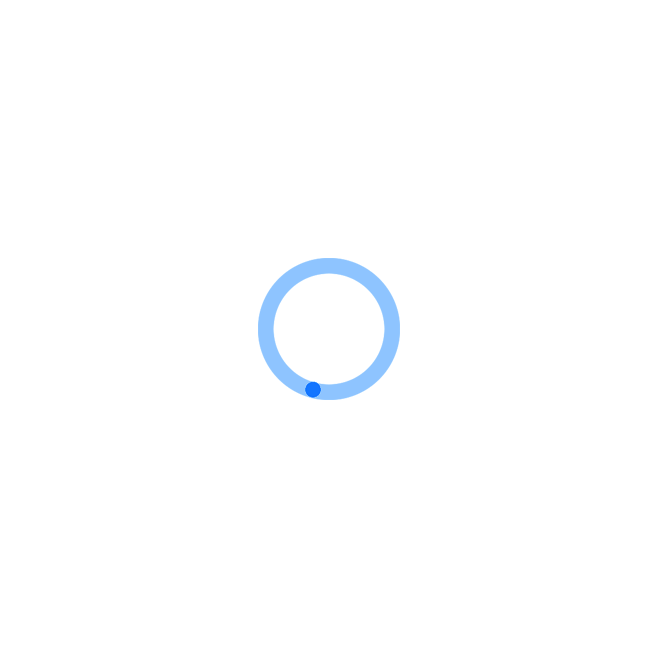
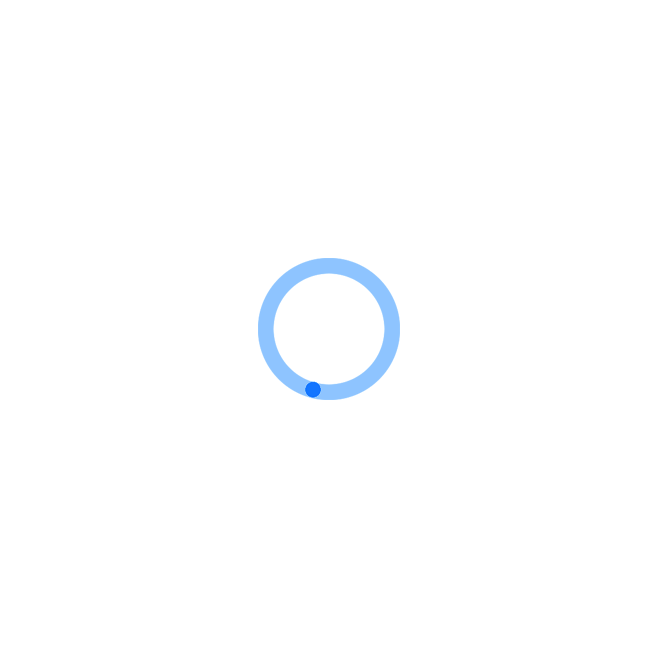
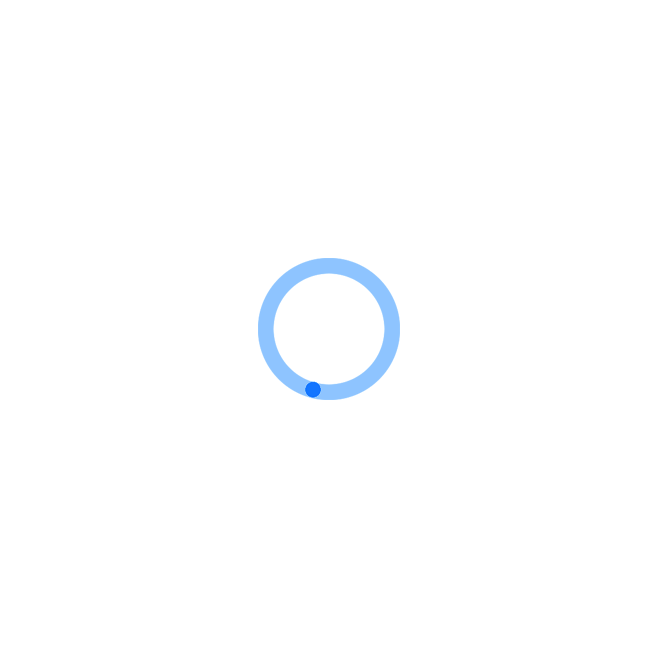
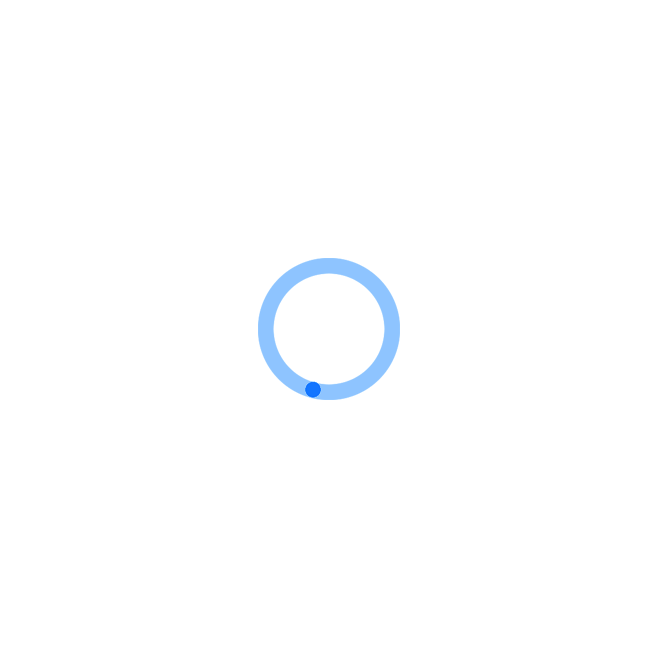
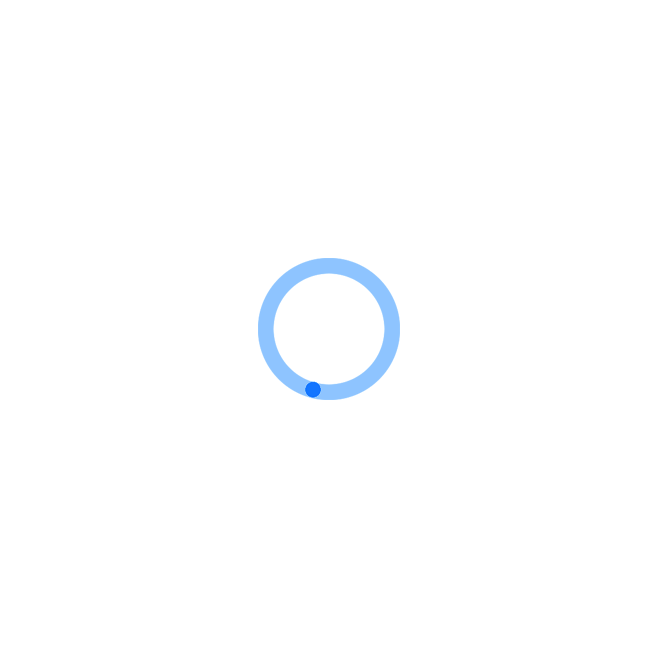
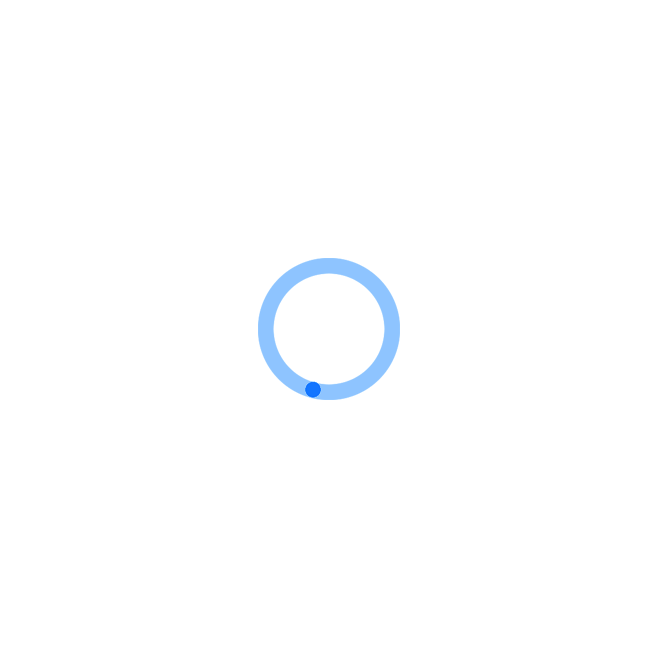
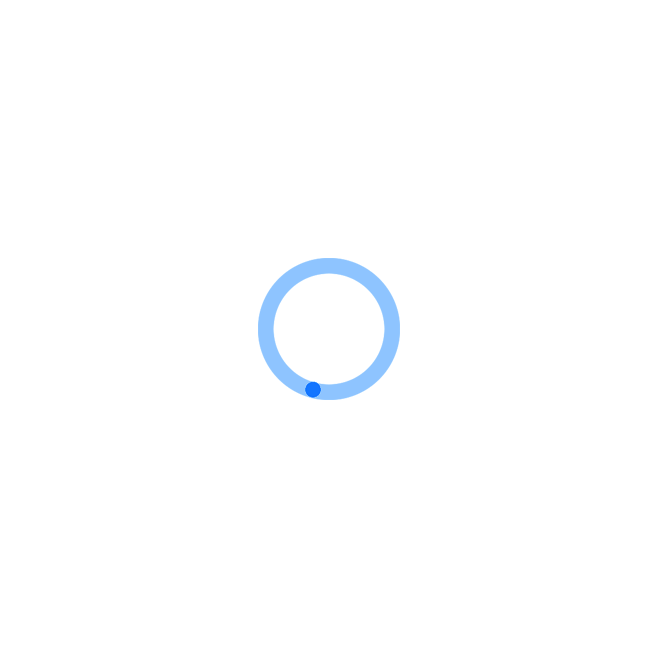
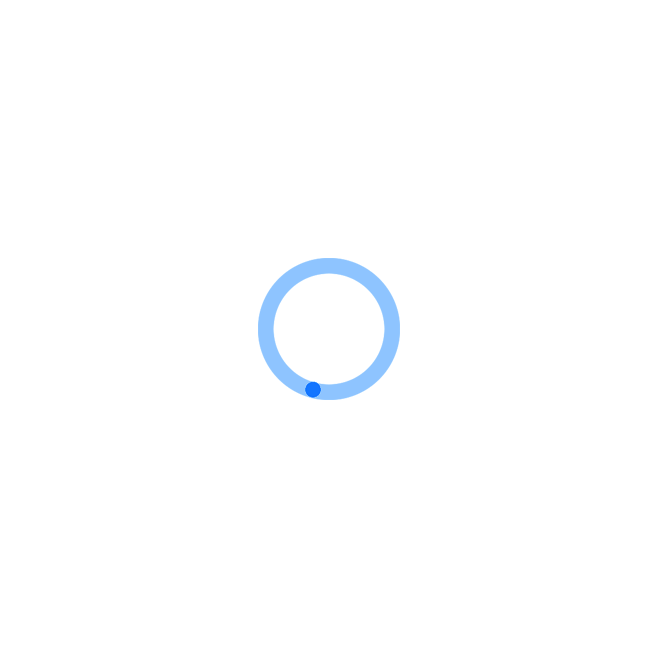
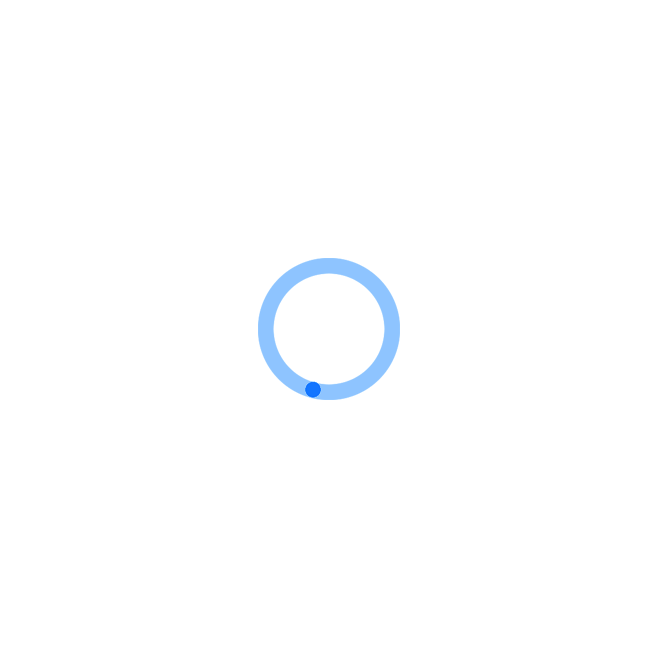
还剩7页未读,继续阅读
文本内容:
消除延迟焦化装置冷焦水系统恶臭--开发旋流除油技术组合工艺(中国石化镇海炼化公司)摘要该文经过对延迟焦化装置冷焦水系统恶臭现状的调查与分析,开发了旋流除油技术组合工艺,在国内首次实现了延迟焦化装置冷焦水系统的密闭处理实际应用情况表明,冷焦水的除油效果及冷却后的温度都达到了生产要求,周围环境也得到了明显改进,达到了消除恶臭的目的关键词延迟焦化装置冷焦水系统旋流除油技术消除恶臭1概况中国焦化装置的冷焦水处理系统普遍采用溢流式冷焦操作,以及隔油池、污油池等老一套处理设施,个别装置的冷焦水采用露天逐级沉降方式,这种工艺流程不但占地面积大、除油效率低,而且空气污染严重为解决以上问题,镇海炼化公司开发了冷焦水密闭循环处理工艺技术,该技术集成了液一液混合注水降温技术、重力沉降与旋流分离组合的焦粉一重油一水三相分离技术、空冷器密闭冷却技术处理冷焦水,实现了焦化冷焦水的密闭处理该技术的主要工艺过程从焦碳塔溢流而出的高温冷焦水,首先与部分低温冷焦水混合,使其水温低于100C进入密闭沉降罐,减少夹带油气的蒸汽挥发;污水在沉降罐中停留一定时间后,焦粉和油大部分得到沉降或上浮,达到初步净化分离经初步分离后的冷焦水还带有一定量的比重接近于水的焦粉以及悬浮油,进入旋流器进一步深度净化,从旋流器出来的含油水返回沉降罐继续分离,净化后的水进入空冷器冷却,再进入焦碳塔循环使用2旋流除焦技术组合工艺延迟焦化装置冷焦水系统恶臭产生的原因主要有凉水塔、隔油池油水混合气挥发多,冷焦水含油浓度高,恶臭严重;冷焦水温度高,冷焦水罐顶呼吸阀、泡沫产生器和液位计口冒油水混合气体,产生恶臭;溢流水进冷焦水罐温度高,产生水击,使管子振动大并拉裂金属软管及冷焦水罐壁焊缝,冷焦水外泄,产生恶臭;凉水塔换热降温效果差,延长了正常的冷焦时间,冷水塔油气挥发时间长;各冷焦水罐及冷焦水池无测量仪表和控制阀,冷焦水系统各工艺参数不易控制等为此,我们开发旋流除油技术组合工艺(如图2),以达到消除延迟焦化装置冷焦水系统恶臭的目的a污油耀油2000mg/L油100mg/L低温冷焦水2台串联预留2台塔顶冷焦溢流水—冷焦水罐—“热水泵提升—》旋流除油器_______________________________污油空冷器2片预留4片n焦炭塔冷y-冷水泵提<一冷水池.一水温965c〜_凉水塔一图2旋流除油技术组合工艺示意图1解决凉水塔、隔油池油水混合气挥发多,冷焦水含油浓度高,冷焦水池周围恶臭等问题针对冷焦水中油水混合气挥发多、冷焦水池周围恶臭等问题,我们分析认为产生这一现象的主要原因为冷焦水含油量高由于冷焦水与其它含油污水有明显的不同,在其组成中,初期为蒸气、含油污水、焦粉三相混合物,其中含油污水中油的密度达到
939.6g/cm3标准状态,与水的密度非常接近;焦粉中,多孔焦粉吸油减轻,部分焦粉密度小于水,混浮于油中,部分焦粉大于水,沉积在底部,部分焦粉与水比重相同,混浮于水中冷焦水中油浮升和焦粉颗粒沉降曲线见图3O根据水质特点,确定了贮罐重力除油除焦——旋流油水分离”两段除油除焦技术,即“油——水”和“液——固”混合物的重力沉降分离法其原理是利用两相比重差使分散的油颗粒脱离水体浮至液面,悬浮的固体颗粒沉降而分离油滴浮升速度和颗粒沉降速度符合Stokes定律对除油器来说,重力分离的效率依赖于正确的水力学设计,在给定流速的情况下,停留时间越长,效果越好因此,在给定上升气速的情况下,分离效率是几何参数的函数,流体的停留时间必须同油颗粒上升至液面时间相对应而对被处理水体来说,除油效率主要取决于水体中浮油含量根据这一原理,我们利用焦化装置原有的3个700m3冷焦水贮罐(贮罐内设有自动收油设施),温度较高的冷焦水进罐后,浮油大部分被去除,轻重焦粉分别被浮升和沉降去除,较好地实现油和焦粉的粗分离,初步除油除焦粉后的冷焦水再经冷焦水热水泵增压后进入后续的冷焦水旋流除油器,冷焦水中的分散油、乳化油经离心分离后,与贮水罐隔出的污油密闭进入污油罐,经脱水后污油全部回收除油后的冷焦水进入空冷器降温,并贮存于冷焦水罐,供冷焦水泵使用这样,实现了冷焦水的密闭循环处理,基本解决了冷焦水含油浓度高、油水混合气挥发多、冷焦水池周围恶臭等问题2解决冷焦水温度高,冷焦水罐顶呼吸阀、泡沫产生器和液位计口冒油水混合气体,产生恶臭问题针对这一问题,在国内首次采用了水一水混合器注水降温技术,即利用经空冷和冷水塔充分冷却后50℃以下的冷焦水经喷射泵直接喷入从焦炭塔顶来的温度较高的溢流冷焦水中,对溢流冷焦水进行冷却降温,使水温降至90C以下,基本解决了溢流冷焦水温度高,冷焦水贮罐顶呼吸阀、液位计口及泡沫产生器冒汽”,污染大气的环保问题3解决溢流水进冷焦水罐温度高,冷焦水夹汽产生水击,管子振动大,拉裂金属软管及冷焦水罐壁焊缝问题为解决这一问题,我们一方面对焦炭塔冷焦改溢流时的塔上部温度和塔顶压力等工艺指标进行了严格规定,防止将大量夹带水汽的冷焦水改入冷焦水罐;另一方面,对溢流水进冷焦水罐流程进行了改造,溢流水由原来从底部进罐改为从罐中部进,解决了溢流水进冷焦水罐温度高产生水击,管子振动大,拉裂金属软管及冷焦水罐壁焊缝问题4解决凉水塔换热降温效果差,冷焦时间长,凉水塔油气挥发时间长问题我们在冷焦水进冷水储存池前,设置了四片空冷,降低了进凉水塔池的冷焦水水温其中两片空冷是镇海炼化检安公司制造叠片式空冷,单位面积的冷却能力比翅片式空冷高出20%之后,运行2年,冷却效果保持较好,四台空冷的稳定运行使得装置在开工之后一直保持停用凉水塔状态,真正实现密闭冷焦5解决各冷焦水罐及冷焦水池无测量仪表和控制阀,各工艺参数不易控制问题为解决这一问题,我们将各冷焦水罐进、出罐大阀改为遥控气动阀,隔油池、冷焦水池、凉水塔池及冷焦水罐加装液位仪,在冷焦水系统增加流量及压力指示,并引入焦化DCS,真正实现了对焦化冷焦水系统的集中自动控制
3、成效分析
3.1投资和运行成本97年焦化装置冷焦水系统改造,增加了3个冷焦水罐及配套液位、温度监控系统,投资为355万元;7月增设旋流除油设备2台)、空冷器(2台)及与其相配套的泵、阀、管线等设计该项目共投资205万元,其中科研投入65万元,生产投入140万元在3月对冷焦水耀作了进一步完善改造,增加了两台蝶片式空冷和一组旋流器,改造技措费用130万,旋流器费用140万,总计270万元三次累计投资为830万该项目实施并正常投入生产后,仅四台15KWH风机及二台30KWH泵的动力消耗,与原凉水塔工艺相比,增加15KWH的动力消耗项目实施后的全年动力消耗
78.84万度电,按每度电
0.53元计,则全年运行成本为
41.78万元
3.2年经济效益本项目的效益主要体现在社会效益及环境效益该技术在镇海炼化公同焦化装置实施后,冷焦水油浓度低于150mg/l,焦粉浓度小于50mg/l,水温小于55C,操作可靠,占地面积小更重要的是,焦化冷焦水系统作业环境大为改进第一,改造前,焦碳塔排放冷焦水时,隔油池入口处蒸汽弥漫,散发出强烈恶臭,臭气浓度高达;改造后,高温冷焦水在管道混合器内与低温冷焦水混合降温后进入污水贮罐,罐顶呼吸口没有蒸汽逸出第二,改造前,高温冷焦水用泵打到凉水塔顶喷淋鼓风冷却,易挥发的有机物被不断吹脱、蒸发、逸散,形成一个影响范围较大的恶臭面源,改造后,从贮罐出来的冷焦水直接进入密闭的旋流器除油和密闭的空冷器冷却,有效地防止了有机恶臭气体的散发该技术实施后,也取得了一定的经济效益一是回收冷焦水中污油产生的效益二是减少凉水塔填料更换和风机维修费用10万元/年污染物削减量项目实施后,净化后冷焦水出口含油浓度在150mg/l左右,污水中所含的蜂类大为削减,且污水中的COD、硫化物、酚含量也大为降低具体见下表1表1冷焦水除油效果测定次数浓度范围平均浓度mg/L mg/L进水12249—60501306出水1245—273166去除率%//
87.3%同时,对焦化冷焦水系统的环境监测结果表明,实施冷焦水密闭处理工艺后,作业环境空气质量明显提高(见表2)o表2焦化冷焦水作业环境空气监测处理量/监测结果(除臭气浓度外)/mg•nf3工况监测点非甲烷烧H2s有机硫臭气浓度t•h-1改造前隔油池入口
3007806.
950.6测不出
1504102.58477隔油池入口测不出测不出测不出50~
100141.7改造后
15010.73测不出测不出测不出凉水塔旁测不出测不出50-
1004.2320旋流器旁测不出测不出测不出
1501.41测不出测不出测不出
1508.375结束语综上所述,冷焦水系统改造项目是成功的,并在国内首次实现了延迟焦化装置冷焦水的密闭处理,冷焦水的除油效果及冷却后的温度都达到了生产要求,周围环境改进效果显着,并很好地改进了焦化装置的工作强度及作业环境可是冷焦水系统敞口凉水塔未拔除,隔油池、冷焦水池未完全密闭,冷焦水中易挥发的恶臭污染物仍有部分被蒸发、逸散,形成恶臭源,有待于进一步的完善改造,准备在以后的大修中所有冷焦水池用水泥完全密封,原有的冷焦水池和冷焦水罐的恶臭气体改用接管与脱臭罐连接,排出气体经过脱臭剂床层催化剂脱臭后,在高处改有序放空,以真正实现冷焦水系统的全密闭处理,彻底解决延迟焦化装置冷焦水系统恶臭对周围环境的污染。
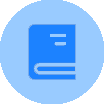
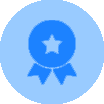
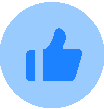