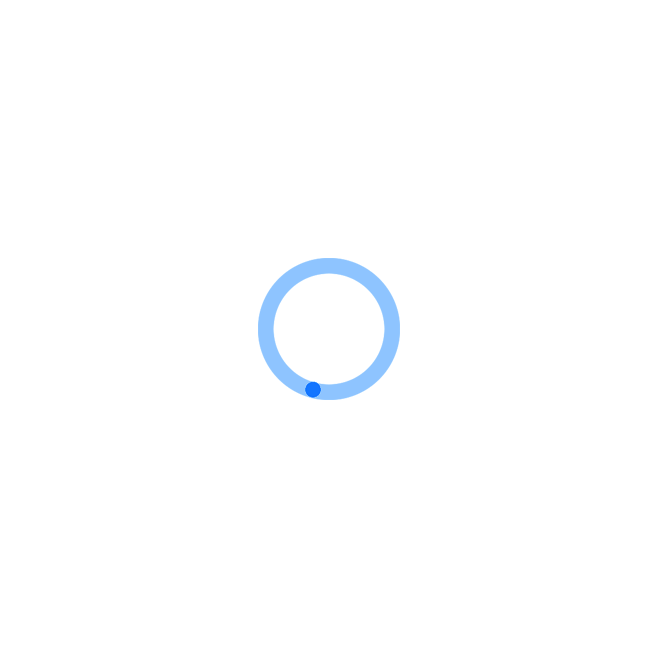
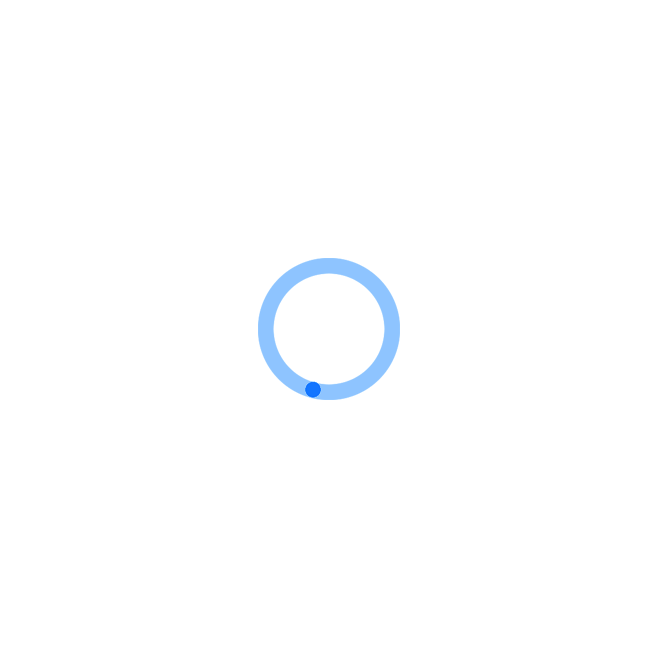
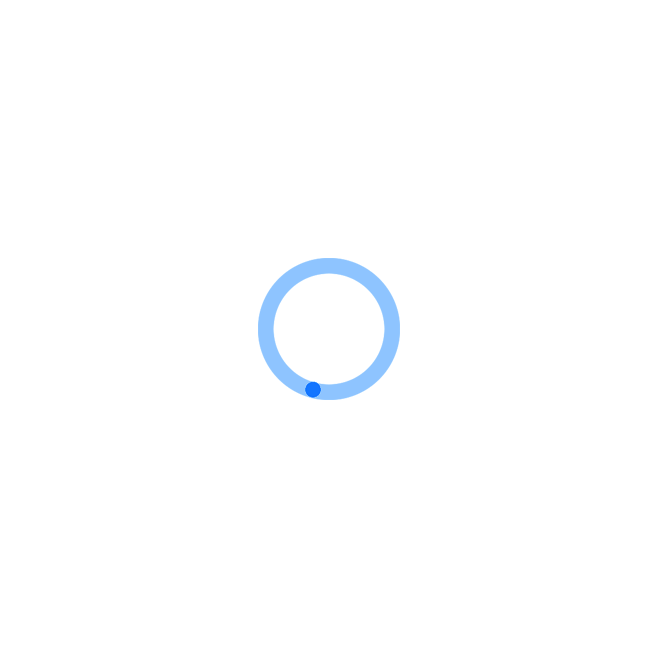
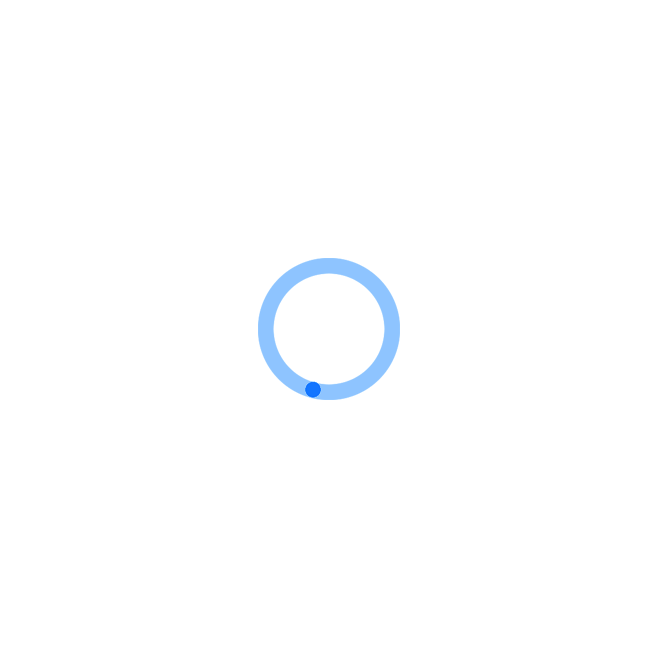
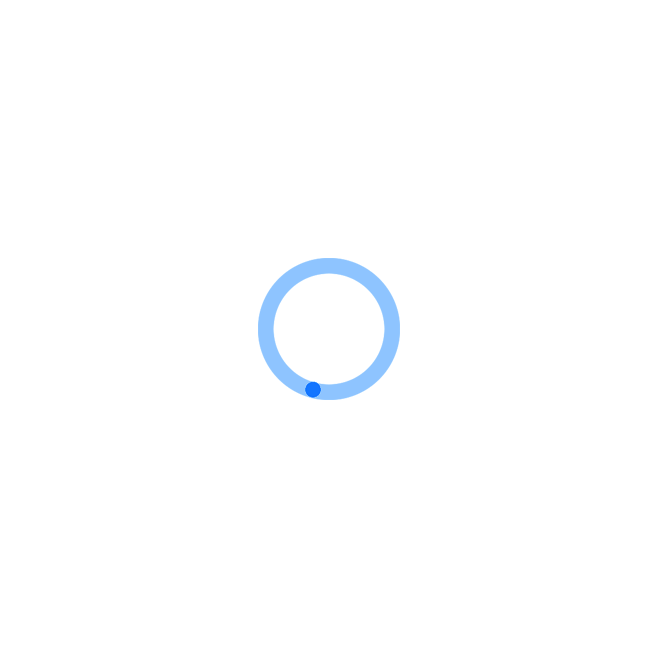
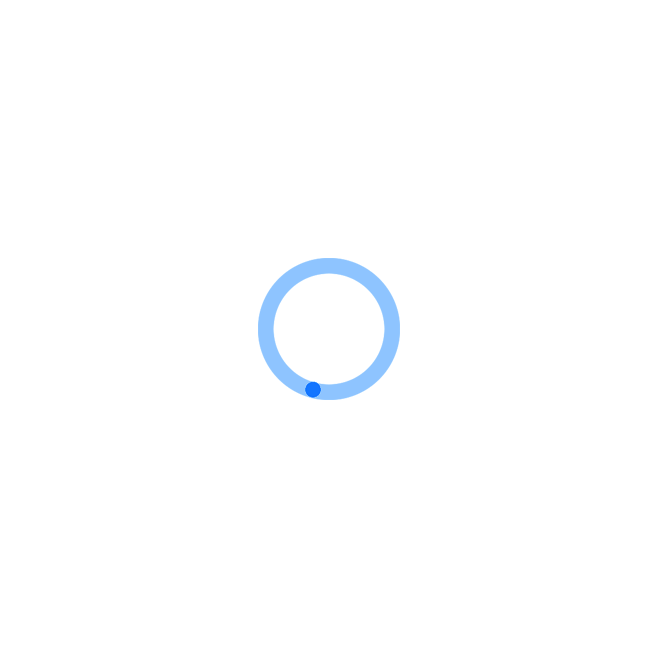
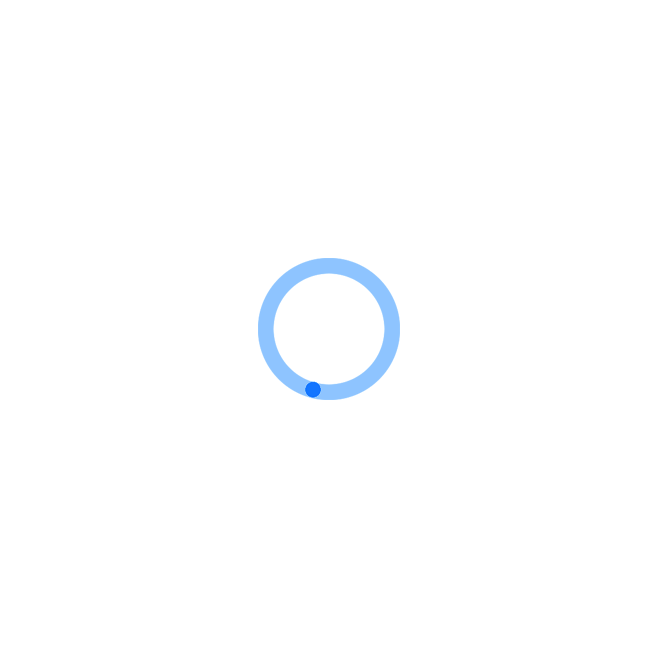
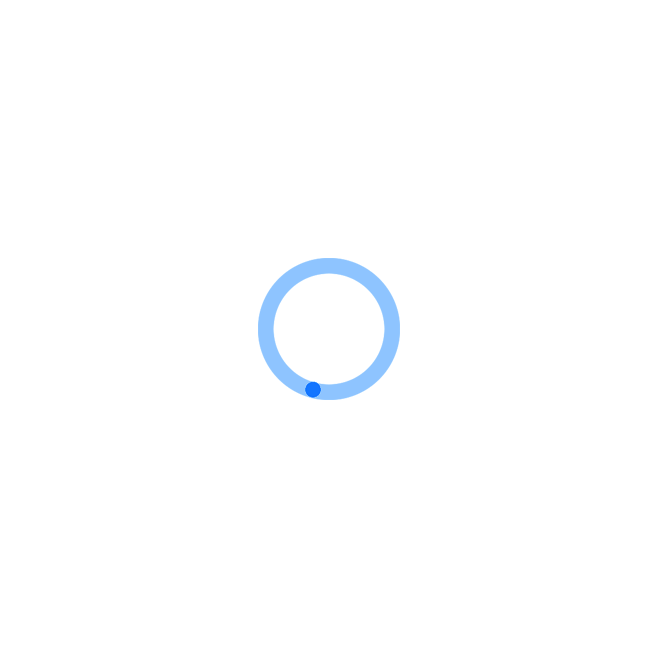
还剩6页未读,继续阅读
文本内容:
标识管理规定
1、目的为防止不同类型、不同状态的产品混淆,避免不合格品非预期使用并确保需要时实现产品的可追溯性,特制定本规定
2、范围适用于所有原材料、半成品、产成品、不合格品、物料、量具及生产设备的标识和检验状态标识
3、职责权限
3.1质检部负责发布产成品包装标识的说明及具体要求;负责组织产品质量缺陷时的调查2生产管理部负责组织各车间完成检验状态标识的设计、制作,并对各车间的标识工作进行监控各车间负责本车间生产过程中的一般性标识的投用和管理;负责各类原材料、半成品、产成品及不合格品标识按要求投用和监控质检部、生产管理部,均可对标识管理规定执行情况进行考核
4、工作程序和要求标识分类标识分为物料标识及状态标识两大类
4.L2物料标识用于明确物料属性,如名称,规格型号,生产批次等
4.L3状态标识用于明确物料检验状态,如待检、合格、不合格等
4.
1.4物料标识与状态标识,依据具体情况,可以合并或独立标识
4.2标识方法及要求
4.
2.1标识方法有张贴标识卡、悬挂标识牌、库存台账记录、外包装印刷或手写等多种型式
4.
2.2产成品包装标识作为关键性标识,由各车间按照质保部要求的产成品生产要求统一执行
4.
2.3检验状态标识作为关键性标识,由生产管理部统一要求,各车间按照规定的样式实施
4.
2.4其余一般性标识,可由各车间自行组织设计和投用.5凡需要书写的标识,需注意用笔的选择,确保可重复利用,确保字迹工整、清晰、醒目;标识内容无歧义.6凡需要张贴的标识,需选择适宜的张贴材料或张贴方法,确保张贴牢固,持久耐用;不易受外界环境的影响而失效.7各类标识的设计和投用,应考虑物料垛放时的情况,确保物料垛放后,标识仍可在外部明显观察(不要求单一包装均可观察)
4.3新购原材料标识原材料到厂后,仓储车间负责将其置于待检区,对于本身未作标识或标识不清的原材料,必须确认物料名称、规格型号等关键信息,并做标识明显不符合标识要求的,可向质保部反馈,并有权拒收2经质保部检验合格的原材料,仓储车间根据《原材料检验报告单》的合格结论办理入库手续入库时,仓储车间应根据供方提供的“送货单”,确认产品名称,规格型号,数量,批次等信息,并在存放过程中持续做好标识,并定期巡查,维护标识完整、准确及清晰3经质保部检验不合格的原材料,仓储车间如未收货,应拒收货;如已收货,应将其放置于不合格品区,并悬挂不合格品标识确保该批物料已进行显著的标识,并做好有效隔离措施,以免误用.4质保部暂未检验合格的原材料,仓储车间办理收货后,应将其放置于待检区,并悬挂待检品标识,确保该批物料已进行显著的标识,以免误用
4.4生产过程中的标识对于生产过程所使用的原材料,应保持其原有产品标识;如不能,车间可在盛装的容器上直接标明其名称、型号、批次等信息未经检验前的产成品,存放按待检品执行;标识按质保部要求的产成品生产要求统一执行
4.5产成品的标识
4.
5.1未经检验前的产成品,按
4.4生产过程标识的要求执行2经检验合格的产成品,转序至仓储车间仓储车间应始终在搬运、入库、贮存、出库等环节,保持完整的产成品包装及胶带、喷码等信息3经检验不合格的产成品,放置于不合格品区或悬挂不合品标识牌,同时做好有效隔离措施,防止其误用4仓储车间库存的产成品,如需再次开封,作业前应征得质保部同意;作业完毕后,按质保部要求重新进行封装
4.6几类特殊情况的标识要求各车间已有库存或在用物资,在自检、互检环节认为存在可疑情况时、或经质检部重新判定为不合格或需拣用时,应将其放置于不合格品区,并悬挂不合格品标识,确保该批物料已进行显著的标识,同时做好有效隔离措施,以免误用同时,及时上报,等待处理各类搬运车辆,只作为物料的临时转运用;不应长时间存放物料,或指定其做为物料的标准存放位置各车间管辖的物料,在未办理物料转移手续前,不应在其他车间辖区内长时间存放4各车间在标识管理过程中,及时完成标识新增、修改、补充、停用,并对其有效性进行监控5各车间应制定适宜的方法开展标识管理工作,明确标识工作的具体责任人如责任区划分、定期巡检等7标识的追溯.1当需要进行追溯时,可依据其原始记录档案,追溯到生产过程、生产单位、操作人员、检验人员、原材料、设备选用、生产数量情况等,以达到追溯的目的.2当接到市场部关于顾客的投诉时,或出现产品质量缺陷时,由质保部组织有关车间进行追溯性调查,直至查出问题发生的工序、时间和原因,调查过程要形成记录8标示工作的考核各车间应针对本辖区内所有原材料、半成品、产成品等物料完成初始标示,标示工作责任人即为工作执行人未按要求完成标示工作的,由本车间对工作负责人进行考核
8.2各车间应每天至少一次安排辖区内各类标示的巡查,并应能明确本次巡查的具体责任人未按要求完成巡查、或巡查后未发现明显问题的,由本车间对工作负责人进行考核由于巡查不到位,出现标示内容与实际不符、或物资无明显标示等情况,并直接造成下一环节工作失误,对上一环节标示工作负责人或标示巡查负责人进行100元罚款若本次工作失误造成较大影响或损失,则对上一环节标示工作负责人或标示巡查负责人进行200~500元罚款当出现
4.
8.2条款中明确罚款事项的情况时,如车间不能明确具体责任人,则对本车间负责人进行相应处罚各车间在各类工作环节中,鼓励员工自检、互检,及时发现物料标示问题,并及时向主管部门汇报经生产管理部确认,确属标示问题且存在较大风险的,进行20^200元奖励以上考核结果,属于车间自身考核范畴的,由各车间在本月考核报表中注明;属于明确罚款或奖励范畴的,由生产管理部统一在本月工资报表中增减物料领发管理规定1总则制定目的规范物料领用、发放流程,使物料领发管理有章可循适用范围公司内各种原材料、辅料、半成品(在制品)的领用、发放作业,除另有规定外,悉依本规定办理权责单位1)物控计划部负责本规定制定、修改、废止之起草工作2)总经理负责本规定制定、修改、废止之核准2物料领用规定领料依据1)物控计划人员依销售订单及成品库存状况,发出生产通知单,确定生产产品名称、规格、客户、数量及交期2)物控计划人员根据《销售订单》、《产品用料明细表》,确定该批产品各制造工程可领物料之明细3)物料明细包括物料编号、名称、规格(工序)、可领用数量4)可领用数量依下列方式确定可领用数量=销售订单批量*每单位产品用量*(1+损耗率)损耗率5%-2%依情况定其中单位产品用量及损耗率依《产品用料明细表》确定5)《批领(发)料单》一式四联,一联由生管部自存,一联交制造部相关工程,一联交资材部相关仓库,一联交财务部《批领(发)料单》作为物领用、发放之依据领料流程1)制造部物料人员依据《批领(发)料单》核定数量,开具《领料单》《领料单》应注明领用物料所用之销售订单号码、《批领(发)料单》号码,以及领用物料之编号、名称、规格及领用数量,其领用数量应少于或等于《批领(发)料单》核定之数量2)《领料单》经制造部权责主管审核后,由物料人员持单向所属仓库领用所需物料3)《领料单》一式四联,一联由制造部自存,一联交仓库,一联送物控人员,一联转财务部4)当《批领(发)料单》上所核定数量之物料领用完毕后,制造部不论何因需追加领用物料时,须开具《物料超领单》方可领料超领规定1)由制造部相关人员填具《物料超领单》,注明超领物料所用之销售订单号码、批量、超领物料编号、名称、规格及超领数量、超领率,并详细阐明超领原因2)超领原因一般有A)原不良补料(即上工程之不良品,需追补)B)作业不良超领(因本工程作业原因产生不良需超领)C)下工程超领(因下工程超领物料,需本工程追加生产数量,导致需追加领料)D)其他原因3)超领权限规定A)超领率低于1%时,由制造部经理审核后,可领用物料B)超领率大于1%时小于3%时,由制造部经理审核后,转PMC经理审核后,方可领用物料C)超领率大于3%时,除上述人员审核外,需经公司副总审核,方可领用物料4)《物料超领单》一式四联,一联由制造部自存,一联交仓库,一联送PMC物控人员,一联交财务部委外加工领料规定1)仓库人员根据采购之《委外订单》,开具《出库单》发放物料给协力厂商《出库单》需注明委外加工单号码、物料编号、名称、规格与数量,发出数量应小于或等于《委外订单》核定之数量2)协力厂商需超领物料,必须填写《超领料单》,经采购、物控人员核准,方可领料3)《出库单》、《超领料单》均一式四联,一联由厂商自存,一联由仓库保存,一联送物控,一联送财务部4)财务部应将属厂商原因之超领责任从付款中扣除3物料发放规定发料作业1)仓管人员接收领料单位的《领料单》或《超领料单》2)审核单据是否手续齐全,与《批领(发)料单》规定之编号、名称、规格、数量是否相符3)符合者予以放物料,并当面点交完成,除领料单一联退领料单位外,其余三联由仓库接收,其中一联自存,另两联分开汇总后,每日送往财务部及生管部物控人员4)根据《领料单》及《超领料单》记录《物料管制卡》,应注意将单据号码记入,以备核查注意事项1)应遵循先进先出之原则2)确保库存剩余物料之标示及可追溯性3)保证发出及余留之物料均妥善包装、保护,不影响品质4)确因特殊原因,物料不能化整为零,发料数量必须大于领料数量时,以物料调拨形式将多出之物料发出(参阅《物料调拨管理规定》)批领(发)料单制造单位NO、领料单领料单位年月日超领料单超领单位年月日4领发料管理规定1领料规定各车间、部室人员领用物料时,依据订单核定的数量,开具《领料单》,《领料单》上应填写领用物料的订单号、物料名称、规格型号及领用数量,并有负责人签名大批量的按单领料可凭《配料单》发料2发料规定按“推陈储新,先进先出,按规供应,节约用料”的原则发料,仓管人员接到领料单位的《领料单》时,仔细核对手续是否齐全,与订单上的订单号、名称、规格、数量是否相符,一切出库物资发放必须由库管员验证领料单据是否合法、有效,签字是否齐全,对不符合规定的领料单应拒绝发料符合时当面清点交付物料,《领料单》一式三联,除《领料单》第一联退领料单位外,其中一联自存并登记入帐,另一联交财务部3成品出库成品根据销售部开具的《发运单》发货,经复核无误后予以出库,成品出库必须做到规格、数量准确无误、包装无损,标志清晰成品出库时由仓管员填写《出库单》,一式三联,除《出库单》第一联仓库自存并登记入帐外,其中一联交收货人可由销售部代收,另一联交财务部.退补料管理规定1退料规定a.余料退库:车间余料退库应填写《退料单》,在对应的栏目中详细填写品名、规格、数量及退料原因等b.质量不良退库如果是因为质量方面引起的退料,必须经过车间检验员检验,并注明原因(制程损坏、来料本身不良等)后方可退料
(2)补料规定车间损耗超标或制程异常,导致物料数量不够需要补料时,需由车间主任填写《补料单》,注明品名、规格、数量、补料原因等,经过副总经理批准后方可补料如果是因为物料本身不良需要补料时,可凭不良物料以次换新,按调换处理,仓管员做好相应的登记.呆滞物料处理规定对于呆滞物料,由副总经理组织仓库、生产、采购、品质等相关人员进行评审,做出处理,通常有以下几种处理方式
(1)将呆滞物料再加工后予以利用
(2)将呆滞物料代用于类似物料,以不影响功能、安全、及外观为原则
(3)将呆滞物料退还供应厂商
(4)将呆滞物料转售给其他使用厂商
(5)将呆滞物料售与中间商,如废品回收站
(6)暂缓处理,继续呆滞,等待时机
(7)将呆滞物料报废处理仓库盘点管理规定
(1)实后缺料盘点法,当某一物料的存量低于一定数量时,(如体积大的物料低于100个,体积小的物料低于400个时),仓管员应及时盘点,核对数量与帐目是否相符
(2)实行循环盘点法,每月底由仓管员对库存物料逐一盘点,核对数量与帐目是否相符
(3)实行定期盘点法,每年一次,在年底进行,盘点完毕后在《物料管理明细表》(台帐)上做好相应的记录,并注明“年底盘点,经过仓库组长审核签字后交财务部和副总经理.仓库安全管理规定
(1)仓库严禁吸烟和使用明火
(2)物料堆放不得影响照明,不得妨碍机械设备的操作,不得妨碍通道与出入口,不得妨碍消防器具的紧急使用,不得堵塞电气开关及急救设备
(3)物料储存重量不得超过货架的安全负荷量
(4)有毒有害、易燃易爆物品隔离存放
六、相关记录表格《物料管理明细表》(台帐)《领料单》《补料单》《退料单》《入库单》《出库单》《配料单》《采购明细表》《产品购销合同》《零星物品请购单》《合理库存一览表》
七、附则
1、本制度由副总经理负责编制、解释、修订
2、本制度自2008年12月1日开始实施制造命令号码产品名称客户产品料号规格升E量序号物料名称料号规格单位可领数量备注确认:审核填表序号制造命令号码物料名称料号规格单位领用数量备注仓管审核填表制造命令号码产品名称客户产品料号规格批量超领状况超领物料名称规格料号应领数量超领数量超领率原因说明副总物控主管填表。
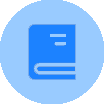
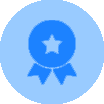
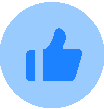