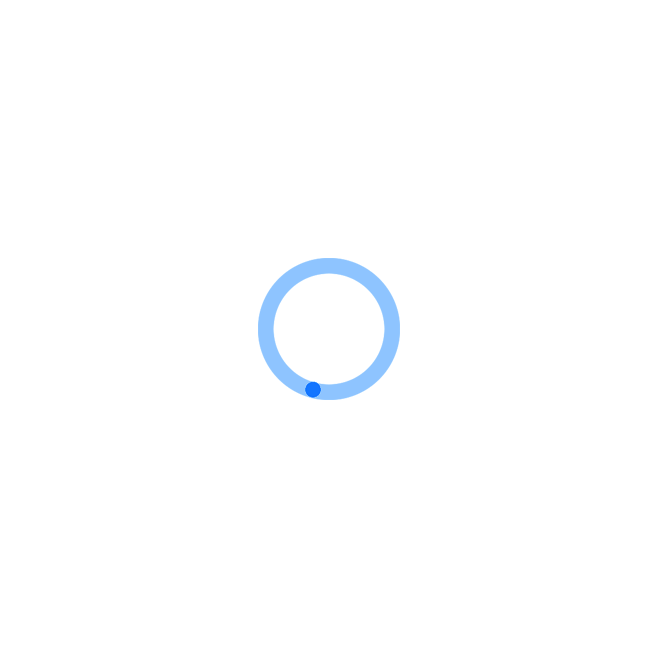
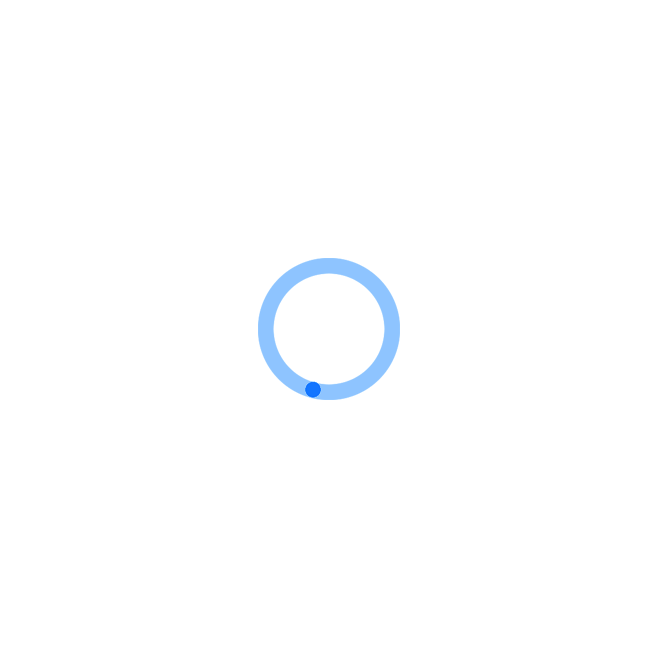
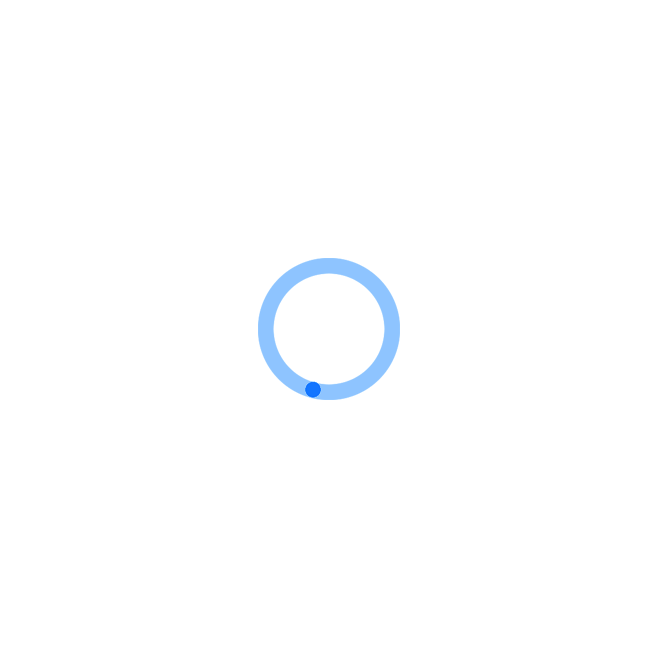
还剩1页未读,继续阅读
文本内容:
设备管理四大重点检修圈
一、为什么预防性维修特别重要?设备管理的发展历程,一直以来都是伴随着企业生产管理和质量管理的要求而延伸进步的,同时它也在不断地寻求自己的价值体现和定位在这个持续进化的过程中,设备管理也在持续借鉴吸收生产管理和质量管理领域的一些精华,逐步形成自己的体系及运作机制我们知道,从最基本的管理诉求来说,企业追求的是设备投入产出最大化,也就是追求设备利用和运营效率的最大化从这个意义上来分析,我们就不难理解设备管理从〃事后维修〃发展到〃预防维修〃阶段的原动力因为必须要解决好设备突发故障对生产计划的干扰和产品质量的负面影响,才有可能来谈论效率最大化的问题所以说,如何有效〃预防〃突出故障的发生,就成为所有设备管理者首先要去思考和解决好的问题预防性维修理念的落地机制,包括较强制性的预防维修计划执行(计划预修制),以及以点检为基础的预防维修制两者的结合,就是目前很多企业耳熟能详的〃点检定修制〃虽然〃点检定修制〃被很多企业所熟悉,但在实际执行过程中,仍在存在着诸多的问题包括预防性维修计划受生产安排影响而无法有效执行问题;预防性维修计划的时间周期和检修内容如何更合理的问题;点检人员的责任心、意识和能力对设备劣化把握的有效性问题;点检标准的要素齐备性以及点检项目的识别和判断问题;简单的定时维修对复杂设备故障无法有效防范问题等等正是为了解决好这些问题,从上世纪70年代开始,人们就尝试不断引入新的故障现象识别技术和检查手段,来有效掌控设备劣化趋势和规律性当然尽管早期一样由于受技术所限,对设备劣化趋势的掌控未必完全有效,但都逐步将基于时间的预防维修导向基于状态的预知维修(状态监测),都在不断丰富和完善着如何做到有效预防和预知故障的技术手段
二、是不是所有的设备都需要预防性维修?人们总是在实践中不断深化对事物本质的认识在设备管理者通过不断加大维修投入(周期性的计划性预防维修队伍的人力成本和预先储备的零备件成本)来实现〃预防性维修〃的同时,也逐渐开始思考是不是所有的设备都需要实行〃预防性维修〃并且对于很多类型的制造型企业来说,居高不下的维修费用和零备件资金占用,常常推高了生产成本而使产品丧失竞争力,所以企业管理层要求设备管理者如何降低维修费用就成了非常理所当然的事情,并且这种要求常常是在保障设备效率不降低的前期下提出的,这也成为衡量与评价企业设备管理核心价值的另一个重要方面鱼和熊掌如何兼得?如何在既要马儿跑得快身体好的同时少吃草?成为摆在设备管理者面前的绕不开的难题,我们必须为这种两难需求突破因为我们要关注〃突发设备停机导致的损失〃与〃为了预防这类损失而做的投入〃之间的平衡关系,所以任何一种极端做法都是不可取的既然并不是所有的设备都需要做预防性维修,既然企业应该需求一种综合费用最优的模式,这里面就牵涉一个维修策略的应用问题也就是说,需要根据设备故障特征进行分类,辅以不同的维修策略,以达到综合费用最优〃维修策略〃的有效运用,就成为搞好设备管理应该把握的第二个关键当然维修策略不是简单地设定是事后维修还是预防维修,维修策略事实上非常丰富和多彩如针对设备的设计缺陷展开〃纠正性维修〃,即不拘泥于原设计而大胆尝试,解决一些重复发生的故障的根源性原因;再比如如何将一个设备的问题原因有效传递给设计方,或者类似机台,实现它机类比检修的问题(类似汽车厂商的召回机制)〃维修预防〃等等这些多模式维修策略并存和综合应用,为设备管理者实现综合成本最优提供了大量有效手段
三、综合工程学和全寿命周期概念设备管理在上世纪60年代进入到〃生产维修〃阶段以后,所有基于其管理重点环节的活动和技术应用,都没有从范围上或者管理理念上有根本性的突破真正实现设备管理不断向前发展的,一个是英国的综合工程学,其倡导的全寿命周期管理,将设备管理的重点内容,从仅关注设备使用和维修环节,向前向后扩展到设备从规划到淘汰报废的全过程,这极大地提升了企业对设备管理范畴的认识,特别是如何加强设备前期管理来有效追求全寿命周期综合成本最小化设备综合工程学是英国人丹尼斯巴克斯提出的设备综合工程学的业务工作范畴,涉及到设备及构筑物的规划、设计及其可靠性和维修性,涉及设备的安装、调试、维修、改造和更新等诸方面的内容综合工程学的要点之一是寻求设备寿命周期费用最经济不少研究资料表明,设备一出厂已经决定了设备整个寿命周期的总费用也就是说,设备的价格决定着设置费,而其可靠性又决定着其维持费一台机械性能、可靠性、维修性好的设备,它在保持较高的工作效率的同时,在使用中的维修、保养及能源消耗费用都会减少因此,设备使用初期的决策,对于整个寿命周期费用的经济性影响甚大,应给以足够的重视设备综合工程学是结合系统工程的理论与研究成果对设备管理的系统思考也是一种从系统整体优化的角度考虑设备维修与管理问题的管理思想也就是说,要用系统工程的思想来看待设备系统,从设备一生管理这个全局出发,对技术、经济、组织进行整体规划和优化,以达到花费少、效率高这个最佳效果深入领会设备综合工程学的精髓,并在实践中建立设备全寿命周期管理的系统模式,就可以站在全局而不是某个阶段、某个领域来考虑设备管理与维修的得失问题所以〃设备全寿命周期管理〃是做好设备管理工作的第三个关键
四、全员参加设备管理的重要性日本长期以来一直按照美国的套路实施设备管理,在上世纪70年代初期,在吸收了中国鞍钢宪法中提出〃台台(设备)有人管,人人有专责〃这种吸收工人参加、走群众路线、提倡合理化建议及劳动竞赛的做法后,他们敏锐地把握住了在实践PM过程中的全员参与问题一即不仅是设备专业人员要思考设备管理和维修模式,还需要认识在岗位操作人员在设备管理领域的重要作用岗位操作人员对设备管理的影响,也包括积极积极与负面影响两方面,积极影响方面需要发挥他们天天接触设备对设备信息的了解,用于早期识别设备故障苗头和把故障消灭在萌芽状态;负面影响消除方面则要通过规范他们的行为,有效减少一些重复性的人为失误,避免这种人为失误导致的人为劣化,加速设备故障的发生这种全员参与设备管理的理念,极大地改变了设备管理团队的主体,追求操作人员和维修人员的共同积极作用,来追求设备综合效率最大化从实践效果看,全员参与设备维护是一种有效、低成本和直接的设备管理与维护理念,不仅有效将设备故障识别与消除在萌芽状态,更有效地将维修人员从大量的、频发、低水准、被动地应付现场故障的恶性循环中解脱出来,有时间有精力思考更深层面的设备管理和维修方面的问题,更好地思考设备故障深层次劣化的规律与掌控手段,也便于更好地开展有效的预防性维修一段时间以来国内设备管理界有一个怪现象,认为TPM和设备管理不是一回事,认为TPM是独立设备管理之外的工作这是非常奇怪的,不考虑全员参与因素的〃设备管理〃是〃设备管理〃,考虑了全员参与因素的〃设备管理〃(TPM)反而不是〃设备管理〃了!这是错误的观念和误区,〃全员参与〃是做好设备管理工作的第四个关键也是最重要的关键。
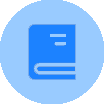
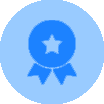
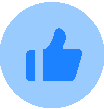