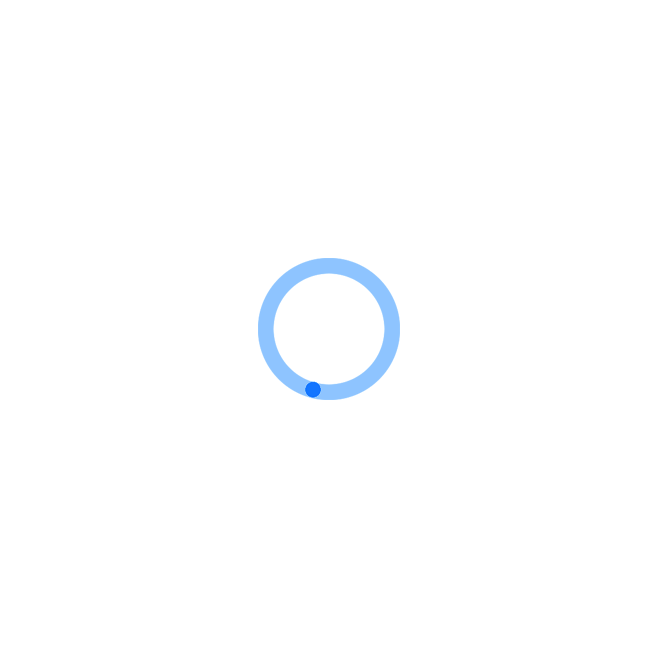
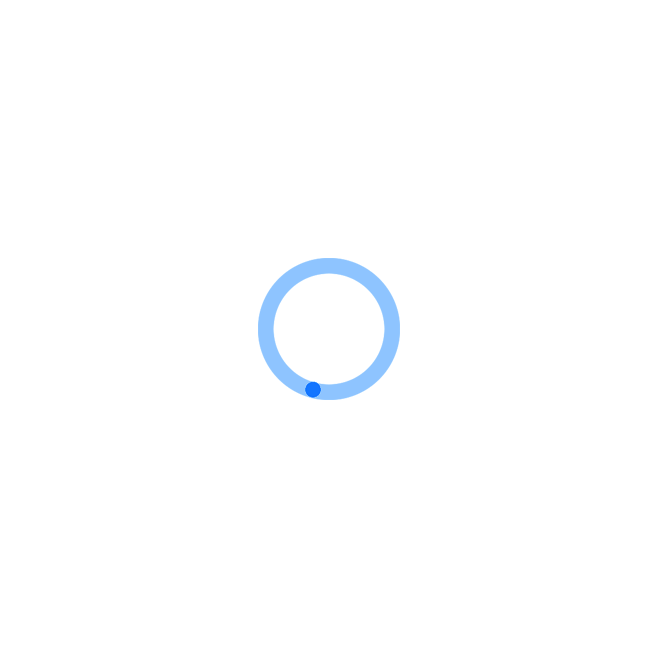
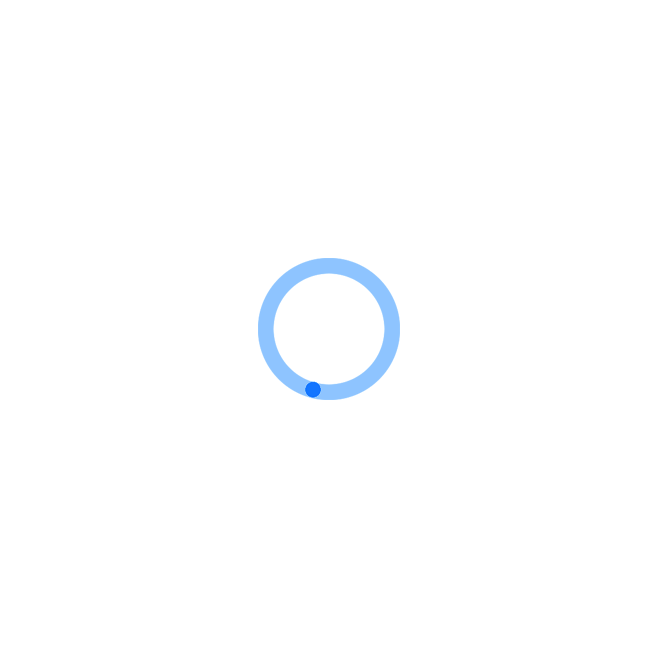
还剩1页未读,继续阅读
文本内容:
首(末)检管理办法定义1首件是指各生产车间加工生产的产品,经自我调试确认,判定合格后,拟进行批量生产前的第一个产品(半成品、成品)首件检验时机2()新产品第一次量产时的首件产品1()每一个生产任务单(订单)开始生产的首件产品2()每一种产品各个工序开始生产的首件产品3()每次更换模具后、调整工装定位后4()数控程序改变后、刀具更换后5CNC()机床故障修复后开始生产的首件产品6()毛坯种类或材料发生变化时7()工艺有重大变化时8()轮班或操作工人变化时9首件检验的主要项目如下3()图号与工作单是否符合1()材料、毛坯或半成品和工作任务单是否相符2()材料、毛坯的表面处理、安装定位是否相符3()首件产品加工出来后的实际质量特征是否符合图纸或技术文件所规定的要求4新产品首件检验4检验流程
4.1()各生产车间依工艺流程加工或调试,并进行自检1()巡检人员在各生产车间加工调试时,应调出各相关检验依据文件或样品,并从旁协助,2同时就外观等易于判定之特性予以确认()各生产车间认定生产之产品合乎要求时,将该首件交巡检人员进一步检验3()巡检人员依据检验文件、规范、对首件进行全面的检查,如判定不合格,应向生产车间4提出,并要求改善,直到判定合格为止()不管首件产品是否合格,巡检人员都应该填写《首件检验报告》,并由送检人员签字5()巡检人员判定合格,或判定不合格但属于设计问题或生产部无法改善之问题时,巡检6人员填写《首件检验报告》,呈质检部主管审核()经品质部主管审核之《首件检验报告》及首件产品后,由巡检人员直接送往技术部,交7具体负责该产品之技术人员作检验()技术部技术人员经检验后,做出合格或不合格的判定,并填入《首件检验报告》中8()技术部、品质部均判定合格后,《首件检验报告》由质检部保留,巡检员在《生产流程卡》9“首检一栏”签字确认,并通知生产车间可以正式量产()技术部、品质部判定不合格时,如属生产原因时,应由生产部/车间改善、调试直到合10格为止;如属于设计原因时,应停止生产,由技术部负责拟出对策加以改善后,方可恢复生产,并需重新作首件确认注意事项
4.2()某些品质特性之判定无法在短时间内得出结论,这些特性于新产品试制时应进行检测,在1首件检验时,可先不检验这些项目()品质部应在量产开始后,依规范随机抽样,就未进行检验的项目实施检验,发现问题应2及时反馈对策()某些检验需要不止一个产品时,可要求生产车间生产足数之“首件”3()首件检验讲究时效,以避免制造单位停工时间太长4()应将合格之首件产品,作为样品由品质部进行标识,车间要单独保存重要件要品质部5直接保存订单首件检验5检验流程
5.1()参照新产品首件检验流程进行1()因不属新产品,在客户没有技术个性变更之一般状况下,只要品质部判定合格即可生产,2不必送技术部检验注意事项
6.2()是否进行长期性试验(如寿命试验)由品质部根据具体产品状况确定1()应将新产品之首件留存样品与各生产任务单(订单)之首件作比较确认2责任
7.首件检验时机车间主管
6.1()在任务下达同时要对操作者进行技术交底工作,指导操作者调试1()监督操作者首件自检并复检确认合格交巡检员,例行首检2()如果没有首检确认进入量产,车间负全责造成不合格由车间自负,不合格品相应处3罚参照相关规定处理不首检罚车间主任元/次50()在首件检验时机”的所有过程,车间主任都必须监督首检4“L2()数控或用工装、模具生产的产品,车间要保留好末件产品方便“终检”5生产操作者
6.2()认真听从车间主任的技术交底,细致阅读图纸,有疑问或不清楚的要向车间主任咨询清1楚认真调试每一个加工要素()首件操作者要先自检,再请车间主任复检,确认没问题后再送巡检员首检2()主动与巡检员配合,提高首检时效3()数控加工的操作者要保留末件产品指给巡检员4()操作者在没有进行首检就进入量产负责一经发现处罚元/次造成的不合格品按相550关规定另做处罚质检部长
6.3()对新产品制定“质量控制点”,编写“工艺检验卡”1()对新产品各道工序检验要点对巡检员进行交底2()对在首检中发生的有争议的问题进行载定,不能自载的上交总程师处理3()对没有按要求首检的生产车间主任和操作者开《质量处罚单》处罚4巡检员
6.4()认真听取部长的质量控制点和检验交底清楚首检要素1()检验前要效对量具,确保准确2()负责首检标识、记录、签字3()对首检失误造成损失负全责、处罚参照不合格品处罚相关规定执行4。
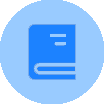
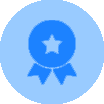
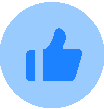