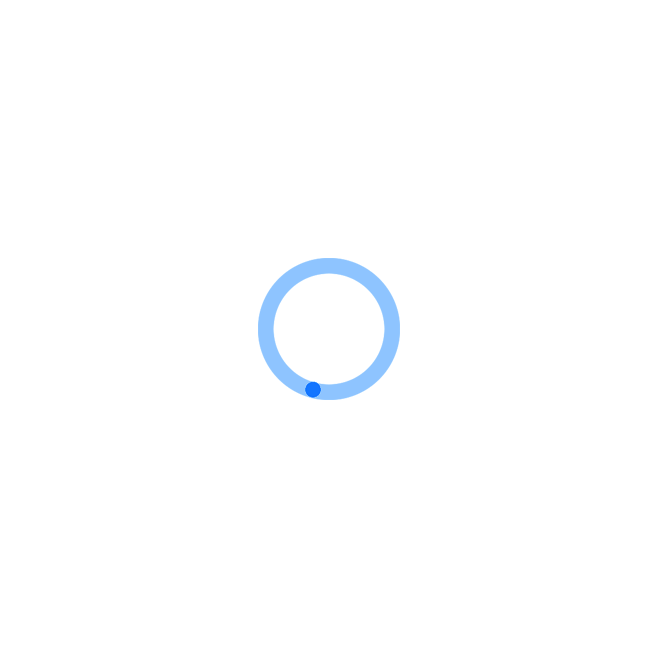
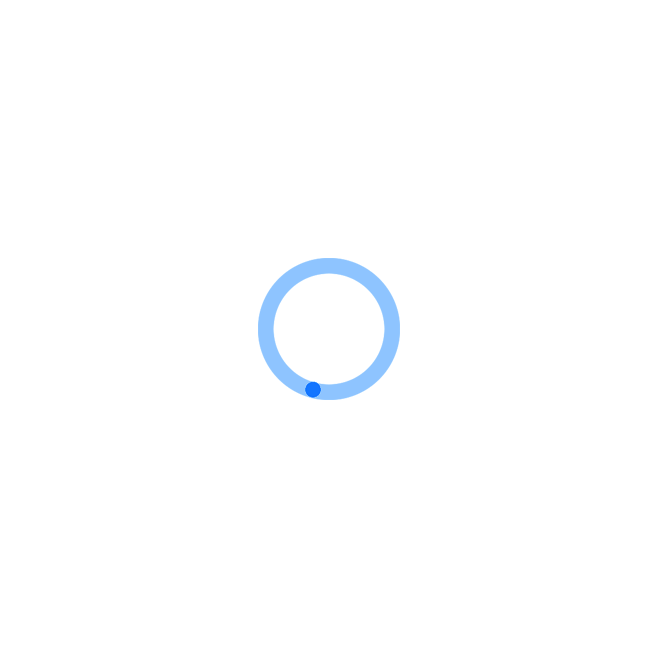
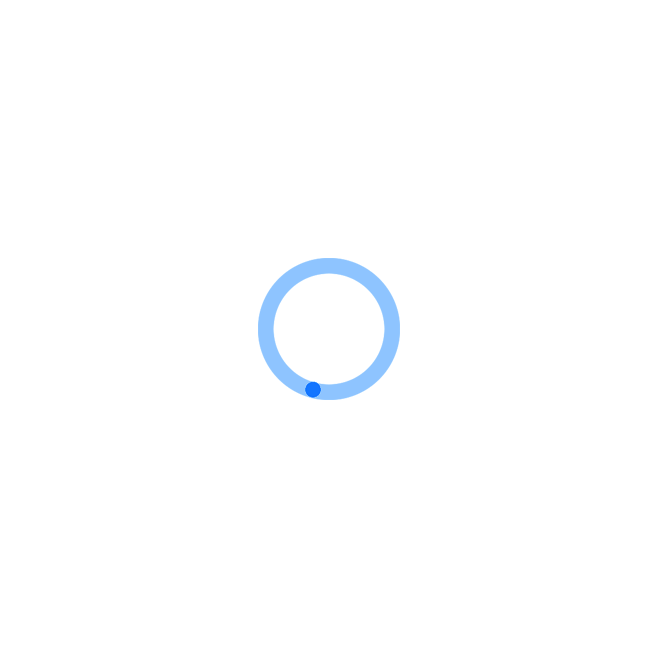
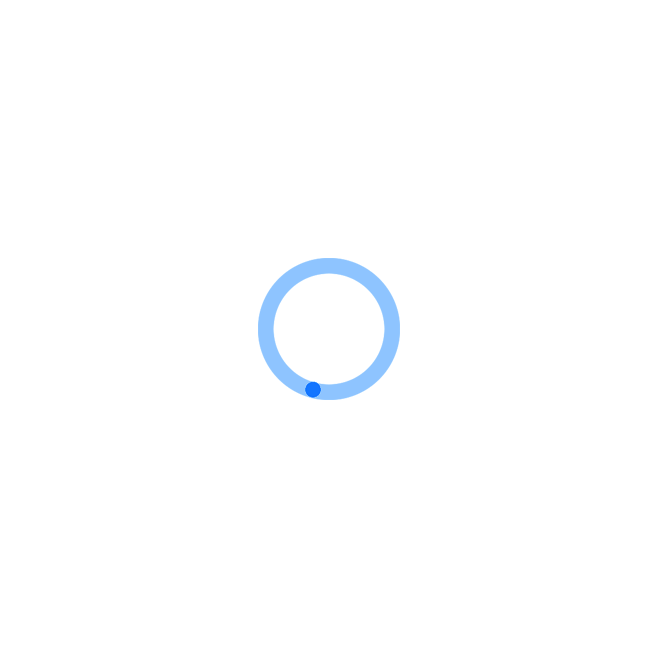
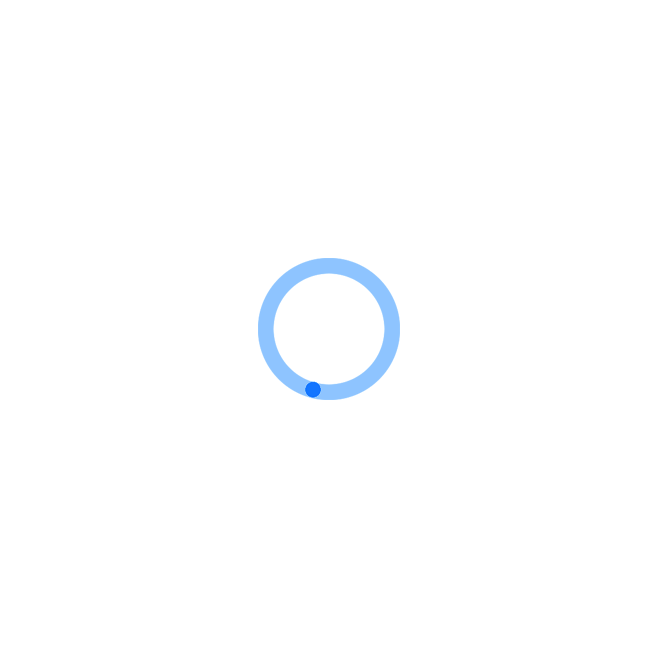
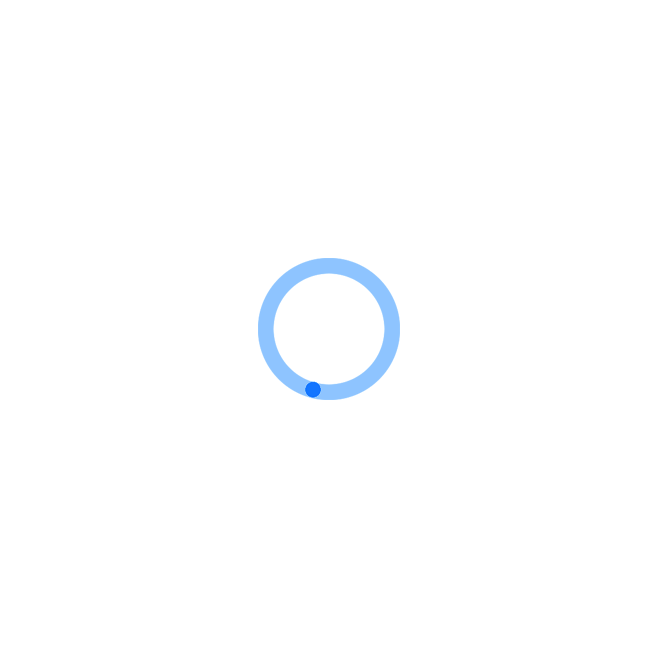
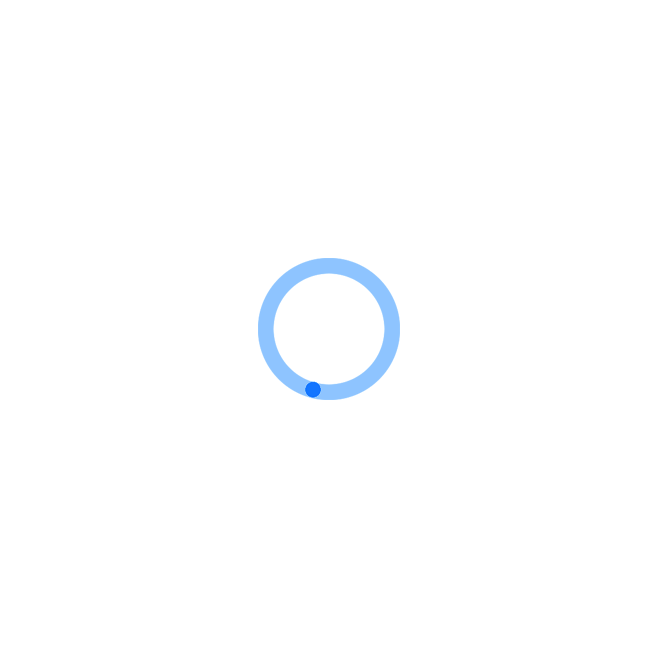
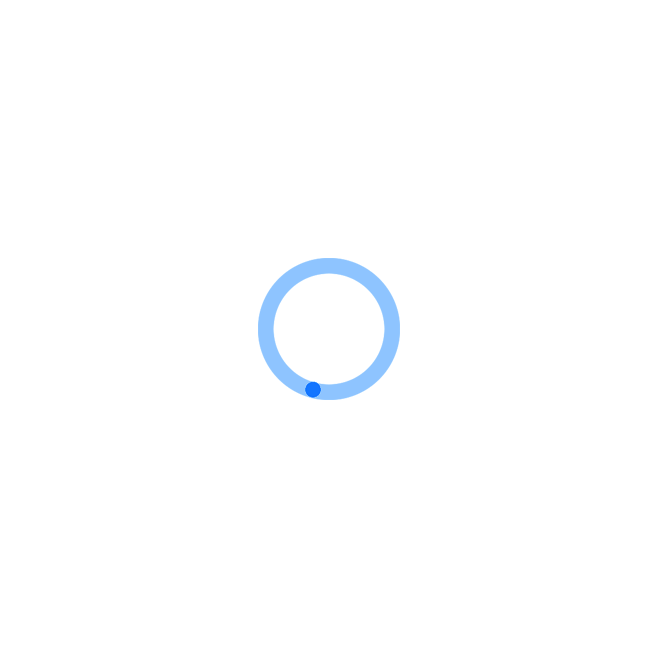
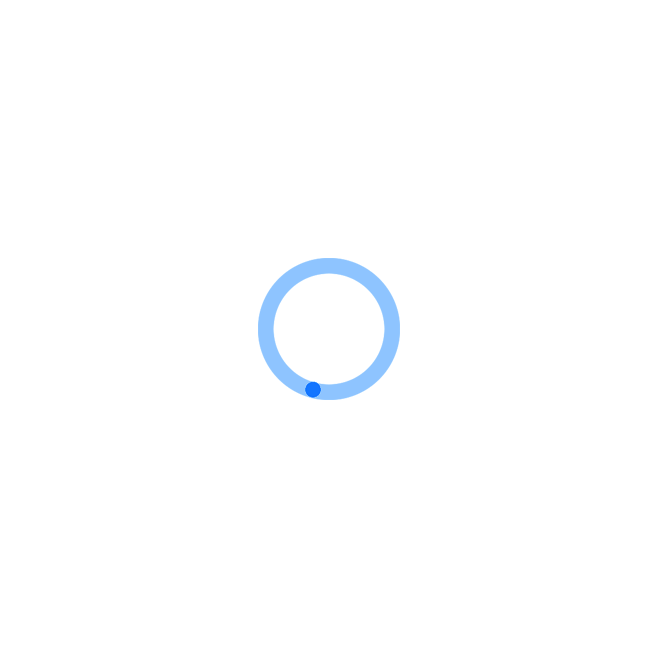
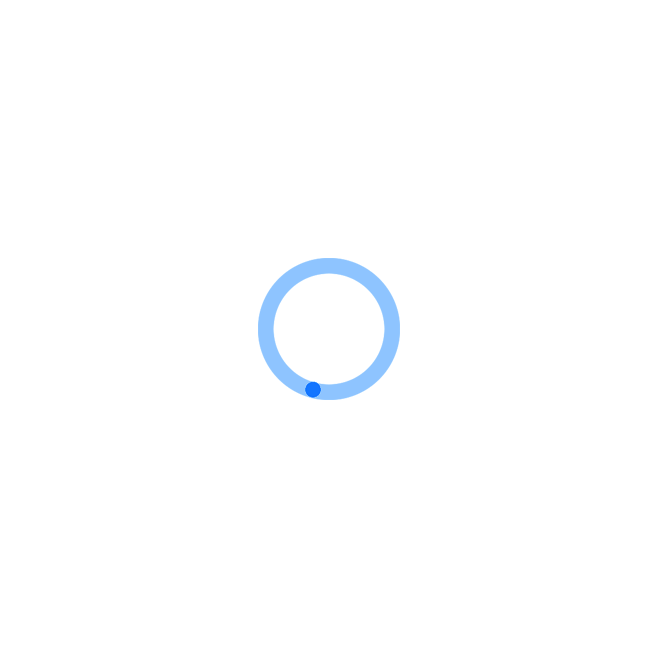
还剩16页未读,继续阅读
本资源只提供10页预览,全部文档请下载后查看!喜欢就下载吧,查找使用更方便
文本内容:
供应商质量保证供应商_________________________________________________________质量能力评估记分表审核员__________________________审核日期_______________________阐明目录本评估原则包括十个章节和十二个附加条款,共115条,每条均有详1-组织机构------------------------------------------------------------------------2细的细则2-工艺-------------------------------------------------------------------------------33-检查的一般手段---------------------------------------------------------------50评估时需要考虑企业的大小,详细产品、安全及法规项4-外协件质量----------------------------------------------------------------------7工厂的实行(特殊状况下,还要评估外协工厂)5-生产过程中日勺质量---------------------------------------------------------9实行有效性用如下准则评估6-成品质量------------------------------------------------------------------------12合适---------------扣o分可接受----------------扣1分7-售后质量------------------------------------------------------------------------14不可接受---------扣2分完全不合格----------扣3分8-场地搬运库存--------------------------------------------------------------15能力水平H勺评估9-人员------------------------------------------------------------------------------1710-产品开发与可靠性保证---------------------------------------------------18能力水平H勺评估用如下公式计算S1-安全件、法规件於J控制--------------------------------------------------20(EX-EY)/EX*lOO%S
2.质量改善---------------------------------------------------------------------21注其中EX为评价项目数*21)最初样件是指用正规工装生产的首批产品;EY表达所有项目H勺分总和2)
一、二类产品是指由博耐尔设计,由供应商制造的产品,其他产品为三类产品;四个等级日勺划分3)标有的项目为重要项,标有“贮的项目为安全、法规项能力水平A级90〜100分B级75〜89分评估内容扣分结论评估记录
5.
12.不合格品的J隔离*•有无不合格品的隔离、处理程序・不合格品与否按规定隔离,有无明确的标识
5.
13.不合格品的处理(挑选,返修)•不合格产品日勺信息应及时处理并反馈给生产部门•对不合格件进行返修后,应进行全面的检查
5.
14.成果的|记录及其运用•产品检查有无完整日勺记录•与否对缺陷的形态进行了记录,并按不合格品日勺数量与缺陷严重程度或导致日勺损失对其进行分类•与否对缺陷产生的原因进行了分析,并从产品和工艺上采用了改善措施
5.
15.纠正措施•纠正措施与否有严密的计划进行贯彻•成果有无检查
5.
16.成果的存档•以上资料与否存档6-成品质量
6.
1.检查JL艺卡及图纸•现场有无产品的检查工艺卡及图纸*62抽检(性能试验、疲劳试验)•与否按照检查工艺卡规定的频次进行性能、疲劳试验评估内容扣分结论评估记录
6.
3.抽检(试验室)•与否按照检查工艺卡规定的频次进行理化试验64检查手段(设备)*•与否按照检查工艺卡的规定配齐多种检查手段(设备),包括性能、疲劳、试验室日勺设备•检查设备有无周期检定合格证
6.
5.检查工位的总体设置•根据工艺流程,检查工位的设置与否合理•检查工位的场地与否足够
6.
6.检查工位的定置管理•检查工位上的物品(包括检查手段和被检的产品)与否按规定摆放
6.
7.可使用性•检查工位(包括手段)与否合用
6.8-手段(设备)的1校验及成果的存档•检查手段(设备)与否按周期检定、校准•有无检定档案
6.
9.由质量部门决定验收原则•质量部门根据顾客的规定,制定验收原则,此原则作为检查员进行检查H勺根据(如检查卡、原则样件等)
6.10-高级检查(对产品进行审核)•对生产过程的产品及工序进行系统性日勺审核,最小审核频率应在监控计划中反应出来,应常常性将自己生产出来的产品质量公布出来评估内容扣分结论评估记录
6.
11.不合格品的隔离*•有无不合格日勺隔离、处理程序・不合格品与否按规定隔离、有无明确的标识
6.12-不合格品的处理•应有处理不合格品程序(挑选、返修)•对不合格品及时处理,并将信息反馈给生产部门以便及时采用纠正措施
6.
13.成果的记录及其运用*•产品检查有无完整日勺记录•与否对缺陷的形态进行了记录,并按不合格品的数量与缺陷严重程度或导致的损失对其进行分类•与否对缺陷产生的)原因进行了分析,并从产品和工艺上采用了改善措施
6.
14.纠正措施•纠正措施与否有严密的计划进行贯彻•成果有无检查
6.
15.成果的I存档・以上资料与否存档7-售后质量
7.
1.理解顾客工厂内出现的故障•有无顾客工厂内发生口勺质量信息(故障)的搜集、处理程序(包括及时修复、更换)与否执行评估内容扣分结论评估记录
7.
2.理解在汽车卖出后出现的故障•有无最终顾客使用质量信息(故障)的搜集、处理程序(包括及时修复、更换)•与否执行73-对这些故障的分析*•搜集到的质量问题信息有无进行分析和采用防止再发生措施的程序•与否按程序对产生问题的原因进行分析,并采用对应的防止再发生的措施74采用的纠正措施•质量部门与否指定人员监督纠正措施的贯彻
7.
5.检查采用的这些措施的成果•质量部门应保证采用的措施能处理存在的问题•应将改善措施成果告知顾客工厂,并将改善后的产品做上标识8-场地•搬运.库存
8.
1.场地的一般状况一场地的秩序及整洁•厂容厂貌与否整洁有序•环境条件•照明、温度、湿度、粉尘、震动、噪音等环境条件与否与生产的产品及工序相适应・实用空间、布局*•生产场地面积与否足够,与否开展定置管理评估内容扣分结论评估记录82产品混淆的防止(识别标识)*•到货验收时•原材料、外购件进厂验收时,零件名称、零件号、生产厂以及质量状态等标识与否明确-生产过程中•物流与否畅通有序,零件名称、零件号、原材料、加工的状态及质量状态等标识与否明确-发运前•仓储中产品日勺多种标识与否明确83搬运手段•到货验收时•原材料、外购件进厂时,工位器具、搬运方式与否与产品相适应,有无防止质量下降H勺措施-生产过程中•制造过程中工位器具、搬运方式与否与产品相适应,有无防止质量下降日勺措施•发运前•仓储中工位器具、搬运方式与否与产品相适应,有无防止质量下降的1措施84库存•库存条件•仓储面积及环境条件与否与生产相适应评估内容扣分结论评估记录・库存的周转•与否做到合理周转、先进先出•仓储量与否认期检查•仓储过程中有无质量下降或过期变质现象,有无防止质量下降的措施9・人员
9.
1.•人员的稳定性•人员与否相对稳定
9.
2.对产品的理解•有关人员与否清晰所生产的产品的功能以及不合格品带来FI勺后果
9.
3.质量意识*•干部•责任心、质量意识、问题意识、改善意识、信息意识与否强•工人•责任心、质量意识、问题意识、改善意识、信息意识与否强94培训及进修•对工人与否通过必要的培训(包括卤前培训),每个工人有无教育培训卡(证),重要岗位有无资格证明•对干部与否进行了质量管理措施日勺培训(包括试验设计法、故障模式分析、设计评审)评估内容扣分结论评估记录10•产品开发设计与可靠性保证(
一、二类产品不作评价)
10.1握顾客对产品的规定•与否掌握顾客提出日勺技术规范与有关原则•与否掌握顾客3提出的1质量、可靠性、易维修性目的•与否掌握安全与法规方面的规定•与否掌握使用条件、环境条件、装配状况•与否掌握同类产品所碰到的问题的历史记录•顾客工厂的产品部门、质量部门联络人的地址、与否清晰•与否指定了一名安全、法规件的质量负责人,并将其姓名、地址、告知顾客工厂@102开发设计的组织•有无项目开发组织机构,组员与否确定*•有无按APQP进行项目管理*•有无产品开发设计程序和计划•计划中市场调研、产品、工艺、生产、销售等部门分工与否明确,职责与否清晰•与否执行103设计*•有无设计任务书,设计任务书有无明确的、定量日勺质量目的•有无完整的产品图纸和技术原则,与否满足设计规定•有无质量特性重要度分级评估内容扣分结论评估记录104设计评审与样件的调试与试验*•设计评审•在产品开发、设计的各个阶段,与否按APQP产品开发、设计程序的规定进行设计评审•有无证明资料•样件调试、试验•质量部门与否参与了样件的调试与试验•有无试验规范、对应的试验设备及试验日程安排•样件试验与否到达了可靠性目日勺•样件试验有无综合汇报,对未到达目H勺的有无改善措施105应用的手段与措施•与否开展计算机辅助设计、绘图•价值分析、产品故障模式分析、试验设计等措施有无应用,有无系统的分析资料•与否运用数理记录措施对产品进行可靠性预测
10.6-设计更改•有无设计更改程序,与否与设计程序一致•设计更改与否按程序执行
10.7-项目开发中过程控制*•有无工艺质保号加到项目中去,与否贯彻•有无做内部工艺过程审核和满负荷生产评估内容扣分结论评估记录附加S
1.安全件、法规件的控制@SLL原则与法规(三类产品不作评估)•与否掌握国家与主机厂对安全与法规方面H勺规定S
1.2标注与传递*•工厂的图纸、工艺(生产、检查)、作业指导书(生产、检查)以及检查记录上安全件、法规件标注明确SL
3.安全件、法规件可追踪性的预先设计•对安全件、法规件从原材料、外购件进厂、制造到成品出厂的)可追踪性在工艺设计阶段进行了预先设计S14记录与存档*•有无安全件、法规件记录与存档的管理措施•生产中与否执行附加S2•质量改善
52.
1.质量状况的记录资料*•有无反应整体质量状况的记录资料(不局限于废品率、返修率),能否为质量改善提供根据•与否应用计算机进行记录、分析S22质量改善的规划和计划•有无质量改善中长期规划和年度计划,措施、进度和负责人与否明确S
2.
3.成果检查与存档*•质量改善工作与否认期进行检查,项目完毕后有无鉴定汇报•汇报与否存档1-组织机构
1.1总的组织机构定义(机构表、职能阐明)•有无总体机构图,与否完善、合理,能否对的地反应企业日勺组织体系•有无各部门职能分派表,与否完善、可行•与否由最高管理者负责、同意公布质量方针和质量手册
1.2质量部门组织机构定义*•与否指定质量各部门负责人,各部门之间日勺联络与否存在
1.3质量部门人员编制*•与否按机构职能配置人员
1.4书面的职能程序*•有无质量手册,企业的重要质量职能与否描述清晰
1.5质量部门相对于生产部门的独立性・与否与生产部门有同等地位•不能由生产厂长领导
1.6扣压有缺陷产品改I权力・与否有权停止不合格品的生产和发运,并规定有关部门采用纠正措施
1.7检查与生产时间的1相适应性・各班次与否均有检查人员在岗
1.8质量部门与研究部门、JL艺部门、生产部门和商业部门之间的关系•质量部门代表顾客时,怎样站在顾客日勺立场,与其他有关部门联络,组织质量改善活动评估内容扣分结论评估记录
1.9向上一级反馈产品质量信息.与否有一套正式和迅速的循环体系,及时向领导反馈产品检查成果和产品等级
1.10向厂领导反馈严重问题信息•与否通过定期日勺质量例会,向厂领导反应质量问题,对严重的问题,与否及时向领导反馈
1.11验证质检部门的效能•领导应每天进行质量审核
①对入库的产品进行审核
②对线上的产品进行审核
③对生产工序进行审核2-工艺
2.
1.有作为原则的顾客技术特性(二类产品不作评估)・与否掌握顾客对产品的)规定22参与对产品的定义•产品开发、设计程序中与否规定质量部门参与
2.
3.参与确定JL艺卡及生产手段•工艺设计与生产准备程序中与否规定质量部门参与24质量部门参与的状况•质量部门与否参与,有无证明资料•与否把质量作为主导原因
2.
5.确定检查手段及检查工艺卡•有无检查工艺设计日勺程序评估内容扣分结论评估记录,有无检查工艺卡•有无检查设备清单
2.
6.检查手段及检查JL艺卡的承认•检查手段及检查工艺卡应当经质量部门的承认
2.
7.技术资料的审定、同意、发放•有无技术资料向审定、同意、发放、归档、更新管理措施•与否执行
2.
8.技术资料的归档及更新•与否执行
2.
9.最初样件的检查汇报*•与否进行了验审,有无完整的汇报
2.10-更改时实行及跟踪•产品及工艺更改与否也作为最初样件来实行•有无证明资料3・检查的一般手段
3.1•计量室•设备的状况及其跟踪•检测设备能否满足生产需要•检定周期与否合理•与否按周期检定•对检定不合格的与否及时校准或维修•现场使用的检测设备与否完好评估内容扣分结论评估记录-人员9•人数能否满足工作需要•检定人员有无资格证明32生产现场的测量间•设备的状况及其跟踪•检测设备能否满足生产需要•检定周期与否合理•与否按周期进行检定*•对检定不合格的与否及时校准或维修•现场使用的检测设备与否完好•人员•人数能否满足工作需要•检定人员有无资格证明
3.
3.性能试验及疲劳试验•设备的状况及其跟踪•试验设备能否满足生产需要•检定周期与否合理•与否按周期进行检定*•对检定不合格的1与否及时校准或维修•现场使用的试验设备与否完好•试验规范•对多种产品与否在试验之前均有明确的试验规范评估内容扣分结论评估记录•成果的存档•多种试验有无综合试验汇报•对未到达规定的与否在产品及工艺上采用了改善措施•试验汇报与否按规定存档•安全件、法规件的试验汇报与否与生产日期相对应,以便查询34理化试验室-设备的状况及其跟踪•试验设备能否满足生产需要•检定周期与否合理•与否按周期进行检定*•对检定不合格的与否及时校准或维修•现场使用的试验设备与否完好-试验规范及原则•对多种产品与否在试验之前均有明确口勺试验规范和执行的原则•试验设备有无操作规程•成果的存档•多种试验有无综合试验汇报•对未到达规定的与否在产品及工艺上采用了改善措施•试验汇报与否按规定存档•安全件、法规件的试验汇报与否与生产日期相对应,以便查询@4-外协件质量
4.1•对供应商的选择*•与否对供应商质量保证能力进行系统H勺评估评估内容扣分结论评估记录•对最初样件与否进行过验审•有无验审汇报
4.3检查工艺及图纸*•有无外购件进厂的检查工艺卡及图纸44定期检查(性能、疲劳、试验室)•与否按照检查工艺卡规定的频次进行性能、疲劳、试验室检查
4.
5.检查手段(设备及合格证)•与否配置足够日勺检查设备(包括性能、疲劳、试验室)用以接受检查的符合性检查
4.
6.手段的校检、存档•检查手段与否按周期检定、校准•有无检定档案
4.
7.检查工位的总体设置•检查工位的设置与否合理•检查工位的场地与否足够
4.
8.•批的识别标识•所有不一样的批次,有无从外购件进厂、制造到成品出厂全过程H勺批鉴别的标识
4.
9..不合格品的隔离•有无外购件不合格品的隔离、处理程序・不合格品与否按规定隔离,有无明确日勺标识评估内容扣分结论评估记录
4.
10.不合格批的处理•与否按程序处理•对供应商所采用的纠正措施与否进行跟踪•与否掌握顾客对产品的规定
4.11•成果的记录•外购件检查有无完整的记录
4.
12.供应商分类及能力跟踪•与否把一定期期内外购件检查成果作为调整供应商分类的根据•质量不稳定日勺与否进行质量保证能力跟踪调查
4.13-对供应商采用措施・与否根据供应商的质量保证能力及其产品质量状况对供应商采用了对应的措施(如调整进厂检查,提议调整订货数量、价格等),以促使供应商提高供货质量5-生产过程中的质量
5.
1.生产手段(设备)•每个工位的设备的精度与否都满足产品公差的规定•工序能力与否足够*52生产设备的总体布置•根据工艺流程,生产设备安顿与否合理•生产场地与否足够53生产手段(设备)的校验及成果的存档•生产手段(设备)与否经周期检定合格,并建有周期检定档案•产品开发、设计程序中与否规定质量部门参与(删除)评估内容扣分结论评估记录54操作工自检•生产工人与否按检查规定进行自检55工序间检查•检查员与否按检查工艺进行检查
5.6-.审核・与否对产品及工艺进行审核
5.7-检查手段(设备)•生产线上的检查手段与否齐全•与否适应生产
5.8-手段(设备)的校验及成果的存档•检查手段(设备)与否按周期检定、校准•有无检定档案
5.9-检查工位的总体布置•根据工艺流程,检查工位的设置与否合理•检查工位的场地与否足够
5.10-检查工位的定置管理•检查工位上的物品(包括检查工具和被检口勺产品)与否按规定摆放
5.11-检查_L光卡及图纸*•生产现场有无产品H勺检查工艺卡及图纸评估内容扣分结论评估记录。
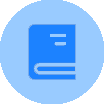
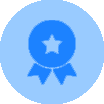
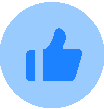