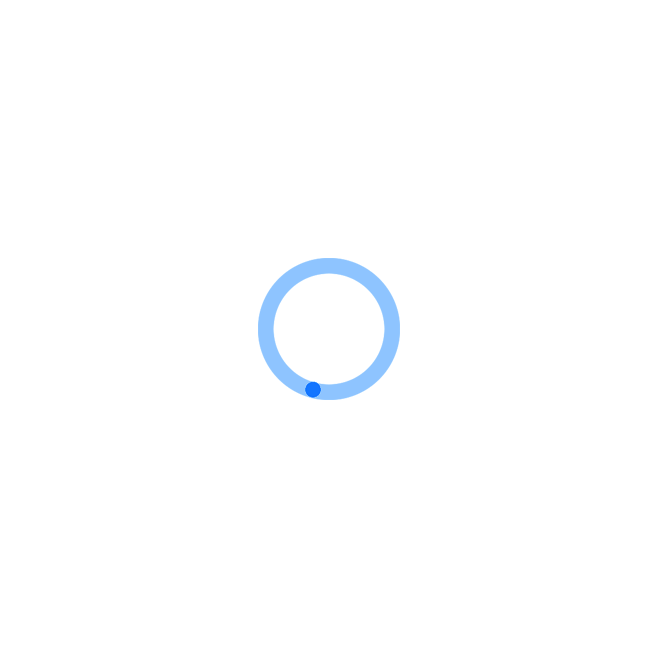
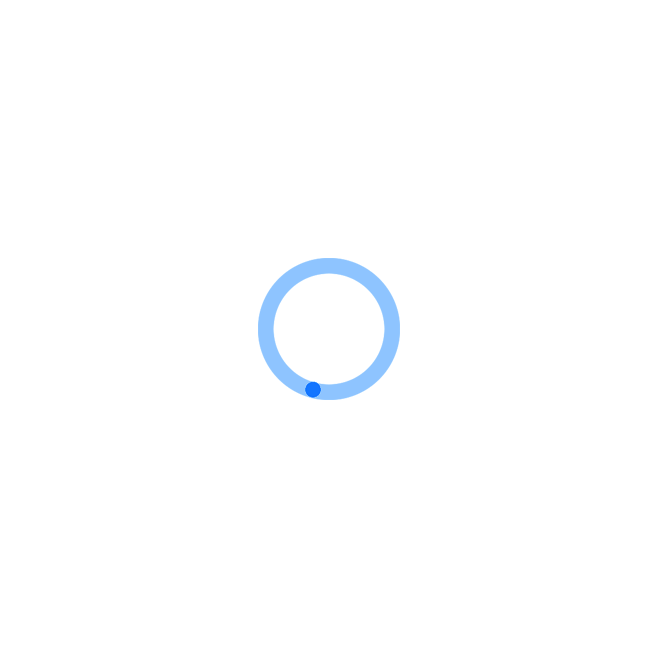
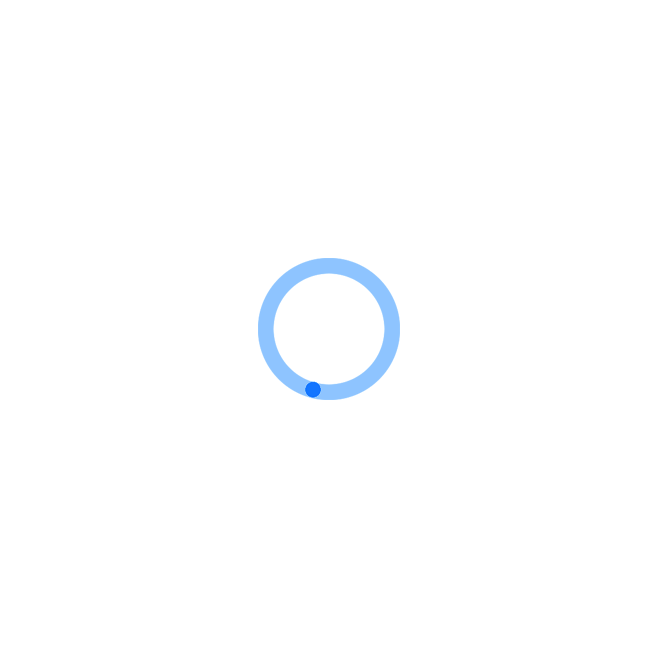
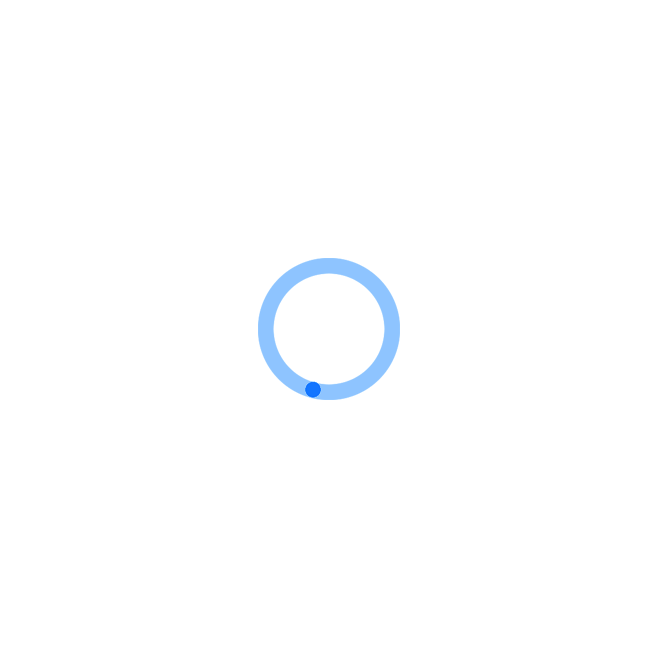
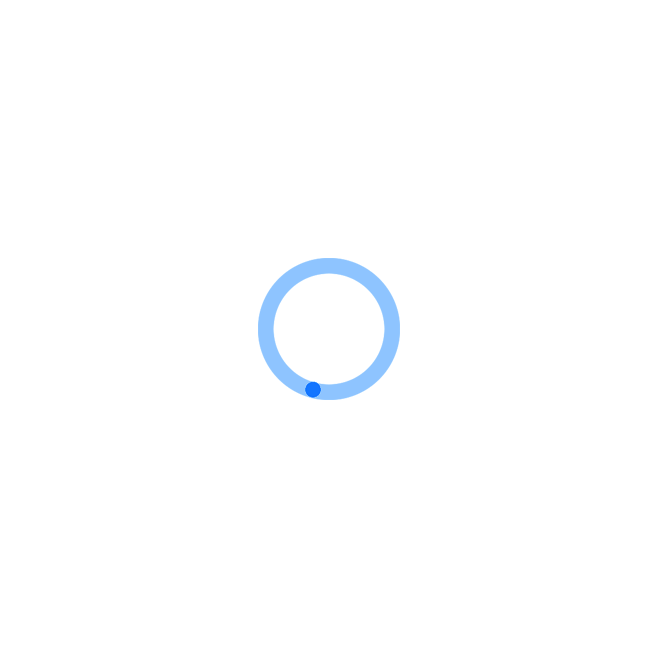
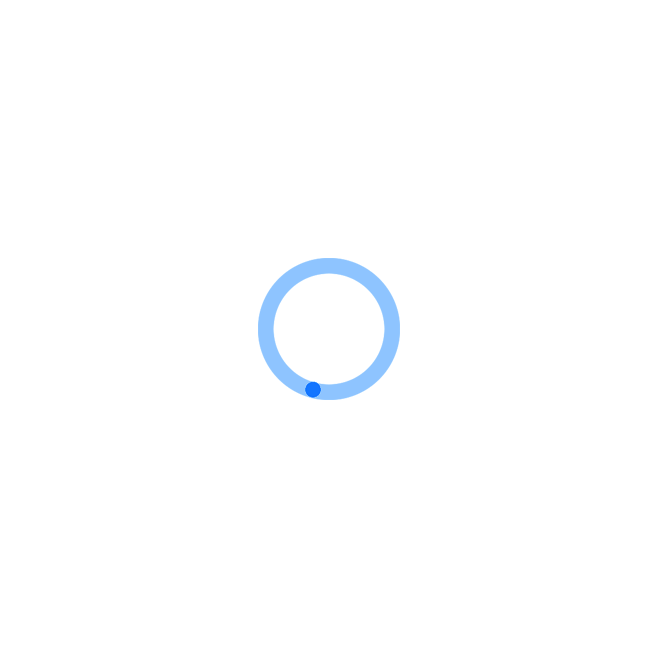
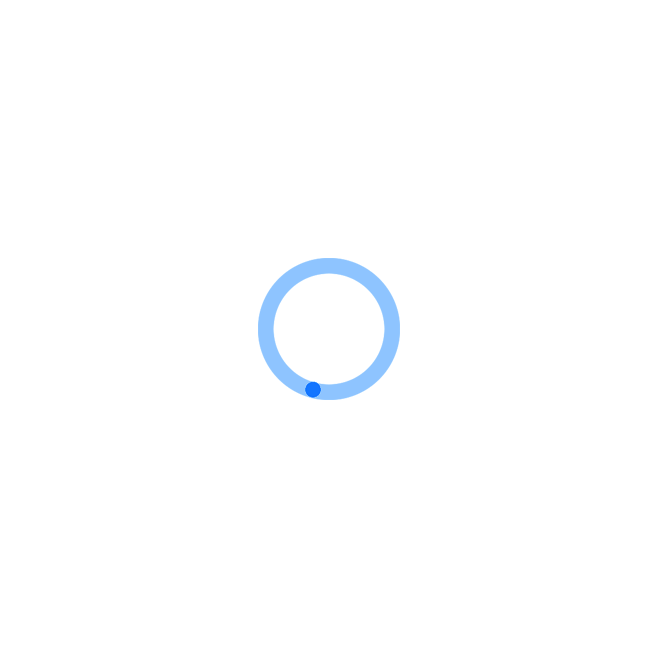
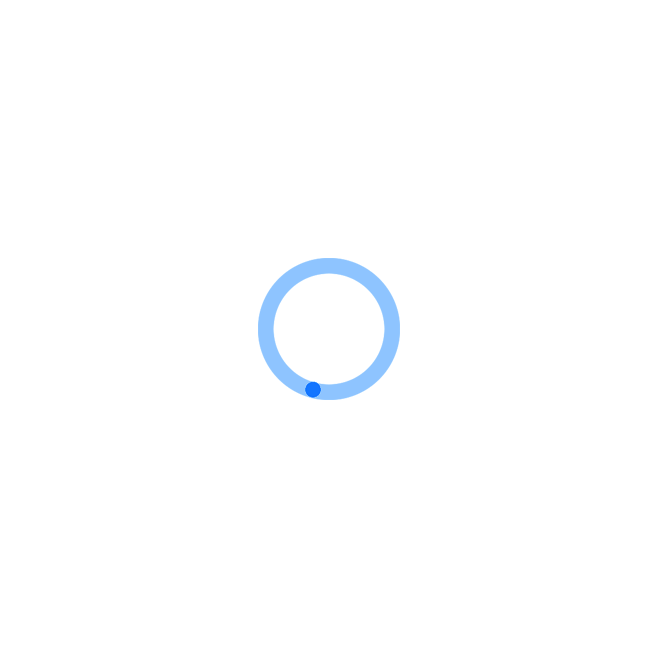
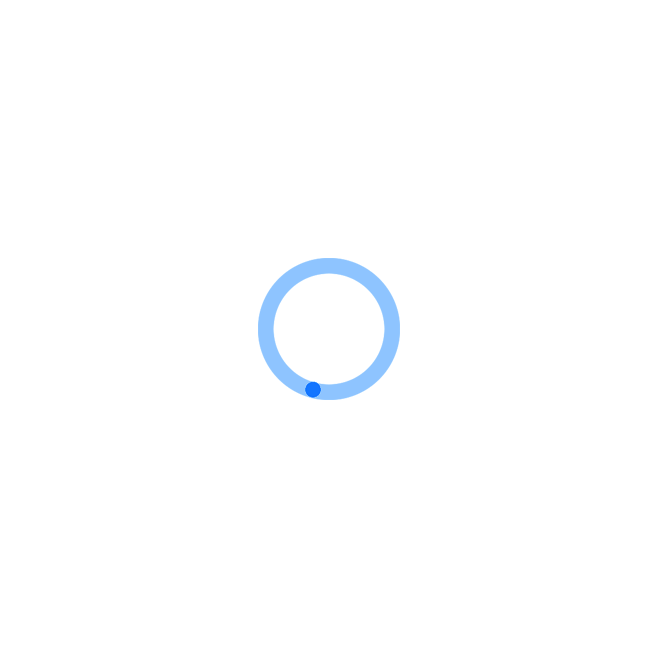
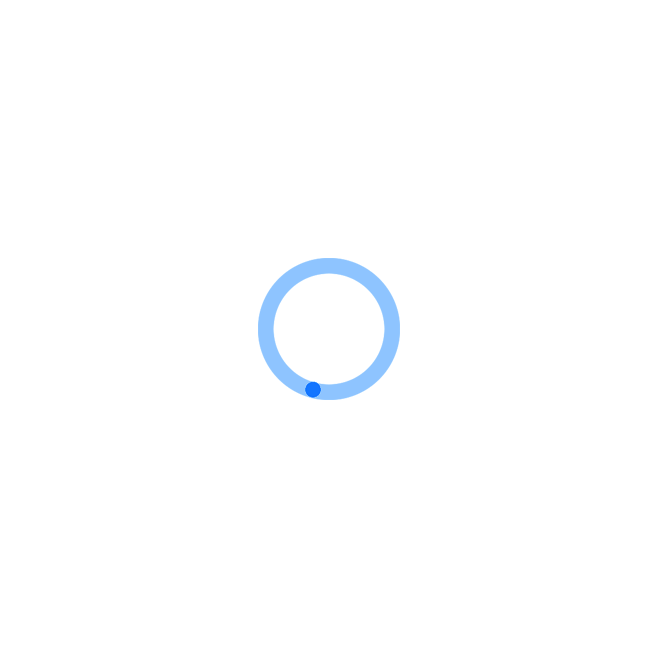
还剩8页未读,继续阅读
本资源只提供10页预览,全部文档请下载后查看!喜欢就下载吧,查找使用更方便
文本内容:
1.62^+
0.0294£可、吟答~式中A=£6,B=1=£3D=cz=i/=1/=1在式3中,被分析事件失效时取-1/2;被分析事件非失效时取1/2在式4中,仅仅当>
0.3时才有效,这一条件通常在d/°y的范围在
0.5〜2之间时才满足注计算方法详见GB/T
24176.2009附录升降法
7.3S-N曲线的测定通常,至少取5级应力水平各级应力水平上试样的数量分配应随着应力水平的降低而逐渐增加,用升降法求得的条件疲劳极限作为S-N曲线上最低应力水平点每级应力水平上试样的数量不少于3个,必要时由双方协商议定以外为纵坐标,N为横坐标,用最佳拟合法绘制成一条曲线,如图5所示注X失效循环次数,N;应力幅,oa,N/mm2;图5典型的S-N曲线图8试验报告试验报告应当包括下列内容a)本标准编号;b)材料的牌号、规格、热处理工艺及常规力学性能;c)试样的制备工艺及其形状、尺寸和表面状态;d)试验机型号;;e)应力循环形式、金、2%、Rf)试验频率/;g)试验过程中任何对本标准的偏离;h)试验结果本标准按照GB/T Ll-2009《标准化工作导则第1部分标准的结构和编写》给出的规则起草本标准修改采用GB/T26076-2010《金属材料薄板(带)轴向力控制方法》本标准结构和技术内容与GB/T26076-2010基本一致,在以下几方面进行了较大修改和补充—范围中增加了-1SRV0的循环应力类型;—试样形状中增加了适合-1WRV0的等截面试样类型,并规定了试样尺寸;—试验程序中增加了试样安装和引伸计安装的细节描述;—结果表示中增加了条件疲劳强度的测定发明专利《一种汽车薄板应变疲劳试验装置及方法》(申请号
202010646804.4),无偿授权给本标准本标准由中国材料与试验团体标准委员会汽车用材领域委员会提出本标准由中国材料与试验团体标准委员会综合标准领域委员会归口本标准起草单位鞍钢股份有限公司、钢研纳克检测技术股份有限公司、中汽研(天津)汽车工程研究院有限公司、中关村材料试验技术联盟、上海大学、山钢集团日照公司、武汉钢铁有限公司、奇瑞汽车股份有限公司、中国第一汽车集团有限公司、泛亚汽车技术中心有限公司、河钢集团股份有限公司、中汽研汽车检验中心(天津)有限公司本标准主要起草人苏洪英、刘仁东、林利、徐鑫、高怡斐、史文、孟宪明、王丽敏、王蓬、吕冬、陆晓锋、芦延鹏、李萧彤、张南、梁笑、李春林、郝志强、丁庶炜、曹政、吴萌、张赛、王存宇、刘培星、沈克、李军、宋伟佳、王彩梅、祝铁柱、熊自柳、李明贺本标准按照GB/T Ll-2009《标准化工作导则第1部分标准的结构和编写》给出的规则起草本标准修改采用GB/T26076-2010《金属材料薄板(带)轴向力控制方法》本标准结构和技术内容与GB/T26076-2010基本一致,在以下几方面进行了较大修改和补充—范围中增加了-1SRV0的循环应力类型;—试样形状中增加了适合-1WRV0的等截面试样类型,并规定了试样尺寸;—试验程序中增加了试样安装和引伸计安装的细节描述;—结果表示中增加了条件疲劳强度的测定发明专利《一种汽车薄板应变疲劳试验装置及方法》(申请号
202010646804.4),无偿授权给本标准本标准由中国材料与试验团体标准委员会汽车用材领域委员会提出本标准由中国材料与试验团体标准委员会综合标准领域委员会归口本标准起草单位鞍钢股份有限公司、钢研纳克检测技术股份有限公司、中汽研(天津)汽车工程研究院有限公司、中关村材料试验技术联盟、上海大学、山钢集团日照公司、武汉钢铁有限公司、奇瑞汽车股份有限公司、中国第一汽车集团有限公司、泛亚汽车技术中心有限公司、河钢集团股份有限公司、中汽研汽车检验中心(天津)有限公司本标准主要起草人苏洪英、刘仁东、林利、徐鑫、高怡斐、史文、孟宪明、王丽敏、王蓬、吕冬、陆晓锋、芦延鹏、李萧彤、张南、梁笑、李春林、郝志强、丁庶炜、曹政、吴萌、张赛、王存宇、刘培星、沈克、李军、宋伟佳、王彩梅、祝铁柱、熊自柳、李明贺汽车用薄钢板第部分轴向力控制疲劳试验方法21范围本标准规定了室温下汽车薄板试样没有引入应力集中轴向力控制疲劳试验的术语和定义、试样、试验条件、试验程序、结果表示和试验报告,提供给定材料在不同应力比下,施加应力和失效循环周次之间的关系本标准适用于厚度为
0.3mm〜
3.0mm的汽车薄板试样不包括缺口试样承受图1所示任一类型、恒负荷轴向循环应力幅的疲劳试验图1循环应力的类型2规范性引用文件下列文件对于本文件的应用是必不可少的凡是注日期的引用文件,仅所注日期的版本适用于本文件凡是不注日期的引用文件,其最新版本包括所有的修改单适用于本文件GB/T3075金属材料疲劳试验轴向力控制方法GB/T3075-2008,ISO1099:2006,MODGB/T3505产品几何技术规范GPS表面结构轮廓法术语、定义及表面结构参数GB/T3505-2009,ISO42871997,IDTGB/T10610产品几何技术规范GPS表面结构轮廓法评定表面结构的规则和方法GB/T10610-2009,ISO42881996,IDTGB/T
16825.1静力单轴试验机的检验第1部分拉力和或压力试验机测力系统的检验与校准GB/T
16825.1-2008,ISO7500-12004JDTGB/T34104金属材料试验机加载同轴度的检验GB/T34104-2017,ISO237882012,MODGB/T
25917.1单轴疲劳试验系统第1部分动态力校准GB/T
25917.1-2019,ISO4965-12012,IDTGB/T24176金属材料疲劳试验数据统计方案与分析方法GB/T24176-2009,ISO121072003,IDT3术语和定义GB/T3075确立的术语和定义适用于本标准4试样
4.1试样形状和尺寸
4.
1.1试样的形状和尺寸取决于试验目的及被测材料的形状其夹持部分应与试样轴线或缩小的试验截面轴线保持同轴或对称
4.
1.2疲劳试验所用的同一批试样应具有相同的形状、尺寸和表面状态
4.
1.3应力比R符合0SRV1时,推荐圆弧形试样,试样的形状和尺寸如图
2、表1所示图2圆弧形试样表1圆弧形试样几何尺寸单位为毫米a W/b raxb
0.3~
3.
01.56b30应力比R符合-1SRV0时,推荐等截面试样,如图3所示
0.02A-B图3等截面试样
4.试样厚度小于1mm时,建议采用防屈曲装置,其几何尺寸需与试样配套并允许在试样宽度的侧边测量应变,防屈曲装置应使试样失效在试验段本标准推荐的防屈曲装置如图4所示1-试样2-聚四氟乙烯板
3.防屈曲板
4.设备夹具图4防屈曲装置防屈曲装置包括上夹具、左右两个防屈曲板及下夹具,防屈曲板与上夹具、下夹具之间分别通过桦卯结构连接将试验机的上、下夹具各切割n个直槽,同时设计左、右防屈曲板与之梯卯连接,这样就使漏出的夹持段宽度W被平均分割成(2n+l)份,相当于减小了未受约束夹持段的“宽度”,从而提高试样刚度防屈曲板中间立段宽度要稍小于试样试验段的宽度应在每个试验开始前通过记录试样在安装防屈曲装置前后在拉伸弹性范围内的应力一应变曲线,比较弹性模量增量,确定附加摩擦力的大小依据试样厚度、强度不同选择不同的锁紧扭矩,一般建议在
0.5Nm〜L4Nm之间,试验过程中保证防屈曲装置不松动的前提下可适当减小锁紧扭矩以减小摩擦力对试验结果的影响应采取一些防范措施防止由于试样与防屈曲装置之间的摩擦引起的力值上升,在试验的任何阶段由摩擦力引起的力值上升不能超过试验力的2%采用约
0.5mm厚的聚四氟乙烯板或氮化硼粉末干燥润滑剂能在一定程度上解决这个问题不推荐使用燃基润滑剂因为它有可能对试验结果产生影响注1直槽数量依夹持段宽度W而定,一般要求被直槽均分后的每段夹持段宽度不大于5mm注2可采用扭力扳手紧固防屈曲装置,施加相同的锁紧扭矩,使防屈曲装置受力均匀,避免因某个螺丝松动而影响试验结果注3聚四氟乙烯板宽度要稍小于防屈曲板中间立段宽度表2等截面试样几何尺寸a hr LcW
0.3〜
1.
03.5〜105-106~107-15单位为毫米推荐试样尺寸见表
24.
1.
4.2试样厚度在
1.0mm〜
3.0mm时,建议不安装防屈曲装置,避免由于防屈曲装置引入的摩擦力影响试验结果的准确性以及试样发热效率偏低的问题,推荐试样尺寸见表3O表3等截面试样几何尺寸单位为毫米a br LcW/b
1.0〜
3.01〜3a3-10a1-3b
1.
54.
1.5矩形横截面试样最小截面尺寸的测量误差不大于±
0.5%
4.
1.6试样夹持部分的横截面积与试样最大应力截面面积之比依夹持方法而定,但不应小于
1.
54.2试样加工
4.
2.1试样所采用的加工工艺应尽可能使试样表面产生的残余应力和加工硬化减至最小,在加工过程中应防止过热或其他因素的影响而改变材料的疲劳性能,力求试样表面质量均匀一致422试样抛光完成后应涂一层防腐蚀油,测试前应将其去除,避免影响测试结果
4.
2.3试样工作部分与圆弧过渡部分的连接应光滑,不得有凹陷
4.
2.4建议纵向铳削或线切割后,再用纵向磨抛的方法进行试验段部分表面的最后精加工
4.
2.5试样测试段表面粗糙度应满足^
0.2nmo5试验条件
5.1试验机的上、下夹具应牢固地夹紧试样端部夹具的中心线应尽量与试验机的施力轴线重合,确保力均匀分布在试样横截面上
5.2试验机施加的负荷值应符合以下要求
5.
2.1试验机静态力的力值准确度应符合GB/T
16825.1的要求
5.
2.2在连续试验10h内,动态力值波动度应符合GB/T
25917.1的要求
5.
2.3为确保试验中施加负荷的一般程序对每个试样保持一样,负荷的动态误差范围应±1%
5.3力循环频率取决于试样刚度和试验要求,所选频率不得引起试样试验部分发热6试验程序
6.1试样的安装
6.
1.1试样在安装时应尽量避免预应变对于先前对中好的试验系统,建议采用位移控制,将试样夹在上、下夹头的一端,然后移动作动器,转为力控制,并将力设置为零,夹好试样的另一端,再装夹引伸计,当其输出归零后,可以进行应变控制转换进行试验
6.
1.2应力比-1SRV0的试验使用防屈曲装置时,防屈曲板与试验机夹具之间的距离应尽可能小,建议不超过2mm,以提高试样刚度,避免造成试样在夹持段屈曲不使用防屈曲装置时,建议将试样夹持段全部放入夹具,减小试样有效试样长度,提高试样刚度,避免试样屈曲
6.2试验控制参数选择
6.
2.1试验频率选择力循环的频率取决于所使用的试验机类型,在许多情况下取决于试样的刚度频率的选择取决于材料、试样和试验机组合如果频率取决于试样和试验机组合的动态特性,就有必要在试验前测量试样的刚度试验频率一般在5Hz〜25Hz范围内,建议采用的试验频率为10Hz〜20Hz同一批试样的试验应在相同的频率下进行在高频率时,试样会产生较大热量,从而影响疲劳寿命和疲劳强度的试验结果如果试样发热,建议降低试验频率如果试样温度超过35C,应在报告中注明注4如果环境影响显著,试验结果可能依赖于频率注5使用防屈曲装置时,试验频率不要超过10Hz,以免试样发热
6.
2.2施加负荷选择
6.
2.
31.1施加负荷应平稳准确、不得超载一组试样中的每个试样加力程序应保持一致平均力和力值范围应该保持在力值范围的±1%内,优于GB/T
16825.1规定的静态误差
6.
2.
1.2建议试样夹持力尽可能小,以降低试样于钳口内断裂的概率
6.3终止试验试样在规定应力下,通常一直连续试验至试样失效或规定循环次数试样失效应发生在试样工作段或最大应力截面处,否则试验结果无效试验过程如有中断,需在试验报告中注明中断时的循环次数和间歇时间7结果表示
7.1由于疲劳试验数据分散度较大,为了获得比较可靠的试验结果,除合理设计疲劳试验方案外,疲劳试验数据应采用数理统计方法进行处理
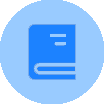
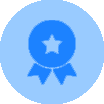
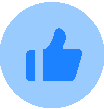