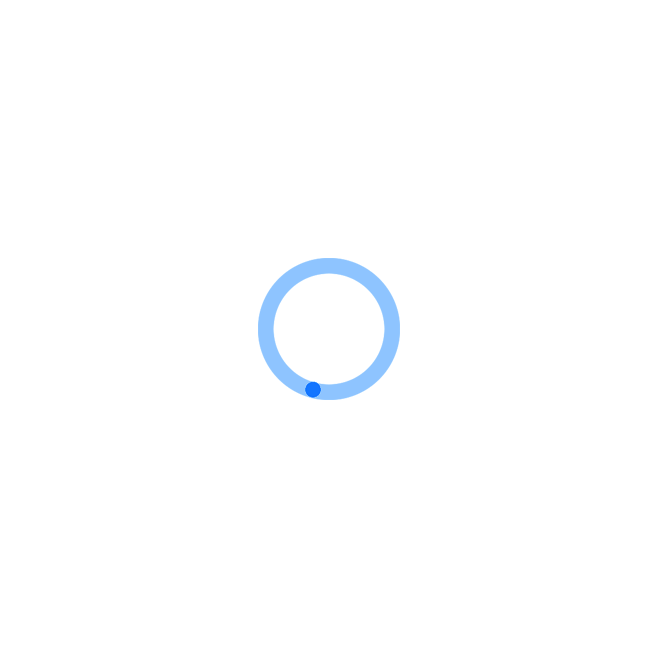
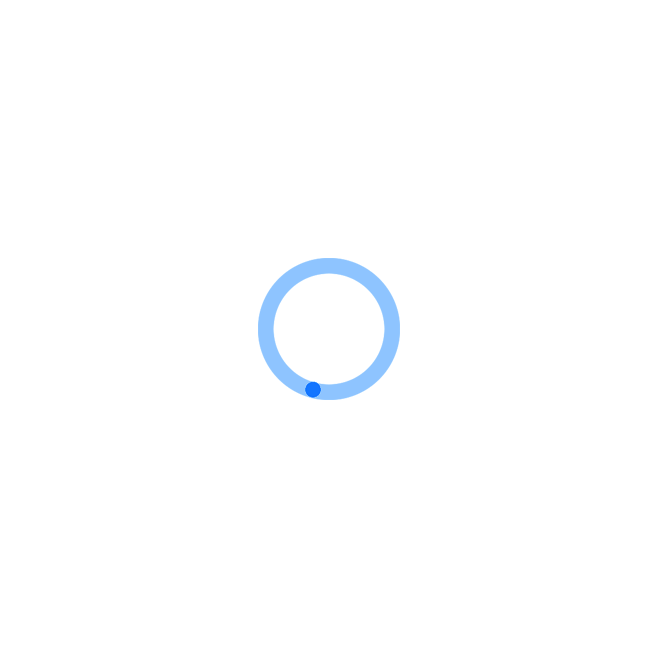
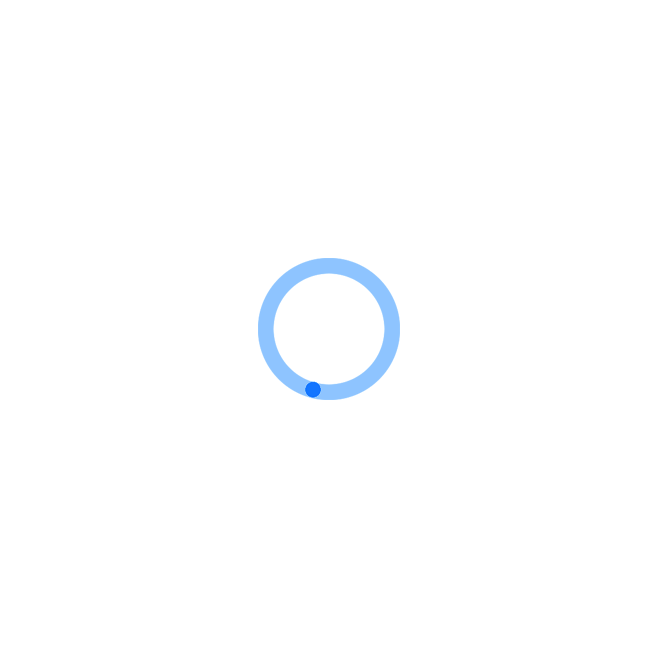
还剩1页未读,继续阅读
文本内容:
目的1为了确保产品质量符合顾客要求,避免使用不合格物料和销售不合格产品O适用范2本公司与产品质量有关的原材料、辅料、半成品、成品检验和试验定义3无参考文件4国家相关标准
4.1《不合格品控制程序》
4.2FA/QEOP-24《新模检验规程》
4.3权责5品管部门负责原辅材料的进厂检验、生产半成品、成品检验和试验
5.1品管部负责各生产工序生产过程监控以及检验记录的控制
5.
2、作业程序6进料检验
6.1仓库仓管员在收到外购产品后,及时进行标识,并通知品管部进行检验
6.
1.1睡由化验室人员依据《国标》和内控标准进行检验,主要检测其成分含量是否符合标准,
6.
1.2检验后应记录于《原辅材料检验报告单》化工试剂主要包括硫酸等化学物品,化验人员依据《化学试剂检验标准》进行检验,检验
6.
1.3后应记录于《原辅材料检验报告单》新开模具检验新开发或新购进得模具将依据《新模检验规程》进行试模,并填写《新模
6.
1.4样品检验报告》其他辅料检验人员应核对品名、规格、厂商、数量等项目进行检验,检查应记录于《原辅
6.
1.5材料检验报告单》中检验后的产品须作检验状态标识,合格品办理入库,未经检验合格产品不准办理入库及使
6.
1.6用,检验发现不合格品依据《不合格品控制程序》处理过程检验
6.2熔铸过程碱厂621化验室负责对熔铸过程中的熔铝水进行化学成分检测,确保各成分含量符合要求,下蒋检测结果记录于《熔铸车间成分分析报告单》,在铸棒过程中应再次取样进行各成分的含量的检测,并记录于《熔铸车间铸棒检验报告单》检验不合格的应依据《不合格品控制程序》进行处理挤压检验
6.
2.1)、挤压首件检查在机台生产新的段面型材时,品管员应负责进行首料检验,主要检查a外观(划痕、拉伤等)壁厚、尺寸是否符合所设定参数要求应将设定壁厚、实际壁厚等内容记录于《挤压型材检验记录》)、挤压过程检查品管部负责生产过程进行检查,每挤压根铝棒进行抽检一次,抽b3-5检数量依据《抽样检测规定》执行,主要进行产品的壁厚、外观,尺寸等项目的检验,并将检验结果记录在《挤压型材检验记录》)、装框复检成品锯切装框后应对产品的尺寸、表面质量、支数是否符合订单要求进行c检查,并记录在《挤压型材检验记录》时效工序检验
6.
2.2依据客户要求对型材进行时效处理,时效检验员负责对时效处理后每框型材的硬度进行抽验,并记录在《时效记录表》上对无表面处理要求得型材经检验合格后可进行包装入库表面处理过程检验
6.
2.3)、槽液检测化验室负责在每天的生产前或生产过程中对喷涂车间前处理各槽液和氧化a车间各槽液进行取样分析,并将检测结果记录在《氧化槽液分析报告单》、《电泳槽液分析报告单》、《粉末喷涂槽液分析报告》)、氧化处理成品检验b品管员负责对氧化成品检验,主要对表面质量、尺寸、膜厚等项目进行检测,并将检测记录填写在《表面车间膜厚记录》《氧化、电泳成品检验日报表》;化验室对阳极氧化着色型材和电泳涂漆型材涂层的性能(氧化膜厚度,封孔质量、颜色等项目)进行检测,并填写《阳极氧化着色型材性能检测报告》《电泳涂漆型材涂层性能检测报告》)、喷涂处理成品检验c喷涂前处理应对产品的长度、尺寸、角度、弯曲扭拧等项目进行检验,并记录在《喷涂中检日报表》,在喷涂过程中品管员应对每挂成品的膜厚进行抽检,检验记录填写于《表面车间膜厚记录表》,品管应负责对最终成品的色差、长度膜厚,表面质量等项目进行检验,并记录在《喷涂成品检验日报表》,以上检验过程若发现不合格依据《不合格品控制程序》进行处理
6.
2.4入库检验
6.3成品检验不合格的产品,依《不合格品控制程序》处理631当检验合格后,方可出货
632、相关表单7删除记录《原辅材料化验报告单》
77.
17.
411.
6.5《新模样品检验报告》
7.2F-《垢力车间成分分析报告单方培铸车间铸棒检验报告单^
7.4《挤压型材检验记录》
7.5《氧化槽液分析报告单》
7.6《电泳槽液分析报告单》
7.7《粉末喷涂槽液分析报告单》
7.8《表面车间膜厚记录》
7.9《氧化、电泳成品检验日报表》
7.10《阳极氧化着色型材性能检测报告》
7.11《电泳涂漆型材涂层性能检测报告》
7.12《喷涂中检日报表》
7.13《喷涂成品检验日报表》
7.14《时效记录表》
7.15。
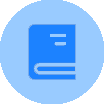
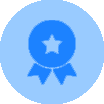
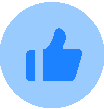