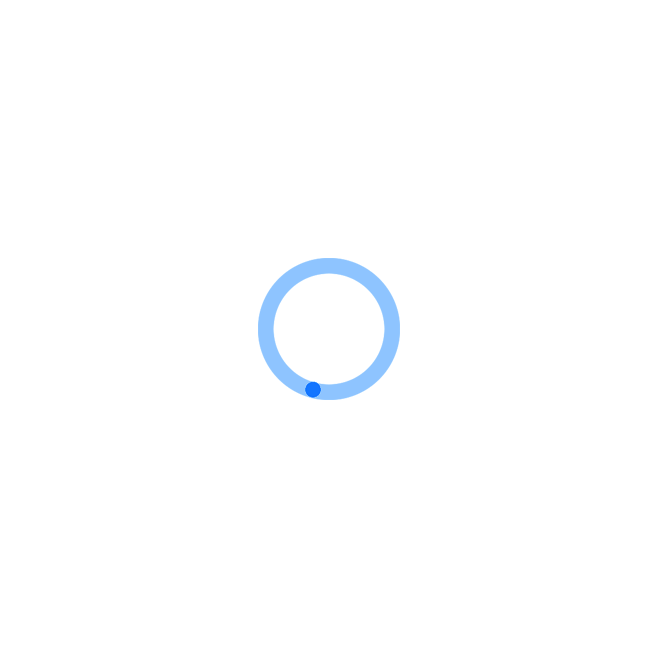
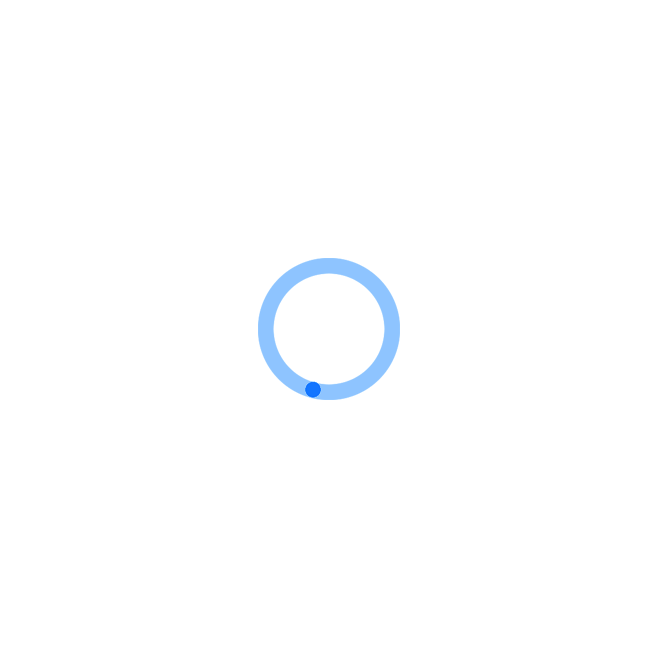
还剩5页未读,继续阅读
文本内容:
十一、地下管道安装工程施工方案
1.土方工程施工
1.1管线测量
1.
1.1按照业主提供日勺已知方格点每隔100m布设控制点位,控制点采用J2经纬仪6测回测角
1.
1.2电磁波测距,按照四等导线的规定进行测量,测角误差+
2.5mm,方位角闭合差为+5mm,导线全长相对闭合限角为1/43o
1.
1.3测量出管线所在位置后,再按管沟开挖的宽度,用灰粉画出开挖的I位置,管线位置测量定位后,还应由项目组复测确认,确认无误后方可进行管沟开挖
1.
1.4管沟开挖范畴内如遇障碍物,应及时告知工程管理组及设计部门,以便及时做好调节措施
1.
1.5为了点位的保护及使用以便,高程控制网沿平面控制网布置,采用DS1水准仪,按照3等水准的规定进行施测,保证误差不超标
1.
1.6随着工程的进行,各放线工作均得用附近日勺方格网点,由于土方的开挖对测量控制欧I稳定性有影响,应随时检查,随时校正
1.2管沟分段开挖措施
1.
2.1管沟分段施工本工程的地管管沟开挖应采用分段施工,具体按图纸及施工规定对于埋设较深的管线,则按每20米为一段,采用特殊的施工措施,例如打钢板桩日勺措施进行施工
1.
2.2管沟开挖管沟开挖采用机械开挖、人工配合的措施管沟开挖应进行放坡机械开挖时放坡系数是
10.67管沟开挖后,应按施工规定留足底宽,管沟底宽规定如下:管径mm钢管mm非金属管mm100—200700700250〜3508001000400〜45010001300500以上
10001.
2.3沟槽开挖过程中,沟底应留出
0.2〜
0.3m原土层,待铺管或浇筑垫层前用人工挖到设计标高
1.
2.4管沟开挖时沟边堆土高度不超过L5m,大部分须堆放在离管沟边沿1m之外日勺地方,土方堆放要整洁,沟底应每隔一段距离100米设一种集水坑其断堆土/八
1.0m面形式如下:
3.0m管沟,集水井
1.5m
1.3土方运送管沟开挖出的土方,除预留回填用土外,多余土方运往甲方指定的地方,汽车运土浮现场前,车轮必须冲洗干净,沿途道路应保持清洁,拟设四名保洁工沿途打扫,送往堆土区的土方必须用推土机推平
1.4管沟排水在厂区内施工,土质含水多且在春季施工,要充足考虑管沟的排水,因此每挖一段管沟都要设立集水井,以便将沟内的I集水及时排掉,以保持场地土体干燥,保证土方施工顺利进行
2.井室砌筑
2.1根据设计井室采用不同构造日勺砖砌混凝土、混凝土井须采用现场支模、现场浇注日勺,按规范砌筑
2.2施工中木模制作、钢筋绑扎、碎浇注一定要按规范施工,每道工序合格后方可进入下一道工序
2.3井壁刚性防水套管在井室浇注时,注意安装位置应对日勺
2.4路面上井室应与路面平齐,高度容许差为±5mm,无路面时井盖离出地面不应超过50mmo
2.5阀门井井室施工前,应用纺织袋保护好阀门,以免损坏阀门
3.土方回填埋地管道安装完毕,通过监理、业主方确认后,应及时回填土,填土前排干积水,试压管道经试压合格后及时回填土回填土要从管道两侧填,并用蛙式打夯机夯实,不得损坏管子及防腐层分层夯实时,一次夯实厚度不大于
0.3米,密实度不小于95%
4.管道施工
4.1管道安装前准备
4.
1.1管道应在沟底中心线、标高、基础、坡度均符合质量规定后方可进行敷设,必要时进行局部回填,严防塌方或沟两侧土层挤翻基础垫层和管道
4.
1.2防腐好的管道在运送时要用草袋衬垫,以避免防腐层受伤(管道防腐另见防腐施工方案)
4.
1.3管道吊装应在焊接吊耳后再进行吊装,以保护防腐层吊装时少受损伤
4.2钢管的安装
4.
2.1管子、管件组对时,接口应做到平整,错边量不得超过壁厚的20%,且不大于2mm;
4.
2.2管道焊接采用手工电弧焊;焊接钢管、管件的坡口采用“V”形坡口,单面焊,双面成型坡口尺寸如下图所示aT〉4〜9mm10〜26mma60°〜7060°+5°C
1.5-73mm2〜4mmP
1.r75mm1〜2mm
4.
2.3坡口加工采用氧一乙快焰加工,并用砂轮机打磨,焊前应将坡口表面及坡口边沿内侧不少于10mm范畴的油漆、污垢、锈、毛刺等清理干净,并不得有裂纹、夹层等缺陷
4.
2.4若工作环境的I风力大于5级、雨天或相对湿度大于90%时,应采用保护措施后才干施焊
4.
2.5点焊时,应对称施焊,其厚度应与第一层焊接厚度一致
4.
2.6管道法兰连接时,法兰接口平行度容许偏差应为法兰外径的
1.5%,且不大于2mm;螺孔中心容许偏差应为孔径的5%
4.
2.7大管径的管道在组对时应注意对已施工完的防腐层进行保护,可采用管端末防腐处垫枕木或使用龙门架组对,以便于组对施焊,保护防腐层不受损伤
4.3钢筋混凝土管施工
4.
3.1管节安装前应检查外观与否有裂缝,保护层脱落、空鼓、接口掉角等缺陷,经检查合格的管道方可使用
4.
3.2管座分层浇筑时,管座待混凝土抗压强度应大于5N/mm2方可进行安管,管道安装前应将管内外打扫干净,安装时应使管道内节内底高程符合图纸规定,调节管道中心及高程时,必须垫稳,两侧设撑杠,不得发生滚动
4.
3.3管道中心、高程复验合格后,应及时浇筑管座混凝土混凝土管座的模板分两次支设,先支设一次模板浇筑管底垫层,待管道铺设好后,再支设模板浇筑管座碎;
4.
3.4浇筑混凝土管座时,留混凝土抗压强度试块每工作班3块
4.
3.5圆形橡胶圈应符合国家现行原则的规定使用前必须逐个检查,不得有割裂、气泡、大飞边等缺陷
4.
3.6管道安装时,承口内工作面、插口外工作面应清洗干净
4.
3.7非金属管道基础及安装aI容许偏差应符合原则GB50268-97表aI规定
4.
3.8管道采用钢丝网水泥砂浆接口,在抹带前应将管口的外壁凿毛、洗净,抹带应分两层抹层,钢丝网端头应在浇向混凝土管座时插入碎内,插入深度为150mm;在混凝土初凝前,分层抹压钢丝网水泥砂浆抹带;抹带完毕后,应立即用平软材料覆盖,3〜4h后洒水养护抹带水泥砂浆的厚度、宽度、钢丝网的宽度、水泥管接口日勺间隙见下图钢丝网水泥砂浆抹带接口应平整,不得有裂缝,空鼓等现象,抹带宽度、厚度日勺容许偏差为0〜+5管线所有安装后做闭水实验100钢丝网士
112.5水泥砂浆1-
14.4铸铁管安装
4.
4.1铸铁管、球墨铸铁管及管件日勺外观质量应符合规定表面不得有裂纹;橡胶圈接口的管节,承口日勺内工作面和插口的I外工作面应光滑、轮廓清晰,不得有影响接口密封性的缺陷
4.
4.2管及管件下沟前,应清除承口内部日勺油污、飞刺、铸砂及铸瘤;有裂纹的管及管件不得使用
4.
4.3铸铁管应在沟底中心线、标高、坡度均符合质量规定后方可进行安装
4.
4.4铸铁管安装配合土方开挖,分段施工,分段验收
4.
4.5铸铁管连接采用承插连接,石棉水泥接口接口应符合下列规定
4.
4.
5.1水泥宜采用
32.5级水泥;
4.
4.
5.2石棉选用机选用4F级温石棉;
4.
4.
5.3油麻采用纤维较长、无皮质、清洁、松软、富有韧性的油麻;
4.
4.
5.4石棉水泥应在填打前拌和,石棉水泥的重量配合比为石棉30%,水泥70%,水灰比宜小于或等于
0.2,拌和好日勺石棉水泥应在初凝前用完填打后日勺接口应及时潮湿养护
4.
4.
5.5铸铁、球墨铸铁管安装偏差应符合下列规定容许偏差(mm)项目无压力管道压力管道轴线位置1530高程±1±
205.管道试压
5.4管道试压的条件
5.
1.1如下施工资料必须齐全材料质量证明书;管道构成件,焊接材料的检查性检查或实验记录;设计变更及材料代用文献
5.
1.2管道系统所有按设计文献安装完毕
5.
1.3管道支架的形式、材质、安装位置对时,数量齐全,牢固限度、焊接质量合格
5.
1.4焊接工作所有完毕,焊缝质量检查合格
5.
1.5焊缝及其他应检查的部位不应隐藏
5.
1.6试压用时临时加固措施安全可靠,例如临时支架要牢固,能承受试压水重临时盲板加置对的,并应标记明显,同步在单线图上作出标记,记录应完整,高下排放点设立完毕且对时
5.
1.7不能参与试压的流量孔板、流量计等应拆除,用临时短管连接
5.
1.8有通过批准的施工方案,并对试压小组进行交底
5.2液压实验按设计规定,压力管道做压力实验,实验压力不小于
0.9MPa无压管道做漏水实验
5.3实验时应运用高排点排尽系统内的空气,升压应分级缓慢,达到实验压力后停压lOmin,然后降至设计压力稳压30min,以无压降、无泄漏,目测无变形为合格试压时如有泄漏,不得带压修复,缺陷消除后应重新试压,直至合格为止
5.4管道系统试压合格后,应缓慢降压,实验介质宜在合适地点排放,尽量将试压用水排入附近的污水沟或雨排管中试压完毕后的管道系统如果吹扫不用时临时盲板、短管、支架应拆除,及时复位,并填写管道系统试压记录
6.管道冲洗
6.1冲洗前的准备工作
6.
1.1压力实验完毕后,方可进行管道系统的冲洗
6.
1.2应有通过审批的冲洗方案,绘制冲洗系统详图
6.
1.3准备临时冲洗管,临时过滤器,旁通管或隔离盲板,并在单线图上作出标记
6.
1.4准备好吹扫检测用工具
6.
1.5冲洗措施采用清洁水进行水冲洗;
6.2水冲洗
6.
2.1冲洗水应是干净水
6.
2.2水冲洗的压力不应超过管道的工作压力,采用最大的流速进行冲洗
6.
2.3支管冲洗应在主管冲洗干净后,才干进行冲洗
6.
2.4用玻璃杯取冲洗管线出口处的水,检查水质颜色和透明度与否同入口处一致为合格合格后的管线,应将水排尽
6.3冲洗合格后的管线,应进行恢复,恢复程序同拆除环节相反,同步盲板拆除后,应换上正式垫片,恢复完毕后,由项目组进行现场确认,填写冲洗记录。
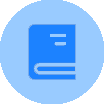
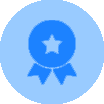
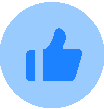