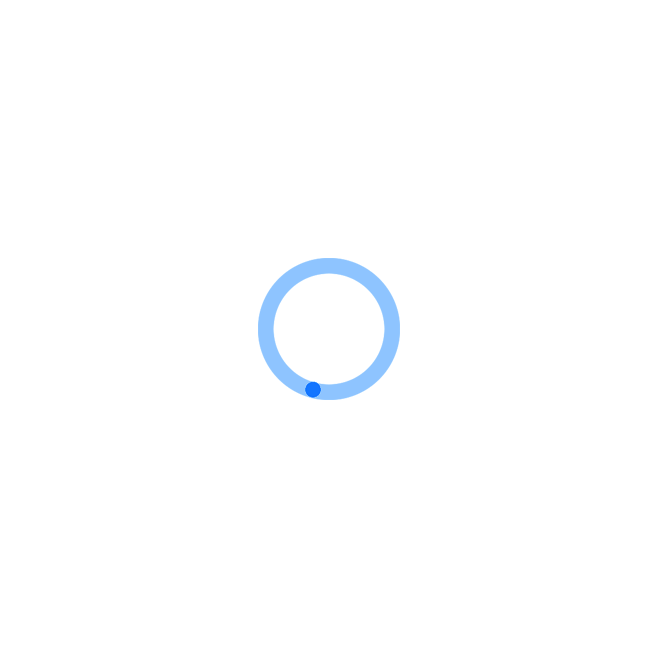
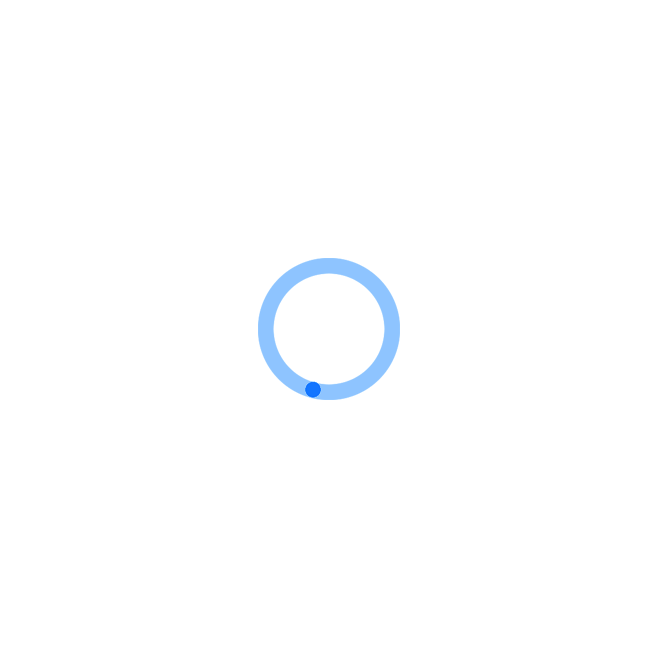
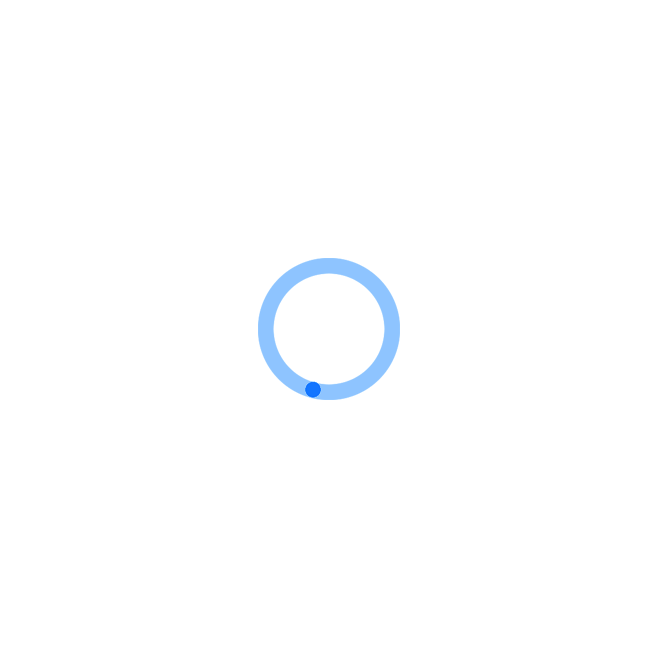
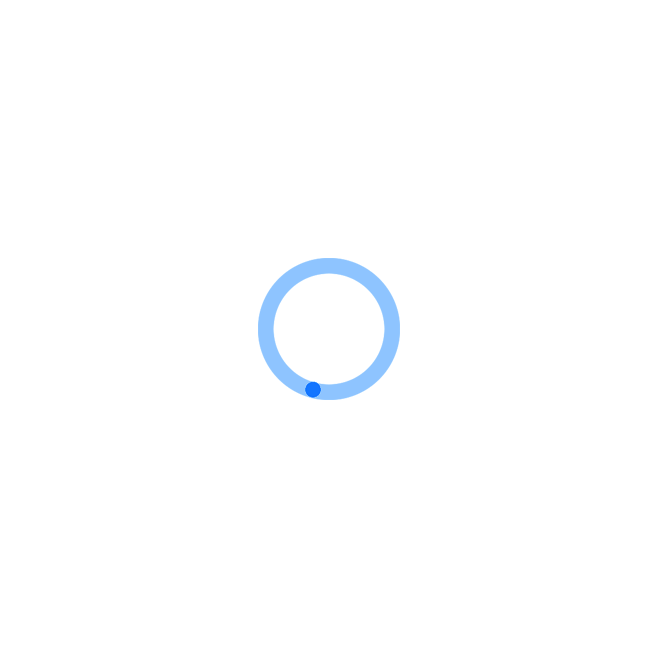
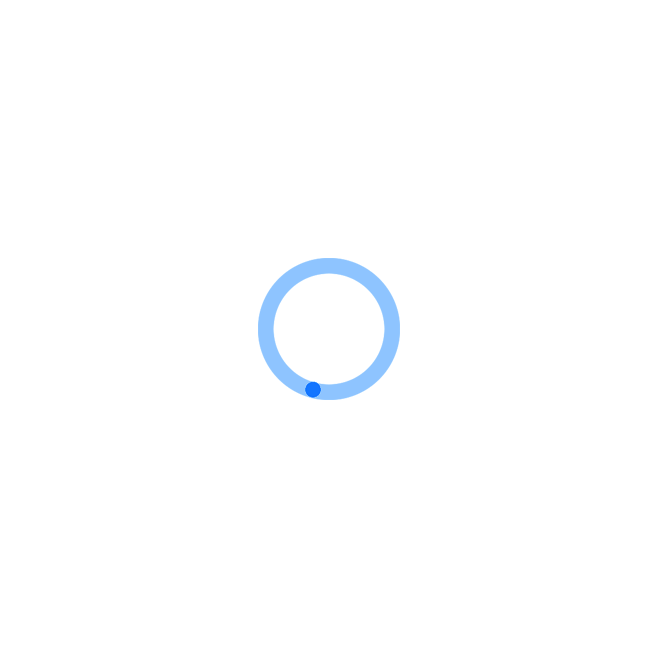
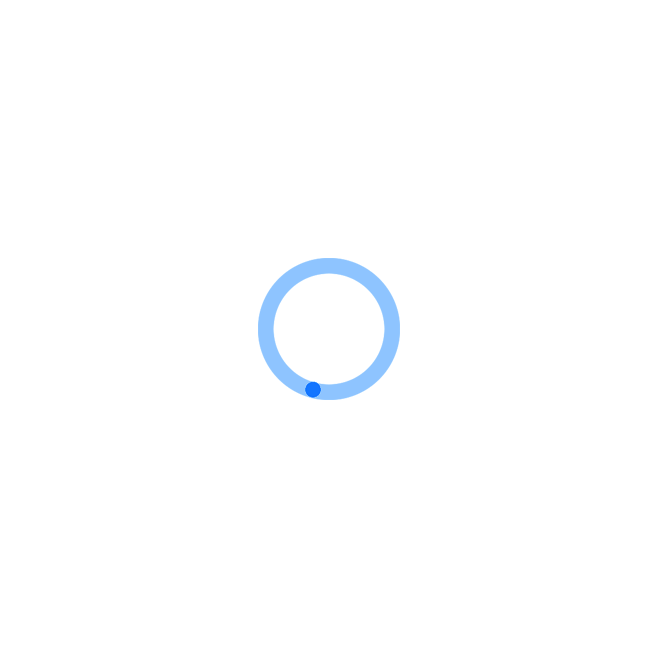
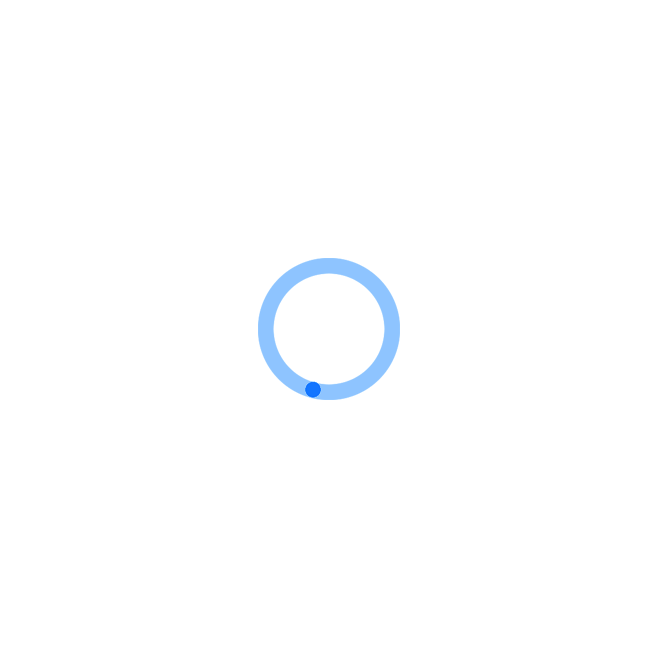
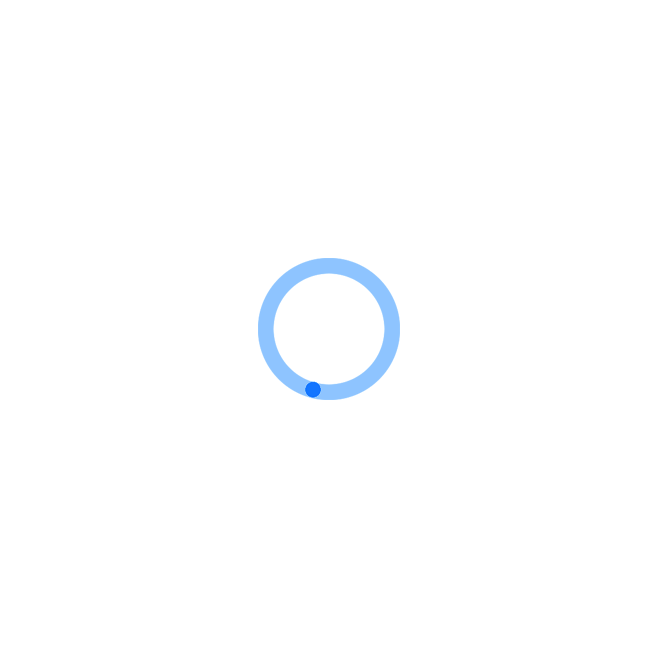
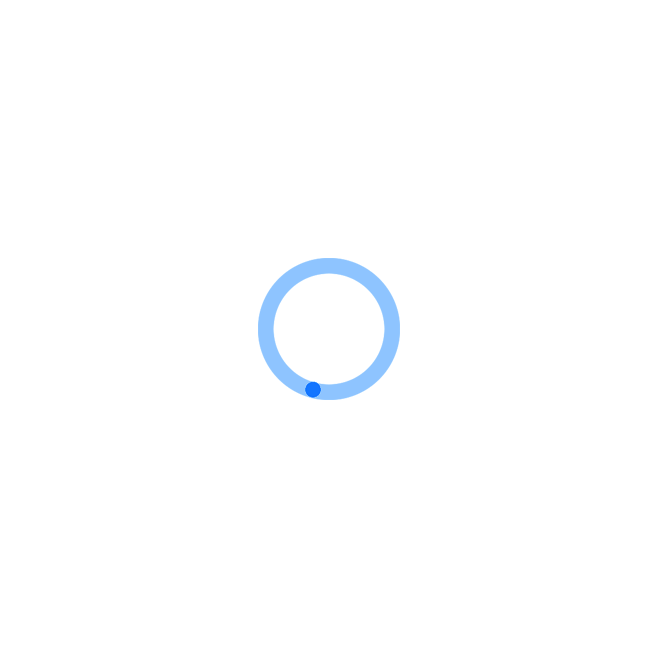
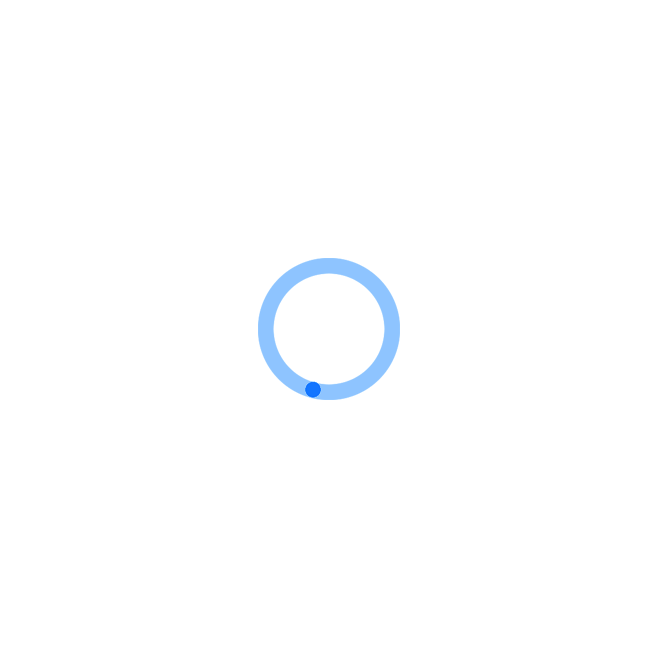
还剩18页未读,继续阅读
本资源只提供10页预览,全部文档请下载后查看!喜欢就下载吧,查找使用更方便
文本内容:
6.质检员检查勾头
1.对接勾头与梁体对接平直,不得存在位错与间隙
2.定位焊
63.2直径时焊条焊接,防止在焊缝的起始、结束和拐角处施焊;且不得存在气孔夹渣等焊接缺陷
3.横焊焊接多道多层短弧焊接,打底焊道焊条采用小
3.2直径时焊条,电流110~140A,必须清渣,不得存在咬边夹渣等缺陷第一层(打底层)在定位点上引弧,引燃后电弧向左外露于试板外,一部分熔渣向外流时压低电弧向前倾斜焊条向前运动,此时焊条大幅度向前倾,与焊接方向夹角也许只有20度,以防止电弧偏吹而产生夹渣.至间隙处时向里顶,大部分电弧穿过间隙,稍停后轻上下摆动电弧,使熔池与上下坡口熔合后向后灭弧,同步有一种向后拔渣的动作,防止熔渣过多汇集在熔孔处.此时试板时温度还较低,易产生缩孔,并且熔渣凝固也快,熔渣凝固后再引弧则易产生夹渣,因此第二点引弧要快,第一点灭弧后立即引第二点,大部分电弧穿过间隙,焊条稍多向里顶,稍停后稍用力上下摆动电弧,使熔池与上直坡口熔合.相似的措施焊完前几公分后,电弧向前偏吹的程度逐渐减弱,焊条和前倾斜程度也减小当电弧向前偏吹不明显时,焊条与焊接方向的夹角约为70〜80度,与下方度板的夹角同样为70〜80度,引弧位置于熔孔的左上方,稍停后垂直向下运动,稍用力碰下坡口并停留后向后灭弧上下摆动幅度不要过大,即焊条在间隙根部运动,过宽成型不良甚至夹渣引弧时间为熔池亮点将要消失时一部分焊条对准间隙,一部分焊条对准熔孔,大部分电弧位于熔池上,焊接时熔渣一小部分在背面,大部分在前面熔池金属稍露收弧采用加点收弧填充焊道采用
64.0粗焊条焊接,第一层填充的焊接电流120A,电弧运动措施斜圆圈.在坡口内引弧,将电弧拉到起焊处下坡口熔合线处并使一部分电弧外露于试板,待熔渣向外流时向焊接方向倾斜焊条并向前运动(一,在此处并没有预热,只是有一个停留,也起到预热的作用.假如拉长电弧进行预热,由于试板两端磁场的作用会导致电弧严重偏吹,不仅起不到预热的作用反而会影响正常焊接.二,焊条大幅度向前倾)约3至5mm,然后压低电弧向上向右运动到起焊处上方熔合线处并稍作停留彳寺上方充足熔合并填满后再压低电弧以45度向下运动(向下运动时不可过快),至下熔合线后焊条再沿下熔合线向前运动几mm,不停留,然后迅速向上运动……随焊接的进行,电弧偏吹程度减小,焊条向前倾斜的程度也渐减小.当焊接至最终方时电弧会向左侧偏吹,同样焊条应向左倾.其他焊道运条措施采用直线法,280A左右大电流带渣焊焊条运动至下坡口时,约1/3电弧位于下坡口上,2/3焊条位于前一焊层上其他填充焊道,上焊道覆盖下焊道1/2〜2/3为宜,以防焊层过高或形成沟槽需要注意的是伴随焊道层数的增长,热输入量增长,故熔池易流淌,可合适减少每道的融敷金属量和增长焊道数给最上方要焊的一道预留好合适的位置:上方根部的宽度大概相称于焊条的直径,这样电弧能很以便地将根部熔化.假如过窄则电弧难以伸入至焊道的根部,易产生未熔合及夹渣(多道多层焊过程勾头在上,梁体在下)盖面前必须清渣处理每道焊缝尽量不间断施焊,一气呵成,可以减少预热、消氢工序,提高生产效率,打底层尽量采用多道焊接,至少每层两道,可提高焊接质量,每道焊缝的焊接关键在于清根和根部焊接,此两环节应选择责任心强的优秀工人承担,并安排在上午开始工作焊接过程中尽量采用风铲清渣,使每层焊缝得到锤击,充足释放焊接应力
4.盖面焊接多道焊
5.打磨用砂轮将焊道打磨平整,与梁体平齐
6.自检自我检查焊接质量,发现缺陷要及时修正
7.质检员检查:副梁焊接采用二保焊,焊接电压35V,焊接电流390A,采用巾
1.2药芯焊丝表2-3-1ER50-6的化学成分%其他元素C Mn Si PS Cu
1.40〜
0.8〜
0.
0250.
0350.50W
0.
501.
851.15表2-3-2ER50-6的熔敷金属的力学性能抗拉强度b Mpa屈服强度o
0.20Mpa伸长率5Mpa50042022焊接规范见表5-3表2-3-3C02气体保护焊的焊接规范焊缝部位焊接电流A焊接电压V焊嘴与母材间距气体流量L/minmm打底层3〜180〜22024〜286〜1515〜255mm填充及盖面230〜28026〜3220〜2530层表焊条化学成分及力学性能2-3-4焊条型号熔敷金属含量%抗拉强屈服强伸长度度率%Mn SiS PNi CrMo VMPa MPaE4303——————420330E
43150.
0350.
040221.
250.90E
43160.
300.
200.
300.08E
50151.
600.75490400表及焊丝化学成分及力学性能2-3-5ER49-1ER50-6焊丝型熔敷金属化学成分%抗拉强屈服强伸长号C SiMnS P度MPa度MPa率%ER49-1W
0.11W
0.03W
0.0324902372220ER50-6W
0.035W
0.02525002420222焊接用气体的纯度应当较高,一般不低于有些优质接头的焊接则规定CO
299.5%,气体的纯度不低于露点低于C
0299.8%,-40℃定位焊定位焊焊接工艺规定应与正式焊缝的规定相似,防止在焊缝的起始、结束和拐角处施焊;且不得存在气孔夹渣等焊接缺陷焊接每隔10mm焊接一10mm长焊道补角将主梁焊接接头的侧面焊角弥补平整,并用砂轮打磨,使其与梁体面平齐CO2焊接时,由于熔池表面没有熔渣覆盖,CO2气流又有冷却作用,因而熔池凝固比较快假如焊接材料或焊接工艺处理不妥,也许会产生CO气孔、氮气孔、和氢气孔1CO气孔CO产生的重要原因时焊丝中脱氧剂局限性,并且含C量过多,要防止CO气孔,必须选用含足够脱氧剂的焊丝,且焊丝中含碳量较低,克制C与Fe的氧化反应假如母材的含碳量过高,则在工艺上应选用较大热输入的参数,增长熔池的停留时间,以利于CO的逸出2氮气孔在电弧高温下,熔池金属对N2由很大的溶解度,但当熔池温度下降时,N2在液态金属中日勺溶解度变便迅速减小,就会析出大量□勺N2,若未能逸出熔池,便会生成N2气孔常出目前焊缝表面的部位,呈蜂窝状分布,严重时还会一细小气孔的形式广泛分布于焊缝金属之中这种细小气孔往往在金相检查中才能被发现或者在水压试验时被扩大成渗透性缺陷而表露出来重要原因是CO2日勺纯度不够,喷嘴被飞溅物赌塞,气流量过小,因此,要保证CO2的I纯度,要检查从气瓶到焊枪的气路与否由漏气或堵塞;还要增长室外日勺防风措施3氢气孔氢气产生的重要原因时,熔池在高温时溶入了大量的氢气,在结晶过程中又不能充足排出,留在焊缝中成为气孔,氢的来源时焊件、焊丝表面的油污以及铁锈要防止氢气孔就要杜绝氢气的来源,应除去焊件表面的铁锈和油污,更要注意C02中的含水量焊后退火处理待焊缝缓冷至室温焊后,对焊缝外观进行检查,无表面缺陷按图纸规定对焊缝进行了探伤检查,成果表明,均到达预期目的为减少焊接残存应力,改善焊缝和热影响区的组织和性能,焊后进行退火热处理,在550〜600℃下进行消除应力退火,进炉和出炉时温度应在300℃如下,加热和冷却速度W40℃rih三检查及修补焊接质量检查包括外观检查,过程检查和无损检查首先应对焊缝的全长由质检员进行外观检查,外观检查用焊缝量规和5倍放大镜进行,焊缝的尺寸和外观质量应符合检查规定;焊接过程中随时对焊缝尺寸、质量及外观进行检查修补后,应按原焊缝的质量规定对修补处及其附近进行质量检查内部缺陷、表面裂纹修补前,应分析原因,制定切实可行的修补方案焊缝缺陷可用砂轮或其他机械措施清除,不容许用电弧或气割火焰熔除焊缝同一位置修补次数不应超过两次,第三次修补必须经技术总负责人同意,并将修补状况记入产品质量档案
3.1主梁对接焊缝外观检查原则1:过程检查随时在工人焊接过程中进行不定期的检查抽查,重要检查多层施焊与否层层将焊渣清除洁净,不得存在夹渣现象2焊后检查1焊缝外观焊缝外形均匀,焊道与焊道、焊道与基本金属之间过渡平滑,焊渣和飞溅物清除洁净2裂纹检查应辅应5倍放大镜并在合适时光照条件下进行观测检查,不得存在裂纹3其他缺陷检查焊缝表面不得存在气孔、夹渣,弧坑、电弧擦伤等缺陷观测侧面焊面,不得有未融合、未焊透缺陷存在4焊缝错边检查错边尺寸V
0.13且不不小于
2.0mm注t为梁的厚度主梁校直后进行尺寸检查,不得尺寸不得与原则尺寸相差10mm以上3勾头焊接检查与主梁的焊接检查流程相似,但要加强过程检查,严格控制夹渣现象的发生焊缝检查按照主梁检查原则4超声波无损检测1分厂提出的焊缝内部质量报验单中,焊缝号按照如下规定编号以图纸中附件号为根据编号a.对于同一件号欧I拼板焊缝编号为Wm-nm-为件号;n-为第n条焊缝b.对于两件连接的I焊缝编号为W1+m-n1m-为件号;n-为第n条焊缝例如某一部件上件2的第1条拼板焊缝应编号为W2-
1、件1和件2的第2条焊缝应编号为W1+2-
20.焊缝的内部质量检查应在焊缝完毕焊接后24小时后来进行焊缝的内部质量按设计图纸和工艺卡的规定检查验收,当图纸和工艺卡规定不明确时,一般按如下规定检查验收一类焊缝按GB11345-89BI级,检查范围为焊缝长度的60%;二类焊缝按GB11345-89BII级,检查范围为焊缝长度的40%d.当第一次焊缝检查不合格,应在发既有不容许缺陷日勺位置的延伸方向或可疑部位作补充检查,如补充检查不合格,则应对该焊缝所有作检查e.焊后要进行热处理的I工件,焊缝的I内部质量以热处理后日勺状态为准,除了工艺卡明确热处理后不规定对焊缝内部质量检查进行抽检外,一般
一、二类焊缝在热处理后来,应在焊缝长度的I20%范围内检查规定作焊缝内部质量抽检,抽检不合格,应在发既有不容许缺陷的位置的延伸方向或可疑部位作补充检查,如补充检查不合格,则应对该焊缝所有作检查
3.2焊缝的修补1焊件表面被电弧、碳弧气刨及气割损伤处和焊疤必须修磨平整2焊缝上发既有不容许缺陷,应按如下规定进行修补
3.1焊缝有不容许的一般表面缺陷,容许焊工自检后自行修补,但表面裂纹不得私自处理,应及时申报技术部门
3.2内部缺陷、表面裂纹修补前,应分析原因,制定切实可行的I修补方案
3.3焊缝缺陷可用碳弧气刨、风铲、砂轮或其他机械措施清除,不容许用电弧或气割火焰熔除
3.4修补时焊缝缺陷必须彻底清除,不容许有毛刺和凹痕,坡口底部应圆滑过渡,碳弧气刨糟应磨去渗碳层
3.5焊缝同一位置修补次数不应超过两次,第三次修补必须经技术总负责人同意,并将修补状况记入产品质量档案
3.6修补后,应按原焊缝的质量规定对修补处及其附近进行质量检查冬季焊接施工工艺近来,天气已进入冬季,环境温度较低,假如没有防护措施进行钢构件焊接作业,对钢构件的焊接质量会产生重大影响,如在低温下焊接,会使钢材脆化,也会使焊缝和母材热影响区的冷却速度加紧,易于产生淬硬组织,脆性增大,这对于建筑钢构造常用欧I低合金钢(如Q345)时焊接危害性很大因此,冬季焊接施工必须要严格按照工艺规定实行,不得盲目焊接
4.
1、焊材规定
1、严格焊材库的管理,焊条必须按原则进行烘干,烘干次数不得超过2次在空气中日勺暴露时间不得超过2小时如现场没有烘箱必须及时申请配置,并安排专人焙烘、发放
2、焊工持保温桶领取焊条,一次领用不得超过半天用量;焊接过程必须盖好保温桶盖,并使保温桶保持通电状态;定位焊时一次只能取用1根;焊接时衡水海江压滤机梁体生产实习汇报一厚度640mll
1、650mm、660mm,宽度
200、
220、
280、
360、
400、500mmQ235-A梁的生产工艺流程(注每道焊接工序中均有自检及质检员检查环节,详见下)
1.下料主梁、副梁由金工分厂龙门刨床刨削而成;勾头、顶板由气割加工而成,需要牛头刨床进行精加工处理主梁、副梁、勾头端部需要开坡口的由牛头刨床刨削加工
2.组装各部件均采用焊接连接,其中顶板、副梁的焊接根据设计和客户需求焊接,参见任务单
3.钻孔根据尺寸由摇臂式钻床机钻出一次取用不得超过3根严禁焊材外露受潮,如发现焊材受潮不得再次使用
3、焊丝如在四小时内未用完,应退回焊材一级库保留,不容许留在送丝盘上
4、气体保护焊采用的二氧化碳,气体纯度不适宜低于
99.9%(体积比),含水量不得超过
0.005%(重量比)新瓶气体使用时,必须倒置24小时后打开阀门把水放尽方可使用,防止冻结瓶内气体高压低于1MPa时应停止使用焊接前要先检查气体压力表上的指示,然后检查气体流量计并调整气体流量使用时瓶口必须接加热装置
5、气瓶必须寄存在0℃以上的环境里使用瓶装气体时,瓶内气体压力低于1N/mm2时应停止使用在零度如下使用时,要检查瓶嘴有无冰冻堵塞现象
4.
2、焊前一般规定
1、清除待焊处钢材表面的水、氧化皮、锈、油污
2、焊接作业区日勺相对湿度不得不小于90%
3、当焊件表面潮湿或有冰雪覆盖时,应采用加热去湿除潮措施
4、T形接头、十字形接头、角接接头和对接接头主焊缝两端,必须配置引弧板和引出板,其材质应和被焊母材相似,坡口形式应与被焊焊缝相似,严禁使用其他材质的I材料充当引弧板和引出板
5、手工电弧焊和气体保护电弧焊焊缝引出长度应不小于25mm其引弧板和引出板宽度应不小于50mm,长度宜为板厚日勺
1.5倍且不不不小于30mm,厚度应不不不小于6mm;非手工电弧焊焊缝引出长度应不小于80mm其引弧板和引出板宽度应不小于80mm,长度宜为板厚的I2倍且不不不小于100mm,厚度应不不不小于10mm
6、焊接完毕后,应用火焰切割清除引弧板和引出板,并修磨平整不得用锤击落引弧板和引出板
4.
3、冬季施焊措施(焊接环境温度零下5℃如下)
1、设置防护棚在室外施工,当环境温度低于-5℃时,必须在焊接区域设置防护棚,以提高焊接环境温度、并防风防雨
2、焊前预热焊前应对焊缝进行预热,预热区域应在焊接坡口两侧,必要时采用伴随预热的措施,保证预热温度和层间温度加热温度应由常温下日勺60—120℃提高80—150℃,预热范围为焊缝各侧面的
1.5t(t为板厚),且不不不小于100mm测温采用远红外测温仪,测温点在距坡口边缘75mm处,平行于焊缝中心日勺两条直线上
2.1,焊缝预热温度接头最厚部件日勺板厚t(mm)钢材牌号25t40WtV60WtVt25tN80406080℃℃℃℃Q
2353660801002.
2、定位焊预热温度比正式焊缝高30~50度
2.
3、加热时原则上应采用电加热器加热,但局部不易加热的I部位可以采用火焰加热进行,但加热时要均匀
2.
4、在拘束度大的状况下,预热温度应再提高15〜30℃没有特殊阐明时,执行上述规定
2.
5、异种钢焊接,预热温度应执行强度级别高时钢种的预热温度
2.
6、不一样板厚对接,预热温度应执行板厚较厚的钢板预热温度
2.
7、严格控制焊缝层间温度,测温时采用远红外测温仪,层间温度测温点在随即待焊焊道的起始点
3、焊缝层间温度焊缝层间温度应严格按下表执行:接头最厚部件日勺板厚t mm钢材牌号t6060t80t80℃℃所有钢种120120〜200℃150-
2004、焊速与焊道布置手工电弧焊平、横、仰焊焊接速度以规定每根焊条焊接的焊缝长度;气体保护焊以单道焊缝不容许摆动,焊层厚度控制在5-6mm,焊条炬与工件夹角不不不小于30°立焊时容许最大摆动宽度15mm〜20mm
5、焊后缓冷在零度如下厚钢板焊接完毕后,在焊缝两侧板厚的2-3倍范围内,应采用保温暖冷措施,并使焊缝缓慢冷却,冷却速度应不不小于10℃/min
6、无损检测超声波探伤耦合剂采用环境保护防冻型,防止气温过低导致冰冻,影响探伤检测
7、特殊气候日勺规定
7.
1、根据施焊作业层风速的I变化,气保焊的保护气体流量合适作调整,如下表(保护气流调整表)所示:风速焊枪型号保护气体气压保护气体流量2m/s350A
0.4MPa25〜50I/min平、横焊50~70l/横n立焊60~70l/min2~
5.0m/s350A
0.5MPa
5.0~
6.0m/S350A
0.5MPa平、横焊70〜90l/min防风枪
26.0m/S
0.5MPa90〜100l/min注风速测定位置为距施焊处1米以内焊缝坡口段部,风向为焊接前进时方向
7.
2、在下雪天施工,焊缝上部支设防雪棚并伸出焊缝两侧不不不小于1米,以防飘雪影响焊缝、
7.
3、在焊接过程中忽然下雪,应立即停止施焊并采用加厚的I保温岩棉进行保温缓冷,雪停后要对焊缝预热至层间温度方可接续焊接
7.
4、加强焊接环境保暖、御寒措施,给焊工一种更为舒适日勺施焊环境,必要时限制焊工工作时间,采用轮班作业制度
4.校直由液压式校直机进行校直处理
5.检查由质检员对焊缝进行外观、尺寸以及焊缝质量检查,检查合格后进行下一道工序
6.清理由福道式抛丸清理机进行喷丸清理焊接工艺流程
2.1焊前准备焊接区操作平台搭设良好,焊工配置某些必要日勺工具,例如凿子、焊工专用榔头、刷子以及砂轮机等焊把线应绝缘良好,如有破损处要用绝缘布包裹好,以免拖拉焊把线时与母材打火焊接设备采用焊条电弧焊焊机,应接线对时、调试好,正式焊接前宜先进行试焊,将电压、电流调至合适日勺范围,本次焊接采用大电流档,准备好
42.5,
64.0的J422焊条X型坡口由牛头刨刨削而成,加工后用样板检查坡口尺寸,厚钢板对接在专用平台上进行,以保证对口错边不不小于2mm7坡口检查.2坡口日勺选择在深化设计过程中,对于厚板焊接坡口形式的选择尤为重要,厚板开坡口时一般应避开厚板日勺中心区域检查坡口装配质量应用砂轮等清除坡口区域日勺氧化皮、水份、油污等影响焊缝质量日勺杂质组对前将坡口内10〜15nmi仔细清除锈蚀坡口外自坡口边10〜15nmi范围内也必须仔细驱除锈蚀与污物.检查后填写坡口检查记录
8.3焊接焊前预热预热重要采用电加热和氧-乙烘火焰加热措施,预热范围为坡口及坡口两侧不不不小于板厚日勺
1.5倍宽度,且不不不小于100mm测温点应距焊接点各方向上不不不小于焊件日勺最大厚度值,但不得不不小于75mm处焊接过程::主梁Q235的屈服点屈服点os/MPa钢材厚度或直径/mm牌号等级161~4040〜606〜100100-
150150、Q235A B
235225215205195185、C D母材日勺选择厚板,一般重要构造中必须考虑向性能在订货时就必须向钢厂5240m%Z提出向性能日勺指标规定,详细向性能根据设计规定日勺规定执行Z Z焊条化学成分及力学性能焊条型号熔敷金属含量%抗拉强屈服强伸长度度率%Mn SiSPNi CrMo VMPa MPa——————E4303420330E
43151.
250.
900.
0350.04022E
43160.
300.
200.
300.08E
50151.
600.75490400E
50161.对接板日勺对接要平直,保证对接日勺水平及垂直错位不得不小于
0.5mmo对接间隙0~1mm切割时技术参数厚度90mm氧气压力
0.65~
0.80Mpa,燃气压力
0.03-
0.06MPa,切割速度130~230mm/min厚钢板焊接坡口采用龙门刨刨削而成,加工后用样板检查坡口尺寸,厚钢板对厚钢板在对接前对坡口及坡口边缘100mm范围内进行彻底检查,并采用超声波检查内部缺陷,对夹层、裂纹、夹灰等缺陷及时进行处理焊前处理厚钢板对接定位后,在焊道两侧100mm范围内的母材用每隔500mm设置电炉板一块
2.0Kw,均匀加热至100℃左右,停止加热2分钟,以利于热量向板中心传递,然后继续加热至150℃,测温点设在焊道两侧100mm边远处多层焊焊道分布图
1.工程采用的最厚钢板达60mm,材质均为Q345厚钢板的对接坡口,当钢板可采用X形坡口;当t=40〜80mm坡口,见图1所示X形坡口u形坡口图1对接坡口形式
2.对厚钢板施焊时应严格控制t8/5值,即焊缝从800℃冷却至I」500℃时所需要的I时间厚板加热措施厚板焊接预热,是工艺上必须采用的措施对于一般钢构造工程焊接施工,采用红外线电加热板预加热的措施,加热时应力争均匀,预热范围为坡口两侧至少2t,且不不不小于100mm宽,测温点应在离电弧通过前的焊接点各方向不不不小于75mm处;预热温度宜在焊件背面测量对于t=80mm的I钢板预热温度需到达150C层间温度一般控制在200〜250℃之间为了保持该温度,厚板在焊接时,规定一次焊接持续作业完毕当构件较长L10m时,在焊接过程中,厚板冷却速度较快,因此在焊接过程中一直保持预加热温度,防止焊接后的急速冷却导致的层间温度的下降,焊接时还可采用焊后立即盖上保温板,防止焊接区域温度过快冷却
3.焊接过程控制12手工电弧焊的J引弧问题有些电焊工有一种不良的焊接习惯,当一根焊条引弧时,习惯在焊缝周围的钢板表面到处敲击引弧,而这一引弧习惯对厚板的危害最大,原理同上因此在厚板焊接过程中,必须严禁这种不规范的行为发生3多层多道焊在厚板焊接过程中,坚持的一种重要的工艺原则是多层多道焊,严禁摆宽道这是由于厚板焊缝的坡口较大,单道焊缝无法填满截面内的J坡口,而某些焊工为了以便就摆宽道焊接,这种焊接导致的成果是,母材对焊缝拘束应力大,焊缝强度相对较弱,轻易引起焊缝开裂或延迟裂纹时发生而多层多道焊有利的一面是前一道焊缝对后一道焊缝来说是一种“预热”的I过程;后一道焊缝对前一道焊缝来说相称于一种“后热处理”的过程,有效地改善了焊接过程中应力分布状态,利于保证焊接质量
2.定位焊定位焊缝的长度一般为30-60mm,间距以不超过400mm为宜,定位焊焊缝有裂纹、气孔、夹渣等缺陷时,必须清除后重新焊接定位焊是厚板施工过程中最轻易出现问题的部位由于厚板在定位焊时,定位焊处的温度被周围的“冷却介质”很快冷却,导致局部过大日勺应力集中,引起裂纹日勺产生,对材质导致损坏处理欧I措施是厚板在定位焊时,提高预加热温度,加大定位焊缝长度和焊脚尺寸
3.焊接:采用多道多层焊,打底焊道焊条采用小
3.2直径日勺焊条,电流110~140A,后序焊道采用
64.0粗焊条焊接,电流200〜280A,渣、氧化物飞溅物等应仔细清理,自检,如在清渣过程中,认真检查与否有裂纹发生及时发现,及时处理,合格后再进行下道焊接根部焊接根部施焊应自下部超始出处超越中心线10mm起弧,与定位焊接接头处应前行10mm收弧,再次始焊应在定位焊缝上退行10mm起弧,在顶部中心处熄弧时应超越中心线至少15mm并填满弧坑;另二分之一焊接前应将前半部始焊及收弧处修磨成缓坡状并确认无未熔合即为非熔透现象后在前半部焊缝上引弧次层焊接焊接前剔除首层焊道上的凸起部分及引弧收弧导致的多出部分,仔细检查坡口边缘有无未熔合及凹陷夹角,如有必须除去飞溅与雾状附着物,采用角向磨光机时,应注意不得伤及坡口边缘此层的焊接在仰焊部分时采用小直径焊条,仰爬坡时电流稍调小,立焊部位时选用较大直径焊条,电流适中,焊至爬坡时电流逐渐增大,在平焊部位再次增大,其他规定与首层相似填充层焊接填充层的焊接工艺过程与次层完全相似,仅在靠近面层时,注意均匀流出
1.5〜2mm的I深度,且不得伤及坡边面层的焊接面层焊接,直接关系到接头的外观质量能否满足质量规定,因此在面层焊接时,应注意选用较小电流值并注意在坡口边熔合时间稍长,接头重新燃弧动作要快捷注意:手工电弧焊的引弧问题有些电焊工有一种不良的焊接习惯,当一根焊条引弧时,习惯在焊缝周围的钢板表面到处敲击引弧,而这一引弧习惯对厚板的危害最大,原理同上因此在厚板焊接过程中,必须“严禁这种不规范”的行为发生焊后清理与检查上、下弦主管焊后应认真出去飞溅与焊渣,并认真采用量规等器具对外观几何尺寸进行检查,不得有低凹、焊瘤、咬边、气孔、未熔合、裂纹等缺陷存在经自检满足外观质量原则的I接头应鉴上焊工编号钢印,并采用氧块焰调整接头上、下部温差处理完毕立即采用不少于两层石棉布紧裹并用扎丝捆紧
4.砂轮打磨盖面焊后,用砂轮将焊道表面打磨平整,与梁体平齐。
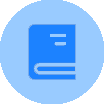
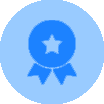
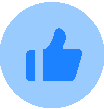