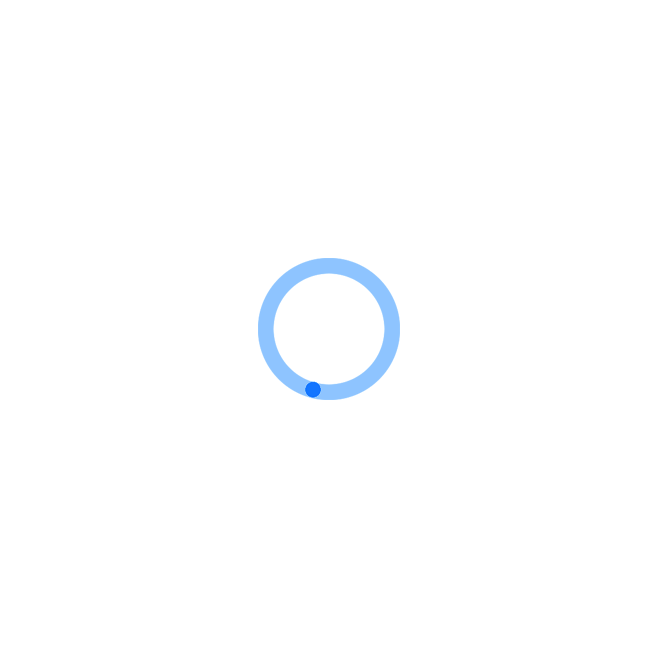
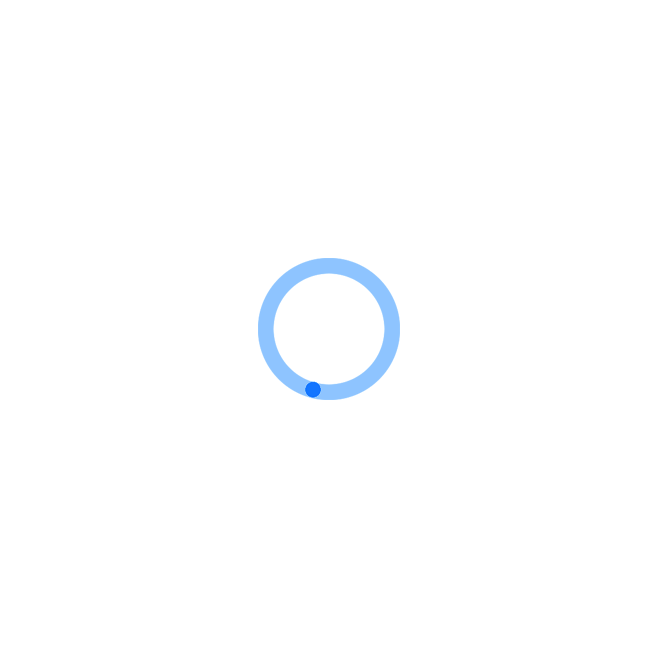
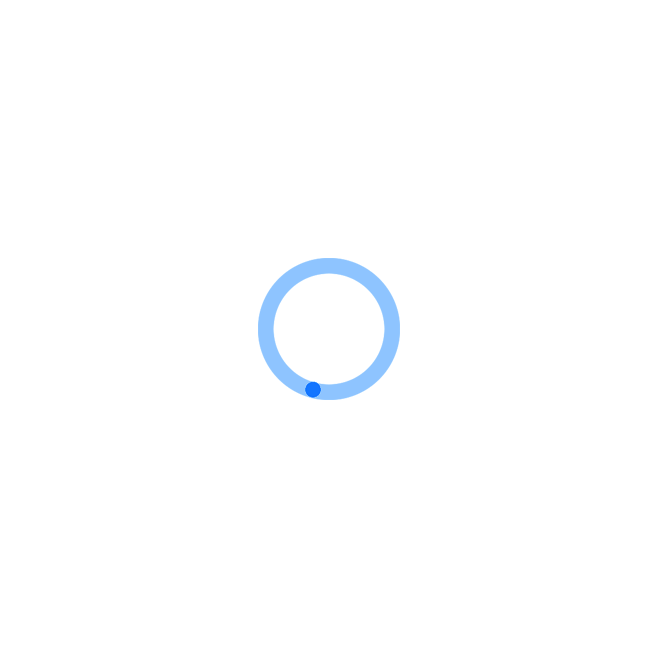
还剩1页未读,继续阅读
文本内容:
断点管理规定版本状态记载版次实施日期更改单号更改原因编制审核批准A/
02017.
08.01//王彩艳洪杰胜姚春峰1目的指导因变更引起的新、老状态零件切换工作,如何进行断点控制,尽量避免呆滞物料同时保持可追溯性另外,指导项目批量生产终止过程中的断点管理工作2适用范围适用于本公司的断点管理3职责
1.1市场部负责确认客户的断点信息,与客户确认各时间节点,及时传递信息至其他相关职能部门
3.2生产部负责客户和供应商断点信息管理,编制断点期间的生产控制、盘点等计划,监控产成品、相关零部件、原材料、外协件的库存,并将断点时间通知下一级供应商
3.3技术中心、品质部负责断点期间内部质量监控4工作程序
4.1一般变更
4.
1.1切换准备
4.
1.
1.1变更通知发布,变更提出部门组织召开切换准备会议,发布切换准备时间计划
4.
1.
1.2技术中心发布新零件BOM、图纸,发布客户工程认可文件
4.
1.
1.3生产部发放采购BOM,更新供应商清单
4.
1.
1.4SQE发布新零件PPAP认可计划,签署并提交PSW文件
4.
1.
1.5生产部发布备货通知给供应商同时进行供应商产能调查,制定PPAP生产计划,并按计划完成生产用物料备料、零件上线等
4.
1.
1.6技术中心发布客户正式的PPAP认可
5.
1.2切换实施
4.
1.
2.1我公司获得客户正式的切换通知后,生产部向供应商发布老零件断点通知、盘点通知
4.
1.
2.2生产部按照盘点计划定期获得供应商及本企业老零件库存信息,定期召开切换例会,反馈切换准备情况,讨论多余老零件的处理方案
4.
1.
2.3新零件到货,生产部进行系统数据维护断点当天,正式完成生产切换,品质部记录断点信息生产部放置/张贴目视化标识
4.1,
2.5涉及需供应商承担的多余物料由生产部负责与供应商协调
4.
1.
2.6对于确认无法使用的老状态零件,生产部集中并清点数量后转入报废物资处理流程
4.2强制变更
4.
2.1对于质量、安全等问题引起的强制变更,要求尽可能早的断点成新零件,由相关部门判定责任方,生产部对老零件进行隔离,发布断点指令,完成强制断点
4.
3.
2.2强制断点时新零件的认可参照相关章节,断点实施参照
4.
1.2章节
4.3批量生产终止/EOP
4.
3.1市场部确认客户EOP相关信息,组织召开EOP准备会议,发布客户总成级EOP零件清单及时间计划
4.
3.2生产部根据总成级清单整理出散件级清单,将EOP信息传递给各供应商
4.
3.3生产部通知供应商盘点,并对长周期零件向供应商进行调查,同时生产部盘点内部仓库、线边库及外库的零件和总成库存,将以上结果反馈至客户
4.
3.4根据EOP节点制定盘点计划,生产部实施盘点,收集盘点结果,召开EOP例会分析可能的呆滞、紧缺物料
4.
3.
4.1距离EOP节点8周以上,每双周盘点,并结合客户盘点节点实施同步盘点
4.
3.
3.2距离EOP节点8周至1周,每周盘点,并结合客户盘点节点实施同步盘点距离EOP节点1周以内,每日盘点,缺件报警
4.
3.4断点当天,根据客户要求实施断点,记录断点信息5附则本制度由技术中心提出并负责解释6签批编制审核批准。
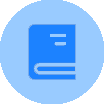
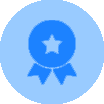
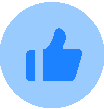