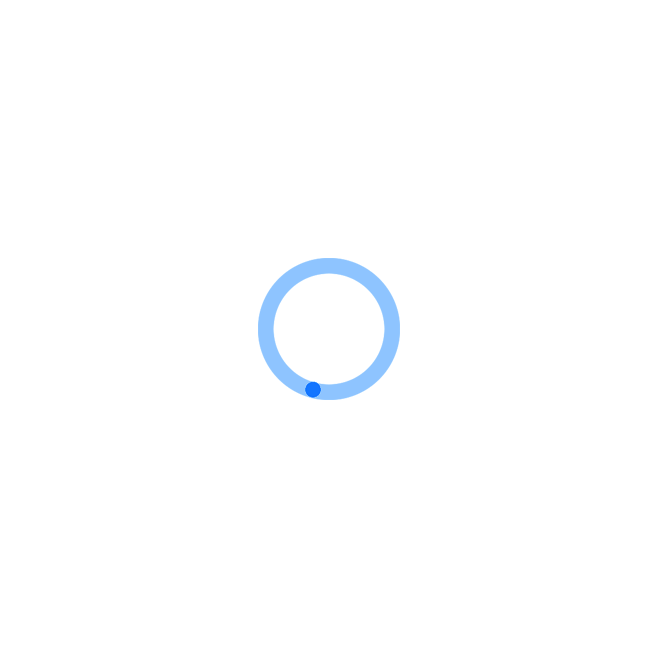
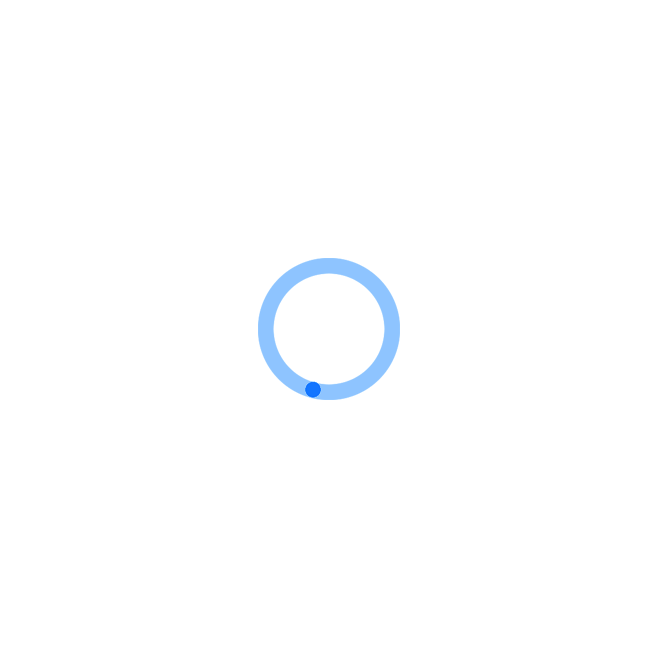
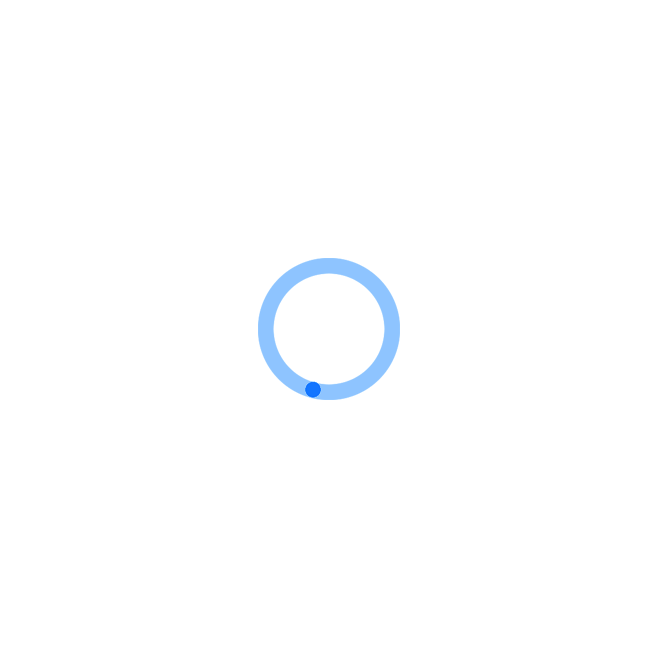
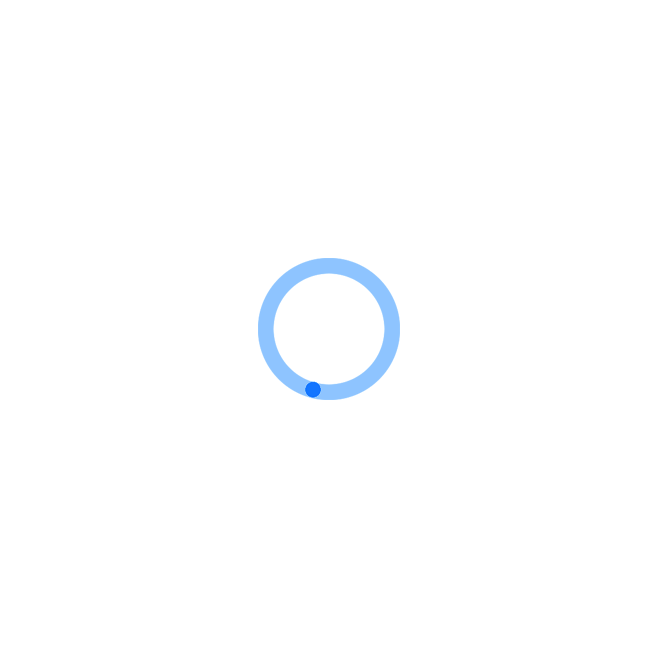
还剩2页未读,继续阅读
文本内容:
计方案的改进性和推存性意见的文件,经上级批准后,作为产品技术设计的依据.其目的在于正确地确定产品的最佳总体设计方案、主要技术性能参数、工作原理、系统和主体结构,并由设计员负责编写(其中标准化规则要求会同标准化人员共同拟定)现对其编写内容和程序作如下规定项目任务书
4.
1.1设计依据(根据具体情况可以包括一个或数个内容)a.国内外技术情报在市场的性能和使用性方面赶超国内外先进水平,或在产品品种方面填补国内”空白二b.市场经济情报在产品功能、特点、形式(新颖性)等方面满足用户要求,适应市场需要,具有竞争能力
4.
1.2产品用途及使用范围.对计划任务书提出有关方面的改进意见.
4.
1.4基本参数和主要性能指标.
4.
1.5总体布局及主要构件结构叙述.
4.
1.6产品工作原理及系统需简略勾画出产品原理图、系统图,并加以说明
4.
1.7国内外同类产品的水平分析比较
4.
1.8标准化要求a应符合产品系列标准和其他现行技术标准情况,列出应贯彻标准的目的和范围,提出贯彻标准的技术组织措施b新产品预期达到的标准化系数列出推荐采用的标准件、通用件清单,提出一定范围的通用件、标准件系数指标c对材料和元器件的标准化要求列出推荐选用的标准化系数和外购件系数指标d与国内外同类产品标准化水平对比,提出新产品标准化要求,并预测标准化的经济效果
4.
1.9关键技术解决办法及特殊材料资源分析
4.
1.10对新产品设计方案进行比较,运用价值工程,着重研究确定产品的合理性能(包括消除剩余功能),并通过不同结构原理和系统的比较分析,从中选出最佳方案.
4.
1.11根据有关方面对新产品设计方案进行的评议情况(A评价),共同商定设计或改进的方案是否能满足用户的要求和社会发展的需要,
4.
1.12叙述产品既满足用户需要,又适应本企业发展要求的情况.
4.
1.13新产品设计实施、试调周期和经费估算
4.2技术设计技术设计的目的,是在已批准的项目任务书的基础上,完成产品的主要计算和主要零件设计.
1.
1.11完成设计过程中必需的实验研究(原理结构、材料元件工艺的功能和模具实验),并写出实验研究大纲和实验研究报告
1.
1.2做出产品设计核算书(如对运动、刚度、强度、振动、热变形、电路、能量转换、能源效率等方面的核算)
1.
1.3画出产品总体尺寸图、产品主要零部件图,并校准
1.
1.24运用价值工程原理,编制技术、经济分析报告
4.
2.5绘制系统工作原理图,并作简要说明.
4.
2.6提出特殊原件、外购件,材料清单
4.
2.
72.7对项目任务书提出的某些内容进行审查和修正.
4.
2.8对产品进行可靠性、可维修性分析
5.新产品试制的管理新产品试制是在产品按科学程序完成“三段设计”的基础上进行的,是正式投入批量生产的前期工作.试制一般分为样品试制和小批试制两个阶段.
5.1样品试制是根据设计图纸、工艺文件和少数必要的工装,由试制车间试制出一件或数十件样品,然后按要求进行实验,借以考验产品结构、性能和设计图的工艺性,考核图样和设计文件的质量此阶段完全在研究所内进行
5.2小批试制在样品试制的基础上进行小批试产,其主要目的是考核产品的工艺性,检验全部工艺文件和工艺设备,并进一步校正和审验设计图纸.此阶段以研究所为主,由工艺科负责工艺文件的编制和工装设计图纸的完成,部分试制工作扩散到生产车间进行.
5.3编制技术文件在样品试制和小批试制结束后,应分别对考核情况进行总结,并编制下列文件
6.
3.1进行新产品概略工艺设计.根据新产品任务书,安排利用厂房、设备、测试条件等设想简略的工艺路线
7.
3.2进行工艺分析.根据产品方案设计和技术设计,作出材料改制、元件改装、复杂自制件加工等项的工艺分析
8.
3.3产品工作图的工艺性审查.编制试制用工艺卡片.
5.
3.5设计产品试验的工装.
5.
3.6计算试制用材料消耗和加工工时.
5.
3.7编写试制记录.
6.
3.8编写试制总结.着重总结图样和设计文件验证情况,以及在装配和调试中所反映的有关产品结构、工艺及产品性能方面的问题及其解决过程,并附上各种反映技术内容的原始记录样品试制总结由设计部门负责编制,供样品鉴定用;小批试制总结由工艺部门编写,供批试鉴定用
7.
3.9编写定型实验报告.定型实验报告是产品经全面性能实验后所编的文件,内容包括定型实验所进行的实验项目和方法、技术条件、试验程序、实验步骤、参照的有关规定等定型实验报告由检验科编制
8.
3.10编写试用(运行)报告试用(运行)报告是产品在实际工作条件下进行试用试验后所编制的文件试用(运行)试验项目和方法由研发部门规定试验通常委托用户进行,其试验程序、步骤和记录表格由研究所设计室负责编制
9.
3.11编制特种材料及外购、外协件定点定型报告,由研究所负责
10.产品鉴定的管理在完成样品试制和小批试制的全部工作后,按项目管理要求应申请鉴定鉴定分为样品试制后的样品鉴定和小批试制后的小批试制鉴定,不准超越阶段进行属于已投入正式生产的系列开发产品,经过批准,样品试制和小批试制鉴定可以合并进行
10.1定工作需准备的文件
10.
1.1定应具备的图样及设计文件供鉴定委员会用的成套资料
10.
1.2常生产应具备的图样及设计文件供产品定型后,正常投产时,制造、验收和管理用成套资料(产品图应备有二十套,发设计、工艺、全资办、检验科、生产科、工具室、装配和零件加工车间、总工程师办,并存档)
10.
1.3产品出厂应具备的图样及设计文件随产品提交给用户的必备文件
10.2织技术鉴定,履行技术鉴定书签字手续技术鉴定结论的内容是
6.
2.1样品鉴定结论的内容审查样品试制结果、设计结构和图样的合理性、工艺性,以及特种材料解决的可能性等,确定能否投入小批试制明确样品应改进的事项,搞好试制评价(B评价)小批试制鉴定结论的内容审查产品的可靠性,审查生产工艺、工装与产品测试设备,各种技术资料的完备性与可靠性,以及资源供应、外购外协、定点定型情况等,确定产品能否投入批量生产明确批量制造应改进的事项,搞好产品生产工程评价(C评价)
6.
2.3各阶段应具备的技术文件及审批程序按照产品图样、设计文件、工艺文件的完整性原则和有关的审批程序办理
7.新产品移交投产的管理
7.1新产品移交投产应具备的文件
7.
1.1新产品要力求结构可靠、技术先进,具有良好的工艺性
7.
1.2产品的主要参数、形式、尺寸、基本结构应采用国家标准或国际同类产品的先进标准;在充分满足使用需要的基础上,做到标准化、系列化和通用化
8.
1.3每一项新产品都必须经过样品试制和小批试制后方可成批生产,样品试制和小批试制的产品必须经过严格的检验,具有完整的试制和检验报告,部分新产品还必须具有运行报告样品试制、小批试制均由总工程师召集有关单位进行鉴定,并决定投产与否个下一步的工作安排在同一系列中,个别工艺上变化很小的新产品,经工艺部门同意,可以不进行小批试制,在样品试制后,直接办理成批投产的手续
7.
1.4新产品移交生产线由总工程师办组织,总工程师主持召开由设计、试制、计划、生产、技术、工艺、全资办、检查、标准化、技术档案、生产车间等各有关部门参加的鉴定会,多方面听取意见,对新产品从技术上、经济上作出评价,确认设计合理,工艺规程、工艺装备没有问题后,提出是否可以正式移交生产线及移交时间的意见
7.
1.5批准移交生产线的新产品,必须有产品技术标准、工艺规程、产品装配图、零件图、工装图以及其他有关的技术资料
7.
1.6移交生产线的新产品必须填写“新产品移交生产线鉴定验收表
7.2技术资料验收
7.
3.1图纸幅面和制图要符合有关的国家标准和企业标准
7.
2.2成套图册编号有序,蓝图与实物相符,工装图、产品图等编号应与已有的编号有连贯性
7.
2.3产品图应按会签审批程序签字总装图必须经总工程师审查批准工艺工装图纸资料应由工艺科编制和设计,全部底图应移交技术档案室签收归档
7.
2.4验收前一个月应将图纸、资料送验收部门审阅
7.
2.5技术资料的验收、汇总、归口管理由研发部负责XX有限公司。
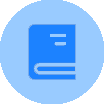
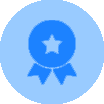
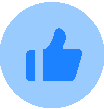