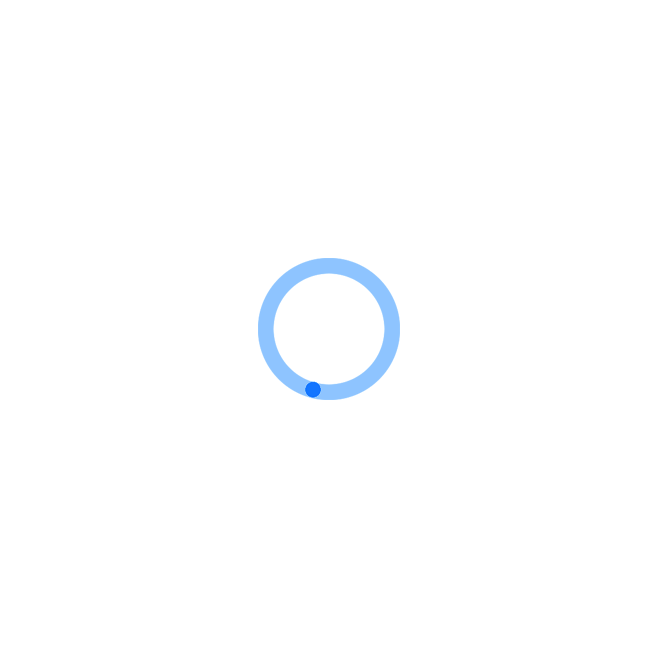
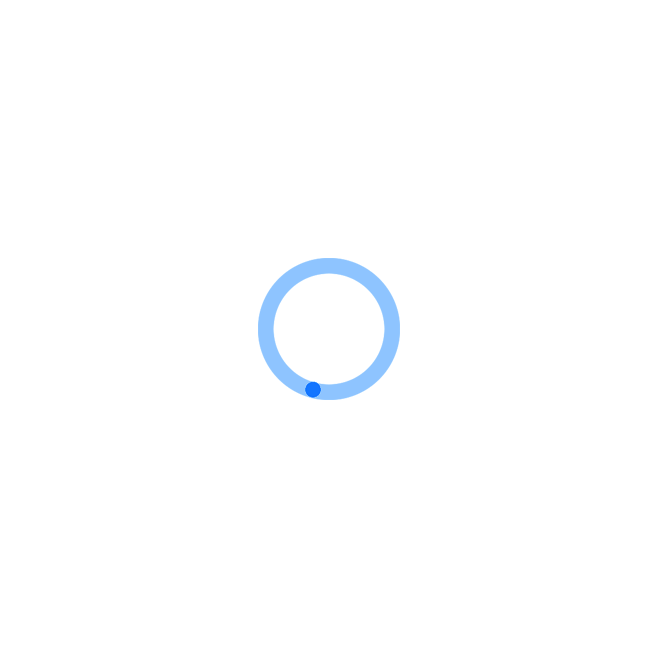
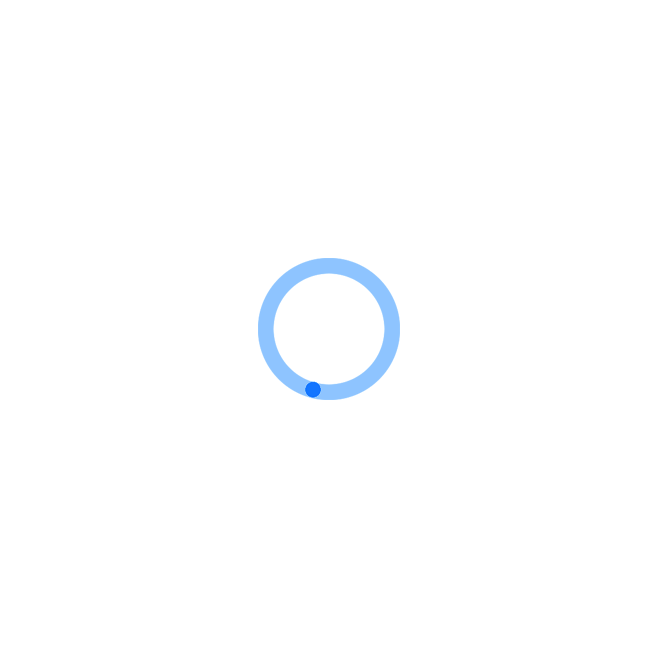
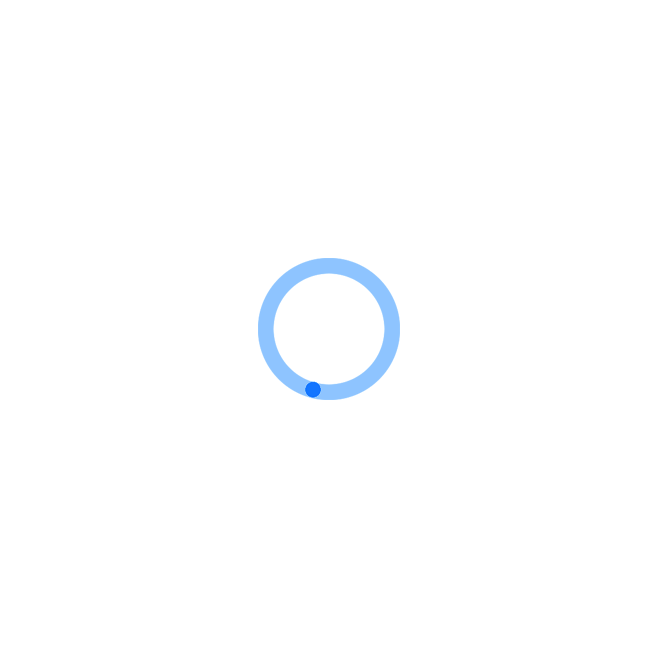
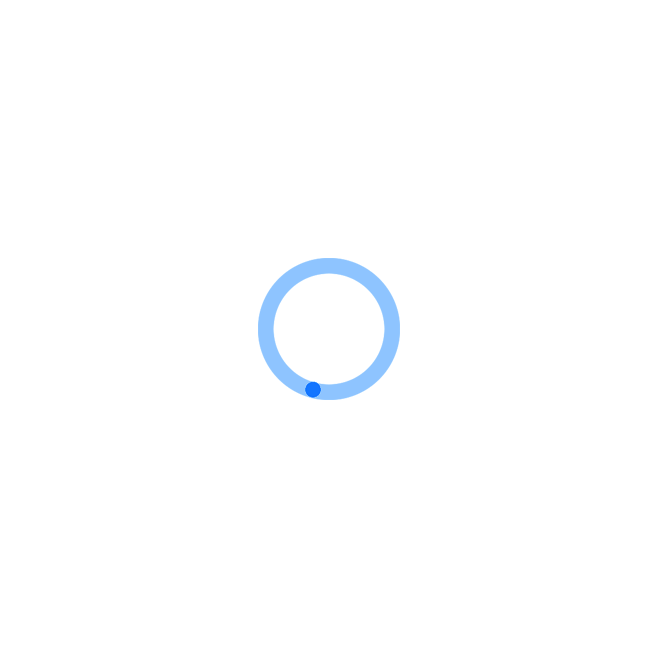
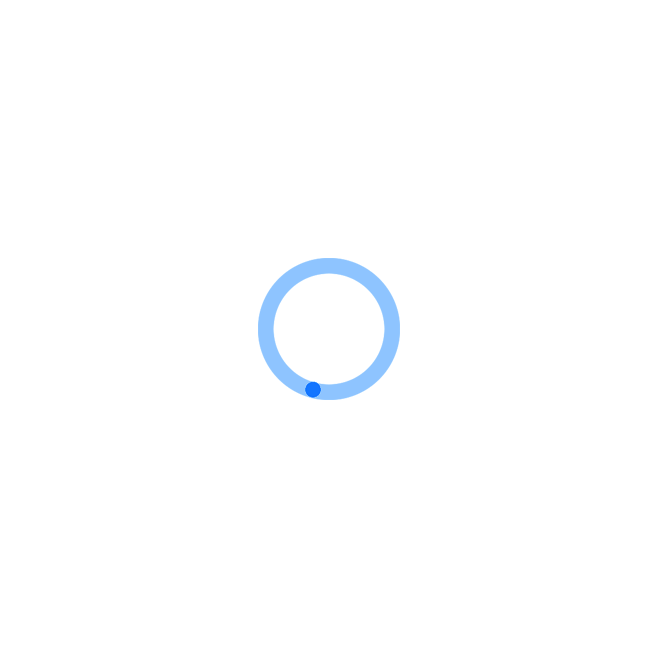
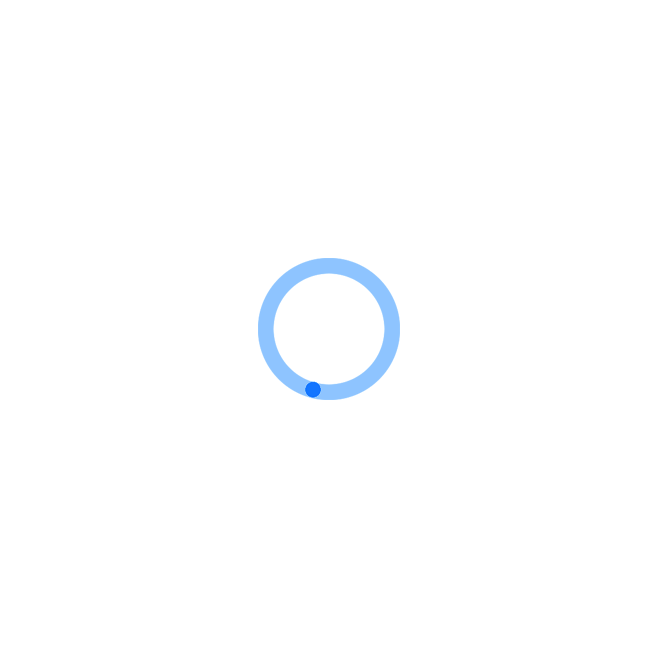
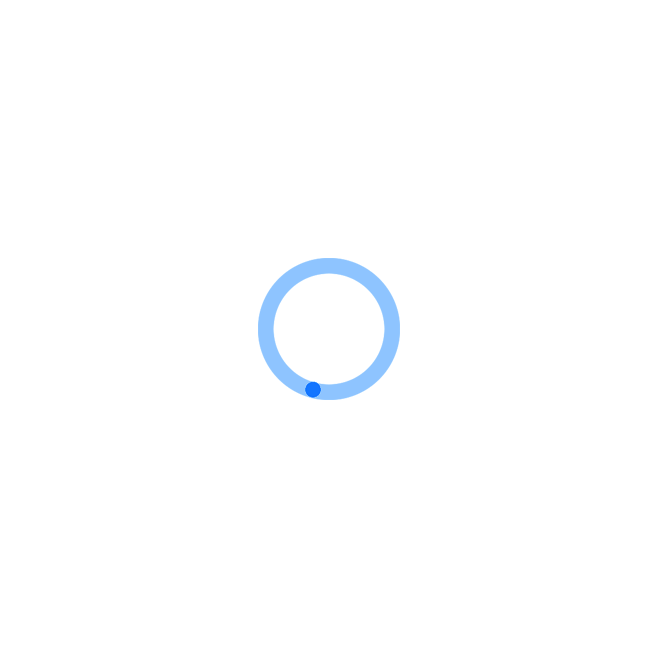
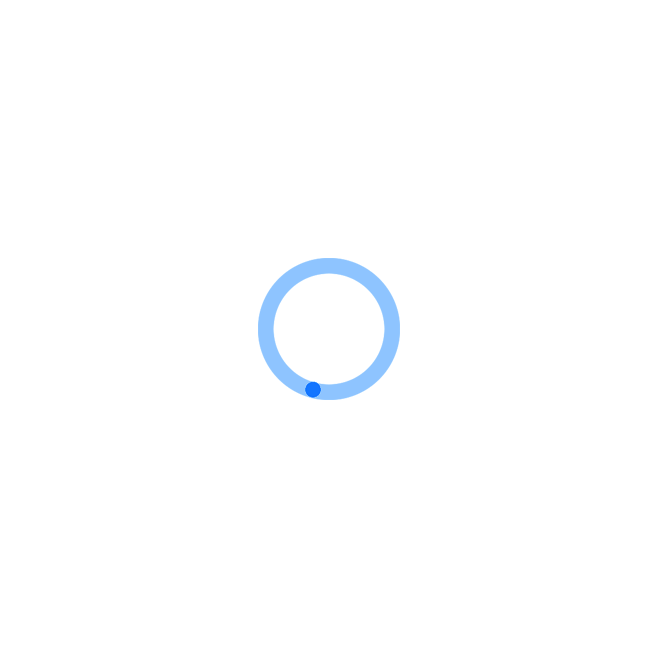
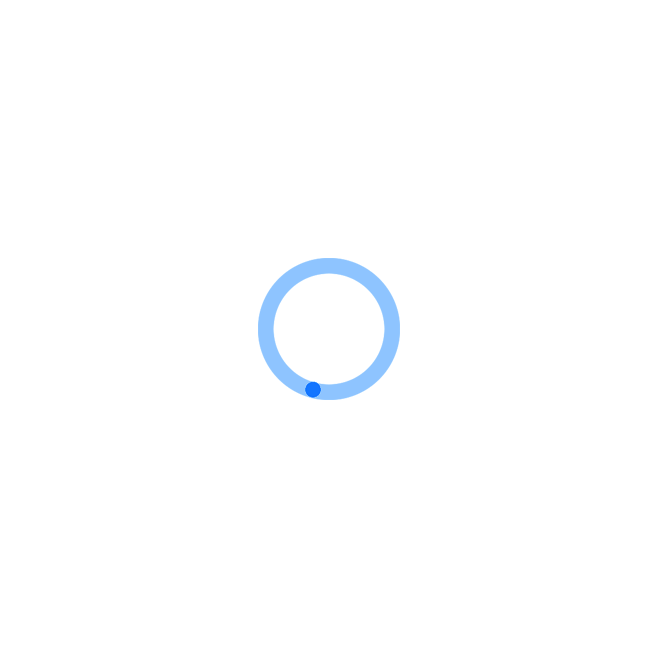
还剩10页未读,继续阅读
本资源只提供10页预览,全部文档请下载后查看!喜欢就下载吧,查找使用更方便
文本内容:
《材料成形工艺基础》
1.1区分以下名词的含义糊状凝固P8与同时逐层凝固P8与顺序凝固P14凝固P15缩孔与缩松P12液态收缩与凝固收缩P11逐层凝固纯金属和共晶成分的合金是在恒温下结晶的,铸件凝固时其凝固区宽度接近于零,因此铸件外层已凝固的固相区和内部尚未开始凝固的液相区之间被清楚的界面分开随着温度的下降,液相区不断减小,固相区不断增大而向中心推进,直至到达铸件中心顺序凝固是指在铸件上建立一个从远离冒口的部分到冒口之间逐渐递增的温度梯度,从而实现由远离冒口处向冒口方向顺序地凝固,即远离冒口的部位先凝固,靠近冒口的部位后凝固,冒口本身最后凝固糊状凝固如果合金的结晶温度范围很宽,或者铸件断面上温度梯度较小,则在凝固的某段时间内,其固相和液相并存的凝固区同时凝固是指采取一定的工艺措施,尽量减小铸件各部分之间会贯穿铸件的整个断面的温度差,使铸件的各部分几乎同时进行凝固液态收缩从浇注温度冷却至凝固开始温度(液相线温度)期间发增加成本,若采用特殊工艺来生产,会降低生产率,增加成本
3.9对于冲裁件、弯曲件和拉深件,在形状设计上有何特别要求P141P132P1431)冲裁件的形状冲裁件的形状应力求简单、对称,并尽可能采用圆形、矩形等规则形状,避免长槽和细长悬臂结构(图
3.74),避免设计成非圆曲线的形状,并使排样时废料最少在冲裁件的转角处,除无废料冲裁或采用镶拼模冲裁外,都应有适当的圆角2)弯曲件的形状弯曲件的形状应尽量对称,弯曲半径应左右一致,保证板料受力时平衡,防止产生偏移当弯曲不对称制件时,也可考虑成对弯曲后再切断3)拉深件的形状拉深件的形状应力求简单、对称,尽量采用圆形、矩形等规则形状,以有利于拉深其高度应尽量减小,以便用较少的拉深次数成形
4.5气体保护焊的主要特点是什么?P157常见的保护气体有哪些?P1551)明弧焊接,便于观察、操作和控制2)适合于各种空间位置的焊接,易于实现机械化和自动化3)电弧在气流压缩下燃烧,热量集中,焊接热影响区较窄,焊接变形小4)焊接电流密度大,熔深大;焊接速度快,焊后不需清渣,因此生产率高5)焊接设备和控制系统较复杂常见的保护气体常气和CO
4.6氮弧焊焊接生产有何特点?其应用范围如何?P157答氧气价格贵,焊接成本高氮气是惰性气体,它不与金属起化学反应,又不溶于金属液中,是一种理想的保护气体,能够获得高质量的焊缝因此氮弧焊保护效果好,且焊缝成形好氮弧焊主要适用于焊接化学性质活泼的金属(铝、镁、钛及其合金)、稀有金属(错、铝、祖及其合金)、高强度合金钢、不锈钢、耐热钢及低合金结构钢等
4.7CO2气体保护焊有何优缺点?其应用范围如何?P157优点CO2气体价廉,成本低,其焊接成本仅为焊条电弧焊和埋弧自动焊的40%左右COZ焊焊缝含氢量低,因此焊缝的裂纹倾向小缺点CO是一种氧化性气体,在高温时会分解,使电弧气氛具有强烈的氧化性,使焊件金属和合金元素烧损而降低焊缝金属力学性能,而且还会导致飞溅和气孔,焊缝成形较差C02焊主要适用于焊接低碳钢和强度等级不高的低合金结构钢,也可用于堆焊磨损件或焊补铸铁件,不适于焊接易氧化的非铁金属和高合金钢C02焊当前广泛用于造船、机车车辆、汽车制造等互业生产
5.4影响粉末烧结质量的因素有哪些?并简述这些因素是如何影响粉末制品质量的P196烧结过程中,制品质量受到多种因素影响,主要有烧结温度、保温时间、保护气氛等
①较高的烧结温度可促使粉粒间的原子扩散易于进行,从而提高烧结体强度与硬度,但过高的温度会导致粉粒表面氧化、晶粒粗大或压坯变形,产生过烧现象
②烧结保温时间也影响制品质量,可视具体情况根据经验确定一般来讲,保温时间长,有利于原子扩散,孔隙减少,密度增加;但保温时间过长,也会导致粉粒的氧化,对于液相烧结,可能还会使液相从压坯表面渗出
③为了防止压坯氧化,烧结一般是在保护性气氛或真空连续式烧结炉内进行,常见的保护气体有氢、分解氨、发生炉煤气及惰性气体等
5.9简述陶瓷烧成与冷却过程中四个阶段的变化P207在加热烧成和冷却过程中,一般有以下四个阶段变化1低温阶段室温300cc残余水分的排除,无化学反应〜2分解及氧化阶段300950C粘土等矿物中结构水的排除,有〜机物、碳素和无机物等的氧化,碳酸盐、硫化物等的分解,石英由低温晶型转变为高温晶型此阶段是烧成的关键阶段3高温阶段950℃烧成温度上述氧化分解反应继续进行,各〜种液相形成;同时,各组成物逐渐溶解,填充在固体颗粒的间隙中,在固一液表面张力的作用下坯体的气孔率下降,进而使坯件的密度增大最后晶体被液相所粘结,而烧结成瓷4冷却阶段烧成温度一室温液相过冷为玻璃相,残余石英发生晶型转变,坯体强度、硬度及光泽继续增大生的收缩凝固收缩从凝固开始温度到凝固终了温度(固相线温度)期间发生的收缩铸件在凝固过程中,由于合金的液态收缩和凝固收缩所造成的体积缩减,如果未能获得补充(称为补缩),则会在铸件最后凝固的部位形成孔洞大而集中的孔洞称为缩孔,细小而分散的孔洞称为缩松
1.2什么是液态合金的充型能力?P10它与合金的流动性有何关系P10化学成分不同的合金为什么流动性不同P9流动性不好对铸件的质量有何影响P10在实际生产条件下熔融金属是否能够顺利充满型腔,从而获得轮廓清晰、形状完整的铸件,这种能力被称为合金的充型能力流动性好的合金充型能力强,流动性差的合金充型能力也差同种合金中成分不同的合金具有不同的结晶特点,其流动性也不同合金的流动性好,不但有利于充型,而且有利于金属液中的气体和非金属夹杂物的上浮排除,有利于对金属凝固时产生的收缩进行补缩合金的流动性差,铸件就容易产生浇不到、冷隔、气孔、夹渣和缩孔等缺陷
1.3拟生产一批小型铸铁件,力学性能要求不高,但壁厚较薄,试分析如何提高合金液的充型能力答1)尽可量提高浇注温度由于壁厚较薄,铸铁可取1450左右2)增大充型压力(即增大推动力)3)选用蓄热能力强的材料作铸型4)提高铸型温度5)选用发气量小而排气能力强的铸型
1.4冒口补缩的原理是什么?冷铁是否能够补缩?冷铁的作用与冒口有何不同?在铸件厚壁处和热节部位(即铸件上热量集中,内接圆直径较大的部位)设置冒口,是防止缩孔、缩松的有效措施冒口的尺寸应保证冒口比它要补缩的部位凝固得晚,并有足够的金属液供给采用”顺序凝固原则”,在铸件上建立一个从远离冒口的部分到冒口之间逐渐递增的温度梯度,从而实现由远离冒口处向冒口方向顺序地凝固,即远离冒口的部位先凝固,靠近冒口的部位后凝固,冒口本身最后凝固,不能够冷铁是用以增加铸件某一局部的冷却速度而安放在铸型内的金属激冷物
1.7既然提高浇注温度能够增强合金的充型能力,为什么又要防止浇注温度过高?P10浇注温度不宜过高,否则金属液吸气增多,氧化加剧,而且使合金的液态收缩量增加,不但充型能力提高不多,反而增大了产生缩孔、气孔、粘砂、晶粒粗大等缺陷的倾向因此,每种铸造合金都有一定的浇注温度范围L8什么是冷变形和热变形?冷变形和热变形对金属的组织与性能有哪些影响冷变形加工和热变形加工各有何优缺点?P22P23在再结晶温度以下(一般是在室温下)进行的塑性成形加工,称为冷变形加工一般把在再结晶温度以上进行的塑性成形加工称之为热变形加工,如热锻、热轧和热挤压等
(1)冷塑性变形后金属组织的特点.1)晶粒变形随着塑性变形变形量的增加,能够看到金属内部的晶粒沿变形方向被压扁或拉长2)位错密度增加和晶粒碎化未变形的晶粒内一般已存在一定数量的位错,并经过部分位错的特定排列构成亚晶界3)形变织构
(2)冷塑性变形后金属力学性能的变化1)各向异性纤维组织的形成和形变织构的出现,均使金属的性能产生各向异性,这对于塑性成形加工是不利的2)冷变形强化随着塑性变形程度的增加,金属的强度和硬度显著提高,而塑性明显下降,这一现象称为冷变形强化,也称加工硬化3)产生残余内应力由于金属塑性变形中存在不同层次和不同程度的变形不均匀性,使金属在变形后形成宏观范围和微观区域(如晶粒内部或晶粒之间)的多种残余内应力热变形对金属组织和性能的影响热变形加工能消除铸态金属的某些缺陷,如使气孔、缩松焊合,使粗大的柱状晶粒或树枝晶破碎并再结晶成为均匀的等轴晶,改进第二相的形态与分布,减小成分偏析等,从而使金属材料组织致密,晶粒细化,成分均匀,力学性能提高由于冷变形加工是在再结晶温度以下(一般还低于回复温度)进行的,金属在变形过程中只有冷变形强化而无回复或再结晶软化,因此所需变形力很大,且变形程度也不宜过大,以免降低模具寿命或使工件开裂冷变形加工的生产率较高,其产品具有表面质量好、尺寸精度高等优点,一般不需要再切削加工(冷变形优缺点)由于金属的热变形一般都在远高于再结晶温度以上进行,软化过程大于强化过程,因此金属具有较好的塑性和较低的变形抗力,这样金属在热变形时可获得较大的变形量,而耗能较小用热变形方法可加工尺寸较大或形状复杂的工件,并能改进金属的组织与性能但由于变形温度高,金属表面易形成氧化皮,工件表面质量和尺寸精度较低(热变形优缺点)i.n根据你所学的知识说明趁热打铁”的意思和道理P25随着温度升高,金属原子活动能力增强,原子间结合力减弱,使塑性提高和变形抗力减小当温度高于金属的再结晶温度后,变形过程中的强化作用可被动态再结晶软化所消除因此,对大多数金属来说,随着温度的增加,总的变化趋势是塑性提高,变形抗力下降,如果经过加热可使原为多相组织的合金发生相变而转变为单相固溶体组织,则对提高其塑性成形性更加有利
1.12什么是金属的超塑性P26超塑性成形有什么特点P26金属这种在特定条件下表现出的超常的塑性变形能力称为超塑性超塑性成形时金属不会发生加工硬化,也不会形成各向异性和残余应力
2.2什么是熔模铸造试简述其工艺过程P44熔模铸造是用易熔材料制成模样,造型后将模样熔化并排出型外,从而获得无分型面的型腔,经浇注后获得铸件的铸造方法熔模铸造的工艺过程其主要工序包括蜡模制造、制造型壳、失蜡、焙烧和浇注等1)蜡模制造把熔化成糊状的蜡料压入压型,待冷凝后取出,就得到蜡模2)制造型壳将蜡模或蜡模组浸入由水玻璃和石英粉配成的涂料浆中,使涂料均匀地覆盖在蜡模表层,然后在上面均匀地撒一层细石英砂,再放人硬化剂(氯化镂溶液)中硬化结壳3)熔去蜡模将包有蜡摸的型壳浸入8595℃的热水中,〜使蜡料熔化并从型壳中脱除,从而在型壳中留下型腔4)焙烧型壳在浇注前必须在800—950C下进行焙烧,其目的是去除型壳中的水分、残余蜡料和其它杂质,洁净型腔5)浇注为了提高合金的充型能力,防止浇不足、冷隔等缺陷,一般在焙烧后随即就趁热(600700℃)进行浇注〜
2.3金属型铸造有何优越性为什么金属型铸造未能广泛取代砂型铸造P47金属型铸造的特点1)金属型造好后,其铸造的工艺过程实际上就是浇注、冷却、取出和清理铸件,从而大大地提高了生产效率,改进了劳动条件,而且易于实现机械化和自动化生产2)金属型内腔表面光洁,刚度大,因此铸件精度高,表面质量好3)金属型导热快,铸件冷却速度快,凝固后晶粒细小,从而提高了其力学性能可是,金属型的制造周期长、成本高,铸造工艺要求较严格,不宜生产大型、薄壁和形状复杂的铸件,铸铁件还容易产生白口组织金属型铸造主要适用于大批量生产的非铁合金铸件,如铝活塞、气缸体、缸盖、油泵壳体以及铜合金轴瓦、轴套等有时也用于形状简单的中、小型铸铁件
2.5什么是离心铸造?它在圆筒形铸件的铸造中有哪些优越性P49离心铸造是将熔融金属浇人高速旋转的铸型中,使其在离心力作用下填充铸型并结晶,从而获得铸件的方法离心铸造的优点是1)离心铸造可不用型芯而铸出中空铸件,工艺简单,生产率高,成本低2)在离心力作用下,提高了金属液的充型能力,金属液自外表面向内表面顺序凝固,因此铸件组织致密,无缩孔、气孔、夹渣等缺陷,力学性能提高3)便于铸造“双金属”铸件,如制造钢套铜衬滑动轴承4)不用浇注系统和冒口,金属利用率较高
3.1何谓自由锻,它在应用上有何特点P90与自由锻相比,模锻有哪些特点P92自由锻是只用简单工具或在锻造设备的上、下砧之间,使金属坯料受力变形而获得锻件的工艺方法自由锻的特点及应用自由锻工艺灵活,所用设备和工具有很大的通用性,且工具简单;生产的锻件范围大,可锻造不到一千克至质量达几百吨的锻件;但生产率低,工人劳动强度大,对工人技术水平要求较高;锻件精度低,且只能锻造形状简单的工件模锻的特点及应用与自由锻相比,模锻有如下特点1)生产效率高模锻时金属变形在模膛内进行,故能较快获得所需要的形状2)模锻件尺寸精确,加工余量小,表面光洁,节约材料和切削加工工时3)能够锻造形状比较复杂的锻件可是,由于受模锻设备吨位的限制,模锻件质量不能太大,一般在150kg以下,而且因为模锻设备投资大和锻模制造成本高,因此只适合于大批量生产
3.6自由锻件的结构工艺性有哪些要求?自由锻件上为什么不允许出现凸台、肋条和斜面?P139考虑到自由锻设备和工艺的特点,自由锻件结构的设计原则是在满足使用性能的前提下,锻件的形状应尽量简单、规则,易于锻造
1.避免锥体或斜面结构
2.避免以空间曲面相交的结构
3.避免加强肋和凸台等结构
4.合理采用组合锻件锻造具有锥体或斜面结构的锻件,需制造专用工具,锻件成形也比较困难,从而使工艺过程复杂,不便于操作,影响设备使用效率,应尽量避免如果出现凸台、肋条,难以用自由锻成形,。
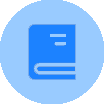
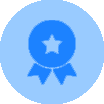
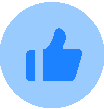