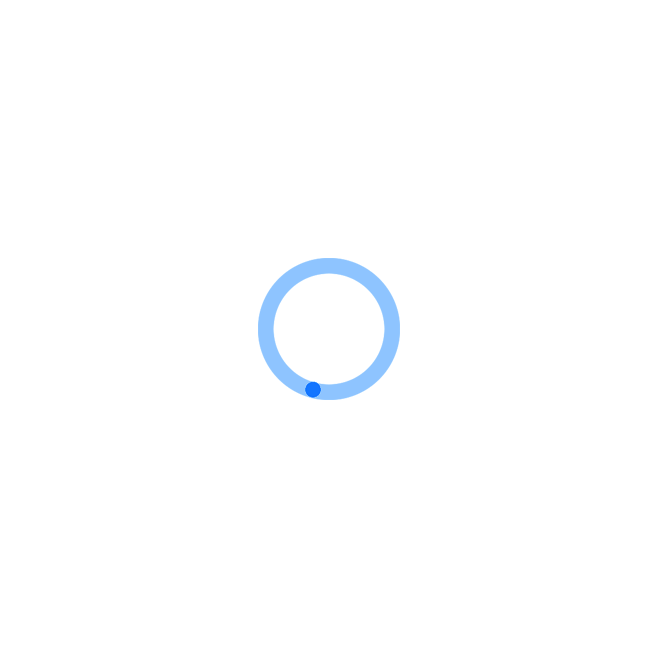
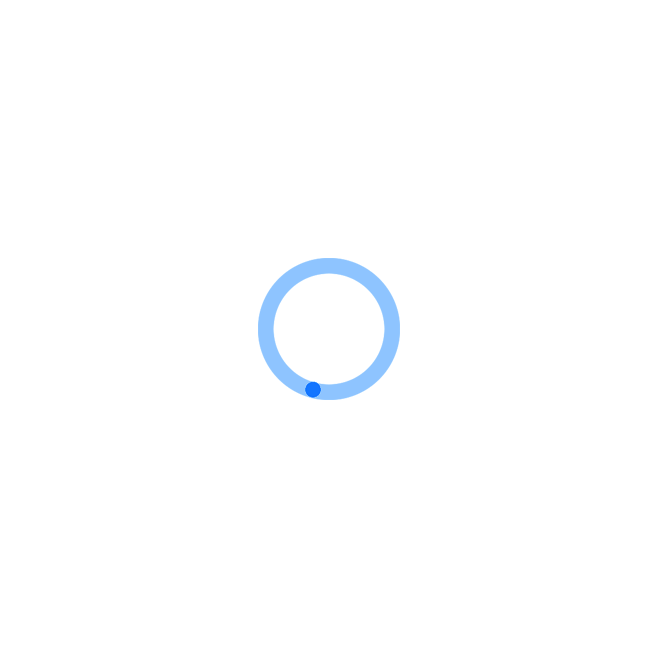
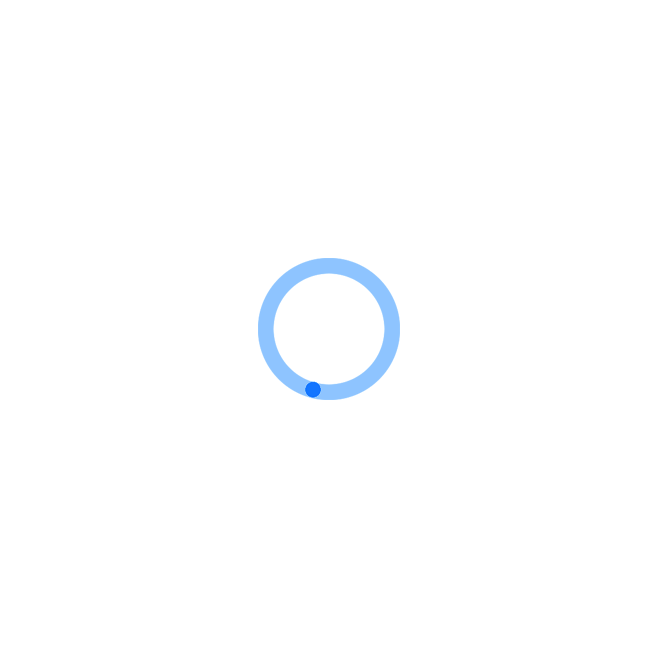
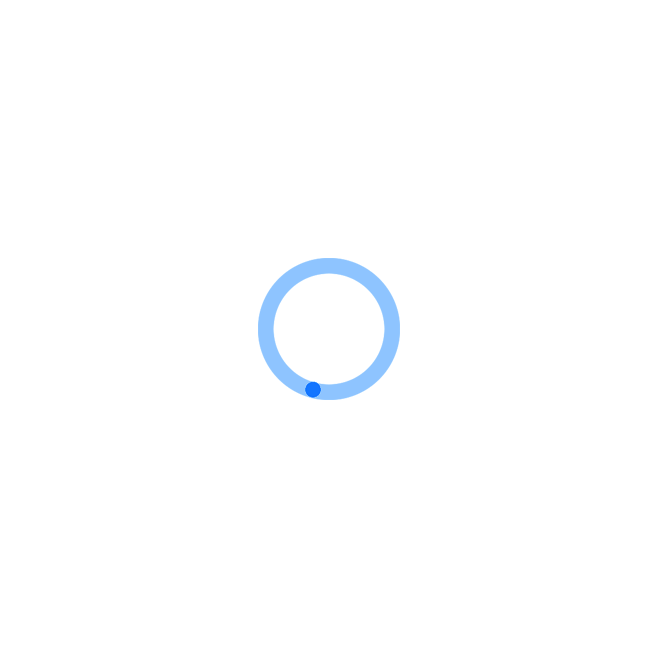
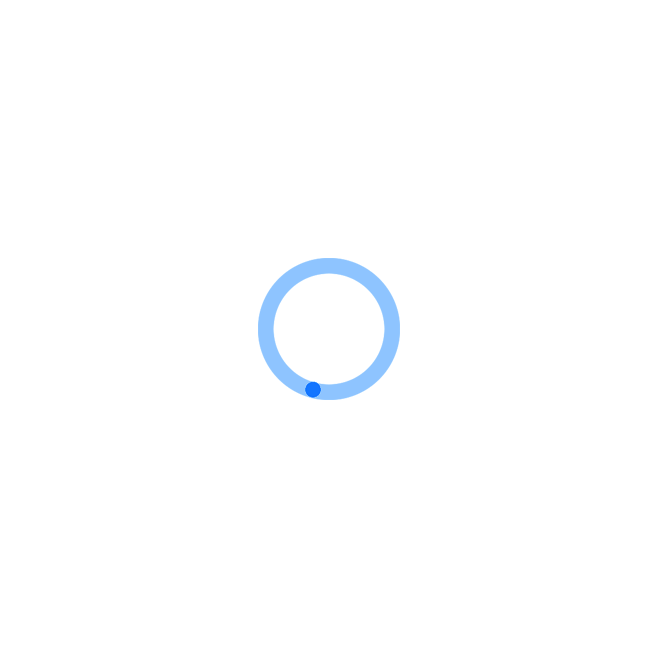
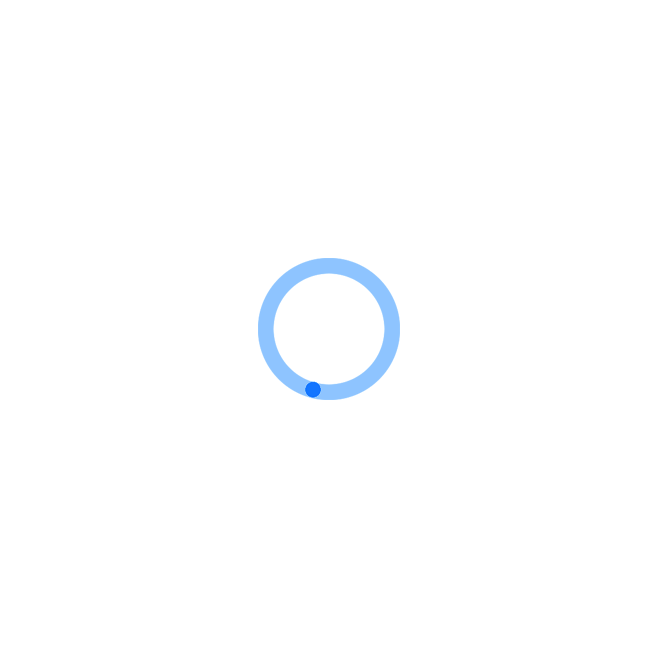
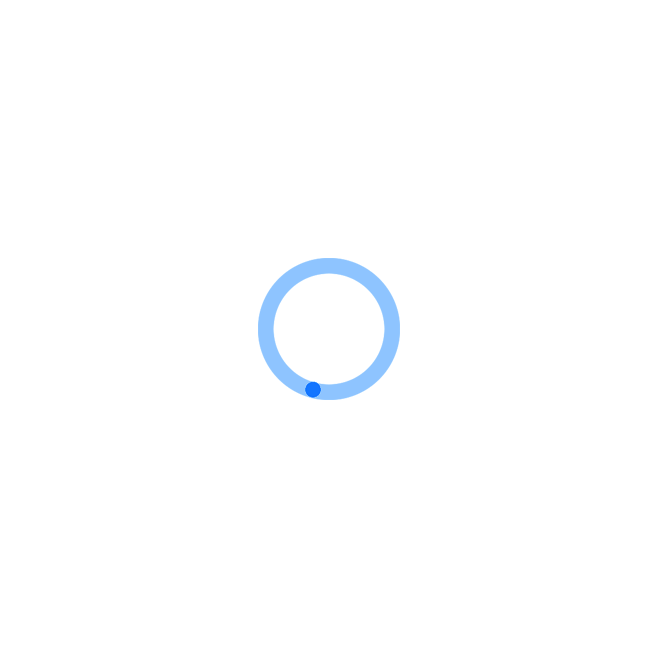
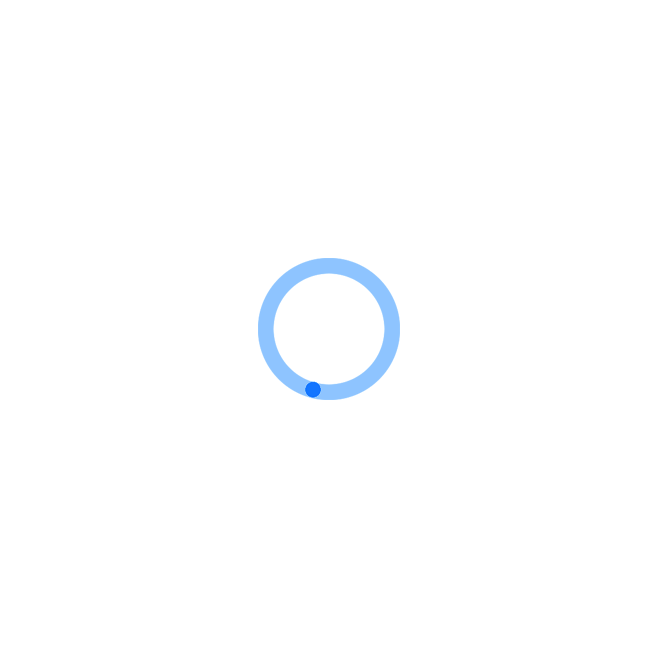
还剩6页未读,继续阅读
文本内容:
化工过程模拟与在线优化化工过程模拟和在线优化是当今化工产业的重要组成部分,对于提高产品质量、降低生产成本、优化生产流程等方面具有至关重要的作用O本文将探讨化工过程模拟与在线优化的应用场景及相应方法,旨在帮助读者更好地理解两者的结合的重要性和应用价值关键词化工过程模拟、在线优化、化工生产、优化算法、过程控制化工过程模拟化工过程模拟是利用计算机技术对化工生产过程进行模拟仿真,以便对生产流程进行优化和改进它可以帮助企业实现以下目标优化生产流程通过模拟生产流程,可以发现生产过程中的瓶颈和问题,进而进行改进和优化,提高生产效率降低试验成本通过模拟实验,可以在实际生产之前对各种工艺条件和操作参数进行试验,从而降低实际生产的试验成本提高产品质量通过模拟生产过程,可以优化工艺条件,从而提高产品质量和稳定性然而,化工过程模拟也面临着一些挑战,如模型精度不够、模拟时间较长、软件接口不统一等因此,在实际应用中需要根据具体问题进行改进和优化在线优化在线优化是一种利用计算机技术对化工生产过程进行实时优化的方法它通过实时监测生产数据,对生产过程进行在线调整和优化,以实现提高产量、降低成本、提高产品质量等目标具体方法包括以下几种调整工艺参数通过实时监测关键参数,如温度、压力、浓度等,对生产工艺参数进行在线调整,以提高产量和产品质量优化设备配置通过对设备运行数据进行实时监测和分析,优化设备配置和操作条件,提高设备利用率和降低能耗改进生产流程通过实时监测生产流程数据,发现生产过程中的瓶颈和问题,提出改进方案,优化生产流程然而,在线优化也面临着一些挑战,如数据波动较大、优化算法不够智能、实时调整存在困难等因此,在实际应用中需要结合具体问题进行改进和优化结合应用化工过程模拟和在线优化具有相互补充的优势,将两者结合起来可以更好地发挥各自的优势,提高化工生产的效率和效益在具体应用场景中,可以采取以下方法利用化工过程模拟软件进行离线模拟,为在线优化提供参考通过离线模拟,可以发现生产过程中的问题和瓶颈,为在线优化提供依据和方向将在线优化算法嵌入到化工过程模拟软件中,实现实时优化通过将优化算法嵌入到化工过程模拟软件中,可以在线对生产过程进行实时优化,提高生产效率和降低成本利用大数据和人工智能技术对生产数据进行挖掘和分析,实现精细化管理通过利用大数据和人工智能技术对生产数据进行挖掘和分析,可以发现隐藏的问题和瓶颈,提出更加精细化的管理方案,进一步提高生产的效率和效益本文探讨了化工过程模拟与在线优化的应用场景及相应方法通过化工过程模拟和在线优化的结合应用,可以更好地发现生产过程中的问题和瓶颈,提高生产的效率和效益然而,在实际应用中还需要克服一些挑战和困难未来可以进一步探索更加智能、高效、精准的化工过程模拟和在线优化算法及技术,为实现更加精细化的化工生产管理提供更加有力的支持复杂化工过程模拟作为化工领域的重要支撑技术,旨在通过计算机模型来模拟和预测实际化工生产过程中的各种现象和行为随着化工产业的快速发展和复杂化,传统的单一尺度模拟方法已经难以满足实际生产的需要,因此,从多尺度到介尺度模拟成为了新的研究趋势本文将深入探讨多尺度模拟、介尺度模拟以及复杂化工过程模拟所面临的新挑战多尺度模拟多尺度模拟是一种基于不同时间尺度和空间尺度的计算机模拟方法,旨在解决化工过程中多尺度耦合问题在实际生产中,化工过程涉及多个物理现象和化学反应,如传递、反应、扩散等,这些现象在不同尺度上相互影响,因此,多尺度模拟方法可以更准确地模拟和预测化工过程然而,多尺度模拟方法仍面临着一些问题和挑战,如数据稀疏、不确定性等介尺度模拟介尺度模拟作为一种新兴的计算机模拟方法,可以更好地处理跨尺度耦合问题介尺度模拟方法通过建立一个统一的模型,将不同尺度上的物理现象和化学反应进行集成,从而更准确、更高效地模拟和预测化工过程介尺度模拟的优势在于其可以减少多尺度模拟中的数据稀疏性和不确定性,同时提高模拟的精度和效率然而,介尺度模拟仍存在一些局限性,如模型复杂度高、参数选择困难等复杂化工过程模拟的新挑战针对多尺度到介尺度的转变,复杂化工过程模拟面临着许多新挑战数据稀疏性是多尺度到介尺度模拟中最大的问题之一由于不同尺度上的数据往往难以获取和整合,导致数据稀疏,影响了模拟的精度和效率不确定性也是复杂化工过程模拟中不可忽视的问题不同尺度上的物理现象和化学反应存在大量的不确定性,如何量化这些不确定性并对其进行有效的控制是提高模拟精度的重要手段模型结构和参数选择也是复杂化工过程模拟中的关键问题在介尺度模拟中,需要建立一个统一的模型来集成不同尺度上的物理现象和化学反应,因此,模型结构和参数选择直接影响了模拟的准确性和效率复杂化工过程模拟在多尺度和介尺度方面都面临着巨大的挑战从多尺度到介尺度模拟的转变,可以更准确、更高效地处理跨尺度耦合问题,但同时也带来了新的挑战,如数据稀疏性、不确定性和模型结构与参数选择等为了应对这些挑战,我们需要加强数据整合与采集能力,提高模型的可靠性和鲁棒性,并探索新的模型结构和参数优化方法展望未来,复杂化工过程模拟将会向着更高精度、更高效率以及更加智能化的方向发展随着计算能力的提升和新算法的不断出现,我们有理由相信未来的化工过程模拟将能够更好地服务于化工产业的可持续发展,促进人类社会的科技进步移动床色谱技术是一种高效的分离技术,广泛应用于化工、医药、能源等领域本文旨在模拟移动床色谱过程,对其进行分析,并提出系统优化的方案,以提高分离效率和降低成本模拟移动床色谱过程分析原料油与吸附剂的接触方式在移动床色谱过程中,原料油与吸附剂的接触方式对分离效果有着重要影响一般来说,原料油通过进料口进入色谱柱,与逆流而下的吸附剂充分接触为了提高接触效率,可以采用细颗粒吸附剂和高进料速度,但需要注意色谱柱的压力降和分离效果吸附剂的吸附机理吸附剂在移动床色谱过程中起着关键作用其吸附机理主要包括物理吸附和化学吸附物理吸附主要依靠吸附剂与原料油之间的范德华力相互作用,适用于分离沸点相近的组分化学吸附则是通过吸附剂与原料油之间的化学键合作用,适用于分离结构相近的组分移动床色谱过程中的其他影响因素移动床色谱过程受到诸多因素的影响,如温度、压力、流动速度等提高温度有利于提高吸附剂的吸附容量和降低解吸难度,但过高温度会导致吸附剂失活增加压力可以提高色谱柱的分离效果,但会增加设备成本和能耗适当提高流动速度可以缩短分离时间,但过快会导致传质效果下降系统优化优化移动床色谱技术的重要性移动床色谱技术的优化对于提高分离效率、降低成本、减少环境污染等方面具有重要意义通过优化移动床色谱技术,可以提高吸附剂的吸附容量、降低解吸能耗、缩短分离周期,从而提高生产效率和降低生产成本可能的优化方案及优缺点分析1选用高性能吸附剂采用具有高比表面积、高孔容、良好机械强度和化学稳定性的吸附剂,可以提高吸附效果和解吸速度但高性能吸附剂往往成本较高,可能会增加生产成本2改进进料方式采用脉冲进料或连续螺旋进料方式,可以提高原料油与吸附剂的接触效率,加快传质过程但进料方式的改变可能会影响色谱柱的压力降和分离效果3优化操作条件在保证分离效果的前提下,适当调整温度、压力、流动速度等操作条件,可以降低能耗和设备成本,提高生产效率但操作条件的改变可能会影响产品的质量和稳定性实验设计原则及数据分析方法为了实现移动床色谱技术的系统优化,需要进行实验研究在实验设计过程中,应遵循以下原则1明确实验目标在实验开始前,需要明确优化的目标,如提高吸附剂的吸附容量、降低解吸能耗、缩短分离周期等2控制变量在实验过程中,应控制其他因素不变,只改变需要优化的因素,以分析其对移动床色谱过程的影响3可比性原则在实验过程中,应保持实验条件的一致性,以保证实验结果的可比性在数据分析过程中,应采用现代化的分析工具和方法,如采用色谱软件进行数据处理和模拟,结合数学建模方法对实验结果进行拟合和预测等通过数据分析,可以深入了解移动床色谱过程的规律和特征,为进一步优化提供依据。
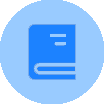
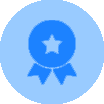
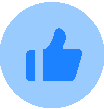