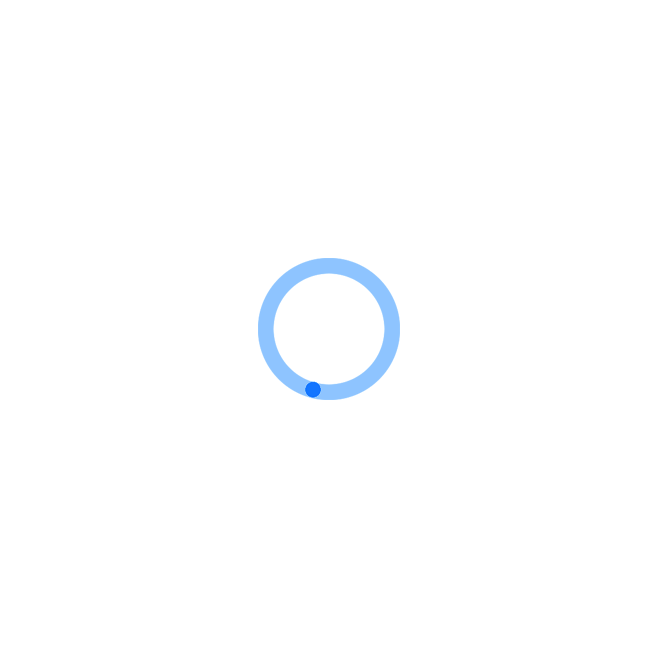
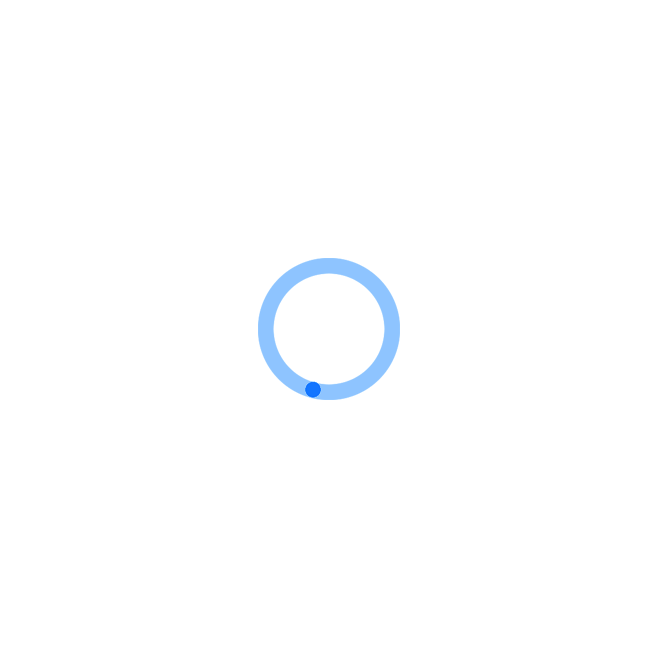
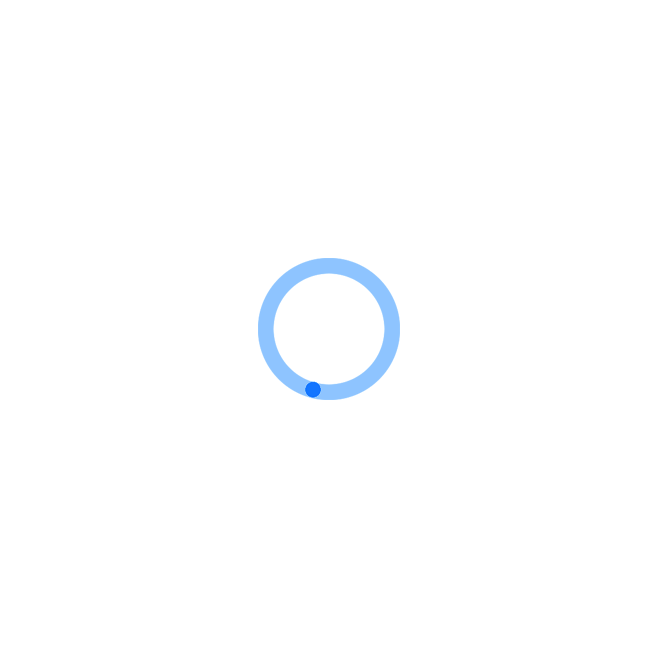
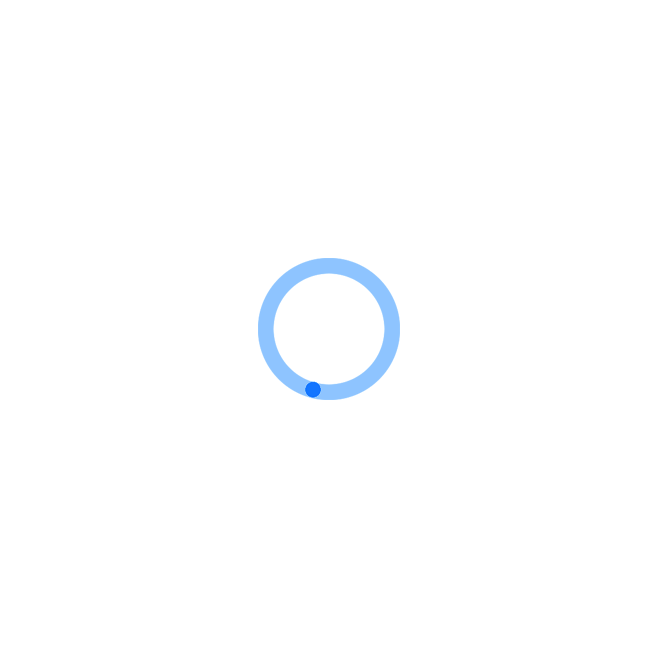
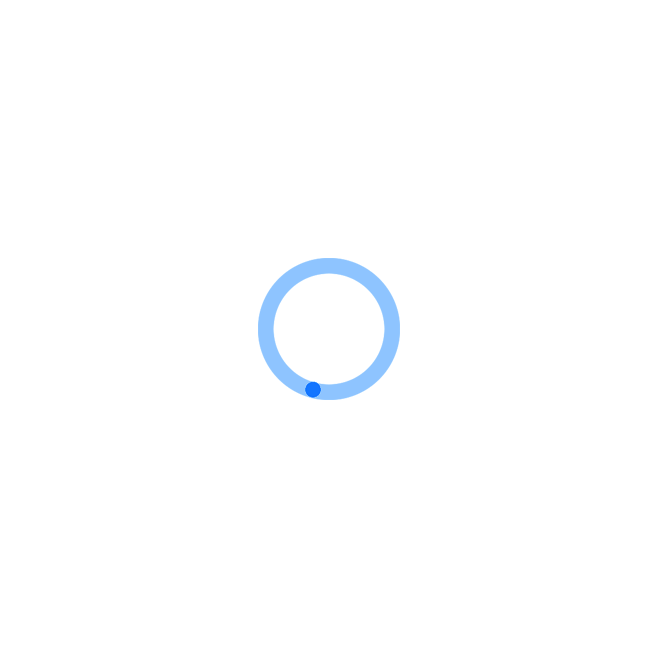
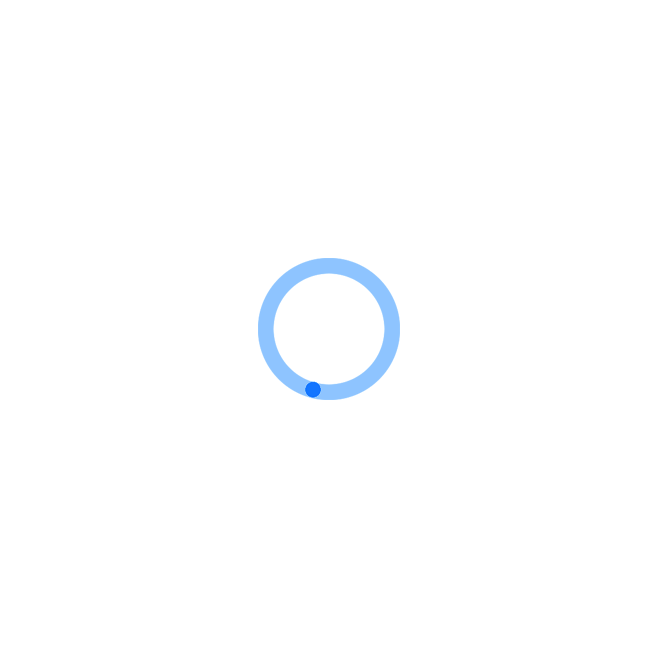
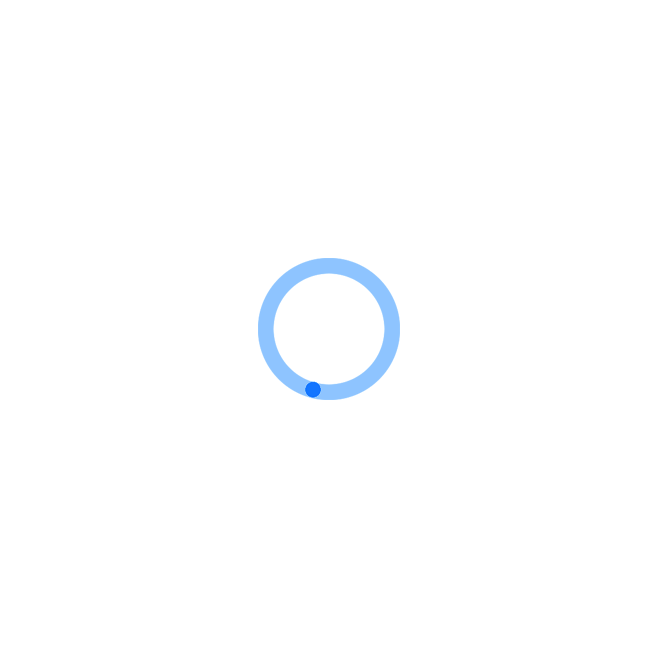
还剩5页未读,继续阅读
文本内容:
1再验证目的22再验证人员23风险评估
23.1风险评估标准
23.2风险评估准则
33.3风险评估内容44文件确认55人员培训确认56再验证方案实施情况57偏差清单68偏差报告69风险的接受与评审610再验证结果611评价及建议612再验证周期613附表7自动颗粒包装机再验证报告1再验证目的确认DXDK-40型自动颗粒包装机运行数据达到继续使用要求;确认DXDK-40型自动颗粒包装机对颗粒剂、散剂包装符合生产需要;确认DXDK-40型自动颗粒包装机加热温度;确认DXDK-40型自动颗粒包装机包装质量;确认在规定的范围内操作,DXDK-40型自动颗粒包装机能稳定的运行且保证各项指标能达到标准2再验证人员由组成再验证小组负责DXDK-40型自动颗粒包装机的再验证工作3风险评估
3.1风险评估标准风险的严重程度(S)风险发生的可能性程度(P)风险的可检测性等级(D)
3.2风险评价准则风险指示值(RPN)二严重程度(S)X发生概率(P)X可检测性(D)低风险(1〜4)、中等风险(6〜9)、高风险(12〜27)低风险为可接受的风险,中等风险及高风险均为不可接受的风险
3.3风险评估内容经再验证小组人员共同对自动颗粒包装机设备再验证进行质量风险评估,对存在的质量风险提出了预防和纠正措施建议第4页共7页《膜通化吉通药业有限公旬GMP文件YZ-SB-20-2019通过对以上风险因子进行评估,对于再验证时间进行安排4文件确认按照(附表1)所列项目逐一核对文件资料,所列文件资料应齐全,且是批准的最新版本5人员培训确认验证前按照验证方案对相关人员进行培训并查阅培训档案,确认相关人员经过了相关文件的培训I,包括自动颗粒包装机标准操作规程、维修保养标准操作规程等详见(附表2)6再验证方案实施情况再验证小组按已批准的再验证方案在质量保证部的监控下,在所用计量器具校验的前提下于年月日进行再验证工作具体实施过程如下运行确认时间年月日对DXDK-40型自动颗粒包装机进行调试运行,检查确认各项指标,结果均符合要求
1.1DXDK-40型自动颗粒包装机空运情况检查确认结果设备安装稳固;包装质量合格;空运转平稳、无异常噪声检查记录见(附表3)
1.2DXDK-40型自动颗粒包装机主要性能确认包括包装质量、装量差异、包装速度、成形机构、输送机构均符合标准记录表见(附表4)性能确认时间年月日与生产同步进行验证
2.1装量差异的确认性能确认所需物料第5页共7页匾醪通化吉通药业有限公旬GMP文件YZ-SB-20-2019再验证方法按确定的标准操作规程开启DXDK-40型自动颗粒包装机后,把装入已清洁、干燥、消毒的DXDK-40型自动颗粒包装机的装料斗内,在机器正常生产包装后每隔5分钟进行取样6次,送到化验室进行称重检测,再验证装量差异可接受标准每袋重控制在go检查记录见(附表5)
2.2包装速度、包装质量的确认性能确认所需物料再验证方法在机器正常工作时,选择包装的某一时刻开始计时,5分钟、10分钟、15分钟、20分钟,查出每个时间内所包装的袋数可接受标准在5分钟、10分钟、15分钟、20分钟内包装的袋数在50-100袋/分时即为合格检查记录见(附表6)
2.3设备负荷情况的确认根据设备的性能测试设备的负荷情况结果包装质量、包装速度符合工艺要求;热封压痕机构,热封严密均匀;牵引机构,运转平稳、各部分运转符合设计要求7偏差清单(附表7)8偏差报告(附表8)9风险的接受与评审对判断的关键性风险和非关键性风险采取的初步风险控制措施若经检查确认符合要求,则其相应的风险可降至为可接受风险,确认结果记录详见(附表9)10再验证结果经审查各项测试结果符合已批准再验证方案制订的标准,完全达到使用计要求和GMP对设备的要求11再验证周期五年记录表见(附表10)12评价及建议通过再验证,已证明该设备能满足生产要求、各项指标符合要求建议再验证委员会发放再验证证书,可投入使用第6页共7页通化吉通药业有限公旬GMP文件YZ-SB-20-201913附表DXDK-40型自动颗粒包装机设备再验证项目小组组长签字年月日第7页共7页严重程度描述评分高后果严重、非常重大的GMP违规、可能对患者造成伤害,直接影响产品质量要素或工艺与质量数据的可靠性、完整性或可跟踪性此风险可导致产品不能使用3中后果严重程度中等、严重GMP违规、可能对患者造成不良影响,影响产品质量要素或工艺与质量数据的可靠性、完整性或可跟踪性2低非严重后果、轻微GMP违规、对患者无不良影响,不对产品或数据产生最终影响,但对产品质量要素或工艺与质量数据的可靠性、完整性或可跟踪性仍产生较小影响1可能性描述评分高经常发生,如复杂手工操作中的人为失误3中偶尔发生,如简单手工操作中因习惯造成的人为失误2低很少发生,如需要初始配置或调整的自动化操作失败1可检测性描述评分低缺乏系统的检测手段,根本不可能被发现,或者有可能会被偶然发现3中通过一个控制手段(或者检测系统)可以被发现,但不可能100%的被发现2高通过一个或多个有效的检测手段,或者在后续的控制程序中,发生的危害全部都能被发现1序号评估项目引起的原因风险可能导致的结果严重程度S发生概率P可预知性DRPN值预采取的控制措施1人员车间人员操作程序不规范,未按规定的要求进行操作,导致验证失败或不能反应真实结果验证结果不能完整证明设备性能1212加强对相关人员的培训指导,增强操作人员对文件的执行力2文件文件本身制定的不完整或内容有误,或者包含有让人误解的信息,对文件的误解使操作人员操作不当达不到验证要求,影响工艺验证的结果1111组织车间相关人员进行集中培训,加强对相关专业内容的理解,并能将相关知识应用到具体的文件中3设备转动设备的主动和被动链轮之间的链条过松或过紧设备运行不畅,易打滑、松脱2228对设备进行定期检查、维护4设备各电器元件、接线松动脱落,各零部件安装紧固不良设备不能正常安装使用,设备易出现故障2124对设备定期进行进行电器元件、接线及筌部件紧固度的确认5设备触控面板功能失效各种参数不能调整,设备不能正常运转,产品质量无法保证3139每次开机前检查触控面板能否正常运行,能否有效控制设备6仪表、衡器仪器仪表、衡器规格不符合生产使用要求,未校验或不在校验期内影响设备运行参数的检查,不能正常判断是否操作正常32212检查所有的仪器仪表、衡器的规格是否符合生产使用要求,是否有校验标志且在校验期内7设备与药品直接接触的设备材质不符合GMP要求影响产品质量3113进行现场确认内容开始时间结束时间运行确认性能确认再验证报告起草确认人确认日期复核人复核日期。
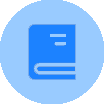
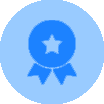
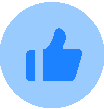