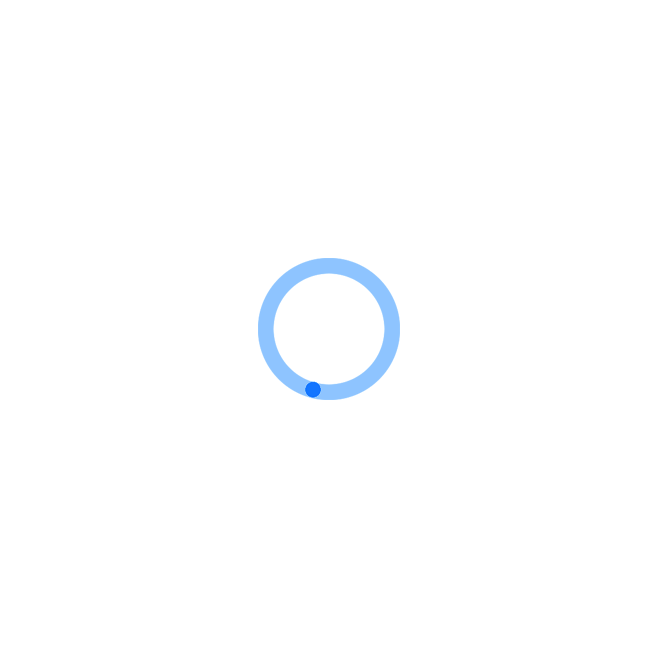
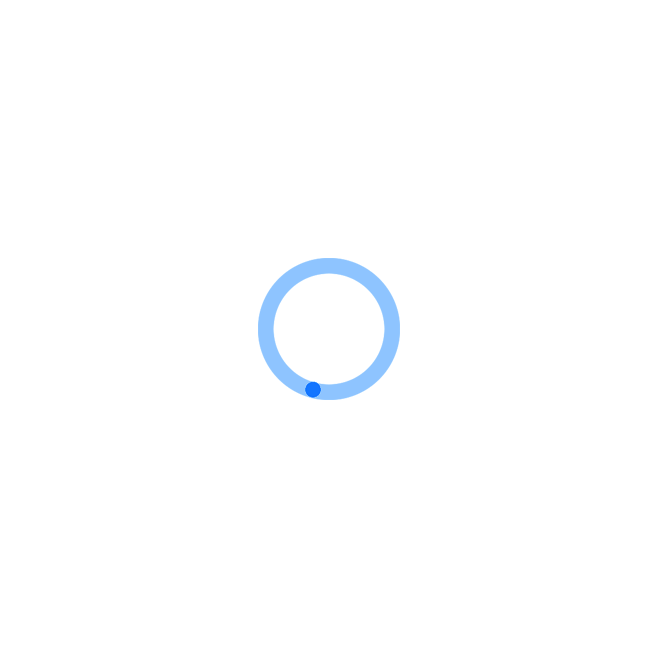
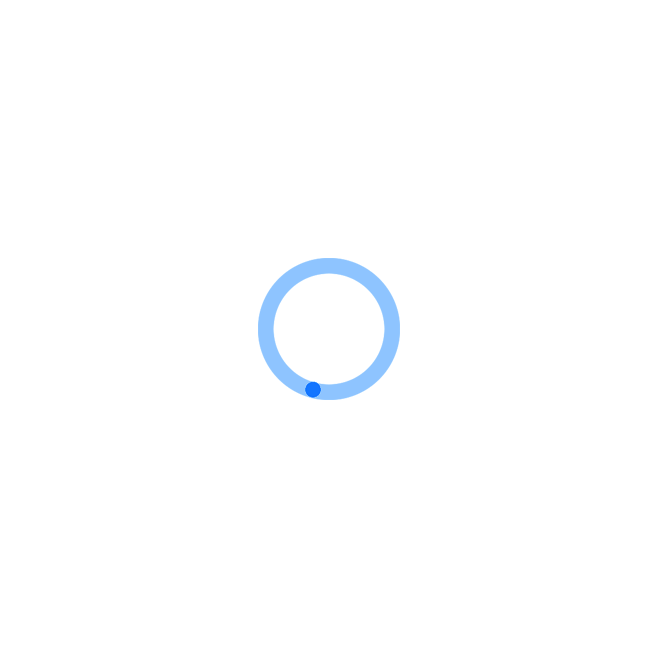
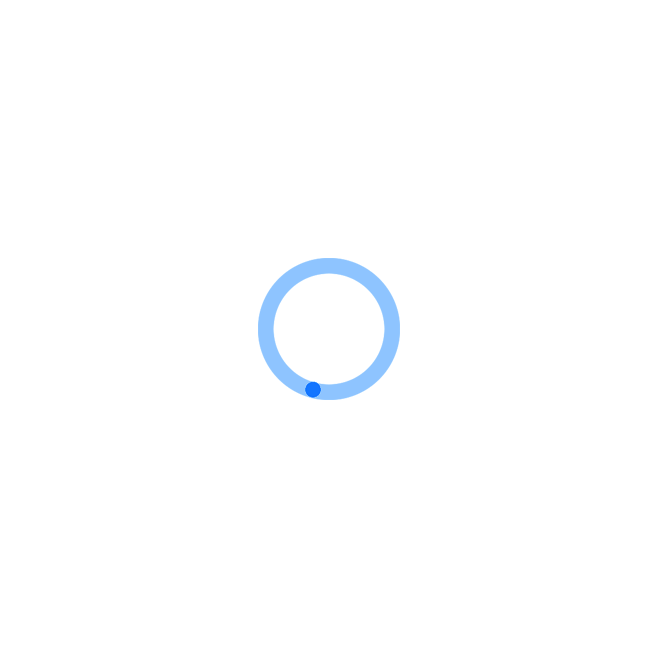
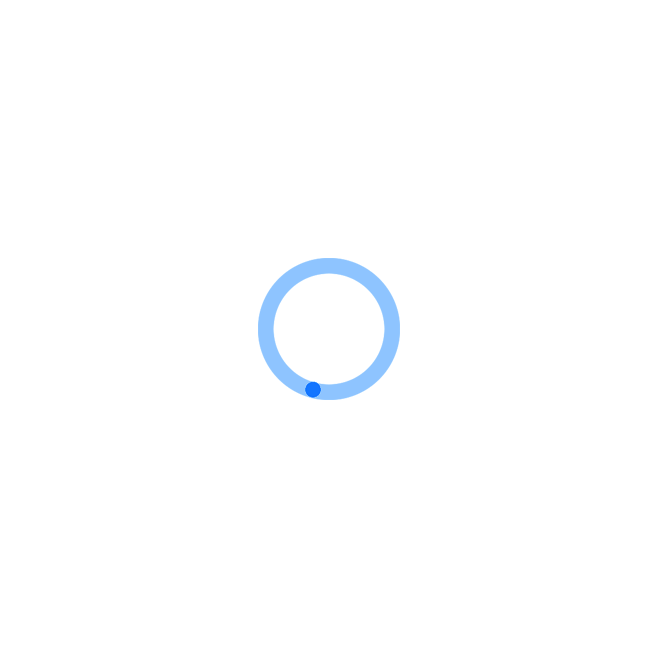
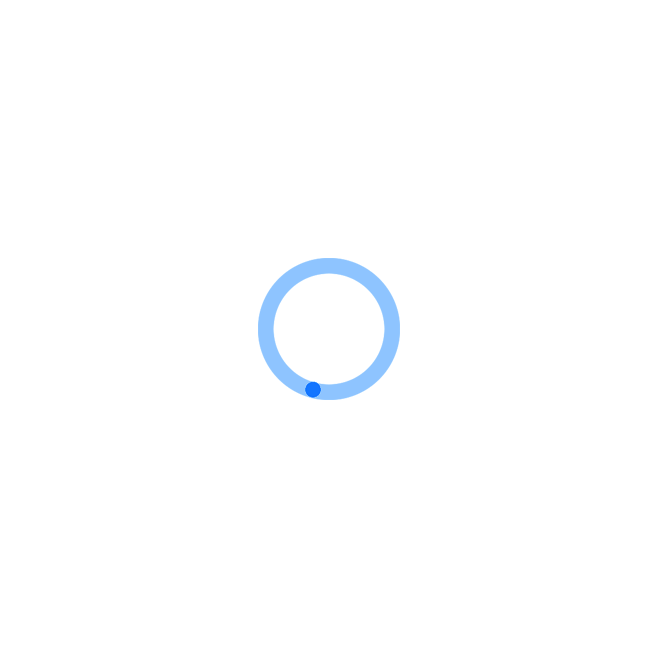
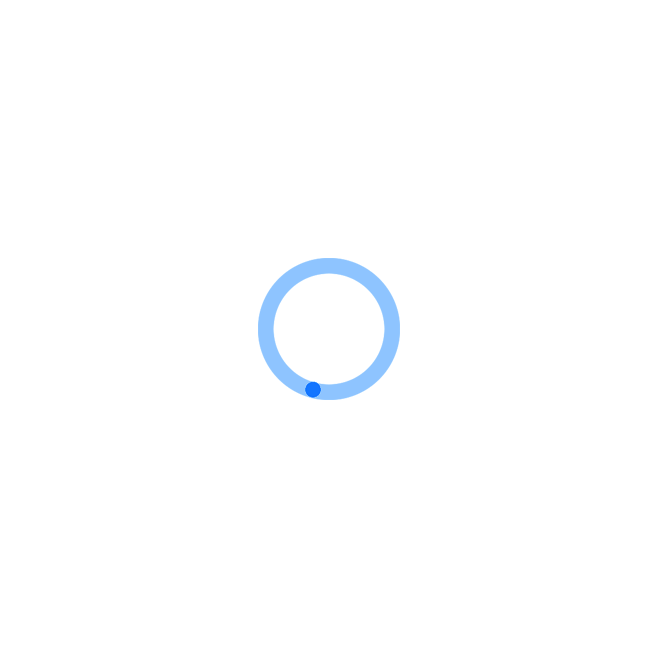
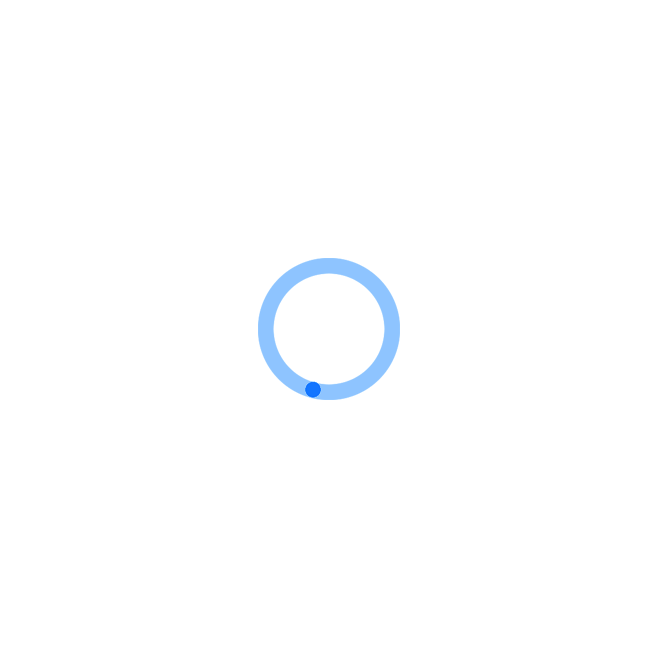
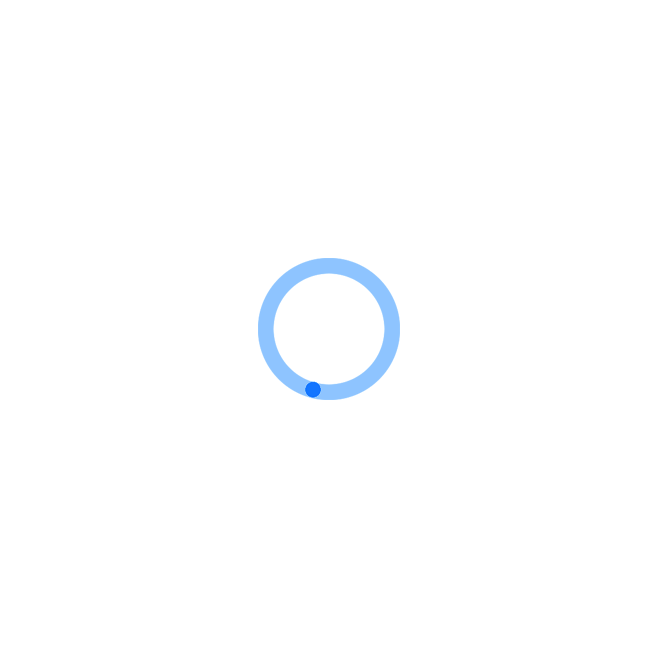
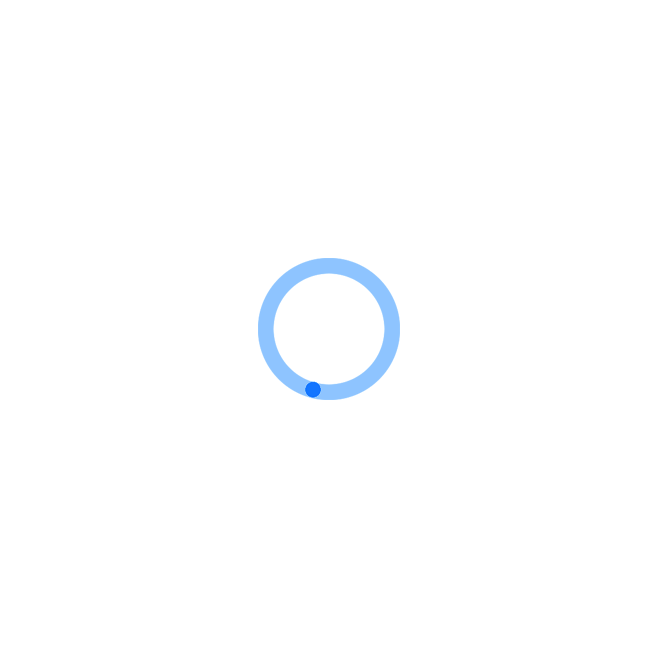
还剩20页未读,继续阅读
本资源只提供10页预览,全部文档请下载后查看!喜欢就下载吧,查找使用更方便
文本内容:
生产车间质量管理制度生产车间质量管理制度—.目的为了提高各车间产品质量,减少不良的发生、保证产品质量的合格性、稳定性,特制定本此规定二.范围本规定合用于各车间各道工序所有成品、半成品的量产和试产三.职责操作者负责各工序产品的质量检查,及标识、区分、定位摆放;生产部各班组责任人负责对各工序产品件的质量抽验、入库管理;技术质检员负责对生产中的产品件进行抽样检验确认;四.规定车间操作者负责自检,作出是否合格的判断通过自我检验,对本工位产品的质量负责;自检产品形成过程中,操作者本人对本作业过程完成的产品质量按照检验标准规定的技术标准进行自行检验,并作出是否合格的判断车间操作者之间负责互检,对加工出来的产品进行二次检验(下序检验上序),有利于保证工序质量,防止疏忽大意而造成的批量不合格品浮现;互检在产品生产过程中,上、下相邻作业过程的操作人员或者组长相互对作业过程完成的产品质量进行二次检查确认3技术检验员负责产品件专检;专检产品在生产过程中,检验人员对产品形成所需要的物料及工序完成的产品质量特性进行专项检验五.内容
1.下料车间:
(七)制程间半成品移转,如发现异常时以异常处理单反应处理第十四条制程自主检查
(一)制程中每一位作业人员均应对所生产的制品实施自主检查,遇质量异常时应即予挑出,如系重大或者特殊异常应即将报告科长或者组长,并开立异常处理单见(表)一式四联,填列异常说明、原因分析及处理对策、送质量管理部门判定异常原因及责任发生部门后,依实际需要交有关部门会签,再送总经理室拟定责任归属及奖惩,如果有跨部门或者责任不明确时送总经理批示第一联-总经理室存第二联质量管理部门(生产管理),第三联会签部门,第四联经办部门
(二)现场各级主管均有催促所属确实实施自主检查的责任,随时抽验所属各制程质量,一旦发现有不良或者质量异常时应即将处理外,并追究相关人员疏忽的责任,以确保产品质量水准,降低异常重复发生
(三)制程自主检查规定依制程自主检查实施办法实施□成品质量管理第十五条成品质量检验成品检验人员应依成品质量标准及检验规范的规定实施质量检验,以提早发现,迅速处理以确保成品质量第十六条出货检验每批产品出货前,品检单位应依出货检验标示的规定进行检验,并将质量与包装检验结果填报出货检验记录表见(附表)呈主管批示后依综合判定执行□质量异常反应及处理第十七条原物料质量异常反应
(一)原物料进厂检验,在各项检验项目中,只要有一项以上异常时,无论其检验结果被判定为合格或者不合格,检验部门的主管均须于说明栏内加以说明,并依据资材管理办法的规定呈核与处理
(二)对于检验异常的原物料经核决主管核决使用时,质量管理部应依异常项目开立异常处理单送创造部经理室生产管理人员,安排生产时通知现场注意使用,并由现场主管填报使用状况、成本影响及意见,经经理核签呈总经理批示后送采购单位与提供厂商交涉第十八条在制品与成品质量异常反应及处理
(一)在制品与成品在各项质量检验的执行过程中或者生产过程中有异常时,应提报异常处理单,并应即将向有关人员反应质量异常情况,使能迅速采取措施,处理解决,以确保质量
(二)创造部门在制程中发现不良品时,除应依正常程序追踪原因外,不良品当即剔除,以杜绝不良品流入下制程(以废品报告单提报,并经质量管理部复核才可报废)第十九条制程间质量异常反应收料部门组长在制程自主检查中发现供料部门供应在制品质量不合格时,应填写异常处理单详述异常原因,连同样品,经报告科长后送经理室绩效组登记(列入追踪)后,送经理室品保组人员召集收料部门及供料部门人员共同检查料品异常项目、数量并拟定处理对策及追查责任归属部门(或者个人)并呈经理批示后,第一联送总经理室催办及催促料品处理及异常改善结果第二联送生产管理组(质量管理部)做生产安排及调度,第三联送收料部门(会签部门)依批示办理,第四联送回供料部门创造科召集机班人员检查改善并依批示办理后,送经理室品保组存,绩效组重新核算生产绩效及催促异常改善结果车间质量管理制度2022-08-1912:52|#3楼本企业质量方针向顾客提供优质的产品,优质的工程,满意的服务创造中心质量惩罚标准
一、目的为提高创造中心各级人员工作责任心,确保产品质量,也为产品检验中做到有据可依据,特制订本规范
二、范围本规定适合创造中心
三、定义1轻微不良以公司及客户立场,不会对客户造成质量隐患,但未能达到产品质量标准的产品不良普通不良以公司及客户立场,会对客户造成一定质量隐患的产品不良严重不良以公司及客户立场,会对客户造成严重质量隐患,同时会引起客户投诉会对公司造成一定影响和经济损失的产品不良
四、质量目标
1、产品质量零部件交验一次性合格率98%关键件主要件优良率60%以上
2、分项工程质量一次合格率100%优良率不低于80%o
3、单位工程竣工交验合格率100%优良率不低于50%o为实现上述方针、目标,全厂职工必须遵守以下原则1坚持质量第一数量、成本必须服从质量,满足顾客要求2严格质量管理质量体系文件是治厂法规,人人必须遵守3强化预防控制落实质量职能,实行全过程预防和控制,保证不合格产品不交付顾客4竭诚服务顾客视顾客为上帝,热情做好售前、售中、售后服务,任何伤害顾客行为都要严格追究
五、各个车间产品检验制度
1、各个车间必须严格按标准、按手艺、按图纸和有关技术文件要求在产品生产过程中坚持三检制度
2、根据产品的技术要求,生产数量在100件以下的,质量管理处检验员按30%进行抽检,发现不合格的要100%进行检验未经检验合格的产品,不得流转或者入库车间、班组检验员负责产品质量、工序质量的自检工作,并认真填写检验记录
3、在同一批产品中,第一个加工出来的产品均为首件,首件必须严格检查,首件不合格严禁继续加工,如属返修、操作者必须及时修好,再次交验首件,知道合格后方能继续加工未经检验合格的,不得继续批量生产,否则由车间领导负责操作者负直接责任首件检查由其操作员和质检部制程检验员进行检验,合格后才可以继续批量生产
4、在首件合格的基础上,各级检验人员应做好中间巡回检查,发现问题应找出原因,采取措施,及时防止废品成批生产并把发现的质量问题及时向班组和生产工人交待清晰
5、产品完工检验时,发现与图纸要求不符的应填写“返修通知书”,完成后重新检验并做好记录发现仍不合格的产品应及时填写不合格通知单
6、创造产品检验应在创造各工序主机手经自检合格后,由检验人员按图纸、工艺、技术要求和检验标准的有关规定进行检验,检验的程序如下
1、外观检查,包括表面缺陷、颜色和其它特殊工艺要求,有无不符合要求等,如发现问题,必须划好记号,通知车间其工段返修
2、加强巡回检查,注意各工艺要求操作,控制其标准要求和质量
3、柜类、班台、特殊工艺的产品要求必须要试装,专检人员应负责按样板或者是图纸、定单要求检验试装,并取做好有关试装情况记录在档
4、及时了生产进度及检验情况,如有返修催促返修工段及时返修好,防止漏件、漏检
7、各原材料到货,需经专职检验人员检验合格签字后,方可流转
8、具有特殊要求的产品,均需按要求检验,合格后方可流转
9、产品装配时,所有产品部件必须是经过检验的合格品,装配完毕后,专检员按安装技术质量要求进行检验
10、在生产过程中,需修改图纸时,由车偶尔有关部门向技术工艺处提出,经技术工艺处主管技术人员审核修改后,以书面通知或者在生产图纸上标签修改内容、姓名和日期,并通知车间和质量管理处,其它任何人不得擅自修改如果车偶尔操作者私自修改应受严厉批评,以至赔偿其相应的经济损失图纸修改后由修改者签字有效,车间和检验人员以修图纸修改后由修改者签字有效,车间和检验人员修改后通知单进行生产和检查验收
11、特殊和关键过程的检验,根据技术工艺确定的过程中,关键尺寸数据所编制的作业指导书,工艺规程和关键工序的质量管理点流程图选择检验计量器具对过程中的数据进行检测验收,并做好检验记录
12、完工产品由车间检验人员通知质量管理处对产品进行抽检和复查验收,并由车间转到成品库办理入库手续,成品库管-理-员开具产品入库手续,产品入库单上必须有车间负责人签字,检验员盖的合格章,否则不得列入车间完工项目零部件不全,产品不完善,性能测试不合格
13、车间办理交验入库手续后,将产品放置在指定地点如有构建的损坏由仓库负责,直到产品运走为止
六、奖罚制度制作质量奖罚制度为贯彻公司质量管理体系的要求,催促员工按工艺规程及图纸要求操作,促进制作质量的稳定和提高,加强全体员工的产品质量意识,提高员工的积极性,更好的控制产品质量,保证公司质量目标的实现从而提高公司的知名度特制定本质量奖罚制度A、奖励.各工序当月工作努力,过程检验一次交验合格率高于95%时,对工组(个人)进行奖励,工组(50-100)元、个人(20-50)元成品一次交验合格率高于98%时对车间奖励200-500元100万以上工程出厂合格率100%对车间奖励500-2000元.提出合理化质量改进建议,采用后能明显提高产品质量和工作效率的,奖励50-200元.当月返工通知单在三次以内且未受到质量处罚的奖励20-100元并作为车间评选先进班组(个人)的质量评定依据质量奖励由质量部提出,经主管领导批准交行政部,重大奖励由质量部提出,公司决定B、处罚首先各工序员工在制作过程中必须要经自检合格后报质检处,经质检员确认方可流入下道工序,做好上下工序的衔接工作,本道工序必须对上道工序的构件进行复查,发现有不合格的不得接收,各工序一次报检不合格由质检员开返工通知单,责令其在规定时间内返工完毕,员工必须无条件在返工/返修通知单上签名,根据存在的错误大小也可对其做出相应的经济处罚,直到整改合格为止所有工序在操作前如有不明事宜或者遇到图纸不清等疑问时必须请示上级主管领导,听从领导的安排,擅作主张而造成错误的应当受到相应的经济处罚为了让员工清晰本工序的质量处罚依据,做好本职工作,特定以下处罚金额
一、开料.材料的材质、下料、精裁尺寸与图纸、定单不相符50-100元.锯路及缺边、爆边、崩边不合格且造成返工10元.可视面有划伤、压伤、起泡、色差及斑点等现象且造成返工20元
二、切割.材料的材质、规格尺寸与图纸不符30-100元.切割尺寸偏差且造成返工20-100元.切割边缘不合格且造成返工10-50元
三、半自动切割
1.坡口角度、方向和尺寸偏差且造成返工3件以下10元3—10件20元10件以上30—100元.下料尺寸偏差且造成返工20-50元.下料板用错30-100元
四、剪板.材料的材质、规格尺寸与图纸不符30-100元.剪板角度和尺寸偏差超出允许范围需返工3-10件20元10-20件20-50元20件以上50-100元
五、组立.翼、腹板规格与图纸不符30元.组立前翼缘板边缘未打磨,腹板未清渣10元.腹板组偏且造成返工门焊前1件10元/人次门焊后1件15元/人次门焊前2-5件20元/人次门焊后2-5件30元/人次门焊前5件以上20-50元/人次门焊后5件以上50-100元/人次
六、门焊.一米内直径为1L气孔2个或者以上5元.密集或者局部连续气孔10元.焊脚尺寸严重偏差需补15元.焊缝严重咬边需补20元.焊穿,焊缝成形超差15元
七、机械矫正.翼缘板倾斜、腹板严重顶弯、构件扭曲造成返工1件2-5件5件以上
八、制孔.孔打错、严重打偏需补孔重打1件5元/人次2-5件10元/人次10元25元50-100元6-10件15元/人次11-20件20元/人次20-50件30-50元/人次50件以上50-100元.孔漏打20元
九、拼装.构件编号不清30元.下料尺寸下短同批构件1-3件10元同批构件3-10件30元同批构件10件以上30-100元.零部件错装、漏装同批构件1-3焊前一次警告、二次10元焊后20元同批构件3处以上焊前10-30元焊后20-50元,总体尺寸焊前10-30元焊后20-50元.拼装焊缝割渣及返工造成的焊疤未修磨干净50元
十、焊接.不打焊工钢号5元.焊缝咬边、弧坑、表面气孔严重、成形过差10元.焊脚高度严重不够或者过大一次口头警告二次10元.封口不封一次口头警告二次5元.未根据工艺而达不到焊缝探伤等级要求20元.据工艺而合格率低于80%(按焊缝长度计算)20元.擅自焊接未检构件50元.转运构件时零部件无意撞落随意装焊30元.漏焊5元
十一、清渣、打磨、火焰校正及抛丸.油漆前未补磨,飞溅过多一次口头警告、二次5元.抛丸后钢丸成堆,未清除干净5元.抛丸不合格需重抛20元.油漆好后火焰校正不合格需重校20元
十二、油漆.油漆用错50-100元.构件锈蚀、毛刺、油污与灰尘未清理干净就油漆20元.磨擦面误涂20元.油漆严重不均匀流挂、起皱10元.油漆严重未达标或者超标10元.油漆露底10元
十三、小件、次构件.材质、规格与图纸不符20-50元.制作尺寸错误10-50元.制作外观超差需返工10-50元
十四、围护.板材材质、规格型号与图纸不符50元.制作尺寸错误30元
十五、包装.吊装不当造成构件变形15元.油漆未干便包装造成油漆脱落20元.未按规定包装30元上述工序制作过程中违反规定而被处罚时,50元以下由质检人员开具处罚单由质量部长批准;50^100元由质量部上级主管领导批准;造成产品报废根据公司制度由责任人按报废损失的比例赔偿,各班组组长负连带责任,在相应工序受到处罚的同时也受相应的处罚,所有处单一份张贴发布,一份质量部留底,另一份上交生产科车间维修质量管理制度2022-08-1914:20|#4楼维修质量是用户满意度的根本,是公司的生存之本,对维修质量的监控是维修质量的根本保证,在维修工作中对维修质量的监控是重中之重,因此,现作出如下规定第一条、用户抱怨的记录来源于公司全体人员,如某员工接到用户抱怨时,应及时向车间主管反映,车间主管须做好相关记录,并对抱怨作出处理;第二条、对已维修完毕的车辆,经质检员检验不合格的项目作内部返工处理;第三条、对已交付用户的维修车辆,发现不合格的项目作外部返修处理;第四条、主修工对返修单所负责任的项目划分;所涉及的项目有所有的维修项目、保养项目与检修项目;维修项目是指用户或者顾问直接开单更换的项目,也就是指换件项目.保养项目是指常规保养的项目,也就是指没有报价的简单保养项目.检修项目是指车辆在车间检修报价的项目,也就是指有报价或者检查维修的项目.第五条、对于返修责任人的划分,主要以任务委托书或者报价单上的签名来确定;第六条、质检员对返修单所负责的项目划分,技术总监根据实际情况分析来确定质检员所需要负的责任,其中,所涉及的项目有车外能目测的项目、需要试车的项目或者试车能试出的项目,所涉及的部位有底盘部分、后行李箱部份、车内部份、车身整体、车轮部份;第七条、对任务委托书上的维修项目,若有漏项或者做错的,则按第二条或者第三条执行;第八条、对同一车辆同一故障连续返修三次的,责任人必须作出书面检讨;第九条、凡涉及到返修项目的所有车辆,服务顾问、质检员、车间主管或者技术总监必须认真填写“非一次性修复表”;第十条、对返修项目的返工性质与责任人的划分存在疑问的,由车间主管或者技术总监根据实际情况分析后确定;第十一条、对返修的车辆,技术总监会通过“月分析报表”的形式在每一个月底定期发布,并指出当月维修质量具体情况,让员工得知维修质量存在的问题和解决方案,确保维修质量得到有效的提高;第十二条、奖罚制度(视情节严重性)※用户抱怨是指普通的用户抱怨,用户在客服回访或者日常工作中向我站相关人员所反映的不满;第十三条、对于在一个月内,同一个人浮现内部返工第5次以上(含5次),按原处罚标准双倍处罚;第十四条、对于在一个月内,同一个人浮现外部返修第3次以上(含3次),按原处罚标准双倍处罚;第十五条、对于在一个月内,同一个人、同一个问题浮现内部返工第2次以上(含2次),按原处罚标准双倍处罚;第十六条、对于在一个月内,同一个人、同一个问题浮现外部返修第2次以上(含2次),按原处罚标准3倍处罚;第十七条、对于报价出错后引起用户抱怨而未造成损失的,则按一次外部返修处理,对于报价出错后引起用户抱怨而造成损失的,则由公司统一按相关规定处理;第十八条、各项返修的严重程度主要参照《返修情节严重性定位处罚图》来进行评定处罚;第十九条、对于内外返修项目若造成直接经济损失的,则由公司统一按相关规定处理;操作者在生产过程中负责本工序产品与上工序产品的质量检验,要严格执行自检、互检的管理规定,杜绝不良的发生,如发现不良产品,及时通知当班班组长与检验员,协助班组长与检验员对不良产品共同进行判定,确认是否合格;如果产品不合格,应及时对已经生产的产品进行排查确认,在不良产品上做标识,并隔离放置生产班组长在生产过程中负责对所生产工序的人员进行安排、指导,对生产的产品进行抽验,在接到不良反馈信息时及时与检验员联系,对不良产品进行判定,组织相关人员对不良现象进行整改,同时安排操作者对不良产品进行区分、标识、隔离放置,填写质量事故单及解决方案后上报本部门领导,及对不良产品的追踪;
1.3下料班组长负责对生产的各工序产品进行首件判定与过程质量抽验,及对操作者进行质量指导,在检验到不良时及时通知领导及不良工序操作者,协助并监督生产员工对不良产品进行区分、标识、隔离放置,并与生产结束后将不良现象体现与当日报表上,编制再发防止报告上报与部门领导处,同时对不良产品做好交接工作并进行跟踪;当班组长在抽检过程中发现严重不良,而操作者自检、互检未发现时,直接对相关责任人员及管理人员赋予50元以上200元以下的罚款,并进行全厂通报,情节恶劣者直接赋予开除处理,并取销当月工资;当产品发生不良时,当班组长对生产操作者进行包庇,不上报者,直接赋予50元以上200元以下罚款,并进行全厂通报,情节恶劣者,直接赋予开除处理,并取销当月工资;
1.6下料车间产品报废率为2%,每超出一个点,对直接生产班组,在当月绩效评定中减一分,同时按照
5.
1.
9.2进行相应的处罚;
5.
1.7在生产过程中对人为操作不当造成产品不良的,如不良产品可以返修;
5.
1.
8.13件以下者赋予警告处理,并车间通告;
5.
1.
8.23件以上20件以下者处以50元至100元罚款,并全厂通告;
5.
1.
8.320件以上者处以100元以上500元以下罚款,,并全厂通告;
5.
1.9在生产过程中对人为操作不当造成产品不良的,如不良产品不能返修的;
5.L
9.1在2%报废率范围的,赋予警告处理,并车间通告;第二十条、以上相关规定若有与公司的管理制度有冲突之处,则一切按公司管理制度的相关规定处理;
5.L
9.2超出报废率的,处以“报废品数量X原材料价格XL5倍”的罚款;
1.10所有处罚条例直接关联部门领导;
5.2合装车间
2.1焊接岗位操作人员在生产过程中负责对本工序生产产品的自检及各附件的检验,对生产的首件进行确认,并交予同工位人员进行互检,如产品合格交予班组长进行检查,确认产品状态,并在生产过程中对所有产品进行自检,确保产品质量,如发现不良产品,及时通知班组长与技术检验员,协助班组长与技术检验员对不良产品共同进行判定,确认是否合格;如果产品不合格,应及时对已经生产的产品进行排查确认,在不良产品上做标识,并隔离放置
2.2打磨操作人员在对产品进行打磨时,负责对焊接状态进行检查(假焊、焊漏、偏移);
2.3合装班组长在生产过程中负责对所有生产工序的人员进行安排、指导,对生产的产品进行抽验,在接到不良反馈信息时及时与技术检验员联系,对不良产品进行判定,组织相关人对不良现象进行整改,同时安排操作者对不良产品进行区分、标识、隔离放置,并及时上报本部门领导,对不良产品的追踪;
2.4班组长负责对生产的各工序产品进行首件判定与过程质量抽验,及对操作者进行质量指导,在检验到不良时,及时通知班组长与不良工序操作者,协助并监督生产员工对不良产品进行区分、标识、隔离放置,并与生产结束后将不良现象体现与当日报表上,编制再发防止报告上报与部门领导处,同时对不良产品做好交接工作并进行跟踪;
2.5班组长在对产品进行抽检过程中发现,产品存在质量问题,且操作人员未检出时,直接对相关责任人员及管理人员赋予相应处罚;
2.
5.1附件开焊、漏焊或者型号错误直接对相关责任人赋予50元至100元罚款,并全车间通报
2.6当产品发生不良时,班组长对生产操作者进行包庇,不上报者,直接给予50元以上200元以下罚款,并进行全厂通报,情节恶劣者,直接赋予开除处理,并取销当月工资;
2.7在生产过程中对人为操作不当造成产品不良的,如不良产品可以返修;
2.
7.13件以下者赋予警告处理,并车间通告;
2.
7.23件以上20件以下者处以50元至100元罚款,并全厂通告;
5.
2.
7.320件以上者处以100元以上500元以下罚款,,并全厂通告;
5.
2.8在生产过程中对人为操作不当造成产品不良的,如不良产品不能返修;
5.
2.
8.1在
0.5%报废率范围的,赋予警告处理,并车间通告;
5.
2.
8.2超出报废率的,处以“报废品数量X产品价格X2倍”的罚款;
5.
2.9所有处罚条例直接关联部门领导
5.3喷涂车间喷涂岗位操作人员在生产过程中负责对本工序生产产品的自检,对色卡进行确认,并交予同工位人员进行互检,如产品合格交予班组长进行检查,确认产品状态,并在生产过程中对所有产品进行自检,确保产品质量,如发现不良产品,及时通知班组长与技术检验员,协助班组长与技术检验员对不良产品共同进行判定,确认是否合格;如果产品不合格,应及时对已经生产的产品进行排查确认,在不良产品上做标识,并隔离放置
5.
3.1在生产过程中对人为操作不当造成产品不良的,如不良产品可以返修;
5.
3.
1.13件以下者赋予警告处理,并车间通告;
5.
3.
1.23件以上20件以下者处以50元至100元罚款,并全厂通告;
5.
3.
1.320件以上者处以100元以上500元以下罚款,,并全厂通告;
5.
3.2在生产过程中对人为操作不当造成产品不良的,如不良产品不能返修;
5.
3.
2.1在
0.5%报废率范围的,赋予警告处理,并车间通告;
5.
3.
2.2超出报废率的,处以“报废品数量X产品价格X
2.5倍”的罚款;
5.
3.3所有处罚条例直接关联部门领导
5.3返修处理
5.
3.1各车间负责对本车间生产的不良产品进行返修,并对返修后的产品进行质量自检,针对返修不到位的产品进行再次返修,直至符合公司质量标准要求,将返修后的产品合理的放置在规定的位置,填写合格标识(工程名称、规格型号、数量),并通知班组长及技术检验员对返修后的产品进行检验;
5.
3.2班组长和技术检验员负责对返修后的产品进行质量判定,在返修过程中对返修产品进行抽验,并在生产结束后将当天返修产品的质量问题进行汇总,上报于部门领导,同时做好对返修产品的质量跟踪
5.
3.4所有处罚条例直接关联部门领导;
5.4奖励
5.
4.1能及时发现本工序产品质量问题的隐患,避免批量不合格发生员工,每举报一次赋予奖励50次/元
5.
4.2发现工艺及技术文件等编写错误,避免产生严重后果员工每举报一次视其影响程度赋予奖励50-100元/次3发现技术检验员将不合格品误判为合格,避免或者减少质量损失者,视其影响程度每举报一次奖励50^100元/次4互检时发现上工序产品存在严重质量问题,避免不合格流入下工序者,每举报一次赋予奖励20次/元5对本工序存在的质量问题或者隐患,能积极提出改善建议被采用者,视其改善效益,赋予奖励50〜500元/次规定自2022年02月日实施生产车间质量管理制度2022-08-1912:35]#2楼第一条目的为保证本公司质量管理制度的推行,并能提前发现异常、迅速处理改善,借以确保及提高产品质量符合管理及市场需要,特制定本细则第二条范围本细则包括
(一)组织机能与工作职责;
(二)各项质量标准及检验规范;
(三)仪器管理;
(四)质量检验的执行;
(五)质量异常反应及处理;
(六)客诉处理;
(七)样品确认;
(八)质量检查与改善第三条组织机能与工作职责本公司质量管理组织机能与工作职责口各项质量标准及检验规范的设订第四条质量标准及检验规范的范围规范包括
(一)原物料质量标准及检验规范;
(二)在制品质量标准及检验规范;
(三)成品质量标准及检验规范的设订;第五条质量标准及检验规范的设订
(一)各项质量标准总经理室生产管理组会同质量管理部、创造部、营业部、研发部及有关人员依据操作规范,并参考
①国家标准
②同业水准
③国外水准
④客户需求
⑤本身创造能力
⑥原物料供应商水准,分原物料、在制品、成品填制质量标准及检验规范设(修)订表一式二份,呈总经理批准后质量管理部一份,并交有关单位凭此执行
(二)质量检验规范总经理室生产管理组召集质量管理部、创造部、营业部、研发部及有关人员分原物料、在制品、成品将
①检查项目
②料号(规格)
③质量标准
④检验频率(取样规定)
⑤检验方法及使用仪器设备
⑥允收规定等填注于质量标准及检验规范设(修)订表内,交有关部门主管核签且经总经理核准后分发有关部门凭此执行第六条质量标准及检验规范的修订
(一)各项质量标准、检验规范若因
①机械设备更新
②技术改进
③制程改善
④市场需要
⑤加工条件变更等因素变化,可以予以修订
(二)总经理室生产管理组每年年底前至少重新校正一次,并参照以往质量实绩会同有关单位检查各料号(规格)各项标准及规范的合理性,酌予修订
(三)质量标准及检验规范修订时,总经理室生产管理组应填立质量标准及检验规范设(修)订表,说明修订原因,并交有关部门会签意见,呈现总经理批示后,始可凭此执行□仪器管理第七条仪器校正、维护计划
(一)周期设订仪器使用部门应依仪器购入时的设备资料、操作说明书等资料,填制仪器校正、维护基准表设定定期校正维护周期,作为仪器年度校正、维护计划的拟订及执行的依据
(二)年度校正计划及维护计划仪器使用部门应于每年年底依据所设订的校正、维护周期,填制仪器校正计划实施表、仪器维护计划实施表做为年度校正及维护计划实施的依据第八条校正计划的实施
(一)仪器校正人员应依据年度校正计划执行日常校正,精度校正作业,并将校正结果记录于仪器校正卡内,一式二份存于使用部门
(二)仪器外协校正有关精密仪器每年应定期由使用单位通过质量管理部或者研发部申请委托校正,并填立外协请修单以确保仪器的精确度第九条仪器使用与保养
1、仪器使用人进行各项检验时,应依检验规范内的操作步骤操作,使用后应妥善保管与保养
2、特殊精密仪器,使用部门主管应指定专人操作与负责管理,非指定操作人员不得任意使用(经主管核准者例外)
3、使用部门主管应负责检核各使用者操作正确性,日常保养与维护,如有不当的使用与操作应予以纠正教导并列入作业检核扣罚
4、各生产单位使用的仪器设备(如量规)由使用部门自行校正与保养,由质量管理部不定期抽检
5.仪器保养
(1)仪器保养人员应依据年度维护计划执行保养作业并将结果记录于仪器维护卡内
(2)仪器外协修造仪器邦联保养人员基于设备、技术能力不足时,保养人员应填立外表请修申请单并呈主管核准后送采购办理外协修造□原物料质量管理第十条;原物料质量检验
(1)原物料进入厂区时,库管单位应依据资材管理办法的规定办理收料,对需用仪器检验的原物料,开立材料验收单(基板)、材料验收单(钻头)及材料验收单(普通),通知质量管理工程人员检验且质量管理工程人员于接获单据三日内,依原物料质量标准及检验规范的规定完成检验⑵材料验收单(普通)、(基板)、(钻头)各一式五联检验完成后,第一联送采购,核对无误后送会计整理付款,第二联会计存,第三联料库,第四联质量管理存,第五联送保税且每次把检验结果记录于供应厂商质量记录卡,并每月根据原物料品名规格类别的结果统计于供应商质量统计表及每月评核供应商的行分于供应商的评价表,提供采购作为选择对抗厂商的参考资料□创造前质量条件复查第十一条创造通知单的审核(新客户、新流程、特殊产品)质量管理部主管收到创造通知单后,应于一日内完成审核
(一)创造通知单的审核I、订制料号-PC板类别的特殊要求是否符合公司创造规范
2、种类-客户提供的油墨颜色
3、底板-底板规格是否符合公司创造规范,使用于特殊要求者有否特殊注明
4、质量要求-各项质量要求是否明确,并符合本公司的质量规范,如有特殊质量要求是否可接受,是否需要先确认再确定产量
5、包装方式-是否符合本公司的包装规范,客户要求的特殊包装方式可否接受,外销定单的ShippingMark及SideMark是否明确表示
6、是否使用特殊的原物料
(二)创造通知单审核后的处理
1、新开辟产品、试制通知单及特殊物理、化学性质或者尺寸外观要求的通知单应转交研发部提示有关创造条件等并签认,若确认其质量要求超出创造能力时应述明原因后,将创造通知单送回创造部办理退单,由营业部向客户说明
2、新开辟产品若质量标准尚未制定时,应将创造通知单交研发部拟定加工条件及暂订质量标准,由研发部记录于创造规范上,作为创造部门生产及质量管理的依据第十二条生产前创造及质量标准复核
(一)创造部门接到研发部送来的创造规范后,须由科长或者组长先杳核确认下列事项后始可进行生产
1、该制品是否订有成品质量标准及检验规范作为质量标准判定的依据
2、是否订有标准操作规范及加工方法
(二)创造部门确认无误后于创造规范上签认,作为生产的依据口制程质量管理第十三条制程质量检验
(一)质检部门对各制程在制品均应依在制品质量标准及检验规范的规定实施质量检验,以提早发现异常,迅速处理,确保在制品质量
(二)在制品质量检验依制程区分,由质量管理部IPQC负责检验
1、钻孔TPQC钻孔科日报表
2、修一-针对路线印刷检修后分十五条以下及十五条以上分别检验记录于IPQC修一日报表
3、修二-针对镀铜(Cu)易(Sn/Pb)后15条以上分别检验记录于IPQC修二日报表
4、镀金-IPQC镀金日报表
5、底片创造完成正式钻孔前由质量管理工程科检验并记录于底片检查要项
6、其他如喷锡板制程抽验管理日报表、QAI进料抽验报告、S/M抽验日报表等抽验
(三)质量管理工程科于制程中配合在制品的加工程序、负责加工条件的测试
1、钻头研磨后规范检验并记录于钻头研磨检验报告上
2、切片检验分PIH、一次铜、二次铜及喷锡蚀铜分别依检验规范检验并记录于(QAEMicrosectionReport)(AQESolderabilityTesReport)等检验报告
(四)各部门在创造过程中发现异常时,组长应即追查原因,并加以处理后将异常原因、处理过程及改善对策等开立异常处理单呈(副)经理指示后送质量管理部,责任判定后送有关部门会签再送总经理室复核
(五)质检人员于抽验中发现异常时,应反应单位主管处理并开立异常处理单呈经(副)理核签后送有关部门处理改善
(六)各生产部门依自检查及按次点检发生质量异常时,如属其他部门所发生者以异常处理单反应处理。
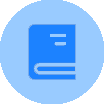
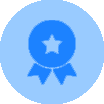
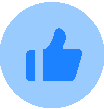