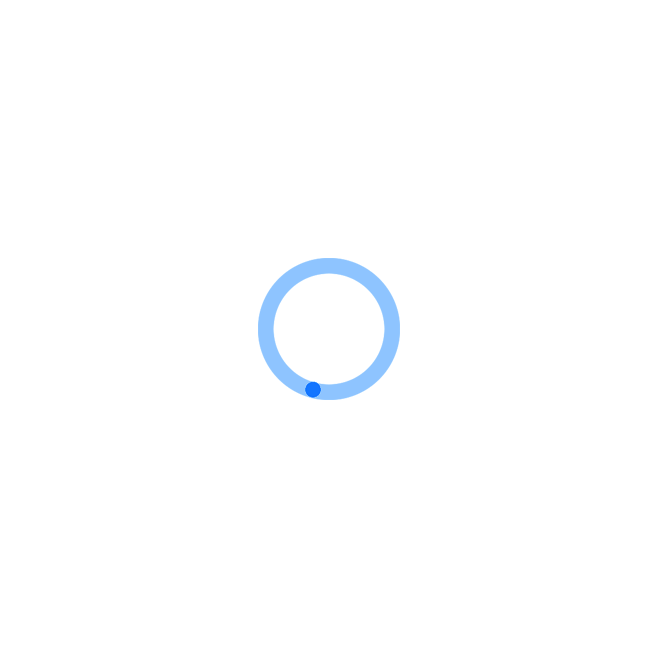
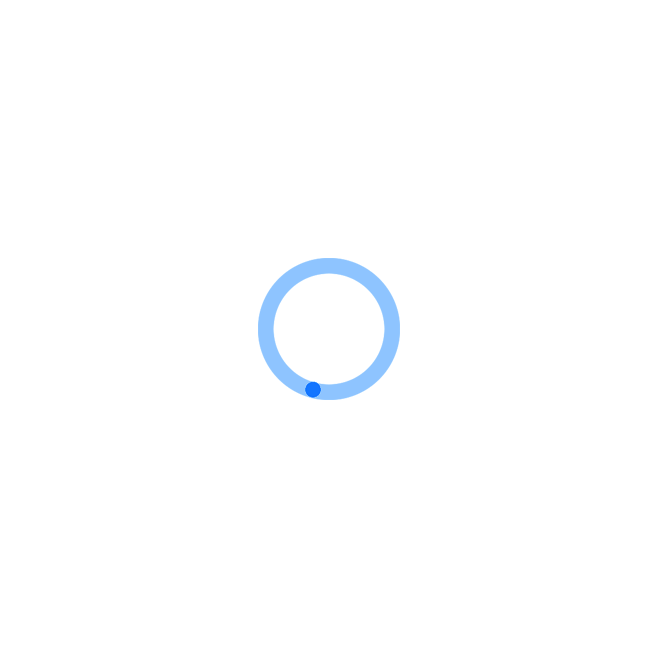
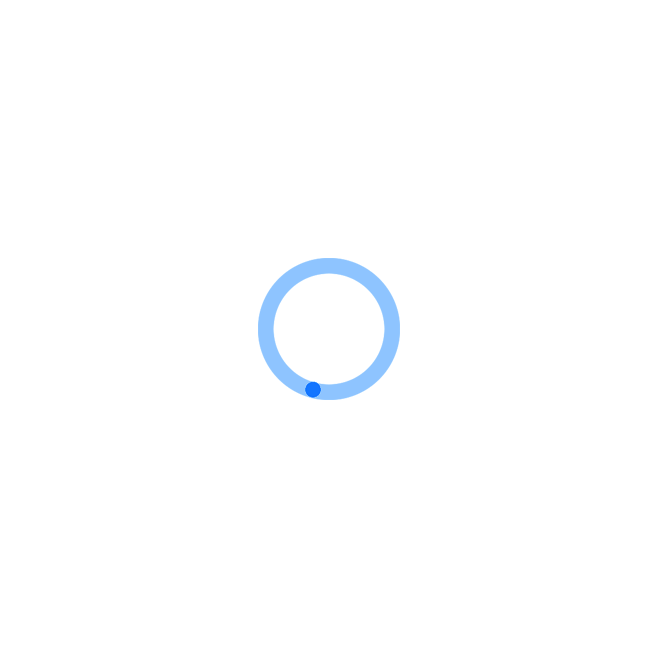
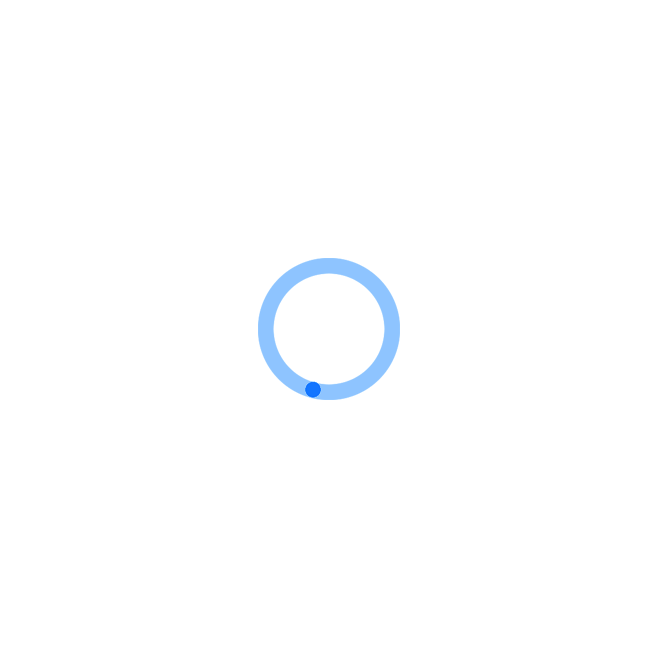
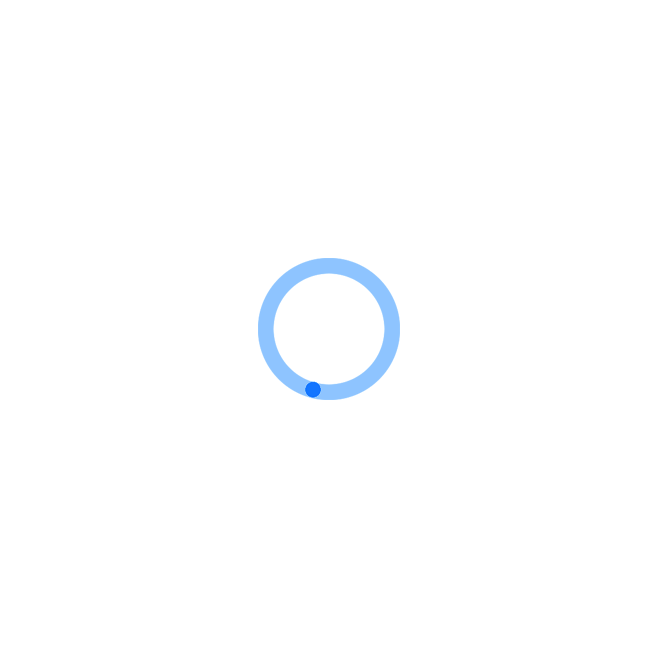
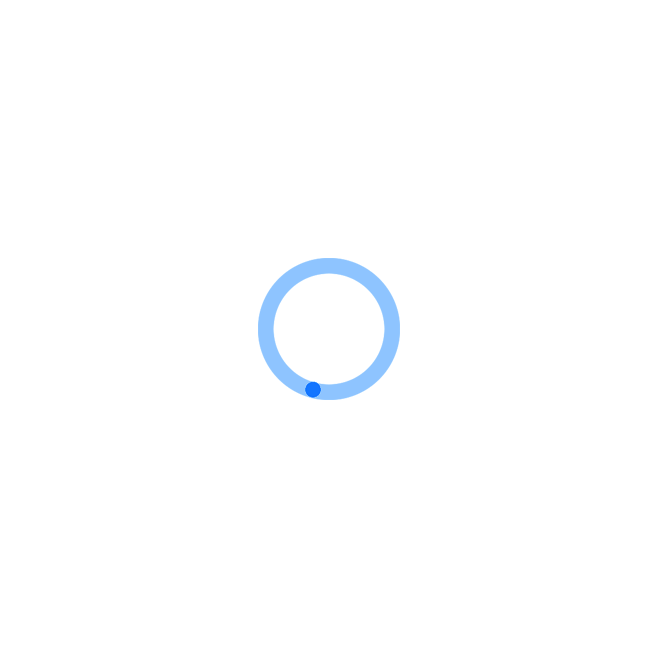
还剩4页未读,继续阅读
文本内容:
灌注桩质量问题缺陷及处理措施根据我本公司在其他类似工程中所积累的经验,对本旋挖桩基工程可能出现的问题作如下分析和预防处理
1、钢筋笼主筋集束1原因分析在起拔护筒过程中,由于钢筋笼净外径与护筒内径间距较小,当一位置处钢筋笼紧贴护筒内壁,护筒按同一方向快速旋转时,钢筋笼随护筒一起转动,使得钢筋笼发生变形2预防处理措施a严把钢筋笼制作精度及运输起吊时的变形保护,吊装时采用工具式加强杆,一次整体吊装安放b钻机在开始起拔护筒时慢速静拔,然后应减小护筒驱动器转动角度,减慢转动速度,顺时针、逆时针方向相结合即顺时针45度,逆时针45度相结合拔动护筒c在钢筋笼第一加劲箍位置内侧增设一道加劲箍
2、桩身夹泥1原因分析a在饱和淤泥质土中施工,起拔管速度过快,碎骨料粒径过大,坍落度过小,佐还未流出管外,旁边的淤泥即涌入桩身b成桩后空孔回填土时间过早,且地面与碎面的距离较大,上部回填的砖石及泥团在很大的冲击力作用下砸入桩身里;)2预防处理措施:a在护筒松动以后,应采用慢速静拔(不转动);)b护筒起拔后,用钢筋网片封住孔口,待5小时后,再进行空孔回填;)c浇注已时,导管要经常拆卸,使得碎的上返力大一些;)d护筒拔出后,桩头振捣
3、护筒起拔困难
(1)原因分析a)配合比砂率不当,碎石级配不连续当遇桩基较深,地下水丰富时,佐浇下去后遇水发生离析,部分失去流动性,并紧紧裹住护筒,使得起拔护筒时碎与钢筋笼随同护筒一起上升,所以起拔困难)b由于护筒内壁磨擦力过大,土颗粒细、粘性大,致使筒外壁沾的泥皮过厚,导致护筒外壁摩擦力加大()2预防处理措施)a调整佐配合比,使碎石级配连续,混凝土有较好的和易性;并且利用大料斗进行浇注,并且加隔水塞,可防止硅离析b)下护筒时与起拔护筒时及时清理护筒外壁,如每班钻孔备小型增压水枪冲洗等,这些措施能减少筒侧壁的摩擦力)c控制护筒一次起拔高度,以免使护筒根部露出混凝土面,造成质量缺陷
4、拔护筒时钢筋笼随护筒帚出
(1)原因分析)a配合比不当,碎石级配不连续由于此处桩基较深,地下水丰富,当仁浇下去后遇水发生离析,部分失去流动性,并紧紧裹住护筒起拔护筒时佐与钢筋笼随同护筒一起上升,上升一段距离,混凝土散落下沉,而钢筋笼却停留在某一位置b)混凝土品质较差,浇筑一段时间后混凝土假凝
(2)预防处理措施)a及时浇混凝土,对不合格或坍落度损失较大的混凝土采用二次搅拌或弃用措施)b对于到现场的硅每车作一组坍落度试验,不满足技术要求(18~22cm),要进行调整已配合比,防止硅离析;)c首灌完成后,要放慢放料速度,根据碎面深度和导管总长正确拆卸导管,拆管前应检测硅面深度
5、堵管()1原因分析)a隔水塞不符合要求,直径过大或过小;b)隔水塞遇物卡住,或导管连接不直,变形而使隔水塞卡住;)c碎坍落度过小或磴搅拌不匀,严重离析;d)导管漏水,碎被水浸稀释,粗骨料和水泥砂浆分离;)e灌注时间过长,表层已已过初凝时间,开始硬化;或硅在管内停留时间过长而失去流动性()2预防处理措施若为隔水塞卡在管内,在深度不大时,可用长杆冲捣;或在允许的范围内,反复提升导管振冲;如不能清除则应提起和拆开导管,取出不合格隔水塞检查导管连接部位和变形情况,重新组装导管入孔,安放合格的隔水塞不合格已造成的堵管,可通过反复提升漏斗导管来消除,或在导管顶部安装激振装置,不断振动导管来解除
6、导管漏水1原因分析a连接部位垫圈挤出,损坏;b初灌量不足,未达到最小埋管高度,泥浆水从导管底口侵入;c连续灌注时,未将管内空气排出,致使在管内产生高压气囊,将密封垫圈挤破;d导管提升过多,埋深太小,孔内浆液侵入管内2预防处理措施处理的措施根据导管漏水程度大小而不同漏水不大,多为从连接处和底口渗入,可集中数量较多,坍落度相对较小的硅拌合物一次灌入,依靠磴下落的压力将水泥砂浆挤入渗漏部位,封住底口的渗入漏水严重时,应提起导管检查连接处的密封圈垫,重新均匀上紧,准备足量的碎拌和物,重新开始灌注若孔内已灌注少量磅,应予清除干净后,方可灌注;灌入碎较多使清除困难时,应暂停灌注,下入比原孔径小一级的钻头钻进至一定深度起钻,用高压水将碎面冲洗干净,并将沉渣吸出,将导管下至中间小孔内恢复灌注
7、断桩1原因分析)a因测深不准或操作不当造成提升导管过高,以致底部脱离在层面;b)出现堵管而未能及时排除;)c灌注中断过久,表层已失去流动性,而继续灌注的碎顶破表层而上升,将有浮浆泥渣的表层覆盖包裹,形成断桩;)d灌入的硅质量低劣;()2预防处理措施对断桩应以预防为主灌注前要对各作业环节认真检查,指定有效的预防措施灌注中,严格遵守操作规程,保证灌注作业连续紧凑,重视佐面的准确探测,绘制硅灌注曲线,正确指导导管的提升,提升应匀速平稳,控制灌注时间在适当的范围内如灌入碎量不够,应先将已灌佐清除再下入导管重新灌注若灌入量较多,可按前述打小孔的方法处理断桩位置较深,断桩承受荷载不大时,可采取钻孔至断桩部位先清洗再钻孔压浆补救,断桩承受荷载较大时,可采取插入钢筋束灌浆制作锚固桩的措施断桩位置较浅或处于地下水位以上可将清除断桩以上碎,支模重新浇筑成桩
8、磴严重离析
(1)原因分析)a导管漏水引起水浸;b)硅搅拌不均;)c骨料级配不当;d)使用的水泥品种不当或失效水灰比过大2预防处理措施应查明原因,重新搅拌磅,如仍不符合要求应予清除加强对进场骨料质量的检查,经常检查佐的配比,以及时发现和纠正水灰比的变化
9、钢筋笼错位1原因分析a钢筋笼固定不当或下导管时挂住钢筋笼,导致笼下落;b钢筋笼固定不当时,初灌碎产生向上的冲力或提升导管时将钢筋笼挂起c钢筋笼在孔口安放焊接时未上下对正,保护块数量不足或桩孔超径严重,使钢筋笼偏斜向一边2预防处理措施:严格细致地控制钢筋笼吊放,并将其牢固地绑扎或点焊于孔口钢筋笼入孔后,检查其是否处在桩孔中心下放导管时,应使导管顺桩孔中心位置而下,避免挂住钢筋笼。
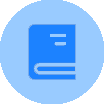
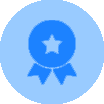
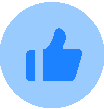