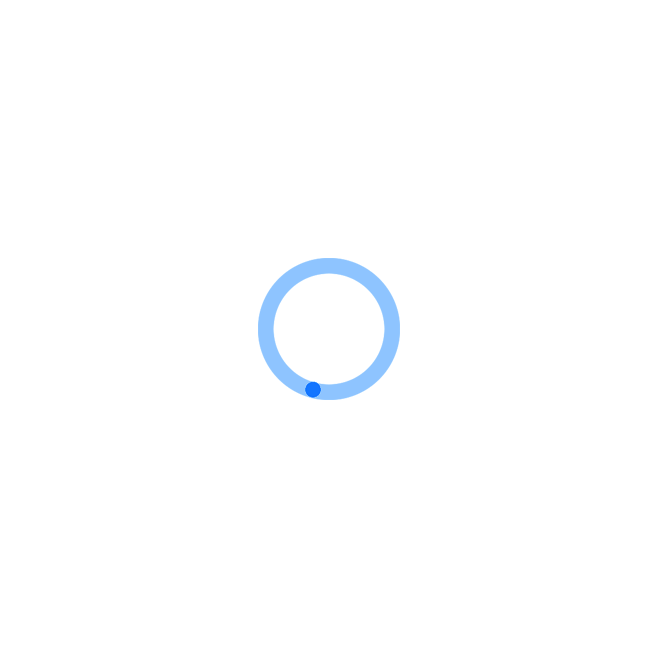
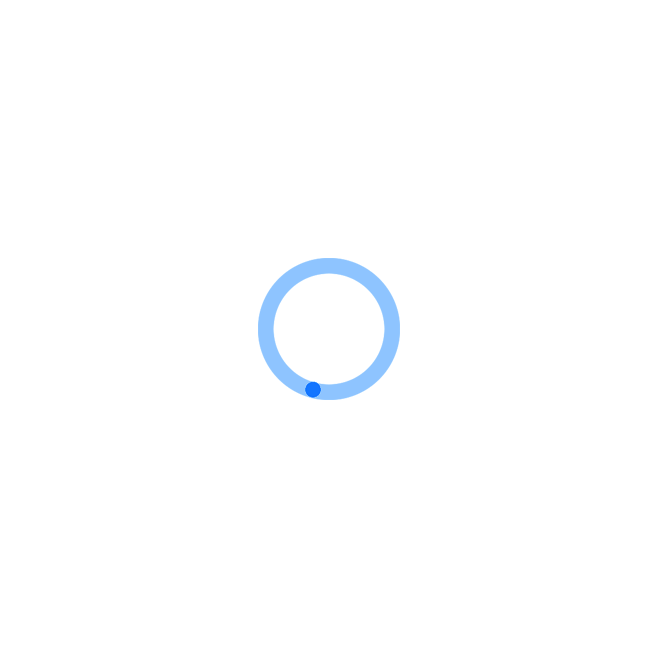
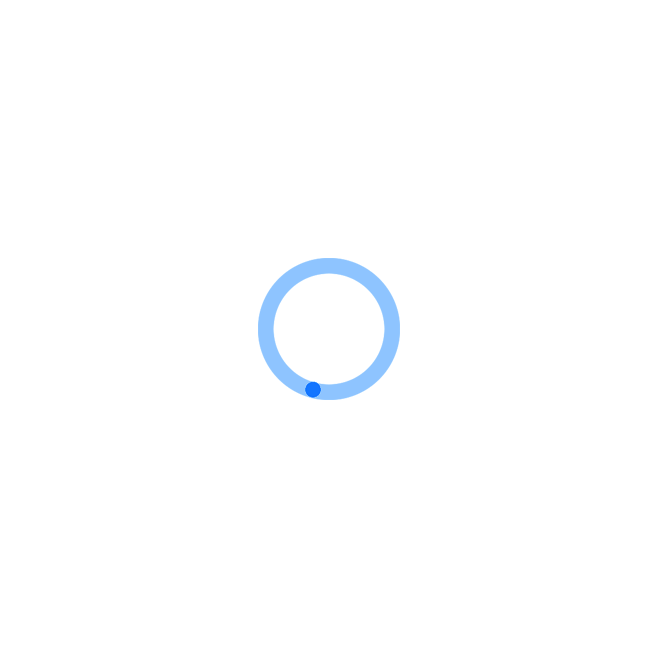
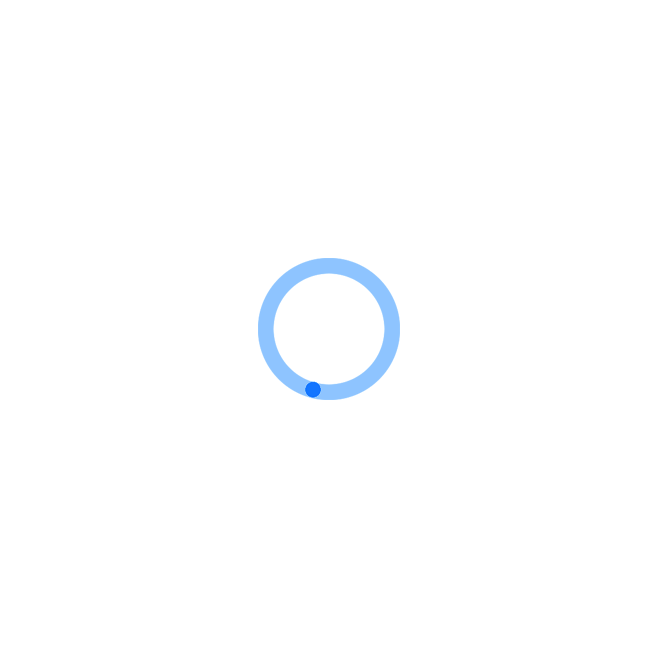
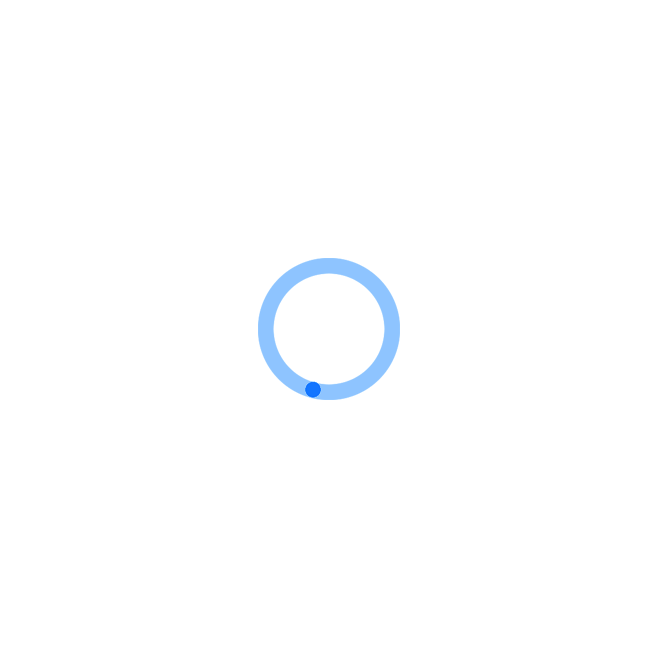
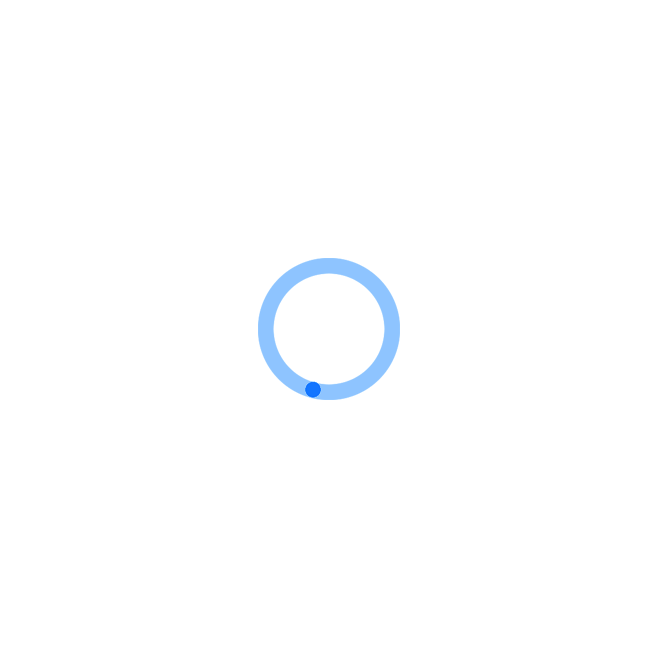
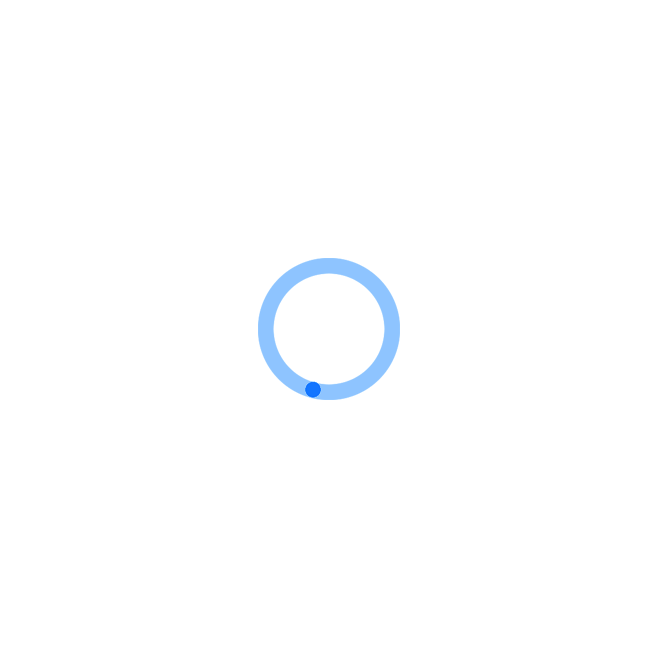
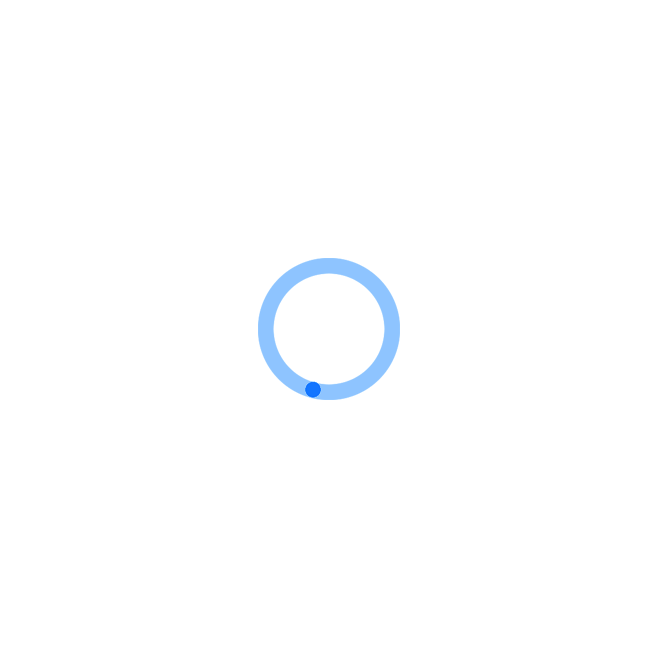
还剩6页未读,继续阅读
文本内容:
(一)物料对粉磨产质量及电耗的影响
1、球磨机入磨物料粒度大小的影响由于物料粉磨时的能量利用率仅为2-3%国内外技术人员经过多年的深入研究和生产实践,提出了多破少磨,以破代磨的预粉碎工艺,使得磨机的产量大幅度提高,粉磨电耗明显降低,增产节能效果明显预粉碎工艺入磨物料粒度由20-25mm缩小到3-5mmo生产实践表明,当入磨物料平均粒度从25mm降到5mm、3mm和2mm时,则磨机产量可分别提高38%、53%和66%众所周知当磨机产量大幅提升时其电耗对应会大幅降低一般不带预粉碎系统的球磨机入磨最大粒度应控制在合理范围另外为减少过粉磨现象,当磨内添加粉状物料如水泥磨用粉煤灰应从磨尾加入,使其先进选粉机,经选粉机分选后细粉作为成品入库,粗粉入磨进行粉磨,提高球磨机粉磨效率
2、入磨物料水分的影响对于入磨物料水分一定要严格控制,物料中保持少量的水分,在磨内气化时,可以带走部分热量,对降低磨温、提高粉磨效率有好处,但物料过于干燥,在磨内流动速度加快,会出现跑粗现象也会影响产品质量如果入磨物料含水分过大,粉磨物料时,筒体内的温度比较高,会产生很多水蒸气,使磨内气体湿含量增大,细颗粒物料会粘在研磨体和衬板上,形成物料垫,使粉磨效率显著降低严重时堵塞隔仓板和出料篦板孔眼,阻止物料通过,以致出现饱磨现象被迫停磨清理,不利于磨机产质量的提高,从而影响磨机整体运行效率当物料中水分波动较大(1%〜5%)会造成磨机产量波动较大,严重影响磨机的正常生产运行入磨物料平均水分一般应控制在1%〜
1.5%为宜
3、入磨物料温度的影响第一,当入磨物料温度超过80℃磨内温度就可超过120℃首先过高的磨内温度易造成物料颗粒产生静电吸附作用由于静电吸附作用,细磨仓中微小颗粒会产生集聚现象,粘附在不平整的研磨体或衬板表面,形成细小颗粒的衬垫层,对研磨体的冲击和研磨起缓冲作用,使粉磨效率降低,电耗增高,水泥磨产量降低10%〜15%且此时的糊球和聚结现象很容易被误认为是由于物料潮湿引起的,实际上是越干燥的物料糊球越严重,因入磨物料水分过小,粉磨过程中产生的热量无法通过水蒸气带出磨外,磨内温度升高,相对湿度降低,静电吸附作用加剧,导致恶性循环第二,当水泥磨磨内温度高达120(:左右时,会造成石膏脱水,生成半水石膏或完全脱水变成无水石膏,引起水泥速凝或假凝,影响水泥质量(淋水)入磨物料温度应控制在460(第三,磨内温度高,对机械设备很不利筒体和轴承等零部件温升也过高,润滑作用降低,影响设备长期安全运转
4、入磨物料均质稳定的影响当入磨物料的质量稳定(粒度、喂料量),喂料量稳定且连续时有利于磨机粉磨效率的发挥和提高
5、入磨物料易磨性的影响水泥粉磨受熟料易磨性的影响较大熟料的易磨性与其各矿物组成的含量、冷却环境有关,当熟料中KH和P值高,C3S含量多,C4AF少,冷却快,质地较脆,则易磨性好如KH和P值较低,C2S和C4AF含量高,因冷却缓慢或还原气氛而结成大块的熟料必然致密,韧性大,易磨性系数小,难磨(二八磨机通风的影响一般来讲圈流磨磨内自由风速宜控制在
1.0-
1.2m/s的范围,如磨内风速过低,将造成磨头负压小,产生冒灰反料现象;细粉不能被及时带出,造成过粉磨现象;磨内温度升高、细粉量大易造成糊球、糊意板,大大降低粉磨效率,从而导致整个系统工况不断恶化因此加大收尘器的维护管理,提高通风面积、降低收尘通风阻力,一方面可以使磨内通风合理,降低磨机电耗,另一方面可以降低排风机电耗磨机系统漏风在实际生产中普遍存在漏风会直接影响磨内通风和粉磨性能,还会造成辅机设备的功率增大,从而使得磨机产量降低能耗增加,所以要重视系统锁风装置的日常维护和巡检,以减少漏风(三八磨机的定期维护和检修
1、填充率、装载量和研磨体级配的合理选择为保证磨机运行状况良好,对磨机要进行定期定检,对磨机的研磨体级配、填充率及装载量进行细化管理,保持磨机稳定高产低能耗运行当磨机规格定后,其磨内有效内径也已确定,生产过程中,如磨机运行良好,产量稳定正常,则需要停机对仓内球面高度进行测量记录,为计算磨机合理的填充率打好基础影响研磨体级配的因素很多,但应坚持以下原则)入磨物料的平均粒度大,硬度大或要求成品细度较粗时钢球的平均球径应大些,反之应小些2)磨机仓内研磨体必须进行大小搭配使用,钢球的规格一般用3~5级不同直径的钢球配合,锻仓级配的钢锻规格一般以2~3级组成若有两个仓用钢球时,则两仓的钢球般相差两级两仓或以上磨一般前仓用钢球,后仓用钢锻或钢球3)同一仓球配应采用两头小中间大的原则,即最大直径和最小直径的钢球少用,中间规格的钢球多用若用两种钢锻时,则各占一半即可,若用三种钢锻时,可根据具体情况适当搭配磨机钢球级配是否合理的判断)若球磨机产量低,产品细度粗,应为装载量不足,或者已磨损严重2)若球磨机产量较高,但产品细度较粗可能由于大球太多,小球太少,即平均球径太大;也可能是前仓的钢球偏多,细磨仓的钢球段太少3)若球磨机产量降低,但产品细度很细有两种可能因素一种是研磨体装载量太多,填充率过大,导致冲击破碎作用较弱,而研磨作用较强;另一可能是平均球径太小所致如何增补研磨体正常生产过程中应根据球磨机磨内研磨体被物料覆盖情况增补研磨体,即停磨的同时停止喂料对于圈流水泥磨,一仓研磨体与物料覆盖层基本保持平衡,二仓料面高于研磨体
2.5cm左右为佳,若钢球露出太多,说明钢球直径过大,或填充率过大,反之则说明球径过小或装载量不足二仓若存料过厚说明填充率不足,反之说明装载量过多另要定期对球磨机内的钢球进行清仓,防止研磨体平均球径的逐渐变小,保持级配的稳定通过对钢球分捡、装填及研磨前后的称重变化,可以掌握已知产量下钢球的损耗量生产过程中研磨体的磨损情况会越来越严重,虽定期补充研磨体,但仍不能保持研磨体级配的正确性,有的钢球变了形,有的甚至是被砸碎有碍于球磨机正常生产,粉碎、研磨效率大大降低,这时如不及时清仓倒球,势必影响球磨机的产量和产品质量清仓倒球,拣出不合格的研磨体,按配球方案重新进行级配是一项必要的措施清仓时间需根据研磨体的消耗、球磨机产量、产品质量情况而定一般对两仓的水泥磨来说,应根据研磨体本身质量进行定期清仓根据仓位、电流下降幅度和研磨体材质消耗量等几方面相结合,来确定补球周期,做好补球记录,增补到最佳填充率如何求得磨机的实际装载量一是将磨机中的钢球倒出后重新过秤;二是根据停磨所测得球面高度来估算,可较为准确的计算磨内实际装载量,容易制定补加钢球的吨数磨内研磨体级配的合理与否直接影响着磨机的产、质量和研磨体的消耗一个合理的研磨体级配是相对的、暂时的,最适宜的级配方案,要根据具体情况,通过长期生产实践,不断进行统计、分析、测定和总结,从而达到不断优化
2、磨机选粉效率、循环负荷率和筛析曲线的定期测定圈流磨是由选粉机与磨机共同组成,选粉机的工作状况对磨机的影响比较大,主要通过循环负荷率、选粉效率与磨机的粉磨效率来反应当循环负荷率增加,意味着通过磨机的物料量增加,喂入选粉机的物料量增加,选粉机负荷增大,分离越不容易,选粉效率则降低;通过选粉效率的公式,也可以看出,循环负荷率与选粉效率成反比,当循环负荷率上升时,选粉效率必然下降循环负荷率还可以从提升机电流的变化及回粉量的变化来进行判断如何根据筛析曲线判断磨内情况工作良好的球磨机筛析曲线分析全线平滑下降,第一仓入料端有倾斜度较大的下降(大约一半左右),接近磨尾处有一小段(约
0.5〜
0.8m)趋于水平,此段不能太长,若靠近入料端的一段筛余曲线不是相对的较陡或者根本没有此段陡线,说明一仓破碎能力不足,则需要调整一仓的研磨体,提高一仓的平均球径若靠近磨尾处的一段水平线太长,说明细磨能力过剩,在各仓中如果出现较长水平段,表示这一段细度变化不大,研磨体的作业情况不良应适当考虑改进研磨体级配或清仓剔除已碎的研磨体要解决两仓的能力不平衡,除调整研磨体的级配外,还可调整研磨体的装载量和仓位长度
(四)、颗粒级配对产品质量的影响
1、水泥颗粒级配对性能的影响在国内外已经进行了长期的分析和研究,并取得了基本结论,对于高等级硅酸盐水泥来说水泥最佳性能的颗粒级配为3〜32Pm颗粒总量不能65%3nm的细颗粒不要超过10%65kim和1|jm的颗粒越少越好,最好没有
2、分别粉磨的优势水泥生产中如将矿渣和熟料混合粉磨,由于熟料和矿渣的易磨性的差异,矿渣的粒径会比熟料的粗,当水泥的比表面积达到350m2/kg时矿渣的比表面积仅有230~280m2/kg如果矿渣达到理想的细度(比表面积达到450-500m2/kg)会造成熟料的过粉磨现象,大量的熟料细颗粒将在很短的时间内水化,产生早期水化热增加、及与减水剂相容性降低等系列弊端,使得水泥性能变差,磨机产量降低,相对能耗升高因此矿渣使用立磨单独粉磨生产高比面积的矿粉,与球磨机比较可以明显降低电耗,提高单机产量然后再与熟料、石膏的细粉混合成水泥,形成分别粉磨”工艺,有利于磨机效率的提高,混合材掺加量大幅提高,且能充分发挥水泥活性,避免过粉磨现象,降低生产成本,实现产品多元化矿渣微细粉的作用一是改善混合料的颗粒分布,尽可能的填充大颗粒之间的空隙,提高水泥颗粒的原始堆积密度,使得水泥在水化之前尽量达到较高的堆积密度,水化以后产生结构更加密实的水泥石,从而提高水泥砂浆和混凝土的强度、密实性和耐久性;二是能起一定的反应晶核的作用,加速水泥初期的水化过程;三是可以降低水泥反应峰值,减少混凝土因发热而引起的裂纹;四是使水泥砂浆有较好的流动性
(五)、联合粉磨系统琢磨机的优化在联合粉磨系统中,弱压机为闭路,起着传统球磨机粗磨仓的作用,后续磨机只承担细磨仓的作用从混压机出来进入球磨机的物料比表面积就已经达到150~200m2/kg如果原传统管式球磨机的设置不变,就难免出现球磨机电耗过高和过粉磨现象为此重新优化球磨机各项性能参数,即可提高水泥质量,又可降低系统电耗联合粉磨系统如何优化
1、大幅度减小研磨体规格13~25mm增加研磨体的比表面积但是,实践表明,研磨体直径不能过小(<13mm)否则产品的颗粒分布范围比终粉磨的还会窄,不利于水泥质量性能发挥
2、减少研磨体在磨内的填充率,即减小钢球的装载量,因为离球磨机中心越近的钢球,粉磨效率就越低
3、由于磨内任务是单一的细磨,球磨机可以改为单仓或双仓即可
4、球磨机的长径比,对于圈流磨,以长径比
2.0~
2.9之间为电耗最低、产量最高,对于开流磨则在4~5之间
5、球磨机的圆周速度也是根据过去入磨粒度25mm时设计的随着球径减小及入磨粒度的减小,也是值得研究的课题。
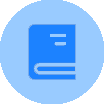
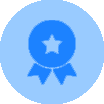
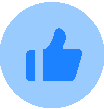