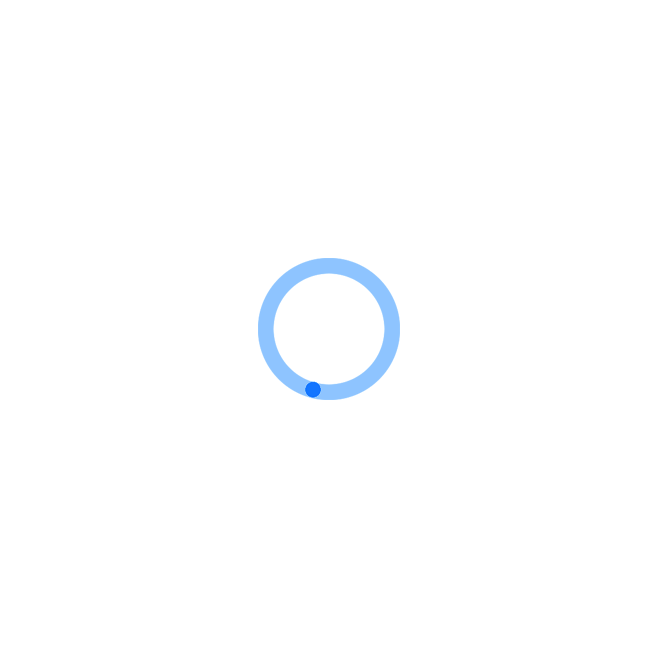
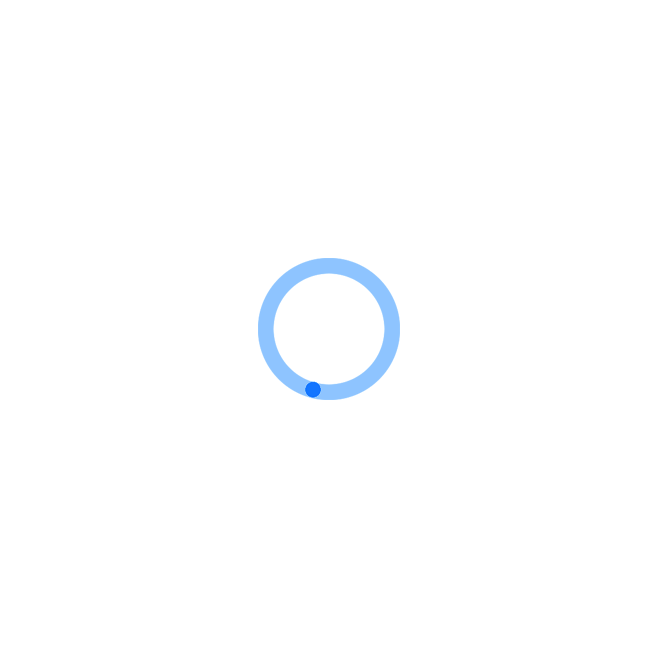
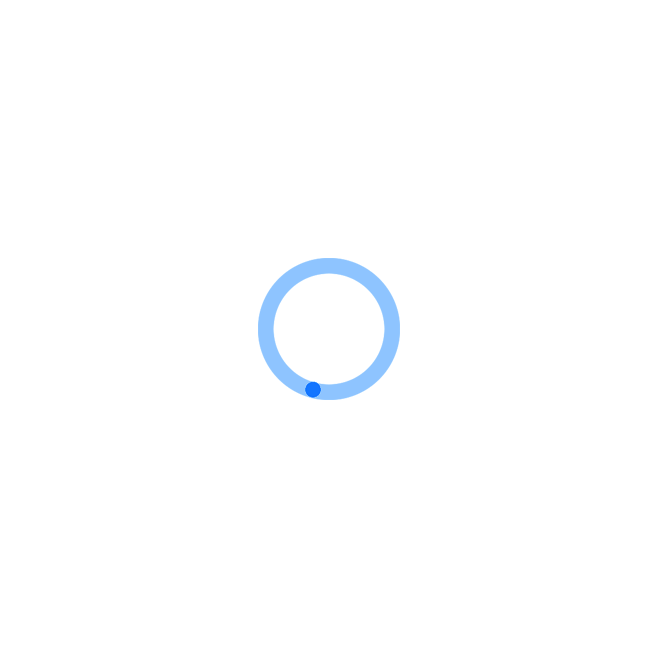
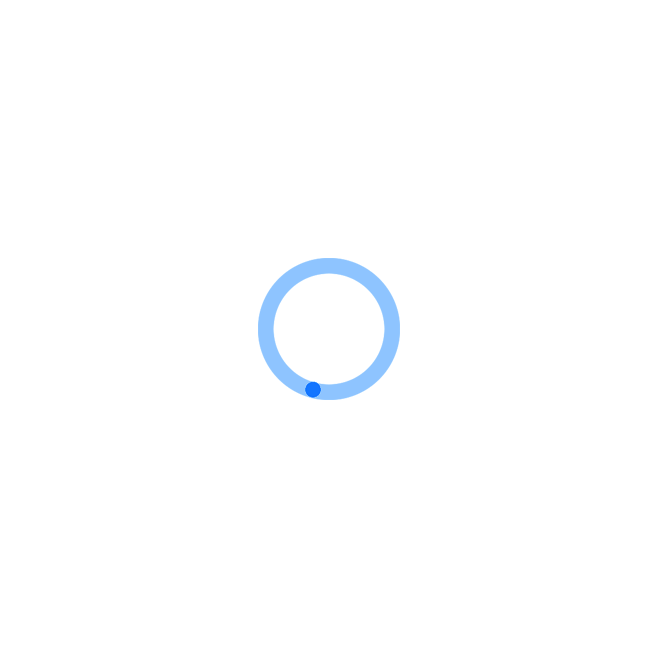
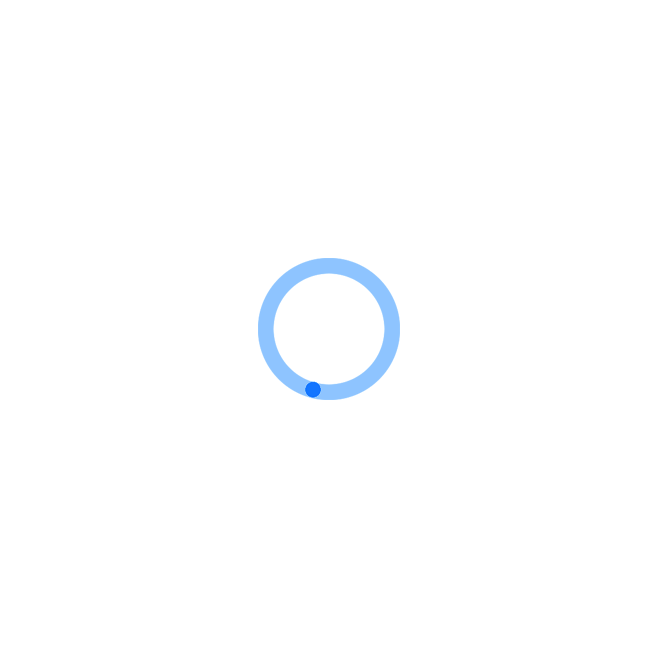
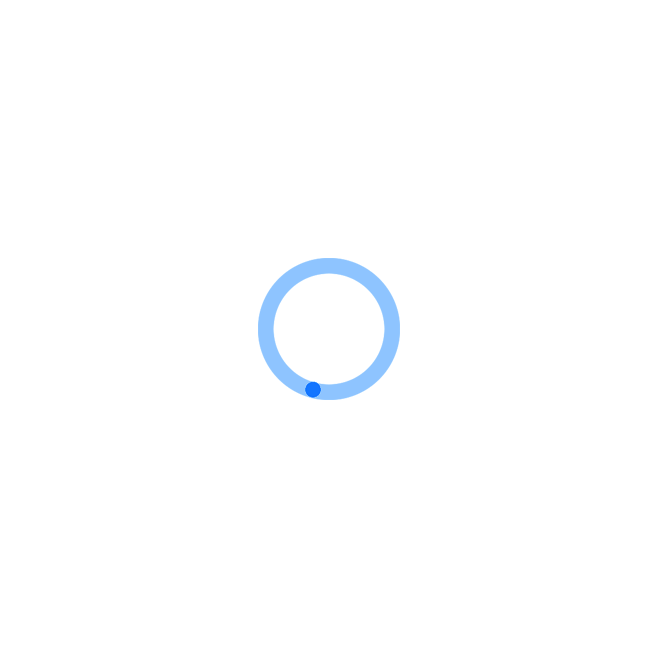
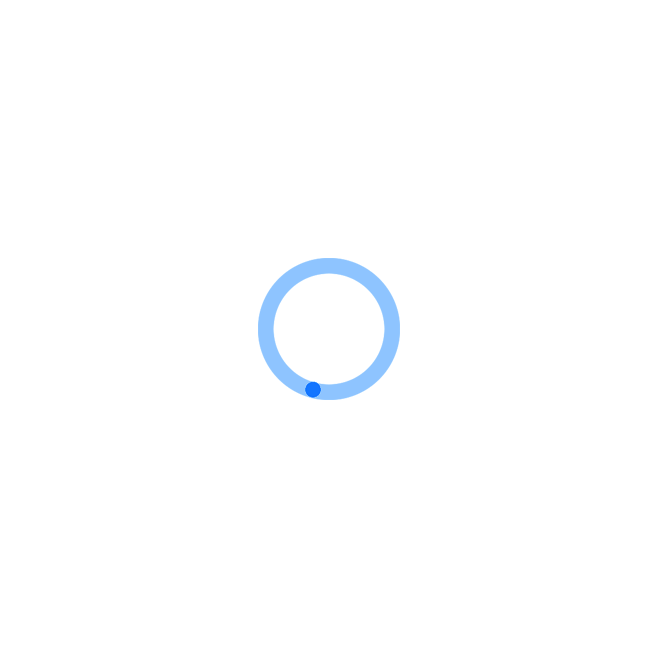
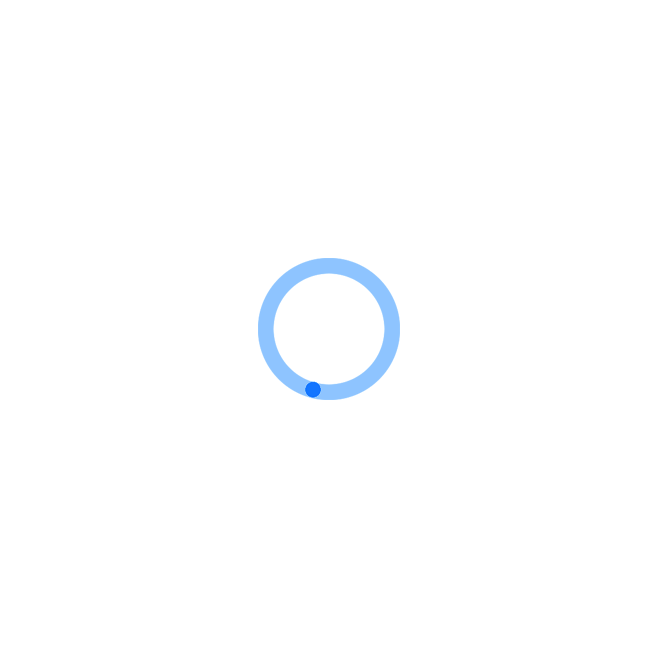
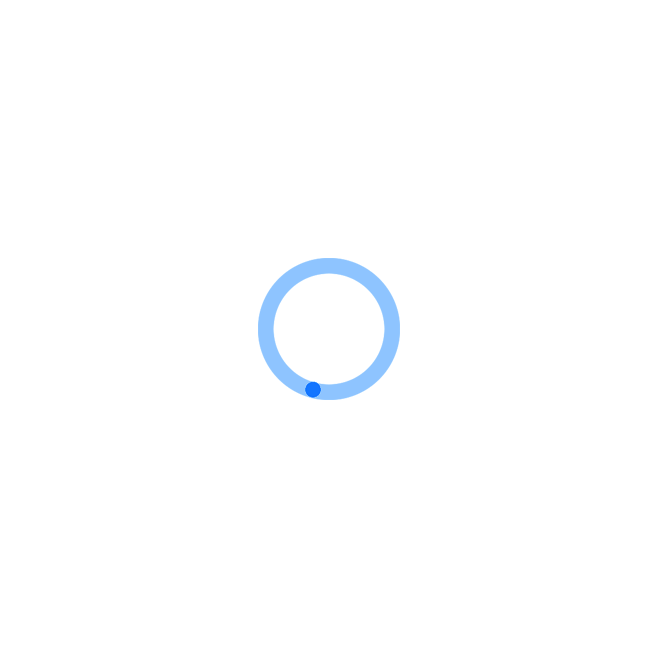
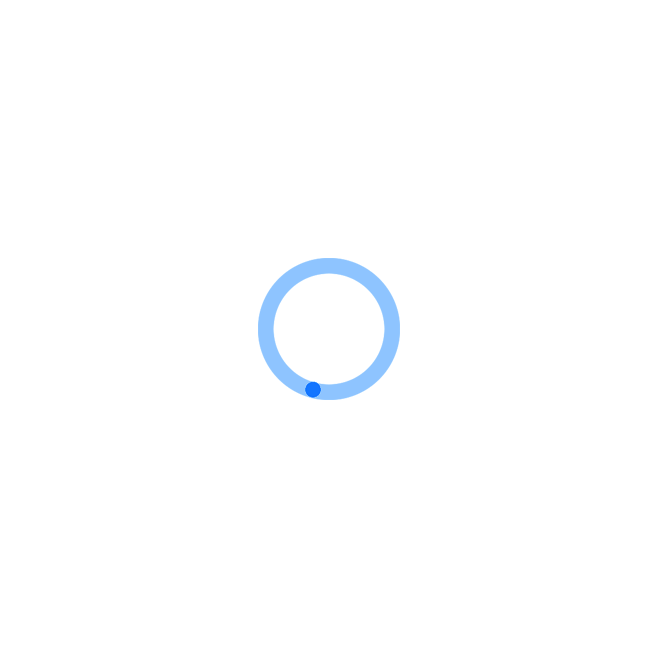
还剩40页未读,继续阅读
本资源只提供10页预览,全部文档请下载后查看!喜欢就下载吧,查找使用更方便
文本内容:
减压阀给定值来调节润滑油压,如润滑油压较高时,可经过适当开启高位油箱加油阀来降低油压,但必须保证高位油箱溢流管能够顺利回油
8、炉气总管真空的调节开大炉气阀门或关小窑气阀门能够提高总管真空度,关小炉气或开大窑气阀门可降低炉气总管真空一般情况下,为降压缩机进口真空,应将其中一个阀门全开(如炉气阀全开),经过开关另一阀门来控制真空度
9、电螺杆油压的调节经过控制油泵出口阀来调节油压,也能够调节回流阀来调节油压
10、背压汽并管网方法首先打开压缩二楼并汽总阀,然后一边开背压汽排气,一边关放空阀(两人配合完成)碳化岗位操作规程第一章碳化工序的生产任务本工序的生产以天然碱为原料制得的清碱液与窑气和炉气混合后的混合气在碳化塔内进行碳化反应制得合格的重碱液,重碱液送滤过工序生产重碱第二章工艺流程及指标
一、工艺流程由精制工序送来的清碱液经泵打入各碳化塔,混合气由塔底进入与清液逆流接触,其中碳酸钠与二氧化碳反应生成碳酸氢钠,由于碳酸氢钠溶解度较小,析出结晶形成悬浮液,反应方程式为Na2C03I+C02g+H20=2NaHC03s+Q该反应为放热反应,反应产生的热量经过冷却水箱由循环冷却带走,以达到合格的出塔液温度
三、主要工艺指标清碱液总碱以Na2c03计165-175g/l清碱液中NaHC03含量W30g/l清碱液浊度<30ppni清碱液温度70-75℃(冬季)65-70℃(夏季)混合气浓度40-60%混合气温度<40℃尾气浓度(C02):〈15%出塔液温度50-60℃循环上水温度<32℃循环水压力
0.3-
0.4MPa出塔液固液比:30-60%碳化转化率70-98%煮塔温度80-100℃碳化塔塔压
0.26-
0.32MPa混合气总管压力WO.38MPa
四、工艺流程简图第三章开停车操作
一、开车操作
(一)联系工作DCS操作工做好与外界联系工作,并做好内部各岗位间的协调指挥工作碳化操作工及时与主控室联系,做好开车前的准备工作
(二)开车前的检查工作
1、检查各润滑部位润滑是否良好
2、各安全设施齐全牢固,符合安全要求
3、各控制仪齐全完好,自调阀灵活好用
4、排除影响设设备运转的障碍物,并通知设备内及周围的人员离开设备
(三)开车步骤
1、按气体液体流向调节好各阀门的开关位置
2、接调度令后联系精制送液,开清液泵送清液进塔生产塔压升至
0.IMPa时通知压缩送气,打开塔底进气阀通气,同时继续进液
3、当塔压升至
0.28MPa时暂停进液.
4、调节进气流量,连续通气半小时以上,视塔的温度情况开始取出
5、调节好进液流量,使塔内液位及塔压维持稳定
6、根据出碱温度,调节好循环水量、控制尾气浓度在15%以下7
二、停车操作
1、与精制联系停止送液
2、停止进液进气
3、根据停车时间决定压塔或绶塔,如停车时间在4小时之内可直接停下,在八小时之内,可将固液比拉至10%左右后停车
4、停车后必须关闭冷却水
5、停车后必须将出碱管吹通
三、倒塔操作
(一)倒塔的目的碳化塔在生产过程中,由析出的结晶在菌帽、塔壁及冷却水管上逐渐结疤,使塔的有效容积减少,冷却水管换热效率降低,塔温升高,尾气中C02含量升高难以控制严重时会导致塔下部堵塞,无法生产,因此必须进行倒塔洗塔
(二)倒塔周期根据塔的运行情况,每塔的运行周期在72小时左右,洗塔时间为24小时
(三)倒塔前的准备工作
1、打开清洗塔倒塔阀,放空塔内洗水,排掉碱疤
2、通千压缩工序,注意压缩机排气压力
3、确保其它运行塔及清洗的塔的倒塔阀关严
(四)倒塔操作
1、生产塔停止进液,维持混合气量正常,打开两互倒塔的靠塔及倒塔阀进行自压,当两塔塔压相同时关生产塔尾气阀,打开新生产塔的进气阀
2、待塔压空后,立即关闭倒塔阀,关原生产塔进气阀,打开原生产塔放空阀,排掉塔内混合气,吹通塔根和出碱管,新塔开始取出,根据转化率的高低调整进气量,进入正常操作注意在倒塔前行检查新生产塔出碱管是否畅通,倒完塔后应吹通原生产塔各管线第四章岗位正常运行操作要点碳化岗位
1、及时执行主控室的各项指令,调整各艺指标在规定范围内
2、及时检查、维护所属设备、电器、仪表,发现问题及时报告值班长联系解决
3、经常检查所属管线阀门,保持畅通无泄漏,定期有蒸汽吹扫各管线
4、经常检查尾气压力,保证其在指标范围内
5、随时查看出碱口,掌握出碱情况
二、DCS岗位
1、掌握清碱液、母液、混合气的浓度、质量情况并及时与有关单位联系
2、做好碳化各项指标的监控工作,及进通知碳化岗位操作工进行操作
3、保持各塔塔压及进气量平衡,运行稳定
4、注意各操作参数的变化情况,控制好转化率及结晶固液比
5、根据生产负荷情况及塔情控制好取出速度第五章不正常现象的处理
2、检查内容⑴设备运转是否良好⑵电压是否稳定并达到要求⑶熔断装置是否合适⑷电机机油是否够用,声音是否正常⑸盘根是否漏水
3、检查方式⑴运行工对所有的泵两小时巡回检查一次⑵检修工每天下湖巡回查泵两次上下午各一次⑶值班电工每天检查电动机线路一次4负责观察水位的人员每天下湖观察水位一次⑸工段长每周全面检查两次,主要检查劳动纪律卫生,设备状况,操作程序,运行记录和交接班记录,工具管理等
4、巡架检查要求⑴严格、认真、细致地检查⑵要做到勤听、勤看、勤摸、勤处理⑶认真填写好巡回检查记录,做到工整、清洁、细致⑷对自己无力解决的问题及时向上反映,不得隐瞒或推托第六章岗位责任制
1、严格执行各种规章制度,保证顺利完成本班生产任务
2、要准确地遵守工艺制度和生产工序的一定顺序,遵守安全操作规程,安全生产责任制规章制度
3、凡盘根了漏水,必顺当班排除,否则不得交班
4、要求交班人在下班一小时之前,把各个泵巡回检查完,接班人在接班一小时内,把各个泵检查完确定各示运行是否正常,盘根是否漏水,凡在一小时内发生的故障,一律由交班人负责过滤工序操作规程第一章生产任务及管辖范围本工序的任务是将碳化工序送来的重碱液用真空转鼓过滤机进行固液分离,同时用洗水洗涤重碱中的盐分,得到水份、盐份合格的重碱本工序操作的好坏对纯碱的质量,产量及燃烧炉的正常操作有着很大影响,同时对降低水、电、蒸汽等的消耗也起着很大作用,因此,在操作中应严格控制各项工艺指标,确保操作平稳本工序的管辖范围包括过滤机、真空分离器、稠厚器、高位水槽、冷凝水储桶、真空泵、鼓风机、高浓母液泵、低浓母液泵、高浓母液桶、低浓母液桶、杂水桶、杂水泵等设备及其所属管道阀门和仪表等第二章生产原理及工艺流程
一、生产原理用真空泵将过滤机转鼓内抽成真空,滤布两面形成压力差,当滤鼓浸入含NHC03悬浮液中时,随着滤鼓转动,液体被抽走,固体重碱被吸附在滤布上经加水洗涤,压辐挤压吸干,最后刮刀卸料,得到指标合格的重碱
二、工艺流程概述自碳化塔来的NHC03悬浮液或制备返回母液进入稠厚器,高浓母液益流入高浓母液桶,送化灰中和工序,稠厚器底部的重碱液流入滤碱机,进行固液分离洗涤压紧得到的重碱由皮带机送往轻灰煨烧工序,滤碱机溢流液流入母液桶,打回稠厚器循环使用,真空分离器分离所得低浓母液进低浓母液桶,经低浓母液泵送往化灰中和工序,真空分离器气体由真空泵抽走,分离器液体进入杂水桶送往中和工序,真空分离器气体由真空泵抽走,分离器液体进入杂水桶送往中和工序、气体排空,滤碱机吹除滤布附着的滤饼,所用的吹风气由鼓风机供给,冷风进入缓冲罐后送入滤碱机
三、主要操作控制的工艺指标总真空度-
0.05Mpa吹风压力
0.
0150.03Mpa〜洗水温度250℃重碱水份W21%过滤损失<
1.5%重碱含NacKO.2%第三章设备的开停倒换方法及系统开停车步骤
(一)开碱车⑴做好准备工作(将开车的工具及安全防护用具等准备齐全)⑵检查碱槽内有无液体及杂物⑶检查各轴承、牙轮、搅拌机等传动机件设备是否完整正常,给油盅加好润滑油
(4)盘动电机靠背轮(转动几转)⑸试车,用合适的工具合电闸,戴上绝缘手套开电门或电器起动补偿器
(6)试车运转正常后,开启进碱阀门⑺碱槽内液面上升到二分之一以上时,依次开启吹风阀,洗水及真空阀门(两人协同操作)⑻根据滤鼓挂碱厚度,重碱盐份,水分及过滤损失的高低,适当调节进碱车碱液,洗水流量压滚压力,稳定操作
(二)停碱车⑴准备工具及安全防护用具⑵关闭碱车进碱阀门⑶当槽内碱液接近抽干时,迅速关闭真空阀门⑷开启洗车专用热水阀门,按照洗车操作步骤将滤布洗净
(三)倒换碱车
(1)按照开车操作步骤将要开的车开起来⑵开启新车进碱阀门,同时迅速关闭要停碱车的进碱阀门,然后按停车步骤停下要停的车(注意尽快倒换,缩短操作波动时间)
(四)开真空泵排烟温度150c给水压力
4.6MPa饱和蒸汽温度
256.7℃减温器调幅度15℃引风机额定风量132532M3/H引风机额定风压4629P鼓风机额定风量44000M3/H鼓风机额定风压10788Pa5—7#炉
1、工作原理利用燃料(煤)燃烧所放出的热量加热工质(水)生产具有一定压力和温度的蒸汽额定蒸发量75T/H汽包工作压力
4.22Mpa过热蒸汽压力
3.82Mpa过热蒸汽温度450℃给水温度104℃省煤器出口水温
195.3℃排烟温度150℃给水压力
4.6Mp饱和蒸汽温度
256.7℃减温器调幅度15℃
2、工艺参数引风机额定风量208555M3/H引风机额定风压7256Pa鼓风机额定风量125937M3/H鼓风机额定风压21249Pa除尘器处理烟气量1M3/Ho压缩工序第一节生产任务⑴准备润滑油和安全防护用具⑵给油盅注满润滑油⑶盘动电动机靠背轮(转动几转),打开轴封冷却水⑷开启真空泵放气阀门,打开工作液阀门,待溢流口有水时关闭⑸合开关,开电动机起动补偿器⑹开启真空泵工作液阀门⑺开启真空泵进气阀门,同时关掉放气阀门(边开边关)⑻根据真空抽气量,调节进出水阀门
(五)停真空泵⑴准备安全防护用具⑵开启放气阀门,同时关闭进气阀门⑶关闭进水阀门⑷停泵、关闭电门、拉下电闸
(六)倒换真空泵⑴按照开真空泵操作步骤,把将要开的泵开起来⑵新开的泵运转正常时,按照停真空泵操作步骤停下要停的泵
(七)过滤岗位的开工⑴根据碳化岗位开工时间和岗位职责分工做好开工前的工作,安全防护用品,油料,药品等准备工作⑵查明各碱车轴承、车轮、搅拌机、阀门、管线以及真空泵、电动机等机件设备是否完整无损,阀门所处位置是否正确,开车进行试车运转⑶试车正常以后,正式开动碱车和真空泵,鼓风机⑷接到碳化岗位开始出碱的通知以后,开启一台碱车的进碱阀,真空阀门、吹风阀门和洗水阀门,然后随着出碱量的增加,逐步提高碱车转速⑸滤布开始挂碱后,检查碱槽液体和真空度,调好碱槽液面高度,洗水流量和真空泵进水量,维持正常过滤操作
(八)过滤岗位的停工⑴根据停工计划和本岗位职责分工,做好停工准备工作⑵随着碳化塔出碱的减少,逐步减少开碱车和真空泵的台数,同时相应的减少燃烧洗涤液泵送液量⑶碳化塔完全停止出碱后,将洗水槽洗水放入碱车抽干,然后按停车、停泵步骤,停下最后一台碱车和真空泵应注意吹风阀门只能在鼓风机停车后,才能完全关闭第四章正常操作要点
一、维护指标操作
1、随时检查碱槽液面,调节过滤机进料量,保持液面不低,碱液不漾
2、经常检查洗水分布情况,消除水槽不平洒水不匀的现象
3、煨烧工序下碱岗位大量加用盘存重碱时,适当降低碱车重碱盐份
4、提高真空泵的抽气效率,防止真空阀门漏气
5、及时清洗碱车,消除滤布堵塞和漏气现象
6、发现漏气串气时,及时倒车,通知检修工进行修理
7、适当调节压辐压力,并保持其表面光滑,加压均匀
8、检查调节洗水温度,控制洗水温度在规定范围内
9、适当调节刮刀与滤鼓的距离(以铅丝1—3毫米为宜),发现距离过大或刀口磨损不平稳时,及时通知检修工进行调整和检修
10、加强同碳化工之间的联系,保证重碱结晶合乎要求
二、洗车的操作
1、开动备用碱车,开启冷风、洗水、真空阀门,试空车待运转正常后开进碱阀门,使之正常过滤
2、当碱液槽见液时,关闭准备清洗碱车的进碱阀门
3、检查滤布有无漏洞,机件有无毛病,利用洗车时间加以处理
4、当清洗车槽内水快满时,开启真空阀门抽干,然后重新关闭,连续进入洗车约15-30分钟
5、当滤布修补和机件水修均已毕后,按以上(1—5)项操作步骤倒车,洗另外一台车或停车备用
6、轮洗清洗各碱车完毕,及时恢复正常过滤操作
三、修补滤布的操作
1、发现滤布漏气漏碱时,如是一般小洞,可利用正常洗车时间进行修补,如果漏洞较大,过滤损失明显上升,必须立即准备倒车修补
2、准备修补滤布的材料(旧滤布)和工具(剪刀托棍等)
3、按洗车操作将备用碱车开启进碱、滤液,同时将要修补的车抽空洗净再由过滤工序巡检人员协调进行修补工作一个负责修补,一人负责开停电门
4、当滤鼓漏洞处转过最后一道压辐时,修补人员立即通知开车人员关闭开关将车停下,随时撬开漏处的铅丝,补上滤布,再用撬棍打紧该处铅丝,然后重新开车,当另一个漏洞转到适当位置时,再进行停车修补
5、按照第4项操作将所有的漏洞补好后,再行倒车或将该车停下备用
6、滤布使用日久,破漏严重无法修补时,则应立即倒用备用车,将破漏严重的碱车洗净后停下,通知检修工换新滤布第五章生产不正常现象的处理和设备故障处理
一、生产不正常现象原因和处理轻灰工序规程第一节生产任务及管辖范围
一、生产任务本工序以重碱为原料,经蒸汽煨炉分解制得合格的轻质纯碱,并回收炉气,供碳化制碱使用
二、管辖范围本工序所管辖范围包括两台轻灰蒸汽煨烧炉及其附属设备,串碱螺旋机、斗提机、轻灰转运刮板、轻灰成品刮板、炉气冷却塔、洗涤塔、洗涤液、冷凝液泵、重碱2#、3#、4#皮带机、储水槽、闪发器,以及所属管道、阀门、电气仪表等第二节生产原理及流程
一、生产原理重碱的主要成份为NHC03,另外还有Na2c
03、Na2s
04、NaCl和H20等轻灰段烧主要是经过蒸汽煨烧炉将重碱中的NaHC03分解,H20蒸发,以达到烧失量合格的轻灰重碱有粘结倾向,重碱水份三
9.5%就会形成碱球和结疤,因此在重碱进炉前与燃烧出的轻灰返碱在预混器内混合来降低水分,防止出现碱球和结疤,一般控制的返碱量为成品碱的
2.5倍,使混合碱水份W8%重碱与中压蒸汽经过加热管进行间壁式换热,温度加至120~140℃时,重碱开始分解,反应方程式为2NaHC03S—H20g+C02g+Na2C03S-Q
二、工艺流程重碱由滤过工序经1#、2#皮带输送机送至分配带,进入下碱口,经过下料器与返碱螺旋机及碱尘螺旋机送来的轻灰进入燃烧炉预混器,充分混合后进入轻灰煨烧炉,经蒸汽加热分解后由炉尾出碱阀出料,经出碱螺旋机送至返碱斜埋刮板机,其中三分之二由返碱溜子进入返碱螺旋机用作返碱,其余碱作为半成品或成品进入转运刮板、斗提机、水合刮板或成品刮板送至水合工序或凉碱炉重碱在炉内分解生产炉气(含有C
02、H20及部分碱尘)借压缩机抽力,从炉头出气方箱引出,经旋风分离器分离出大部分碱尘后,经过水封槽进入炉气总管,分离器分离出的碱尘由碱尘螺旋机送入预混器炉气在总管及水封槽内经循环冷凝液喷淋、洗涤剩余碱尘后,由炉气冷却塔顶部进入,在塔内被自下而上的循环冷却水间接冷却到40-60℃,炉气中的水蒸汽大部分被冷凝,冷凝液自塔底被冷凝液泵抽出循环洗涤碱尘,一部分由洗涤液泵抽出送往滤过,冷却后的炉气由冷却塔下部进入洗涤塔下部,经过补充水进行进一步冷却和洗涤,洗涤液由洗涤液泵送往滤过由电厂送来的中压蒸汽经过汽轴进入煨烧炉加热管,换热后产生的冷凝水进入冷凝水贮槽,冷凝水从贮水槽底部排出进入闪发器,闪发蒸汽进入重灰炉主蒸汽管或低压管网,冷凝水送重灰闪发器进行二次闪发
三、轻灰工序简图第三节主要工艺指标
一、温度
1、重碱温度>30℃
2、轻灰炉出碱温三190c
3、中压汽温度270330℃〜
4、轻灰炉气出气温度三105℃
5、冷凝塔出气温度V50C
6、洗涤塔出气温度V40C
7、冷凝塔循环上水温<32℃
8、冷凝液温度5065℃〜
9、轻灰闪发汽温度>192℃
二、压力
1、中压汽压力
2.
83.IMPa〜
2、炉头压力一10~-lOOPa
3、闪发汽压力
1.
01.3MPa〜
三、液位
1、冷凝塔洗涤液位8001200mm〜
2、贮水槽液位400600mm〜
3、闪发器液位500800mm〜第四节开停车方法及步骤
一、开车
(一)系统开停方法及步骤
1、开车前的准备工作⑴检查炉气系统,清理炉气管线及分离器内碱疤⑵检查各下碱溜子,保证其畅通,检查清理预混器的重碱下料器⑶检查蒸汽、冷凝水系统各阀门的开关位置
2、暖炉升压至工作压力
3、检查开启设备在暖炉过程中对设备进行仔细检查,确认无障碍时开启,具体开启顺序为水合刮板机或轻灰成品刮板一斗提机一轻灰转运刮板一预混器一返碱螺旋机一碱尘螺旋机一重碱下料器一返碱斜埋刮板机一出碱螺旋机f出碱阀f重碱皮带机开启设备必须按照以上顺序,防止运碱设备憋料
4、将冷凝塔洗涤塔投入使用,洗涤液冷凝泵开启
5、具备以上条件时,轻灰炉打快车,抽炉气,投入重碱煨烧作业二具体开停步骤
1、准备工作⑴检查煨烧炉及其附属各设备是否清理干净,各部件是否完整,电气设备是否良好,安全装置是否牢固⑵检查炉气管线是否清理干净⑶检查各仪表是否完整、齐全、有效4检查各处人孔盖是否盖好⑸检查煨烧炉各油泵油桶是否加满油,确认托辐底座齿轮底座和空气密封系统的油位符合要求后,启动油泵,向各润滑泵注油6确认密封用压缩空气压力符合要求,在向炉头炉尾的密封用气缸通气前,应先使密封处于张开位置,检查润滑油确实流入密封面后,经过压缩空气将密封环压紧⑺检查并确认炉内有足够底碱8确认仪表气压力达到要求,检查各自调阀是否灵活好用
2、暖炉升压⑴打开中压汽总阀及管线上导淋,确保进炉蒸汽阀关闭⑵通知电厂,暖管1小时⑶打开炉尾不凝汽排放阀⑷打开冷凝水贮槽主路各阀及顶部放空阀⑸关闭闪发器、出气阀和出水阀,打开异淋⑹当总管压力升至
0.8MPa,缓缓打开进炉蒸汽阀,使炉内压力不超过
0.IMPa,并关闭中压汽总管导淋⑺检查各管线及阀门汽轴有无泄漏⑻从燃烧炉进汽到升压不得小于1小时,具体暖炉时间分配如下:
00.IMPa1小时
0.TO.3MPa1小时
0.
31.OMPa1小时〜
1.0~
2.OMPa1小时
2.0~3MPa半小时⑼暖炉通汽前将轻灰炉慢车运行10当不凝汽排放口有大量蒸汽跑出30分钟后,关闭不凝汽排放阀n当冷凝水贮槽排污管有大量蒸汽冒出时,关闭排污阀12当闪发器压力升至
0.3MPa时,打开重灰炉并蒸汽管线上的导淋,打开闪发器并汽阀暖重灰炉生产轻灰时,当闪发器压力与管网压力相等时,打开并低压管网阀门13打开闪发器冷凝水排水阀,关闭各排污、导淋
3、设备开启⑴按照准备工作中设备开启顺序开启各设备⑵按以下方法检查和启动设备
①检查传动装置,电气安全装置是否齐全完好
②联系电工检查电气装置是否符合开车要求
③检查减速机、轴承、轴瓦的润滑情况,确保润滑良好
④检查各设备人孔,清理孔盖是否盖严
⑤确定设备周围无障碍物,以上准备工作在完成后,启动设备,空负荷运转
⑥当设备不能启动时,及时查明原因,联系电工及检修工处理
4、将炉气系统投入正常⑴向冷凝塔及洗涤塔补水⑵启动冷凝液泵、洗涤液泵⑶检查水封槽状况,将启用炉水封槽排水阀打开,补水阀关闭,炉气蝶阀打开⑷将备用炉水封槽排水阀关闭,水阀打开,确保其液封,并关压缩工序的任务是将窑气、炉气在兑气缸内混合,经螺杆压缩机压缩后为碳化工序提供合格的混合气第二节生产工艺流程
一、流程简述石灰窑产生的窑气经洗洗涤、冷却,再经静电除尘,使其含尘量降至20mg/m3以下,然后经窑气分离器分离出所携带的水,进入兑气缸,同时轻灰燃烧产生的炉气,经分离器进入兑气缸与窑气混合,压缩机轴入混合气,压缩后的气体经后冷器冷却至合格温度后,经分离器、分气缸进入各碳化塔
二、主要控制指标
1、压缩机进口真空一
2.
08.OKPa〜
2、排气压力WO.38MPa
3、混合气进气温度540℃〜
4、压缩给机排气温度<100℃
5、压缩机打气量290m3/min
6、机壳冷却水压>
0.2MPa
7、回油温度W60C
8、仪表气压力
0.05—
0.6MPa
9、轴封气压力^
0.43MPa
10、汽轮机进汽温度435C
11、汽轮机并汽压力.
3.2MPa
12、背压汽压力
0.391MPa闭炉气蝶阀⑸关闭启用炉分离器放空阀,打开伴热、蒸汽、回水阀⑹调节炉气总管蝶阀,检查其是否灵活好用
5、投碱作业⑴当轻灰炉各项准备工作已完成,碳化塔具备出碱条件时,将轻灰炉打快车⑵轻灰在炉内循环,当炉气温度达到HOC,出碱温到190C时,适当开启炉气总管自调阀,通知碳化能够取出⑶重碱下炉后注意监视各项指标,使其在规定范围内
二、停车
(一)系统停车方法及步骤当生产系统需要长时间停车时,按系统停车步骤进行停车
1、当碳化停取,碱车停止挂碱、重碱皮带机无碱后,联系调度室及电厂,调整蒸汽压力
2、停下重碱20分钟后,将轻灰炉打慢车,停抽或少抽炉气,停出碱阀
3、当返碱螺旋机无碱后,按以下顺序依次停下各运碱设备出碱螺旋机一返碱斜埋刮板一返碱螺旋机一轻灰转运刮板一斗提机f水合刮板机或轻灰成品刮板
4、停抽炉气,打开分离器放空阀,停碱尘较刀、预混器
5、逐渐降低进炉蒸汽压力(联系电厂)
6、当炉内蒸汽压力降至
0.5MPa时,关闭闪发器出汽阀
7、电厂切汽后打开贮水槽排汽阀,关闭闪发器出水阀,打开闪发器排污,中压汽导淋
8、当炉内压力为零时打开不凝汽排放阀
9、当炉体表面温度降至40℃,各部温度接近常温时,停下炉体
10、本岗位各设备停止后进行全面检查、清理
(二)临时停车
1、将轻灰炉打慢车
2、通知电厂降低蒸汽压力
3、利用自调阀调节进炉蒸汽压力
4、当有运碱设备自停时,必须按照停车顺序由前到后停下各运碱设备第五节正常操作要点
一、主控人员
1、密切注意蒸汽压力、温度、流量和重碱质量变化情况,根据出碱温度、炉气温度,通知岗位人员调整返碱量
2、注意炉头压力和炉气浓度,控制在指标范围内
3、注意监视冷凝水贮槽和闪发器液位,保持液位在指标范围内,发现异常及时处理
4、注意监视和控制洗涤塔、冷凝塔液位、水封槽液位,防止炉气液封
5、经常注意密封用压缩空气压力
6、加强与电厂联系,掌握蒸汽压力、温度、流量情况、重碱加减量时要及时与电厂、压缩联系
7、注意观察冷凝塔、洗涤塔出气温度,调整循环水及补水量
二、煨烧组长
1、经常与主控联系,了解各指标情况
2、定时巡检设备,检查电机温度及轴承润滑情况
3、观察各电机电流,不得超过额定电流
4、执行DCS操作工的指令,调节不正常指标巡回检查路线重灰返碱插板一重灰返碱较刀一串碱螺旋机一碱尘螺旋机f返碱螺旋机一返碱插板
三、下碱岗位人员
1、检查四楼下碱口是否畅通
2、经常敲击重碱溜子,确保其畅通
3、当煨烧系统故障,需要挡碱时,及时挡碱
4、按时检查水封槽、炉气管线喷淋情况,发现问题及时联系有关人员解决巡回检查路线重碱下料口一重灰炉气管线一炉气管线一水封槽一斗提机
四、司炉工
1、定时检查各运转设备运行情况,各轴瓦润滑情况,电机电流,了解设备负荷情况
2、每隔1小时开启一次油泵,使其运行半小时
3、经常查看轻灰炉主电机电流,掌握炉内存碱量情况巡回检查路线重碱下料器一预混器一托轮一主电机一炉尾一主蒸汽管线阀门一重灰炉尾一主蒸汽管线阀门一重灰主电机一各托轮一预混器一一水碱进料口一凉碱炉一主电机一出碱阀一水轴
五、泵工
1、定时检查冷凝液泵、洗涤液泵运行情况
2、检查冷凝水、闪发汽系统管线及阀门,发现跑冒滴漏及时联系处理
3、定时检查冷凝塔、洗涤塔运行,根据DCS操作工通知,调节冷凝塔循环水量巡回检查路线洗涤液泵一冷凝液泵一凉碱炉循环管线一重灰闪发器一贮水槽一重灰冷凝塔一轻灰洗涤塔一轻灰冷凝塔一轻灰闪发器一轻灰贮水槽
六、皮带工
1、经常检查润滑部位的润滑情况,并定期注油
2、经常检查主动辐、尾辐、坠辐、电动滚筒、减速机等温升、油面、振动和声音是否正常
3、经常检查皮带胶合处是否牢固可靠
4、经常检查皮带是否有跑偏或撕裂情况及调整
5、经常检查皮带周围是否有杂物并及时清理
6、经常保养尾辐、头辐丝杆,保证调节灵活
7、每小时巡回检查一次巡回检查路线重碱4#皮带f重碱3#皮带f重碱2#皮带f重碱1#皮带f水合1#皮带一水合2#皮带
七、刮板工
1、检查各刮板电流,了解其负荷情况
2、检查刮板传动链条、减速机、主链条运转情况
3、检查刮板各轴承润滑情况
4、当设备出现异常情况时及时通知检修及其它相关人员巡回检查路线轻灰转运埋刮板一轻灰斜埋刮板一轻灰成品刮板f水合轻灰刮板f重灰返碱刮板f凉碱埋刮板f3#轻秋线刮板重灰岗位操作规程第一章岗生产任务及管辖范围
一、生产任务本工序是以一水碱为原料,经蒸汽煨烧炉分别制得合格的重质纯碱;轻灰及重灰经凉碱炉或凉碱机冷却至5(T80c后送筛分包装工序进行包装
二、管辖范围本工序的管辖范围包括重灰蒸汽煨烧炉及其附属设备、重灰炉气系统、凉碱机、凉碱炉以及所属管道、阀门等第二章生产原理及工艺流程
一、生产原理重灰燃烧是利用低压蒸汽(
1.3Mpa)经过重灰蒸汽煨烧炉间接加热一水碱使其脱水,反应式为Na2C03-H20(S)Na2C03(s)+H20(g)t反应产物为重质纯碱(简称重灰)凉碱是利用循环水经过凉碱炉(凉碱机)与轻灰(重灰)间接换热以达到冷却的目的
二、工艺流程离心机分离出的一水碱经1#、2#一水碱皮带送入重灰炉预混器,与返碱螺旋机送来的返碱混合后进入重灰炉,经燃烧脱水后,由出碱阀出炉,经出碱螺旋机、斜埋刮板机运至煨烧三层,一部分经返碱溜子、返碱螺旋机进入预混器用作返碱,剩余部分进入凉碱埋刮板机送到凉碱炉或凉碱机,可经过控制插板,选择凉碱设备,轻重灰均可进入凉碱机或凉碱炉燃烧产生的炉气(水蒸汽及微量碱尘),借排风机吸力从炉头出气箱引出,进入炉气总管,经过循环冷凝液喷淋洗涤碱尘并降温,然后经旋流板除雾器除雾后排空
三、主要工艺指标
1、重灰炉出碱温度^150℃
2、凉碱机(炉)出碱温度W80℃
3、重灰炉出气温度^105℃
4、冷凝液温度50飞0℃
5、炉头压力0~-50Pa
6、低压汽压力
1.
01.3MPa
7、储水槽液位400600mm
8、闪发器液位100400mm〜
四、重灰工艺流程图
五、凉碱工序工艺流程图第三章开停车
一、重灰炉的开车
(一)煨烧炉开车
1、开车前的准备工作⑴检查煨烧炉、返碱螺旋机、重灰斜埋刮板机、出碱螺旋机、出碱阀、主电机等各部位是否完整,电气设备是否良好,安全装置是否牢固⑵检查煨烧炉内加热管是否清洁、光滑,各附属设备内有无杂物,各连接溜子是否清扫干净⑶检查炉头、炉尾气缸压紧的端面密封,所用压缩空气是否具备,端面密封开合是否顺畅、严密⑷检查各油泵油桶是否加满油,各减速机油位是否合乎要求⑸检查各电流表、温度表、压力表、流量计是否完整、齐全、准确、有效6暖炉前30分钟,启动排风机进行放空
2、暖炉升压⑴打开低压汽总管上的导淋⑵当轻灰炉闪发器压力升至
0.3MPa时,打开闪发器并汽阀低压暖管⑶打开炉尾不凝气排放阀4打开重灰贮水槽,闪发器排污,关闭贮水槽冷凝水排水自调阀,打开贮水槽放空⑸将炉体慢车运行6打开进炉蒸汽阀,让蒸汽缓缓入炉,待旋转接头汽室普遍温度达3050℃之后,逐渐加大汽量〜⑺当不凝汽排放阀有大量蒸汽排出30分钟后,关闭炉尾不凝汽排放阀8当储水槽的放空和排污管有大量蒸汽跑出并无杂物时,关闭储水槽放空阀,打开排水自调阀,关小排污9详细检查各部位温升情况,有无泄漏,确认无误后方可开始升压,从通汽暖炉到作业不得少于
4.5小时,具体时间分配如下压力MPa时间分钟0—
0.1N
900.1—
0.
32600.3—
1.
02601.0—
1.3与6010当闪发器压力抵压管网压力相等时,打开蒸汽并网阀,关闭排污、导淋11当生产稳定后,将储水槽、闪发器液位控制在指标范围内二附属设备的开车
1、准备工作⑴联系电工向电气设备送电2检查各运碱设备有无存碱⑶检查各减速机、轴承润滑情况4检查传动设备周围有无障碍物⑸将返碱插板全部打开
2、设备开启⑴各项准备工作完毕后,点动设备,确定无异常情况时⑵开启顺序预混器一返碱螺旋机一斜埋刮板机一出碱螺旋机一出碱阀⑶当设备点动不能启动时,应进行手动盘车,憋料或有异物卡死时,应通知检修工开盖处理⑷当某一运碱设备不能启动时,不得启动前一设备三冷凝塔、排风机、除雾器的开启
1、检查炉气管线是否清理干净
2、启动冷凝液泵后检查喷淋管线是否畅通
3、检查排风机附属部件,传动、电气安全装置是否齐全完好
4、检查旋流板除雾器,丝网除雾器是否清理干净
5、启动排风机
6、当一水碱进炉后打开冷凝塔上水、回水阀,控制排汽温度在指标值内
7、冷凝液、洗涤液泵的开启方法⑴检查泵周围有无障碍物⑵检查泵体各部件是否完整⑶确保塔内液位已加好⑷盘车是否灵活,泵内响声是否正常⑸通知电工检查、送电6打开泵进口阀、轴封冷却水⑺启动电机⑻泵转速正常后,缓慢打开泵的出口阀⑼调节出口阀,使其压力达到指标值
8、排风机的开启⑴检查设备周围是否有障碍物⑵检查备用风机进出口阀门是否关严⑶盘动叶轮、听叶轮与泵壳是否磨擦
13、润滑油压力
0.25—
0.3MPa
14、压力油压力
0.8MPa
15、冷油温度W40℃
16、压缩机经向瓦温<75℃
17、压缩机止推轴承温W80C
18、汽轮机径向瓦温W80C
19、汽轮机推力瓦温<80℃
20、滤油器压差
0.035MPa
21、汽轮机转速6067r/min第三节工艺流程解图第四节开停车步骤
一、汽轮机的开车
(一)开车前的准备工作
1、通知各有关岗位做好汽轮机的开车准备
2、打开汽轮机主蒸汽管线上的导淋,通知电厂送汽暖管
3、联系电工检查电气设备,并向电器设备送电,联系仪表工检查各仪表
4、启动油泵,调节压力油压力至
0.8MPa,润滑油压NO.25MPa
5、联系电工、仪表工做联锁试验,并将油泵联锁状态打至正确位置
6、检查各阀门开关位置,确保压缩机吸空、放空阀全开,背压汽放空全开4通知电工送电⑸通知主控打开进风管自调阀⑹打开排风门、进风门7起动风机二凉碱炉的开车
1、开车前的准备工作1检查凉碱炉以及附属设备是否清理干净,各机部件是否完整,电器设备是否良好,安全装置是否可靠⑵检查各电流表、温度表、压力表是否完整、齐全、准确、有效⑶检查凉碱炉及各运转设备周围障碍物是否全部清理⑷检查板式换热器、循环水、软水管线是否畅通,阀门是否灵活好用⑸检查软水泵是否备用6确定包装各运碱设备已全部启动7凉碱炉应在重灰炉启动之前启动
2、开车步骤1启动出碱螺旋机⑵启动主电机⑶启动进碱埋刮板⑷当凉碱炉进碱后,打开循环回水阀及循环上水阀⑸使用板式换热器时,打开换热器循环水时、进口阀,将软水罐加满水,启软水泵
二、停车一重灰炉的停车
1、系统停车顺序停进一水碱一炉打慢车一停出碱阀一出碱螺旋机一斜埋刮板机一返碱螺旋机一预混器停出碱阀口,全开返碱插板,待返碱螺旋机无碱后,按以上顺序依次停下各运碱设备
2、具体停车方法1停进一水碱后,保持返碱循环10分钟,控制出碱温度不低于150℃o2停快车,将重灰炉打慢车,停出碱阀⑶逐渐关小进汽,降低炉内压力4全开返碱插板,返碱螺旋机无碱后停各运碱设备⑸关闭进汽阀,当炉内压力接近常压时,打开炉尾不凝气排放阀,打开贮水槽放空及排污,打开闪发器排污,关闭闪发器出汽、出水阀6停排风机7关闭冷凝塔,循环、上水、回水阀
3、临时停车当设备发生故障或其它特殊情况下,需临时停车110分钟至4小时停车,停下一水碱,将炉体打慢车,停出碱阀,关小蒸汽阀,降低炉内压力⑵停炉4小时停车,停下一水碱,将炉体打慢车,停出碱阀,各运碱设备,将炉内压力降至
0.5MPa以下⑶停炉时间超过24小时,应按系统停车方法停车⑷煨烧炉自停,且慢车不能启动时,应将炉内压力放空
4、事故停炉⑴由于电源中断或设备故障等,煨烧炉无法正常运行时,应作事故停炉处理2联系水合,停下一水碱⑶事故停车应将炉体打慢车或手动盘车,防止炉体损坏⑷将进炉蒸汽压力降低二凉碱炉的停车
1、停止进碱后继续运行,直至炉内碱全部倒空
2、关闭循环上水、回水阀
3、停出碱螺旋机
4、停凉碱主电机第四章正常操作要点
一、主控人员
1、密切注意进炉蒸汽压力、温度及流量,调节其在指标范围内
2、注意炉头负压,保持其在指标范围内
3、注意炉气温度,通知燃烧操作工,调节返碱量
4、注意重灰及凉碱炉出碱温,使其在指标范围内
5、注意监视水槽及闪发器压力、液位,使其在指标范围内
二、煨烧操作工
1、密切注意一水碱来量及质量,联系主控了解炉气温度,及时调整返碱量
2、经常检查返碱螺旋机运动情况,返碱量的大小,杜绝无返碱操作
3、经常检查预混段的运转情况,发现进碱、出气不畅要立即联系清理,清理时要迅速,以减少波动
4、经常检查出碱阀及出碱螺旋机运行情况
5、炉内要有足够量的存碱
6、检查汽、冷凝水系统,及时联系消除各种跑、冒、漏
7、经常检查供油装置的运行情况,定时开启油泵,检查炉体齿轮啮合情况,滚圈、托轮、挡轮接触情况,保持轴承、轴瓦、链轮等传动部位润滑情况良好,减速机油位符合要求
8、经常检查端面密封情况,压缩空气压力尽可能控制在低限,以免端面磨损过快
9、电气装置保持完整、清洁有效
7、打开进出口消音器排污阀,放尽内部积水
8、打开后冷器及分离器排污
9、检查各注油点油压是否符合要求,将高位油箱加满油
10、做静态试验,速关阀试验
11、手动盘车3周
12、检查工艺气是否送上
13、联系调度送精制水
14、打开机壳冷却水
(二)汽轮机的开启
1、当蒸汽管线上导淋干水后,打开主蒸汽旁路,暖二段管
2、当蒸汽压力在
3.IMPa以上,蒸汽温度达到250℃以上时,打开主蒸汽阀,关闭旁路阀
3、将危急保安器挂闸,调整旋纽旋至最小,逆时针转动启动手柄当启动油压与速关油压相等时,停止旋转,观察速关阀是否打开,完成速关油与压力油的切换
4、继续逆时针旋转启动手柄,当调速汽门动作时,停止旋转调速汽门逐渐打开,汽轮机启动
5、及时联系电厂提高蒸汽压力
6、低速运转1020分钟后,将启动手柄旋至底,锁定手柄〜
7、打开轴封气,根据排气温度适当开启喷水
8、关闭蒸汽管线上的导淋
9、根据调度安排将背压汽并管网
(三)并入生产系统
1、适当开启螺杆压缩机回流
2、联系石灰窑,给静电除尘送窑气
3、打开窑气阀,关闭吸空阀
4、逐渐关小放空阀,提高排气压力
5、打开碳化塔进气,关闭放空阀,用回流阀调节排气压力
二、电螺杆的启动
(一)准备工作
1、通知各有关岗位做好启机准备
2、按照启动汽螺杆的
3、
4、
5、
6、
7、
8、
9、
13、
14、各步做启动电螺的准备工作
3、打开电机冷却回水、上水阀
4、启动盘车电机,盘车在10分钟以上
5、联系调度提高电压
(二)启动
1、停盘车电机,摘开盘车齿轮
2、点动电机
3、打开轴封气
4、根据非气温度调节喷水量
(三)并入生产系统(与汽螺杆并气方法相同)
三、停车
(一)汽轮机停机
1、将压缩机卸掉负荷,打开吸空排空阀,关闭窑气、炉气阀
2、降低转速,将背压汽放空,通知电厂注意蒸汽压力
3、将转速降至3000转/分钟,手动停机(危急保安器拉闸)
4、迅速关闭主蒸汽阀
5、关闭喷水轴封气
6、打开主蒸汽管线上导淋,通知电厂切汽
7、打开进出口消音器放水阀
8、转子停止转动后,根据油温和汽轮机温度情况,关闭或关小冷油器上水、回水阀
9、机壳冷却水继续通10分钟以上,油泵继续运行半小时以上
10、机组停车后1小时内,需盘车56次,每次盘车起始位置与〜最终位置应旋转180°,以后4小时内,每隔1小时盘车一次
(二)电螺杆的停机
1、卸掉压缩机负荷,打开吸空、放空、关闭窑气、炉气阀门
2、按停车按钮
3、关闭喷水轴封气
4、机壳冷却水及电机冷却水继续通10分钟以上
5、油泵继续运行半小时以上
6、启动盘车电机,每隔1小时盘车一次,每次10分钟,直至压缩机、电机温度正常
四、启动多台压缩机的并气当单台压缩机打气量不足或需要倒停时,需在生产过程中完成并气
1、关小新开压缩机的放空阀,逐渐提高排气压力
2、降低运行压缩机的负荷
3、打开新开压缩机的窑气阀、炉气阀
4、当新开压缩机的排气压力与分气缸压力相等时,打开分离器至分气缸阀门
5、根据生产需要均衡两台机组的负荷第五节正常操作要点
一、DCS操作工
1、注意观察压缩机的排气压力、进口真空度,保持在指标范围内
2、注意监视润滑油压力、温度,如有异常,联系操作工调整
3、注意观察汽轮机主蒸汽压力温度、背压汽压力,发现异常及时与调度室联系
4、注意监视汽轮机(或电机)、压缩机各轴瓦温度,发现异常及时处理
5、注意观察压缩机排气温度、来气温度、喷水压力,发现异常及时联系解决
6、根据生产需要,通知操作工调节打气量
7、注意监视轴封气压力,当低于排气压力时,及时联系调度调整
二、现场操作工
1、经常检查机组排气压力、排气温度,调节其在指标范围内
2、经常检查油系统,调节油温、油压在指标范围内,检查油系统是否漏油
3、经常检查油箱油位、润滑油质,发现问题及时报告
4、检查主蒸汽压力及背压汽压力,及时发现各种跑冒滴漏
5、滤油器的操作当滤油器前后压差大于
0.035MPa时,应进行滤油器的切换具体操作方法为先打开压力平衡开关,让备用的一个滤油器充满油,然后打开旁通管路,从排气口放气,直到油流出后关闭放气口,转动手柄进行切换,使备用的一个投入使用,然后关闭压力平衡开关,通知检修工清洗或检修替换下来的滤油器
6、冷油器的操作当冷油器热效果差或漏油时,需进行切换,具体操作方法为首先打开冷油器的各个进出口阀门以及排气阀门,直至油和水充满壳端和管端为止然后打开压力平衡天关,转动手柄进行切换在冷油器长时间使用的情况下,每天用10分钟开足进水阀,以最大流速经过管子,用以冲洗掉一些沉积物
7、油压的调节1汽轮机压力油的调节,经过控制运行油泵的出口阀来控制压力油压2汽轮机润滑油压的调节当压力油压调好后,能够经过调整。
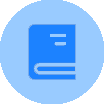
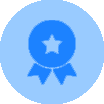
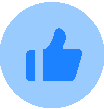