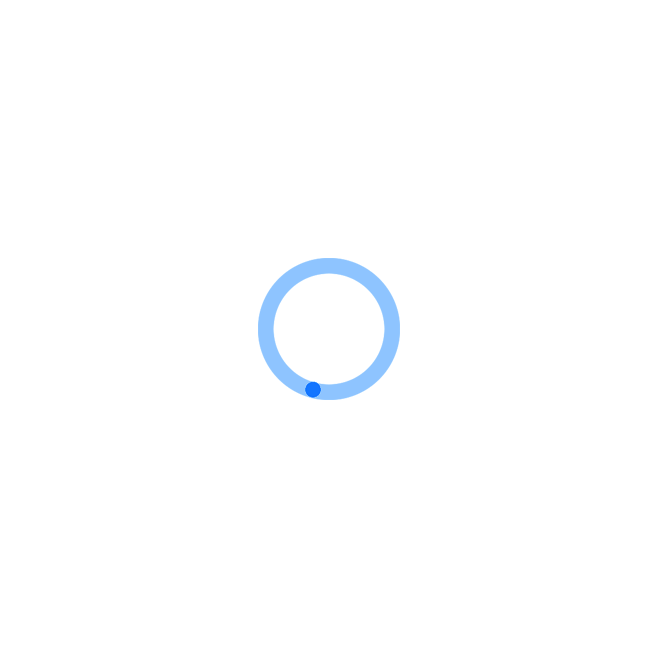
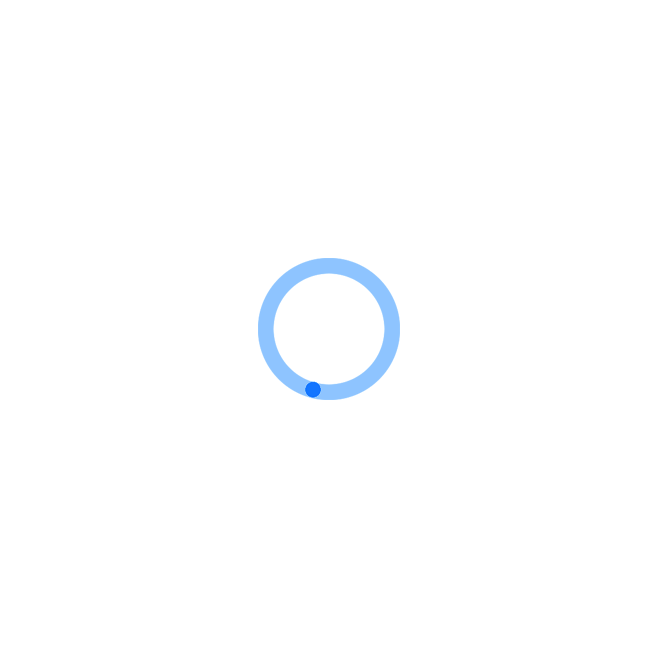
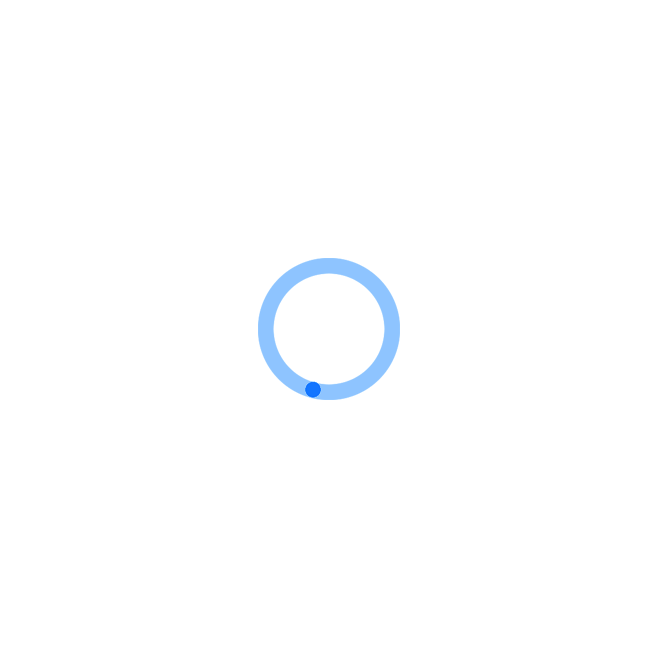
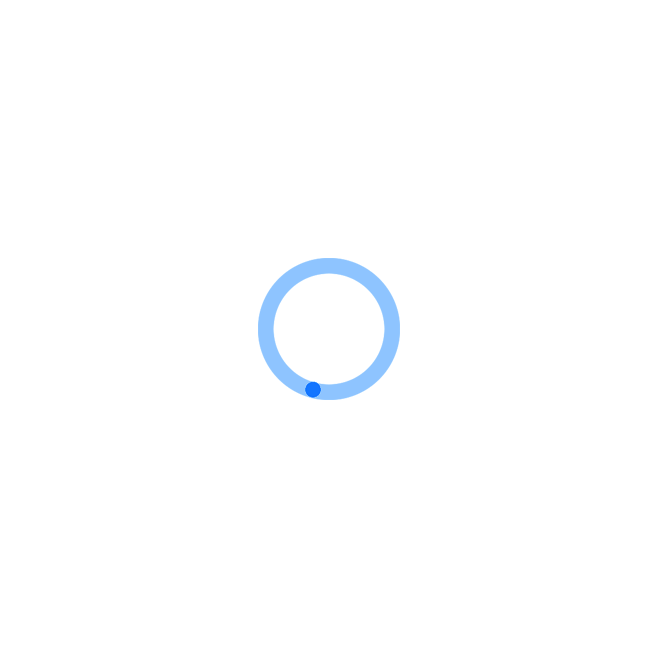
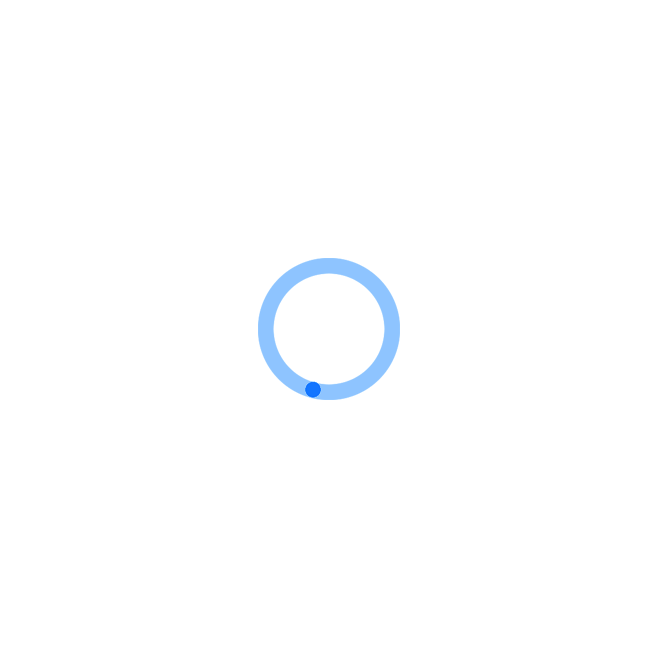
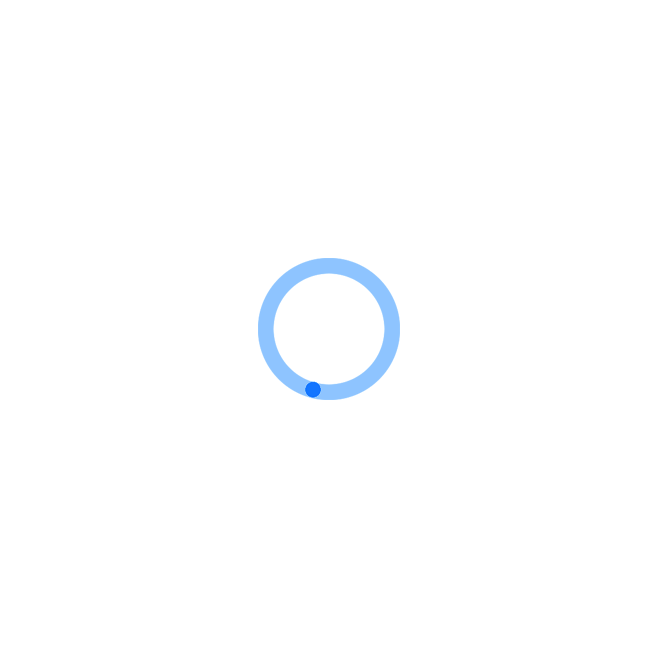
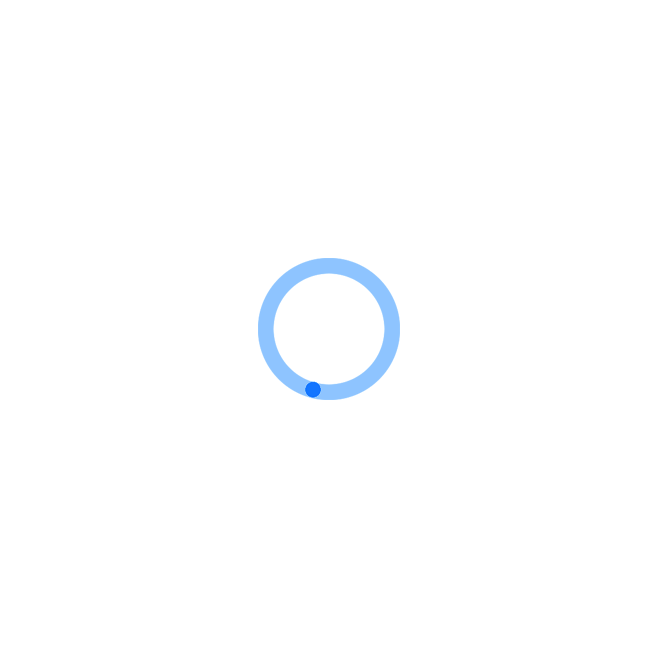
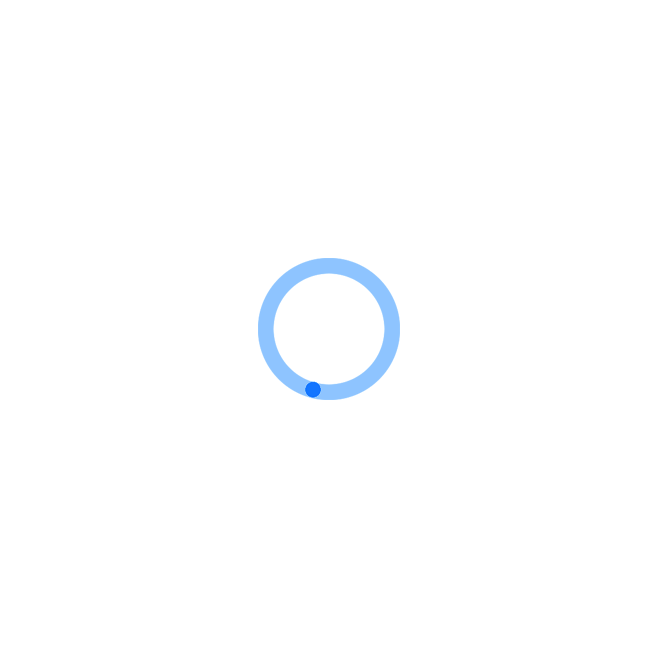
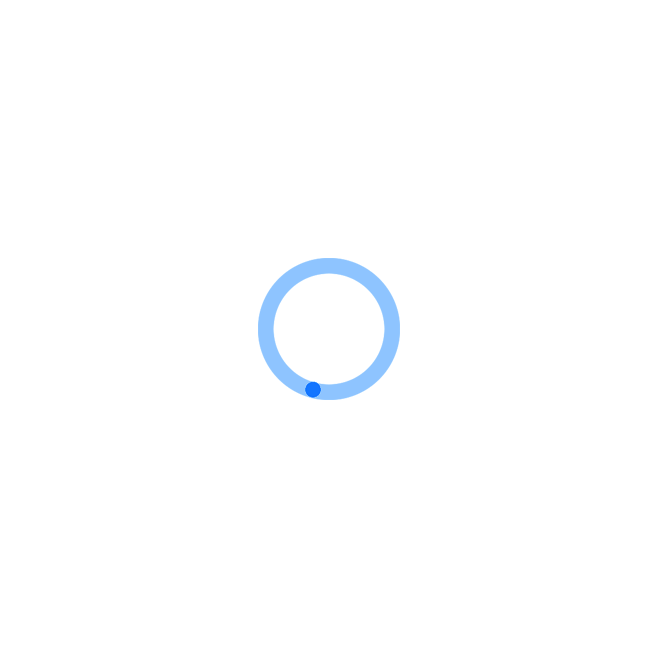
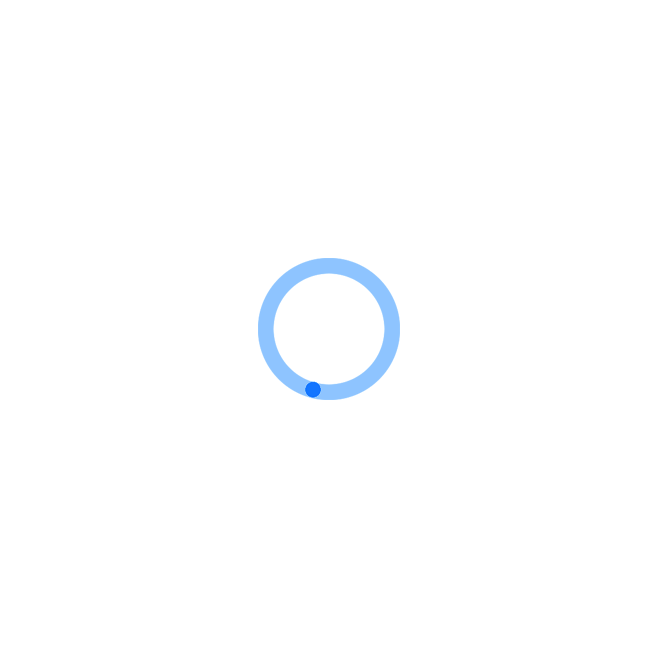
还剩13页未读,继续阅读
本资源只提供10页预览,全部文档请下载后查看!喜欢就下载吧,查找使用更方便
文本内容:
铸造铜及铜合金的熔炼第一章炉料和配料第一节金属熔炼损耗定义金属熔炼损耗指熔炼过程中,金属的挥发、氧化烧损、与炉衬作用的消耗等全部损耗的总和一挥发在熔炼过程中,金属的挥发是难以避免的,特别是一些易挥发元素有时会因挥发损失过大致使控制成分发生困难;故在熔炼工艺上应视情况采取相应措施挥发损失主要取决于金属的蒸汽压;此外,与其浓度和氧化膜性质、熔炼温度和时间、炉气性质和压力、熔炼设备和炉膛面积等因素有关金属的蒸汽压随温度的升高而增加金属的蒸汽压愈大或沸点愈低,挥发损失愈大提高金属的熔炼温度,其蒸汽压和挥发损失也相应增加在实际生产中,一般熔炼温度越高、时间越长、易挥发的元素含量越多、炉膛内气压越低、熔池面积越大、覆盖条件越差、挥发损失就越大铝、钺等在熔池表面形成保护性氧化膜,能显著减少合金中易挥发成分的损失熔炼设备对金属挥发影响较大,一般感应电炉的挥发损失较少,而反射炉的损耗较大常见元素的蒸汽压从大到小排序HgAsCdZnMgBaCaSbBiPbAlAgSnCuSiAu汞碑镉锌镁钢钙睇锄铅铝银锡铜硅金
二、氧化烧损熔融金属中合金元素的氧化烧损,与合金元素对氧的亲和力及含量有关,凡与氧的亲和力比基体金属大、表面活性强的元素,必然易于烧损;如铜合金中的铝、错、钛、硅、镒、铭、锌、磷、铅等,均比铜更易氧化烧损所以,从各种合金元素对氧的亲和力及氧化膜的性质,便可估计出合金元素氧化烧损的趋势有利于抑制铸造过程中产生的成分偏析,羽毛状晶、浮游晶和粗大金属间化合物的形成;提高抗裂纹的能力获得细晶组织的途径1)控制凝固时的温度制度即增加冷却速度和降低浇注温度,增加冷却速度的作用是增大过冷度,提高形核率2)细化处理向熔体中加入少量的特殊物质,来保证熔体内非均质形核,这种特殊添加剂叫作晶粒细化剂3)动态晶粒细化向处于凝固过程中的熔体施以某种物理的振动或搅拌,在熔体中造成局部起伏,给晶体的游离的增殖创造条件第二.铸锭缺陷及质量检测
一、化学成分废品分两类,一类是主要成分不合格,另一类是杂质含量超过了限度主要成分不合格的原因及分析方法类..原・防止方法•纯金属・・1・.原料品位不合格
2..熔炼期间吸收了某些杂・.
1..原料的品位不应低地所熔金属的品位2一避免熔体中杂质含量增高合金・
1.混料
2..配料计算或称量错误
3..某些元素的熔损大
4..炉前化学成分时,发生差错••如试样没有代表性,化学分析误差大,补偿或冲淡计算以及称料错误
5..化学成分发生偏析现・.
1..加强原料管理
2..配料计算及称量均应准确
3..易熔损元素的配料比应取中上限,熔炼过程中应力求减少其熔损尽量缩短熔铸时间
4..调整化学成分时应严肃认真如取样前应彻底搅拌熔体,炉前分析应准确,补偿或冲淡时应认真计算和反复核实
5..避免减少化学成分的偏析现象杂质含量高的原因及防止方法类..原・防止方法•原料不..
1..新金属品位低,含杂质较高2一旧料多次返工,某些杂质积累过高
3..混..
1..原料中的杂质,不应高于所熔金属或合金的杂质限度
2..含杂质较高的旧料,应与适量的新金属搭配使用
3..加强原料管理熔炼工艺不・.
1..变料时洗炉不彻底
2..熔体中某些元素与炉衬之间发生化学作用
3..熔体与覆盖剂之间发生化学作用
4..某些添加剂元素积累
5..工具材质不当,熔炼时发生熔蚀现象
6..返炉残料中混有杂..
1..变料时,应彻底洗炉
2..炉衬材料应合适;防止熔体温度过高
3..覆盖剂应选用恰当,防止熔体温度过高
4..尽量少加添加剂;发现添加剂有明显积累现象时,应立即采取措施
5..根据金属或合金性质不同,应选用不同材质的熔炼工具;尽量减少工具与高温熔体的接触时间
6..返炉残料应经过挑拣
二、气孔存在于铸锭内部的气体空穴,称作气孔形状有圆形、长圆形及不规则的针状等多种,而且大小也不一样气孔的存在减小了铸锭的密度,加工气孔可被压缩,但不易被焊合,常在加工和热处理后引起材料起皮和起泡等缺陷常见气孔有三种内部气孔、表面气孔和皮下气孔内部气孔产生的原因一般有以下情况
1..炉料有油污、水分、乳液、铜锈、铜豆等
2..工具、新开炉炉衬干燥不彻底;
3..覆盖剂、;熔剂潮湿或覆盖不好;
4..装料顺序不正确;
5..熔炼时间过长;
6..脱氧、除气不良;
7..铸造温度高,速度快;
8..保护性气体质量不佳;表面气孔产生原因
1..托座或底垫潮湿;
2..模温过低,吊包、中间包等工具不干燥;
3..涂料刷得不均或太厚;
4..锭模内壁有孔洞、;缝隙皮下气孔产生原因
1..润滑油含水;
2..水压过大
3..结晶器或水冷模漏水
4..铸造速度过快,涂料来不及挥发
三、夹渣(杂)包括表面夹渣及内部夹渣夹渣破坏基体的连续性,降低金属的塑性,使制品分层,降低材料的冲击性与疲劳强度产生原因去渣精炼不良;清炉不彻底,挡渣不好;扒渣不净;润滑油或涂料过多,质量不符要求;铸造温度低,速度快或金属液翻动厉害;保护性气体质量不佳;含高熔点元素的铜合金中,特别是当铁、铭、银、错等以纯金属形式加入时,铸锭内部易出现未熔的纯金属夹杂块避免措施应保证进入铸模(结晶器)的熔体中不含渣如出炉前彻底捞渣;向立式铁模浇注金属时最好采用漏斗等
四、偏析定义铸锭各个部分及晶粒内部成分不均的现象称为偏析其影响表现为以下几个方面由于化学成分不一致,其力学性能、物理性能以及抗腐性能也不同;使加工困难如锡青铜产生反偏析,铸锭表面含锡高,增加切削量及压力加工的困难;由于偏析使易熔共晶富集在晶粒连界且成网状组织,增加铸锭在冷却过程产生的热裂倾向连续铸锭时,温度高、速度快、液穴深,易形成反偏析
五、缩孔与疏松当金属或合金由液态变为固态时,由于发生体积收缩而在最后凝固的地方出现的孔洞,一般称为缩孔缩孔分三种一种是尺寸较大的集中缩孔,多产生在铸锭头部及中部;一种是分布在晶界和枝晶间的分散性小缩孔,常称为疏松或缩松;肉眼分辨不清的缩孔则为显微疏松
1..缩孔内表面参差不齐,近似于锯齿状与表面光滑的气孔很容易区分缩孔一般出现在铸模铸锭,可在模顶上附加保温帽并在浇注后不断用高温熔体及时补口,可在很大程度上减少缩孔的深度,甚至可完全把缩孔移至保温帽内
2..疏松与缩孔的主要区别是,疏松多分散地分布在晶粒之间,缩孔多集中地分布在铸锭最后凝固的地方前者洞穴较小,后者洞穴较大影响缩孔与疏松产生的因素金属或合金本性、铸锭的形状及尺寸、铸造工艺条件等铅黄铜、铝青铜等结晶温度范围较小的合金,多产生集中缩孔,结晶温度范围较大的锡磷青铜,则易形成疏松另外,热容大、吸气强的合金也易产生疏松,如Qsi3T等防止缩孔和疏松的方法在保证进行顺序凝固的条件下,适当提高铸造温度并及时补缩
六、裂纹铸造生产中常见裂纹有热裂(在结晶过程中产生的)与冷裂(在凝固后的冷却过程中产生的)两种两种裂纹各有其特征前者多沿晶界裂开,裂纹曲折而不规则,有时还有分枝裂纹,裂纹多分布在铸锭最后凝固的区域或靠近这些区域后者多产生在温度较低的弹性状态下,常穿过晶粒内部,裂纹较规则,有的冷裂是以热裂为基础转变而来的铜、镇及其合金在铸造生产中出现的裂纹多为热裂纹,其产生原因与铸造应力密切相关随着铸造方法的不同,引起裂纹的主要应力也不一样当采用铁模及水冷模铸造时,所出现的裂纹大多数是由于受机械应力的影响;而采用直接水冷连续铸造时,则往往由于铸锭内外层温度梯度大,从而产生的收缩应力也大,所以使铸锭产生裂纹的应力主要是收缩应力影响热裂纹的因素
1..金属或合金的性质”
1..金属或合金本身的热脆性;
2..凝固线收缩率大小;
3..金属或合金在固液区内的抗拉强度及伸长率的高低;
4.
1.质含量及分布情况・
2、铸造工艺及设备、工具情况;.
3、冷却强度大小.防止产生热裂纹的基本方法
1..调整合金中的主成分及限制杂质含量;
2..加入微量变质剂细化晶粒或使晶界某些易熔物变为高熔点化合物;
3..搞好脱氧去气等精炼工作;
4..降低铸造温度;
5..改变供流方式,如由一点供流改为向铸锭周边均匀导入金属熔体;
6..降低铸造速度、减小冷却强度,必要时采用红锭铸造;
7..力求使铸锭各部分冷却均匀;
8..适当增加结晶器的长度.常见热裂纹的类别及产生原因.
1.表面纵向裂纹产生原因
1..金属或合金有热脆本性(如紫铜、铝青铜、锡磷青铜等较易出现这种裂纹);
2..铸锭出结晶器下口时,局部表面温度高;
3..局部冷却不均;
4..结晶器内套外壁上水垢较厚;
5..结晶器内金属水平高或使用长结晶器;
6..锭模或结晶器内套变形;
7..铸造温度高,铸造速度快
2..表面横向裂纹的产生原因
1..合金本身高温强度差;
2..结晶器(或锭模、石墨套)内表面粗糙或粘有金属,润滑不良或铸锭产生了悬挂;
3..结晶器(或锭模)安装不正或内壁变形;
4..结晶器内套外壁上水垢多,导热性差加上铸造速度快;
5..石墨套与铜套配合不紧密,局部冷却缓慢;
6..锭模卡子不紧或内壁有裂纹;
7..铸造开始时,放流快,开车早且铸造速度快,铸锭来不及冷凝(如铸造被青铜时,这一点较明显);
8..卧式连铸时,停、拉时间不当;
9..铸造温度低
3..内部裂纹产生原因有
1..铸造速度快,铸造温度高;
2..水冷不均;
3..受合金本性影响;
4..使用了过短的结晶器;5一t甘烟或浇铸管埋入过深
七、麻面(麻坑)麻面是铁模铸锭时易出现的一种缺陷,其产生的原因是
1..锭模内壁不平整光滑;
2..清理锭模不彻底;
3..锭模、漏斗温度特低;
4..涂料不均或过薄;5・.漏斗眼堵塞;
6..注流不直或冲烫模壁;
7..铸造温度特低,铸造速度慢
八、表面纵向条痕.卧式连铸时石墨内套上粘有氧化渣或其上产生了凹槽,往往造成铸锭表面纵向条痕消除办法,若条痕呈断续式,可以降低拉速,提高频率,当缺陷消除后再恢复原来的拉速和频率若条痕呈连续式,则应更换石墨内套第四.熔炼设备第一.工频有铁芯感应电炉
一、工作原理工频炉也叫低频炉,相当于在短路状态下工作的变压器炉子的感应线圈相当于变压器的一次线圈,熔沟中的金属相当于变压器的二次线圈将工业频率的交流电引进一次线圈时,通过电磁感应,在熔沟金属中将感应出很大的电流,电流在熔沟中产生使金属发热的功率,使金属加热熔化由于熔沟中热金属和炉膛内冷金属比重不同,以及电动现象的影响,熔化的金属流入炉膛并带来热量使冷料熔化优点熔炼迅速,热效率高;由于电磁力引起金属液的自动搅拌,能保证温度和成分均匀
二、构造与技术性能有铁芯感应炉由炉体、水冷或风冷系统电气设备三部分组成炉体包括炉架、炉身、感应圈、水.套(或耐火套)、铁芯、倾动装置等炉身下部是炉底也叫炉底石,外部是由钢板焊起来的外壳(最好用青铜等非磁性材料制成);内部是用耐火散料捣筑的炉衬炉底石安装熔沟样板熔沟宜采用大截面积熔沟或不等截面环形熔沟,使用效果较好以避免熔沟温度与炉膛温度相差过大及断沟的产生熔沟按配制方式分为立式、卧式,与水平成一定角度三种,按熔沟数量为分单熔沟和双熔沟两种双熔沟的优点是炉子的电抗较小,可提高炉子的功率因数及生产率
三、炉底石的制造一种是在炉底壳内用一定粒度的耐火散料捣筑后烧结而成,另一种则是在炉外预制成型
四、炉的使用及维护
1.
1.炉过程中,从熔沟局部熔化到全部化通的过程叫起熔过程在起熔过程中,应注意以下两点a..在起熔过程中,若电流表指针摆动或电流突然下降,这表明将有断熔沟的现象发生,此时应迅速倾动炉体(15度角),直到电流指针恢复正常为止b..熔沟化开后,若发生窜铜水现象,应立即停电,将电压倒回一级并向窜铜水处插入预热过的铜棒或浇入高温铜液,倒回原电压级,继续烤炉
2..停炉后需继续送水或送风冷却线圈和水冷套,直到炉温降到接近室温时停水或停风
3..在炉子工作期间,应注意维护好线圈、铁芯和炉底石否则,一旦线圈损坏或熔沟中液体金属环凝固断裂、炉底石损坏等现象出现时都可能导致停炉第二.无铁芯感应电炉
一、工作原理也叫塔蜗感应炉,在耐火材料t甘烟外面,围绕一个通水冷却的称为感应器的线圈,即为一次线圈它实质上相当于一个空气变压器,金属炉料相当于短路的二次线圈电流通过感应器产生磁场,在金属炉料中感应出电动势,因其短路连接而在炉料中感应产生强化的电流,使炉料加热并熔化优点熔炼温度高,可达到1600多度,熔化速度快,对熔体的搅拌作用比有铁芯的感应电炉更为强烈;容易变换合金牌号,适宜于小量或大批、连续或间断、多品种的生产缺点单位电能消耗高,功率因数低分为工频无铁芯感应电炉(50HZ)、中频无铁芯感应电炉(频率10000HZ以下而又远高于工频)和高频无铁芯感应电炉(频率在10000HZ以上)三种电流在炉料中的分布不均匀,电流密度在靠近塔竭壁的薄金属层中最大,由边缘向中心迅速减少电流密度由表面向中心减少到表面密度的%的距离,叫穿透深度,在这层中放出主要热量,使炉料加热和熔化
9....4
三、其他金属损耗1熔融金属或金属氧化物与炉衬材料之间的化学作用,造成金属损耗
2、金属在熔炼时,熔融金属因静压力作用可能渗入炉衬缝隙,而导致高温区局部熔化,使渣量及渣中金属损耗增加,这种情况在新炉开始生产和炉子快损坏时较易出现此外,机械混入渣中的金属,以及扒渣、飞溅等也造成金属损失
四、降低熔炼损耗的方法
1、选用熔池面积小的炉子熔炼如采用工频炉代替反射炉
2、制定合理的操作规程易氧化、挥发的合金元素应制成中间合金在最后加入,或在熔剂覆盖下熔化装料时要做到炉料合理分布,尽量采用高温快速熔化,缩短熔炼时间熔炼黄铜时采用低温加锌
3、碎屑散料应制成捆或团使用
4、正确控制炉温在保证熔融金属的流动性及其它工艺要求的条件下,选择适当的熔炼温度
5、炉气一般以控制微氧化性气氛较好;
6、选用覆盖剂可防止金属氧化和减少挥发损失含有铝、钺等元素的合金,由于能在熔融金属表面形成致密的氧化膜,一般不再加覆盖剂;但操作中应注意勿使氧化膜遭到破坏;
7、正确选择覆盖剂或熔剂,使具有足够的流动性和覆盖能力,同时采取高温扒渣、捞渣等措施,降低渣中金属损耗
8、利用脱氧剂使基体金属的氧化物还原(*)
9、采用真空熔炼或保护性气体熔炼第二节杂质的控制
一、杂质的来源在熔炼过程中,大多数杂质是金属从炉衬、炉气、熔剂、炉渣、操作工具等方面吸收的如炉衬材料选用不当时,在熔炼温度下,金属就会与炉衬相互作用,不仅降低炉衬寿命,而且会使某些杂质进行金属如在酸性炉衬的工频炉中熔炼铝青铜时,会使合金增硅燃料不纯时也会增加杂质,如用含硫高的煤气或重油作燃料时,在加热和熔炼铜、镇的过程中,会因下列反应而增硫Cu+S=Cu2SNi+S=Ni3S当铜和铜合金用米糠作覆盖剂,镇和银合金用稻草灰作覆盖剂时,都会使金属增磷从炉衬、炉气、覆盖剂或熔剂中吸收的杂质,虽然每次熔炼所吸收的量很小,但由于部分炉料经反复使用,杂质含量也有可能逐步积累增多,甚至造成报废许多杂质在熔炼中的烧损比合金的组成元素少,反复回炉熔炼会使杂质相对含量增加因此,生产中新金属与旧料的使用量一般保持一定比例,使杂质不超过一定含量此外,变料时洗炉不彻底,炉料管理不善,原料的混料等都会使金属中杂质增多
二、控制杂质的途径
1、加强炉料管理,杜绝混料
2、在可能条件下,新金属和旧料搭配使用,旧料的使用量不超过炉料的50%;
3、变料时,必须按金属的杂质要求,准确计算洗炉次数;
4、选用化学稳定性高的耐火材料如镁合金用镁砂炉衬,铝青铜用中性炉衬等;
5、与熔融金属接触的工具,尽可能采用不易带入杂质的材料,或用涂层保护第三节炉料炉料包括新金属、厂内旧料、外来废料、二次重熔料、中间合金等
1、新金属电解铜、电解银、电解锌、电解锡
2、厂内旧料包括熔铸车间的残料、洗炉料和废品,铸锭加工的锯屑和切削屑,加工车间返回的残屑、残料及边角料等(废梗、刨花、铜渣)
3、外来废料如紫铜、白铜角料、火烧铜
4、二次重熔料铜块装料顺序及原则
1、炉料入炉前应检验化学成分及杂质含量;
2、炉料应该清洁干燥、无尘土、油污、腐蚀物
3、为装炉方便,锭块要堆垛整齐,边角料要打包制团,散料应装入料斗等,以减少装炉时间原则1)炉料中总质量最多的金属应最先入炉,即基体金属首先入炉如熔炼铜合金时,先熔铜2)易氧化,易挥发的合金元素,应留到最后装炉和熔化3)合金熔化放出大量热的金属,不应单独加入,而应与预先留下的基体冷却料同时加入如将铝加入到铜液中,所放出的热量,可使局部温度升高200度以上4)一般两种熔点相差较大的金属,应先装入易熔金属,然后再加入难熔金属,利用难熔金属的熔解作用,使其逐渐溶解于低熔点金属中如熔炼白铜时,由于铜
(1083)的熔点比镇
(1451)低出较多,故先熔铜后加入银,只需在1250-1270时镣可全部熔化如硅青铜熔炼时,将硅和镒先熔化在感应炉起熔体中,合金熔体含气量大为减少第四节中间合金一使用目的与要求1)便于加入某些熔点高、易氧化燃烧或挥发的元素到合金中去;2)有利准确控制合金的化学成分;3)避免金属液过热,减少熔炼损耗;4)缩短熔化时间第二.熔炼与铸造第一.除气和脱氧
一、气体的来源.能溶解于金属中的气体,主要是氢和氧在熔炼过程中,气体的主要来源有
1..炉气非真空熔炼时,炉气是金属中气体的主要来源在炉气中除含有氧、氮外,还含有水汽、氢、一氧化碳、二氧化碳、二氧化硫和碳氢化合物等炉气的成分随使用的燃料和燃烧的情况的不同而变化;如以重油或煤气做燃料的反射炉或用烟炉中,常含有570%的水汽和较多的氢、一氧化碳等
2..炉料电解金属表面大都有残留电解液,加工车间返回料大都含有油、水、乳液等外来废料大都有水腐蚀物、锈蚀等特别是露天堆放和潮湿季节,炉料表面吸附有水分这些都会使金属在熔炼过程中吸收较多的氢
3..耐火材料耐火材料中所含水分也能促使金属吸气,新炉开始生产时尤为严重
4..熔剂许多熔剂都带有水分,其中一些(如木炭、米糠等)含有吸附的水分,有些熔剂(如硼砂)本身带有结晶水为减少熔炼过程中气体的来源,熔剂应进行干燥或脱水处理
5..操作工具操作工具预热不彻底,也会增加金属的含气量
二、气体的溶解过程及溶解度气体在金属中溶解度金属在固体时,气体的溶解度很小,随着温度的上升溶解度缓慢增加,到熔点温度时溶解度急剧增加,继续提高熔融金属的温度,气体溶解度继续增加,到某一最大点后开始下降,到金属的沸点温度时,气体溶解度几乎等于零不同的合金元素对气体在合金中的溶解度的影响也不同,某些元素如镁等与气体有较大的结合力,使合金中的气体的溶解度增加另上些元素如铝、锡等能使气体在合金中的溶解度降低铜合金中合金元素对氢气溶解度的影响如下Cu+N..Cu+P..Cu+A..Cu+A..Cu+S..Cu+A I
三、除气方法
1..气体除气法一种为惰性气体(如N2等),另一种是活泼气体(如CI2等)气泡越小,数量越多,对除气是有益的但由于气泡上浮的速度大,通过熔体的时间短,且气泡不可能均匀分布于整个熔体中,故用此法除气不容易彻底;随着熔体中含氢量的减少,去气效果显著降低2・・熔剂除气法熔剂除气是利用熔盐的热分解或与金属进行置换反应,产生不溶于熔体的挥发性气泡而将氢除去如铝青铜常用冰晶石熔剂除气,白铜和银合金常用萤石、硼砂、碳酸钙等熔剂除气熔剂精炼时,一般将干燥的熔剂用带孔罩压入熔池中为了提高除去效果,也可采用干燥氮气将粉状熔剂吹入熔池中熔剂在除气的同时,还可去渣
3..沸腾除气在工频炉熔炼高锌黄铜时常用的一种方法但需具备两个条件一是高锌黄铜的沸腾温度较低,二是熔沟部分熔体温度较高铜锌合金的沸腾温度随锌含量的增加而降低由于工频炉中熔沟部分熔体温度最高,首先形成锌的蒸汽泡随即上浮伴着熔池温度的升高,炉膛内的蒸汽压也随逐渐提高;当温度升高到整个熔池接近锌的沸点时,甚至使整个熔池表面出现冒泡当熔池上面的蒸汽压升高到超过大气压时,锌蒸汽便向炉口喷出,被氧化燃烧,形成沸腾的喷火现象次数越多,除气效果越好,一般2-3次即可含锌量小于20%的黄铜,不能利用沸腾除气缺点在于低沸点金属元素(如锌等)损耗较大
4..其他除气法1)冷凝除气;2)振荡除气;3)直流电解除气
四、脱氧过程使金属熔体中的氧化物还原而除去氧的过程称为脱氧熔融金属及合金中的脱氧过程属于置换反应,凡在操作条件下,能从熔融金属中取得氧的任何物质,即氧化物的分解压比被脱氧金属氧化物的分解压为低的元素,一般都可作为脱氧剂
五、脱氧剂分为表面脱氧剂和溶解于金属的脱氧剂两种表面脱氧剂基本上不溶于金属,脱氧作用仅在与金属接触的表面进行,脱氧速度较慢它的优点不溶于金属,脱氧剂不会影响金属的质量常用的表面脱氧剂有碳化钙、硼化镁、木炭、.B203等溶于金属的脱氧剂,能在整个熔池中与熔融金属中的氧化物相互作用,脱氧效果好得多缺点是剩余的脱氧剂将留于金属中而影响金属的性能常用的脱氧剂有磷、硅、镒、铝、镁、钙、钛、锂等这些元素可以中间合金的形式加入脱氧反应所产生的细小固体氧化物,使金属的粘度增大,或成为金属中分布不均匀的夹杂物,故应控制加入量对脱氧剂的要求
1..对金属或合金的性能无害
2..脱氧产物最好不溶于熔融金属,且容易除去
3..脱氧剂应足够活泼,即脱氧产物应与熔融金属在比重和熔点上有较大的差别铜磷中间合金除能脱氧外,并能改善合金的流动性,在铜合金生产中应用较广第二.精炼
1..氧化精炼
2..除渣精炼
3..熔剂使用熔剂的作用是防止吸气、氧化;除气、除渣;细化晶粒;通过熔剂加入某些元素熔剂按用途分覆盖剂、精炼剂、氧化剂、还原剂、变质剂按化学性质又分为酸性、碱性、中性三大类酸性熔剂如硼砂、硅砂等,用来除去碱性和中性如氧化物;而碱性熔剂如苏打、碳酸钙,则用以除去酸性及中性氧化物;中性熔剂有碱金属、碱土金属的氯盐和氟盐,如KCL、NaCLCaCI
2、CaF2等以及木炭、米糠、玻璃等铜和铜合金常用木炭、米糠等作覆盖剂,既可保温和防氧化,又可结渣和改善流动性第三.变质处理变质处理是金属或合金在熔铸过程中,广泛应用于改善材料性能、提高产品质量的重要手段变质处理的方法很多,如加变质剂、机械振动、超声波振动、快速冷却等变质剂的作用有
1..细化晶粒
2..使合金中高熔点化合物的粗大晶粒改变形状,并均匀分;
3..使晶界上的链状低熔点物减少并球化,或形成细粒高熔点化合物;
6...F...铜铁中间合金加入炉.・细化晶粒、提高冷加工塑性..C...铜基中间合金,出炉•前加..细化晶粒、提高高温塑性、提高抗张强度铝青..M..纯金属,出炉前加・・・细化晶粒••B
10、B
3.T.一纯金属,出炉前加...细化晶粒、提高高温塑性•孟奈.纯金属,完全熔化后加.细化晶粒、消除硫的影响•第四.熔炼工艺参数
一、熔炼工艺参数选择
1、制定加料顺序的原则
1..先加数量较多的炉料,在实际生产中,一般先加不少于炉料的30%的金属;
2..具有较高蒸汽压的金属应最后加入;
3..熔解时能产生很大热效应的金属,不作最后一批料加入,以防金属熔体过热;
4..先加较难氧化烧损而较易还原的金属,或较难与炉气及炉衬相互作用的金属
2、熔炼温度熔炼温度对铸锭质量影响较大,温度过高不仅容易产生粗大晶粒、裂纹、偏析等缺陷,而且会促使金属与炉气、炉渣、熔剂、炉衬间的相互作用加强,增加金属的氧化及挥发损失,并促使金属吸气;而温度过低又会使熔体去渣效果降低、铸锭操作困难确定出炉温度的原则
1..保证金属液有一定的流动性;
2..保证浇铸操作的正常进行,防止产生冷隔、夹渣等缺陷;
3..根据不同合金的铸造特性,在保证浇铸操作正常进行的情况下,尽量彩低温出炉第五.铜及铜合金的熔炼
一、黄铜熔炼工艺特性及操作要点
1..锌的除气和脱氧性能很好,操作中加入脱氧剂铜一磷的目的,主要是改善合金的流动性;
2..含锌大于20%的黄铜,一般可按喷火次数作为实际出炉依据;
3..尽量低温加锌,高温捞渣,以减少熔炼损耗;
4..以冰晶石作熔剂的合金,冰晶石加入量约为炉料重量的%;
5..铁以Cu-Fe或Al-Fe中间合金加入,易氧化元素如神、镀等与铜制成中间合金加入
二、青铜熔炼工艺特性及操作要点1)青铜宜采用中频感应电炉熔炼,硅砂或镁砂炉衬,但用有芯感应炉熔炼铝青铜时,最好使用中性或碱性炉衬;2)硅青铜、锡锌铅青铜吸气性强,应使用煨烧木炭作覆盖剂,装料后立即加入足够木炭,直到浇铸完毕不再向炉内添加木炭
三、白铜熔炼工艺
1..白铜宜采用工频或中频感应电炉熔炼,硅砂或镁砂炉衬;
2..为提高普通白铜的热塑性,可加入钛、错作变质剂
3..装料时如炉内残留铜水过少,银、铁不易熔化时,允许先加入少量紫铜以加速熔化
四、银和银合金熔炼工艺
1..镇和镇合金采用中频或高频感应电炉熔炼,高铝砂或镁砂炉衬;
2..为提高纯银和镁合金的热塑性,细化晶粒,可加入少量钛作变质剂,在炉料全部熔化后加入;
3..加炭脱氧时,可用小块木炭慢慢加于液面,一次加入过多或过快易造成金属液上涨,甚至外溢木炭加入量视木炭与金属液反应情况而增减;
4..加镁脱氧时,镁用银片包住,迅速插入金属液中也可采用银镁中间合金作脱氧剂第六.铜合金铸锭
一、锭模铸锭分圆锭对开立模、圆锭整体模、圆锭水冷模、斜模及无流模等影响锭模铸锭品质的因素
1、浇注时间.不同牌号的铜合金都有最适宜的铸造温度,高于或低于这个温度将直接影响铸锭的质量对于锭模铸锭的方式来说,铸造温度的控制与浇注时间密切相关,因为浇注时间越长,先后浇注的金属熔体的温度差越大对于铸造温度范围较窄的合金来说,浇注时间越长,浇注也益越难控制、气氛;2熔体从出炉到浇注完毕的整个过程中,气,始终对熔体的质量产生影响影响的程度取决于浇注方式、流柱大小与长度,通常在大气下浇注时,熔体易受到明显的氧化,因为流柱越短,与大气接触表面积越小,氧化损失就越少流柱越平稳、,氧化机会也越少一旦流柱保护得不严密,不可避免产生氧化,氧化膜与液流俱下,裹入熔体中,凝固后便成夹渣
3、烧注温度温度过高或过低都是不利的因为采用较高的浇注温度,势必就要使炉内熔体的温度作相应的提高这将引起铜或铜合金在熔化和保温过程中大量的吸气,同时也会增加烧损,在浇注时会使氧化加剧此外,过高的浇注温度也会对锭查的寿命产生不利影响,尤其是平查浇注时查底板更容易遭到破坏当浇注温度偏低时,熔体流动性变差,不利于气体和夹渣上浮,也易使铸锭产生冷隔缺陷因此,必须根据合金的性质,结合具体的工艺条件,制定适当的浇注温度范围
4、浇注速度1)在保证铸锭产品质量的前提下,适当提高浇注速度;2)对于某一确定的金属或合金,若合金化程度低,结晶温度范围小,导热性好,可适当提高浇注速度;
4..若锭模的冷却强度大,铸定直径小,浇注速度也可适当提高
5、结晶方向在锭模铸锭方法中,应力求使铸锭结晶的顺序是自上而下的,这就必须保证铸锭的散热方向尽量保持由下而上为了使铸锭的凝固结晶过程尽量适应其顺序结晶的条件,有多种方法改进锭模结构,增加模底厚度和模体下部壁厚以改善锭模下部的冷却条件;为了造成锭模上部缓冷条件,在锭查顶部加设保温帽;适当提高铸造温度,同时降低铸造速度以保证顺序结晶所需要的铸锭上下部分之间的温度梯度
6、涂料的使用使用目的防止熔体粘模,改善铸锭表面品质,保护锭模、减少磨损、防止模体损坏,使锭模建立起适于浇注的气氛.涂料选择浇注铜合金所用的最理想的涂料应该是有足够的挥发成分;有与熔体的浇注温度和浇注速度相配合的挥发温度和挥发速度例如使用油性涂料时,理想的状态是涂料能在熔体表面与模壁接触的边界上大量蒸发,并且蒸发出的气体产物能够笼罩和包围住不断上升的熔体表面,把木炭、氧化物颗粒、涂料挥发后的残渣等夹渣物从模壁推向铸锭中心的液面上,随液面上升而上浮涂料的种类一是挥发性的,主要由各种油类和烟灰等组成;二是非挥发性的,主要是保温性氧化物,多用于轻合金锭模铸锭主要涂料有煤油加炭黑;豆油加肥皂;洒精加松香
二、水平连铸线坯水平连铸线坯也称水平拉铸,线坯内部和表面品质都好、致密且力学性能均一该法适用黄铜、青铜和小截面线坯的连铸生产水平连铸采用拉-停-拉-停地步进式进行的在“停”的一段时间内,让金属沿结晶器内壁凝固成壳,而后拉“出一段,再做下一周期的“停-拉:因此J拉”的行程J拉-停的频率「停-拉”的时间比例是重要的工艺参数水平拉铸线坯也设有牵引装置以控制和调节拉铸速度,对相同规格的线坯,视合金不同其拉铸速度也不同第三.铸锭组织与控制第一.铸锭的宏观组织
一、典型的铸锭组织铜合金铸锭的组织包括晶粒的形状、大小、取向、分布、完整性,各种缺陷以及合金元素的分布等等它们对铸锭的热加工性能及制品的性能,尤其是力学性能都有着重大的影响宏观组织,一般分以分辨出晶粒不同的三个区域a.激冷区,紧靠模壁的一个外壳层,由无规则排列的细小等轴晶粒组成,也称作表面等轴晶区,仅几个晶粒厚b.柱状晶区,由垂直于模壁,彼此平行的柱状晶粒组成c.等轴晶区,位于铸锭的中心区域,由较粗大的等轴晶粒组成,也称作中心等轴晶区在经细化处理的铜合金铸锭中,往往全部为等轴晶,而没有柱状晶,或是全部柱状晶,而没有等轴晶即使具有上述三种晶区的铸锭,其各自的宽度也会因合金、铸锭方法及工艺的不同而不同
二、铸态组织对性能的影响
1..柱状晶组织对性能的影响工业生产的铸锭以柱状晶组织居多柱状晶对铸锭的性能影响很大,因为在柱状晶交界,往往存在着低熔点共晶组织及夹杂物、气孔和疏松,还可能出现晶间裂纹,是铸锭脆弱的地方当铸锭承受冷热加工时,易于沿此处开裂,另外,柱状晶本身的方向性也降低铸锭的力学性能和加工性能因此,用于塑性加工变形的铸锭,希望柱状晶区尽可能小,等轴晶区尽可能宽,特别注意避免出现粗大的柱状晶组织另一方面,由于柱状晶本身存在枝晶不甚发达而较致密,故其强度较高对于高温机件,则需得到柱状晶组织,以显著改善其耐热性
2..表层粗大晶粒对性能的影响在铸锭生产中,如工艺控制不当,易出现铸锭表层粗晶粒组织,这会导致加工制品表层组织不均匀,深冲时会出现制耳因此,在加工前需通过铳面以消除
3..粗大金属间化合物对性能的影响铜合金铸锭中的一些高熔点金属化合物初晶,多呈块状、片状或针状不均匀地分布在基体中,这些金属化合物一般较硬脆,降低铸锭的塑性,并降低材料的横向性能、疲劳极限和耐蚀性当粗大金属化合物分布不均时,则危害更大适当提高浇铸温度、加在冷却强度,可减少化合物初晶的数目,有利于防止粗大化合物初晶的形成严格控制合金成分或进行晶粒细化处理是防止粗大化合物形成的有效方法利用过热法也可以细化金属化合物初晶,改善铸锭组织的均匀性,进而提高材料的力学性能
三、铸锭组织控制途径.由于铸锭的结晶组织对其半成品组织及性能具有遗传影响目前一致认为细小等轴晶组织是铸锭的最佳组织有如下优点各向同性;组织致密;强度高;枝晶细;第二相分布均匀,。
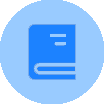
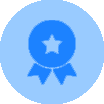
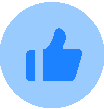